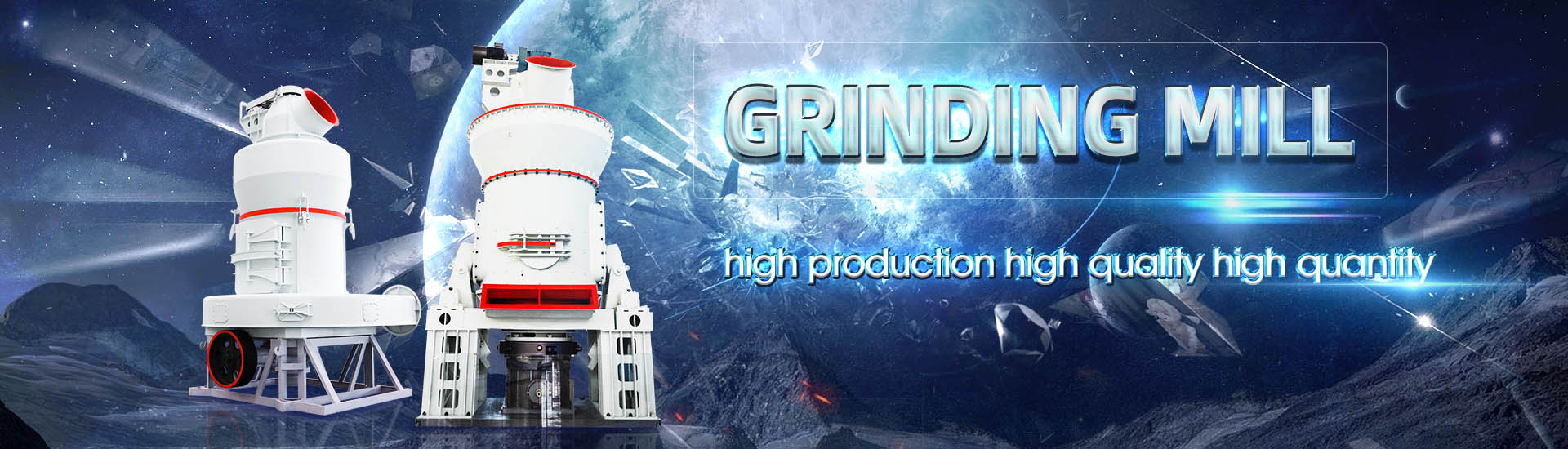
How to reduce the third wind powder in steel ball mill
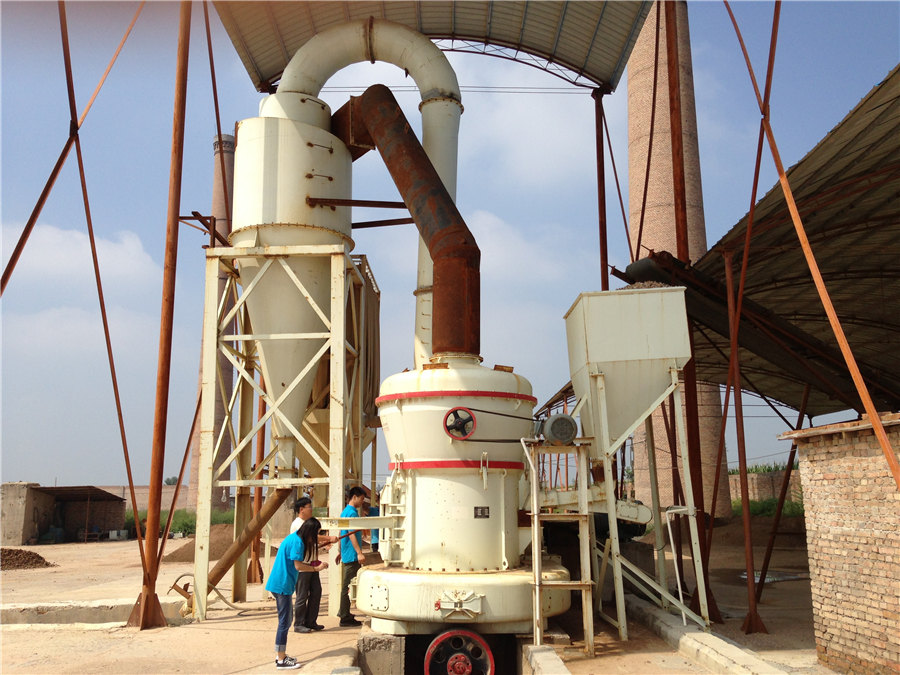
BALL MILLS Ball mill optimisation Holzinger Consulting
Ball mill optimisation As grinding accounts for a sizeable share in a cement plant’s power consumption, optimisation of grinding equipment such as ball mills can provide significant cost and CO2023年6月27日 This review found that ball milling is the best tool for reducing the particle size of recycled metal chips and creating new metal powders to enhance mechanical properties and Producing Metal Powder from Machining Chips Using Ball Milling 2021年7月12日 The ventilation effect of the ball mill is roughly in two aspects: one is to discharge the fine powder in the mill in time, so as not to affect the grinding efficiency; second, How to ventilate the ball mill ALPA Powder Equipment2023年6月27日 This review found that ball milling is the best tool for reducing the particle size of recycled metal chips and creating new metal powders to enhance mechanical properties and (PDF) Producing Metal Powder from Machining Chips Using Ball

Best way to determine the balltopowder ratio in ballmilling?
If you want to reduce the particle size, you should use small balls with slow rpm to get cascading effect and if you want to mix them then you can do with big balls with high rpm As for as2023年3月14日 I want to reduce the amount of powder, let's say, a half of the optimized one, to be proceeded further by ballmilling The parameters that have been optimized are : volume How can I determine the best RPM and balls to powder ratio for 2020年1月11日 After consulting Fote engineers and having a reference, here five methods are sorted out for the improvement of ball mill efficiency and the materials utilization rate This can 5 Ways to Improve the Ball Mill Efficiency FTM2015年6月19日 Use this online calculators for Motor Sizing and Mill sizing as well as mill capacity determinators In extracting from Nordberg Process Machinery Reference Manual I Ball Mill Design/Power Calculation 911Metallurgist
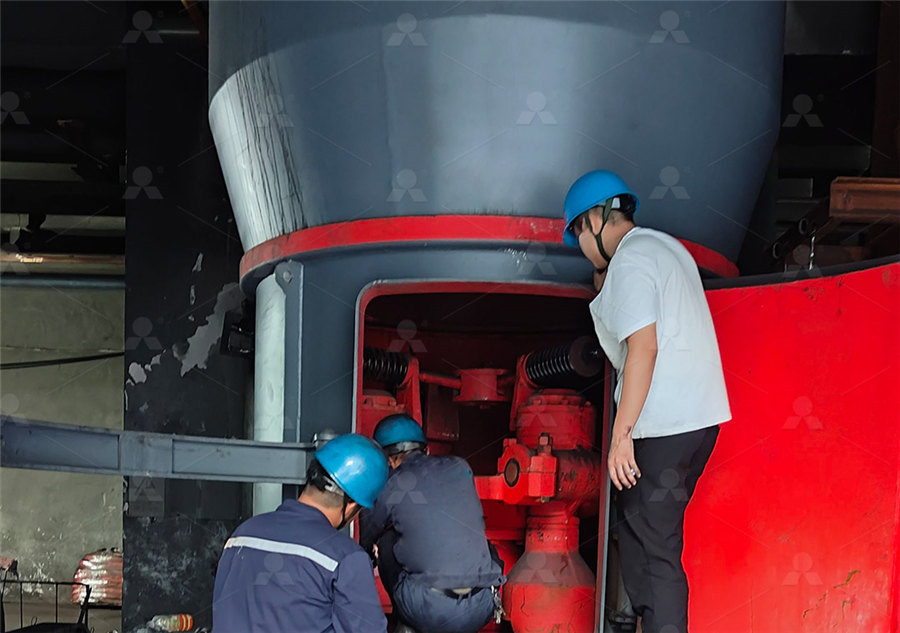
Key Factors for Ball Mill Optimization in the Mining Industry
Ball mill optimization is a critical process in the mining industry It ensures that grinding mills operate efficiently, reducing costs and maximizing production In this guide, we’ll cover the key The ball mill is a tumbling mill that uses steel balls as the grinding media The length of the cylindrical shell is usually 1–15 times the shell diameter ( Figure 811 ) The feed can be dry, Ball Mill an overview ScienceDirect Topics2013年4月1日 The role of classification in milling appears to have been neglected in the current efforts to reduce the energy consumption of grinding Two past approaches, experimental and modelling, for quantifying the effects of classification efficiency and circulating load on the capacity of closed ball mill circuits, are revisited and discussed in this paperClosed circuit ball mill – Basics revisited ScienceDirect2018年12月13日 To investigate the power of ball mill with differing lifter shapes, a series of Discrete Element Method (DEM) simulations were performed on a ball millEffect of Lifter Shapes on the Mill Power in a Ball Mill
