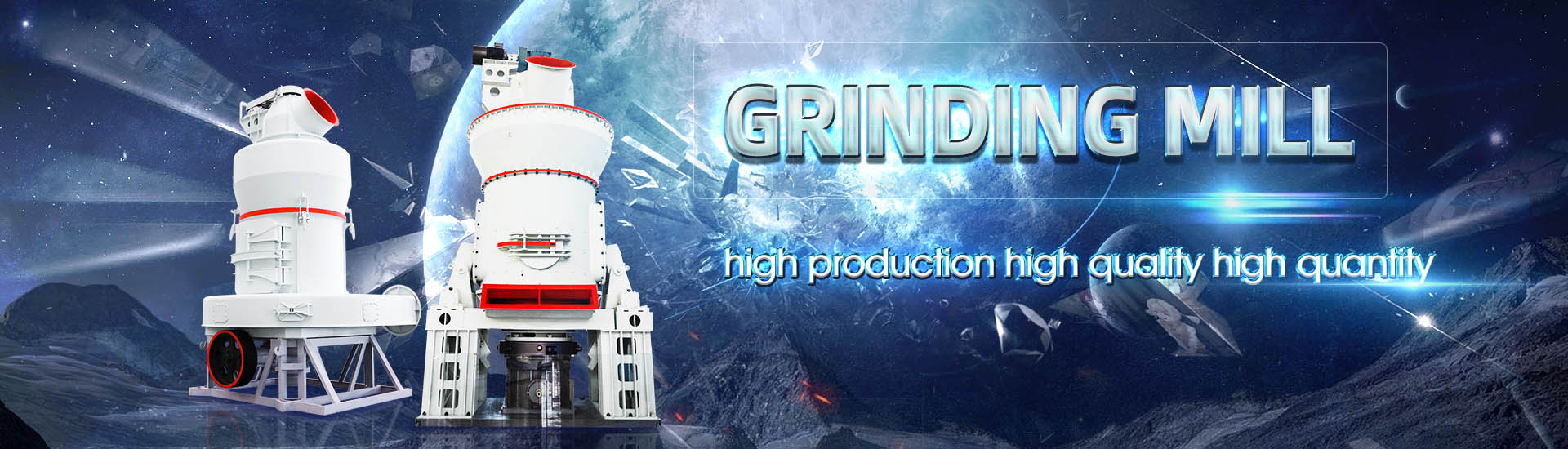
How to use laterite nickel ore slag
.jpg)
Review on comprehensive utilization of nickel laterite ore
2024年11月1日 This paper systematically reviews the traditional hydrometallurgical and pyrometallurgical processes used to extract valuable metals such as nickel, cobalt, 2023年9月26日 What are the ways to utilize laterite nickel smelting slag? (1) Ferronickel slag production of cement mixing materials: After nickeliron slag is finely ground to fine powder, it can be added to cement clinker to make What are the ways to utilize laterite nickel smelting slagIndustrially, the pyrometallurgical treatment of laterites is mostly accomplished with a wellestablished method, namely, the rotary kiln–electric arc furnace (RKEF) process, which includes three main operations—calcination, Nickel Laterite Smelting Processes and Some Examples The current FeNi Nickel Pig Iron (NPI) and Ni matte smelters operate with nickel laterite ore that meet fairly specific criteria in terms of their Ni grade, Fe/Ni, Ni/Co and SiO2/MgO ratios These HydroPyro Integration in the processing of Nickel Laterites
.jpg)
Comprehensive Utilization Technology of Laterite
2024年6月25日 It can be used as the surface layer of large volume cementitious material to resist dry shrinkage cracks caused by longterm contact with dry air, protect the waste slag cementitious material in the lower layer and ensure the 2017年1月1日 The pyrometallurgi cal methods on treating nickel laterite ores consisted of producing ferronickelCurrent Studies of Treating Processes for Nickel Laterite Ores2002年8月1日 Processing of laterite ores traditionally consists of a two stage process using fossil fuels (eg, coal, oil, natural gas) in the kiln operation followed by electric furnace smelting Nickel laterite processing and electrowinning practice2024年8月7日 The two main processing methods for laterite ores are smelting and HighPressure Acid Leaching (HPAL) Smelting is used primarily on saprolite ores to obtain an iron Nickel industry Part 2 Processing nickel laterites and smelting
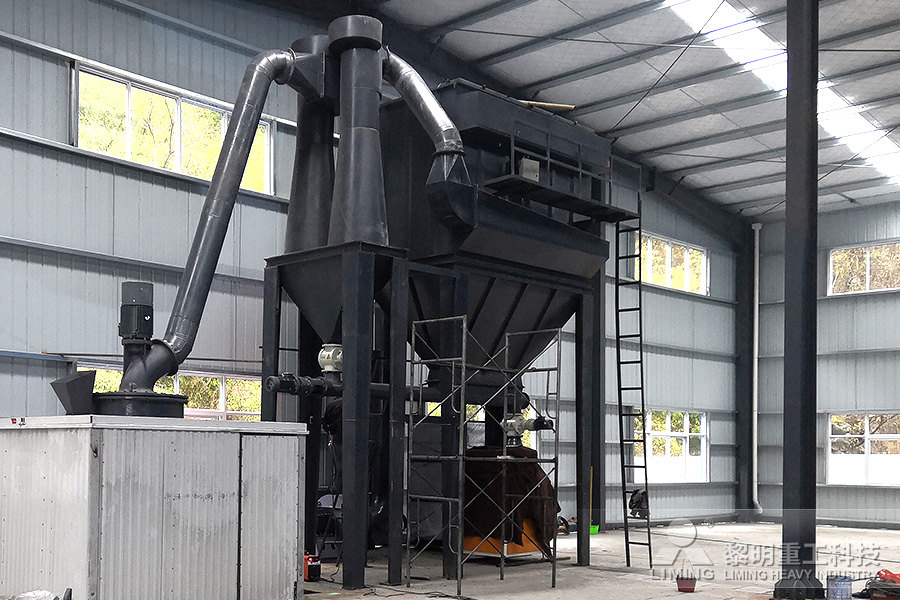
Solid state reduction and magnetic separation of nickeliferous
Conversely, the laterite ore reserves are growing, and since the laterites are close to the surface, then open cut mining can be employed, and this is a simpler technology For the sulfide ores, 2023年11月11日 Nickel is widely used in industrial processes and plays a crucial role in many applications However, most of the nickel resource mainly exists as nickel oxide in laterite nickel ore with complex composition, resulting HighGrade Ferronickel Concentrates Prepared from 2011年6月1日 In these cases there may be opportunities to reduce the greenhouse emissions from nickel laterite processing apart from those associated with improvements in energy efficiency One possible option is nonacid leaching of the laterite ore, eg bioleaching (McDonald and Whittington, 2008a, Hallberg et al, 2010)Assessing the energy and greenhouse gas footprints of nickel laterite 2022年5月31日 The processing methods of laterite nickel ore is mainly divided into two types: pyrometallurgy process and hydrometallurgy process According to the difference of nickel, cobalt content and ore type, and different working How to Extract Laterite Nickel Ore? 7 Processing
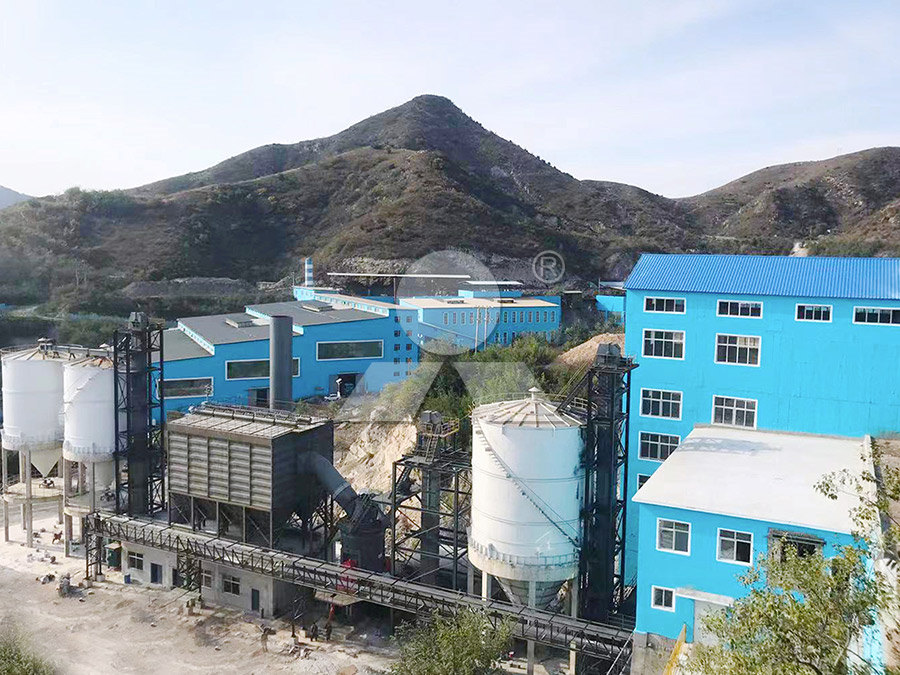
Assessing the energy and greenhouse gas footprints of nickel laterite
2011年6月1日 For each 01% reduction in nickel grade, production costs increase by about 3% to 4%, and the existing RKEF process is only economical viable for treating laterite nickel ore with nickel grades 2024年5月1日 Basicity is an important parameter in the smelting of nickel laterite to obtain lowtemperature melting point and lowliquidus slag viscosity, resulting in less energy consumption and a more The advances in the recovery process for precious metals from nickel 2013年4月15日 Nickel laterite ores account for over 60% of global nickel supply They are the product of intensive deep weathering of serpentinites under humid tropical conditionsNickel Laterite Ore Deposits: Weathered Serpentinites2016年11月1日 The research of smelting low ferronickel from preconcentrate nickeliron ore with 276 % Ni and 3800 % Fe total was carried out to find an effective way for stainless steel enterprises to use the lownickel laterite reasonable The results show that Ni and Fe both have a certain degree of enrichment, and impurities and harm elements have different degrees of Reduction Smelting Low Ferronickel from Preconcentrated Nickel