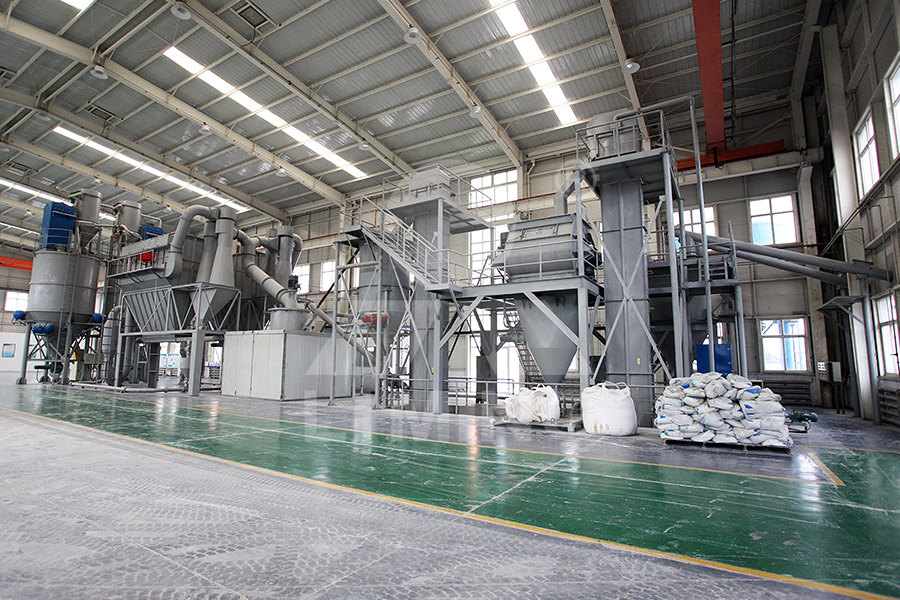
9 ways tell you how to improve ball mill efficiency
2021年7月5日 Ball mill is the key machine in the grinding stage,how toimprove its efficiency the steel ball will hit the material more times, the grinding large, and the filling rate is too high, which will easily cause the steel ball to move Changes have taken place to reduce the impact on largeparticle materials 4 Reasonable steel 2024年8月1日 3 Types of Ball Mill Media for Black Powder When producing black powder using a ball mill, the type of grinding media used plays a crucial role in the efficiency and quality of the final product Different types of media have various advantages and disadvantages, affecting the grinding process and the characteristics of the black powderEffective Ball Mill Media for Superior Black Powder Production2021年6月9日 For example, MQG1500×3000 ball mill, its larger ball loading capacity is 95~10t, the initial ball loading should be 75~8t, the remaining steel balls of steel forging will be added after the ball mill is driven for 3~4 days; the weight ratio of the ball loading is Φ100 mm Accounted for 40%, Φ80 mm accounted for 30%, Φ60 mm accounted for 15%, and Φ40mm accounted How to add load steel balls of ball mill ? Reduce wear damageI want to ball mill 60 gm of Al powder in steel jar with 10mm diameter ball size it is challenging to ball mill pure Al at room temperature because you risk to splat the metal on the balls How to calculate ball to powder ratio? ResearchGate