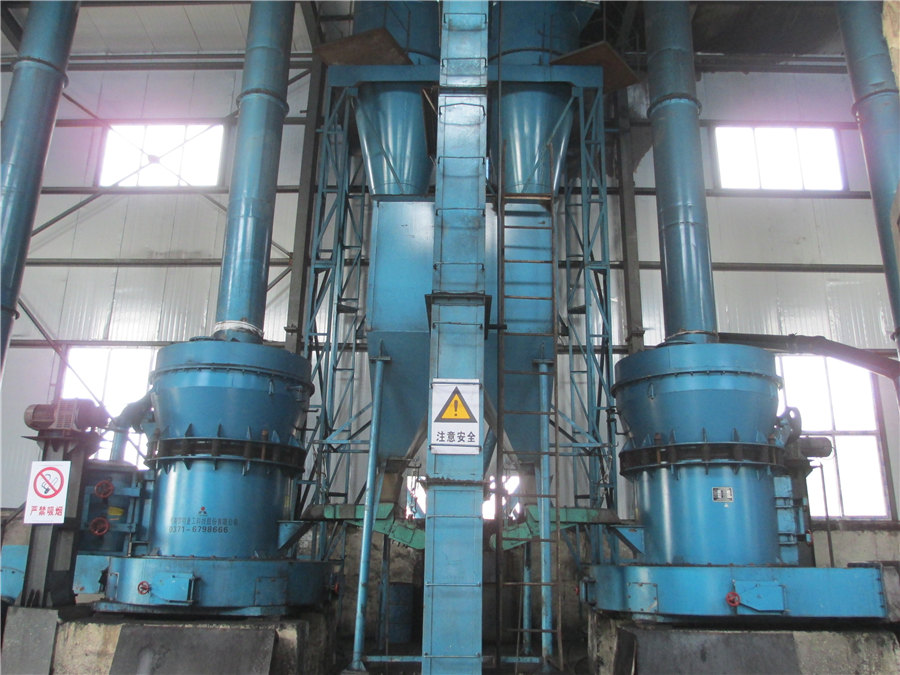
Study on the Mechanical Properties and Mechanism of a NickelIron Slag
2023年11月4日 Nickeliron slag was provided by a metallurgical material company located in Anshan, Liaoning Province, China First, the nickel laterite ore was crushed to 50–150 µm; subsequently, we added the reducing agent anthracite and cosolvent limestone The reduction and smelting output of the nickel content was greater than 10% of the crude Use of nickel slag also reduces the need for its disposal and lowers the cost of producing new aggregate materials particles ranged from black to white or clear, with occasional, relatively soft, reddish brown particles (possibly laterite ore) Both types of hard nickel slag particles were considered to be good (ie, could not be scratched, Nickel Slag an overview ScienceDirect Topics2023年10月10日 Reduction–sulfurization smelting is an effective method for treating solid hazardous waste and recovering valuable components from them In this work, a waste hydrogenation catalyst (WHC), an automotive exhaust purifier waste catalyst (AEPWC), a vulcanizer, and laterite nickel ore were mixed, and the reduction smelting behavior of this solid Reduction–Sulfurization Smelting Process of Waste Hydrogenation Download scientific diagram XRay Diffraction (XRD) analysis of laterite nickel ore from publication: Preparing FerroNickel Alloy from LowGrade Laterite Nickel Ore Based on Metallized XRay Diffraction (XRD) analysis of laterite nickel ore
.jpg)
Modelling of Nickel Laterite Smelting to Ferronickel
Modelling of Nickel Laterite Smelting to Ferronickel Douglas R Swinbourne School of Civil, Environmental and Chemical Engineering, RMIT University, 124 Latrobe Street, Melbourne 3000, Australia Keywords: nickel laterite smelting, ferronickel Most nickel is produced as the metal, but about a third of the world’s new nickel is ferronickel2023年5月5日 1 Introduction Nickel slag (NS) is a waste product from the nickel industry, which can be incorporated with other natural resources to enhance specific characteristics