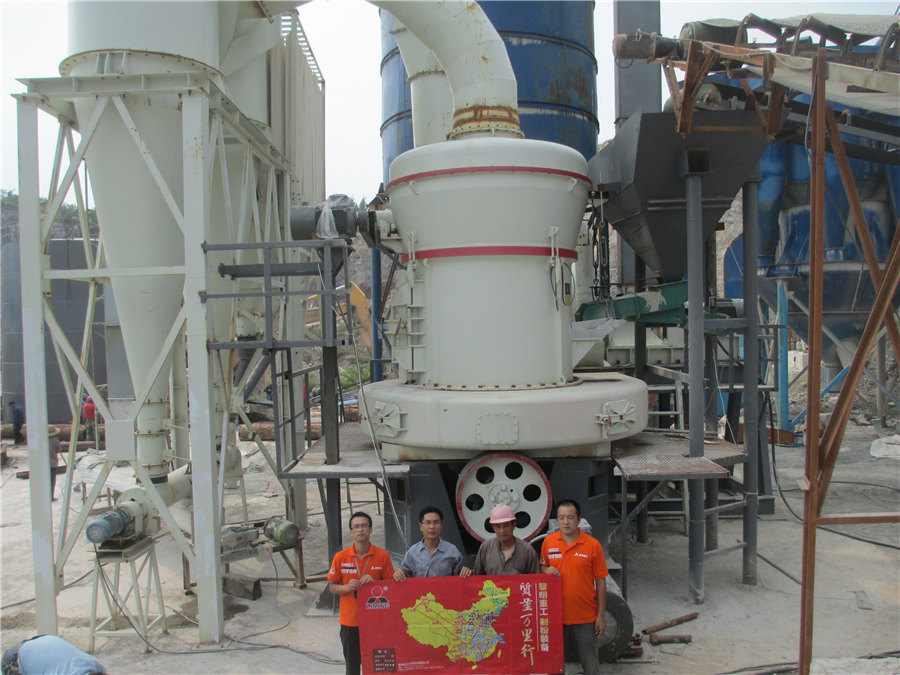
Ball mill: Principles, construction, working, uses, merits, and
2024年1月28日 2 Liners: An abrasionresistant material such as manganese steel or rubber typically lines the inner surface of the cylindrical shell to protect it from wear due to the grinding action 3 Balls: They place steel or ceramic balls, typically used as grinding media in a ball mill, inside the shell and rotate them with it 4 Feed and Discharge: Entering the hollow shell at the 2021年1月1日 Comchambered with the design of Φ 35 × 13m threechamber ball mill, the design process of ball mill is described in detail General arrangement of the mill Filling rate of grinding body in each (PDF) Design of Threechamber Ball Mill ResearchGate2021年6月29日 Nowadays, ball mills are widely used in cement plants to grind clinker and gypsum to produce cement The research focuses on the mill speed as well as air classifier speed effect on the two Effects of Mill Speed and Air Classifier Speed on Performance of OPTIMUM BALL MILL SETUP The success of a ball milling application depends on the correct selection of accessories and process parameters This includes jar sizes, jar materials, ball sizes, number of balls, particle size, material fill level, speed Three rules for the optimum ball mill setup RETSCH
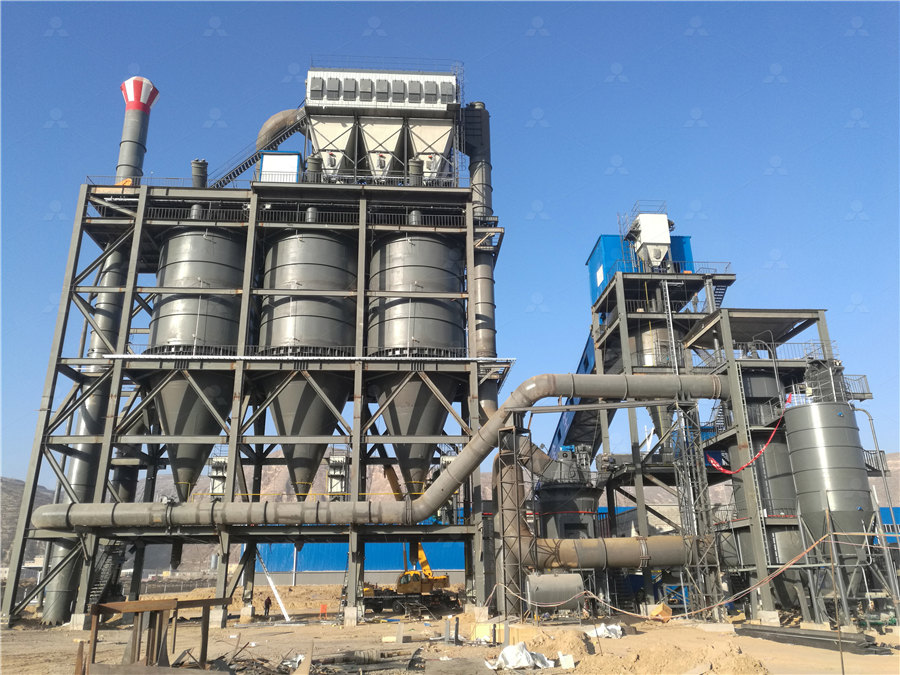
Ball Milling 911Metallurgist