for various applications 1 The high magnetite content of NS is the primary reason for its use in the absorption of electromagnetic interference (EMI) emissions, 2 sensors, 3 batteries, 4 alkaline Nickel Slag/Laterite Soil and Nickel Slag/Iron Sand 2 Alternative Nickel Laterite Smelting Processes to the Rotary KilnElectric Furnace (RKEF) Process 21 The Vaniukov Process The Vaniukov process is a wellestablished technology for pyrometallurgical treatments, especially for the smelting of copper ores [11,12] Its use in laterite smelting was studied in the last decadeNickel Laterite Smelting Processes and Some Examples of Recent Nickel and Cobalt Production Michael S Moats, William G Davenport, in Treatise on Process Metallurgy: Industrial Processes, 2014 223 Extraction of Nickel and Cobalt from Laterite Ores About 40% of the world’s primary nickel production starts with laterite oresLateritic Ni, Co deposits contain layers of one or both of (1) nickeliferrous, cobaltiferrous goethite Laterite Ore an overview ScienceDirect Topics
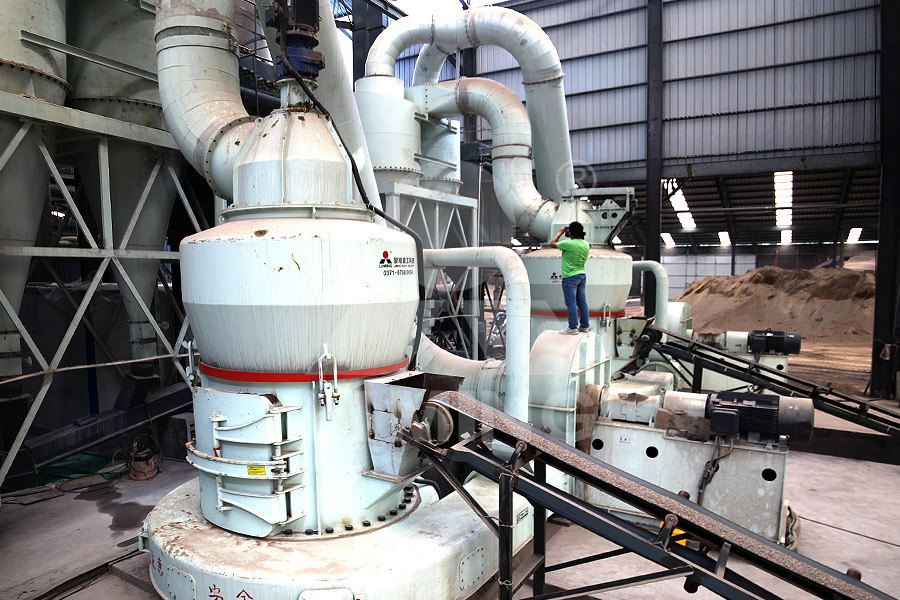
Magnetic separation for recovering iron resources from acid
2024年8月21日 The acidleaching tailings of laterite nickel ore are a hazardous waste generated by the laterite nickel ore industry [1], [2], [3] As global demand for nickel continues to rise and nickel sulfide resources decrease, the extraction of nickel resources from laterite nickel ores the main development trend of the global nickel industry in the coming years [4]2022年8月22日 MHP is one of the intermediate products of nickel laterite ore processing through the hydrometallurgical route The solution after the leaching reaction is precipitated to separate solid–liquid parts through countercurrent decantation The pH is adjusted for leached liquor obtained to remove ions such as Fe +3, Al 3+, and Cr +3 as hydroxide Recent Progress in Hydrometallurgical Processing of Nickel Lateritic OreTo acquire understanding of Ni enrichment from laterite ore, the mineralogy and crystal chemistry of a low grade limonite type nickel laterite ore sample assaying 097% Ni from Indonesia were Chemical composition of nickel laterite ore sample (mass fraction 2024年11月1日 