2017年4月22日 The average ball consumption for mills in closed circuit has been plotted in Fig 15 for steel balls and for cast composition balls Enough data are not available to plot curves for hard and soft ores, and individual figures will vary considerably from the average of the curves, which are given merely a guide as to what may be expected and also to show the increased 2013年12月1日 Wet ball mill is one of the most predominantly used method for the purpose of mixing and grinding of raw materials in laboratories and industry [1], [2], [3]The ball mill process is very complicated process governed by many parameters, such as ball size, ball shape, ball filling, slurry loading (with respect to ball amount), powder loading with respect to the amount of total Effect of ball size and powder loading on the milling efficiency 55 known as the distribution function [45, 46]) describes the distribution of fragment sizes obtained after a breakage of particles of size xjThus, b1j, b2j, , bnj are the mass fractions of particles in size classes 1, 2, , n after a breakage of particles in size class j The mechanism of breakage is illustrated in [23] by a diagram shown in Fig 3Grinding in Ball Mills: Modeling and Process Control Sciendo2023年3月14日 I want to ball mill 60 gm of Al powder in steel jar with 10mm diameter ball size yet I am in doubt whether to maintain the powder/zirconia ratio or just reduce the powder amountHow can I determine the best RPM and balls to powder ratio for wet Ball
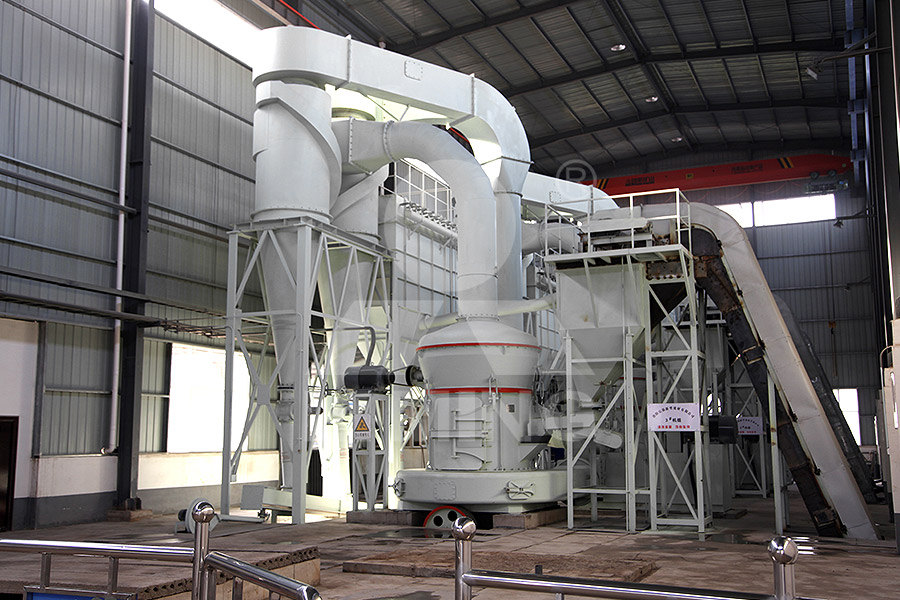
How to choose between ball mill and vertical roller mill?
2022年6月24日 The ball mill is the key equipment for the material to be crushed and then crushed The centrifugal force generated by the rotation of the cylinder will bring the steel ball to a certain height and then fall down, HGM superfine powder mill Fineness: 1502500mesh Yield: 0245t/h see More >> Clum ultrafine vertical millCement Ball Mill A ball mill is a type of grinder used to grind, blend and sometimes for mixing of materials for use in mineral dressing processes, paints, pyrotechnics, ceramics and selective laser sintering Ball mill in the cement industry is used to reduce the size of clinker into fine particles also called as cementEffects of Mill Speed and Air Classifier Speed on Performance of 2020年7月2日 A comprehensive investigation was conducted to delineate the effect of ball size distribution, mill speed, and their interactions on power draw, charge motion, and balls segregation in a (PDF) Effects of Ball Size Distribution and Mill Speed and Their 2022年4月26日 Watch this video introduction to steel milling basics Tech expert Kurt Repsher walks you through how to choose the right end mill and lubricant for your steSteel Milling Guide: How To Mill Steel YouTube
.jpg)
Ball Mill an overview ScienceDirect Topics
The history and necessity of mechanical alloying M Sherif ElEskandarany, in Mechanical Alloying (Second Edition), 2015 2515 Planetary ball mills The Planetary ball mills are the most popular mills used in MM, MA, and MD scientific researches for synthesizing almost all of the materials presented in Figure 11 In this type of mill, the milling media have considerably high 2015年1月31日 More balls with small size results in fine powder As a thumb rule powder to be milled should be taken as 25% of total ball weight If the quantity of charge is very less then milling balls will How can one select ball size in ball milling