Nickel laterite ore, as a major source of nickel, holds tremendous potential for future utilization This paper reviews the commonly used production technologies and emerging processing techniques for the development and utilization of nickel laterite ore, summarizing the latest research findings on its comprehensive useReview on comprehensive utilization of nickel laterite ore
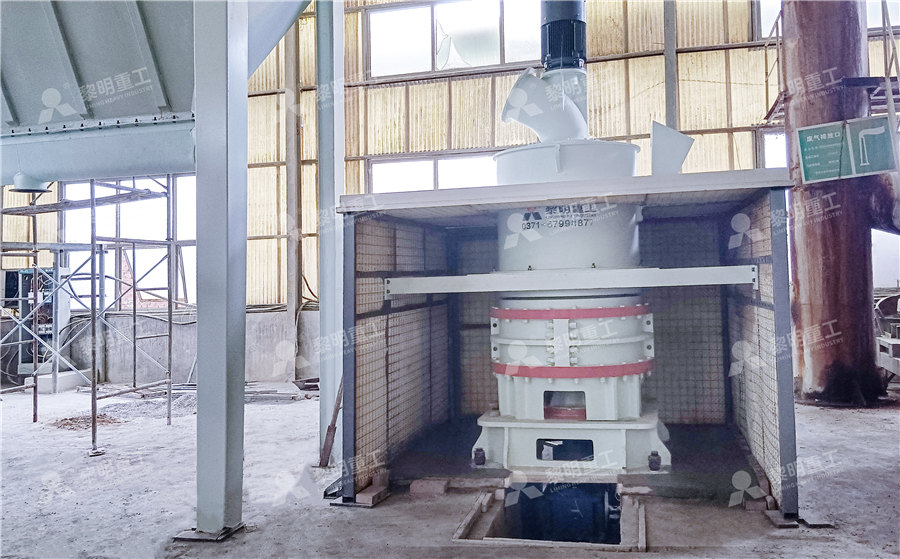
Mineralogical characterization and design of a treatment process
2017年2月10日 Laterite ore deposits are formed by nickeliferous olivines via prolonged weathering and leaching processes and are mainly distributed in tropical and subtropical regions near the equator (Dalvi et al, 2004)Moreover, the formation of a nickel laterite may be influenced by the composition, topography, structure, climate, and duration of the formation of the 1 Ore Preparation Saprolite ore has a moisture content of 34 wt% in the ore The saprolite type laterite nickel ore that has been separated will then be crushed, screened to size (100200 mesh), and blended first to get a mixture according to the desired compositionLiterature Review: Comparison of Caron Process and RKEF On The 2022年7月1日 Large and ParticleScale energy assessment of reduction roasting of nickel laterite ore for Ferronickel production via the rotary KilnElectric furnace process The drawbacks of the RKEF process are the large amounts of generated dust and slag, significant CO 2 emissions, and excessive energy consumption [18]Large and ParticleScale energy assessment of reduction roasting 2017年1月1日 Secondly, the mixture of nitric acid an d the nickel laterite ore with a certai n ratio of acid/sol id are Slag proper ties can influen ce met al/slag separation an d operati ng temperature Current Studies of Treating Processes for Nickel Laterite Ores

Nickel laterite deposits – geological overview, resources and