and how much material 2024年2月27日 The world’s steel demand is projected to increase from 1,880 Mt (million tonnes) in 2020 to 2,500 Mt in 2050 By 2050, the steel demand is expected to increase fivefold The steel manufacturing is energyintensive and How to Control Air Pollution in the Steel Industry?2023年10月27日 The ball mill is a rotating cylindrical vessel with grinding media inside, which is responsible for breaking the ore particles Grinding media play an important role in the comminution of mineral ores in these mills This work reviews the application of balls in mineral processing as a function of the materials used to manufacture them and the mass loss, as A Review of the Grinding Media in Ball Mills for Mineral
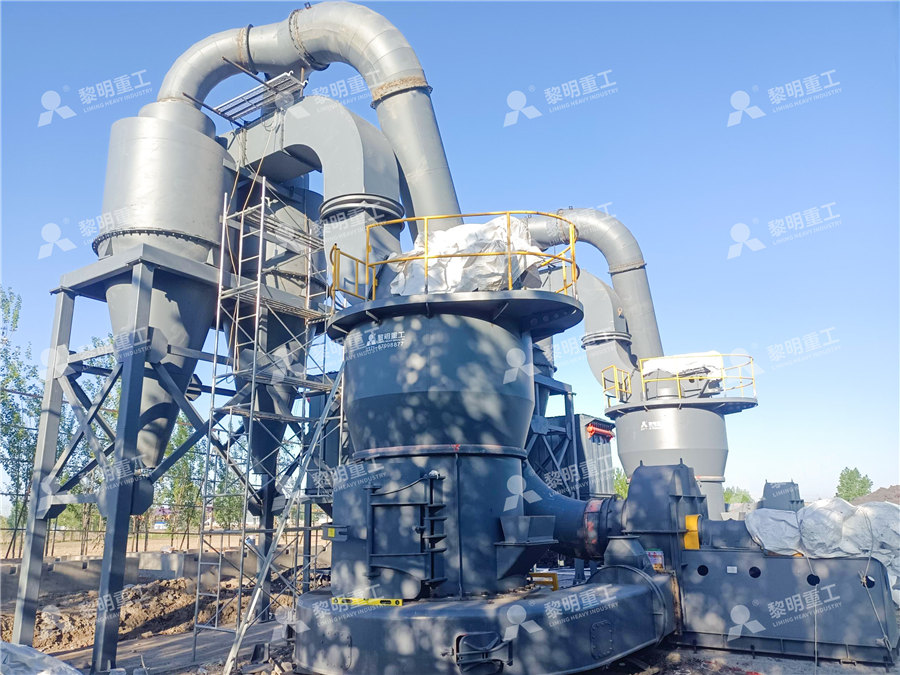
How to choose the ball loading and loading ratio of
Selection of ball loading When a ball mill works, its efficiency generally depends on the sum of work done by each ball (number of impact times and impact force) Therefore, it is necessary to give full play to the efficiency of each steel ball, 2021年6月2日 In order to achieve the specified grinding fineness, the workload of the ball mill is bound to increase, and then the energy consumption of the steel ball will increase In order to reduce the How to reduce the energy consumption of ball mill LinkedIn2017年4月15日 Normally the amount of balls should be 5055% of the apparent volume of the mill, as in a normal ballspacking we have about 40% of empty space between them, this means that we will have 30% of How to decrease particle size of alumina powder with ball milling 2015年10月20日 Worn balls Worn balls perform more poorly than spheres, reduce the grinding chamber in the mill, and increase power consumption [9] Spherical balls are mostly used for ball mill processes but are INVESTIGATION OF EFFECTS OF GRINDING MEDIA SHAPES TO