Nickel can be enriched to ore grade in parts of the profile by being incorporated into the structure of the newly formed stable minerals or into the alteration products of primary minerals2021年6月1日 Leaching behaviour of slag and fly ash from laterite nickel ore smelting (Niquelândia, Brazil) Appl Geochem, 64 (2016), pp 118127, 101016/japgeochem201509019 View PDF View article View in Scopus Google Scholar 8 Nickel industry: Heavy metal(loid)s contamination sources 2023年11月27日 How to reduce the energy consumption of the rotary kilnelectric furnace (RKEF) process has become an important issue for the stainless steel industry The aim of this study is to reduce the energy consumption of ferronickel production from saprolite nickel laterite in the RKEF process The effects of the slag binary basicity, FeO content, and Cr2O3 content on Enhancing Rotary KilnElectric Furnace Process of Saprolitic Laterite 2020年10月1日 A coalbased direct reduction process was used to recover the ferronickel from lowgrade nickel laterite oreThe effects of basicity on the compressive strength, metallization rate, microstructure, and reduction characteristics of carbonbearing nickel laterite ore pellets were investigated The results show that the metallization rate of iron and the compressive strength Effects of direct reduction process on the microstructure and
.jpg)
Recovery of highquality iron phosphate from acidleaching
Recently, the rapid development of electric vehicles has raised concerns about the availability of the metal resources required for Liion batteries, such as iron (Fe), cobalt (Co), and nickel (Ni) [1], [2]Laterite nickel ore, which accounts for 75 % of the total nickel reserves, has emerged as a primary source for nickel mining in the future [3], [4], [5]1 Ore Preparation Saprolite ore has a moisture content of 34 wt% in the ore The saprolite type laterite nickel ore that has been separated will then be crushed, screened to size (100200 mesh), and blended first to get a mixture according to the desired compositionLiterature Review: Comparison of Caron Process and RKEF On The 2023年4月23日 Nickel ore refers to the naturally occurring rocks or minerals that contain significant amounts of nickel Nickel is a chemical element with the symbol Ni and atomic number 28 It is a silverywhite metal with a relatively high melting point and excellent corrosion resistance Nickel is commonly found in the Earth's crust, but it is typically extracted from its Nickel (Ni) Ore Properties, Formation, Minerals, Deposits