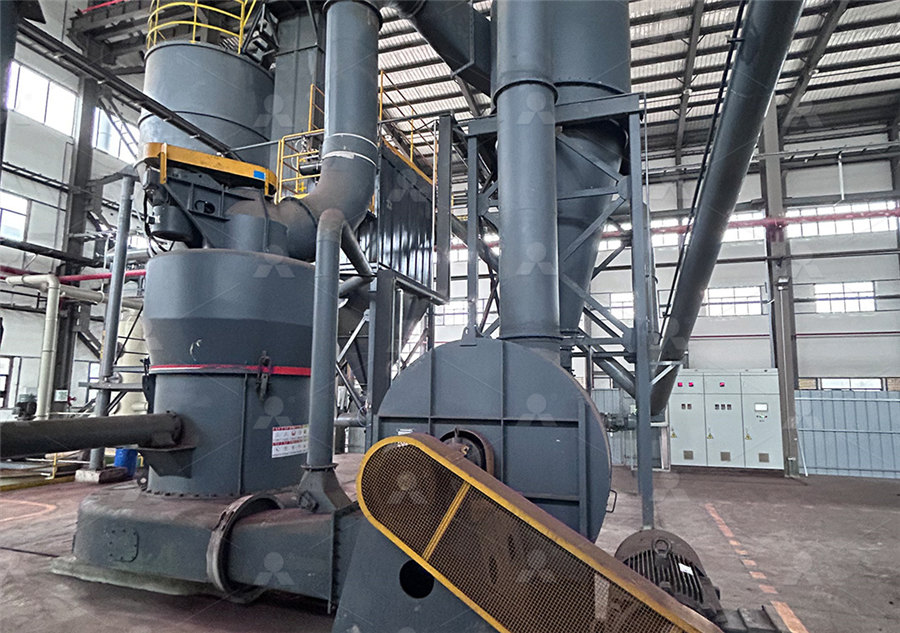
(PDF) Producing Metal Powder from Machining Chips Using Ball
2023年6月27日 Metal scrap: (a) scrap metal from turning; (b) scrap metal from grinding; (c) scrap metal from milling [48] 2020年10月1日 The current study investigates the type of ratio for ball mill jars listed in Table 3 and [63,80,168,181,183] Different balltojar ratios can affect the milling kinetics, the size, and Silicon Powder Properties Produced in a Planetary Ball Mill as a I am trying to ball mill Ni Co Cu Fe using Spex 8000 D mixer mill I milled the 4 metal powders in 10:1 BPR using 2 wt% of Anhydrous MethanolWhy is the alloy powder sticking to the balls and inner wall of Ball Mill Introduction There are three main stages to mineral processing in the mining industryThese are: Comminution (crushing and grinding); Beneficiation (separation and concentration); Smelting and refining; Ball mills are employed in the comminution stage as grinding machines (size reduction)The purpose of grinders in the mining industry is to reduce Ball Mill (Ball Mills Explained) saVRee saVRee
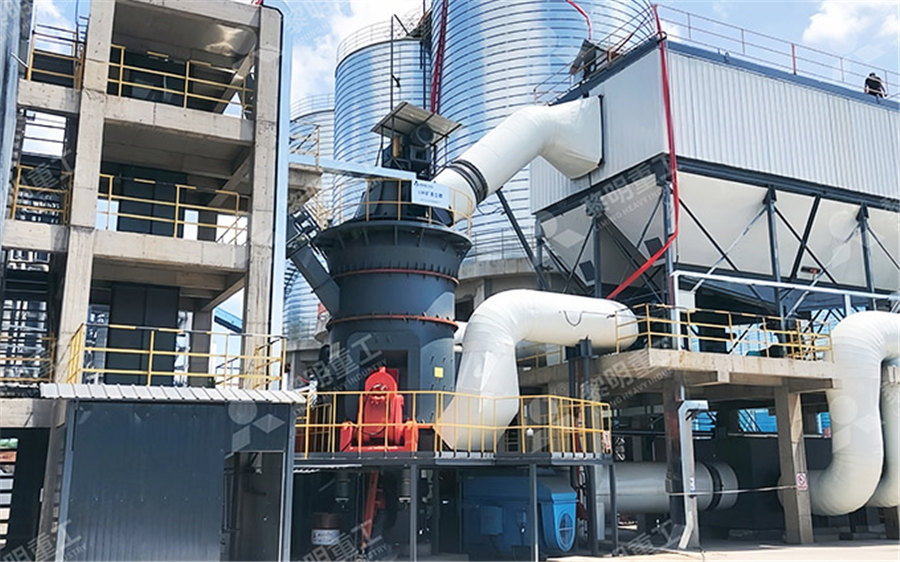
Closed circuit ball mill – Basics revisited ScienceDirect
2013年4月1日 The role of classification in milling appears to have been neglected in the current efforts to reduce the energy consumption of grinding Two past approaches, experimental and modelling, for quantifying the effects of classification efficiency and circulating load on the capacity of closed ball mill circuits, are revisited and discussed in this paper2018年12月13日 To investigate the power of ball mill with differing lifter shapes, a series of Discrete Element Method (DEM) simulations were performed on a ball millEffect of Lifter Shapes on the Mill Power in a Ball Mill2021年7月5日 Ball mill is the key machine in the grinding stage,how toimprove its efficiency the steel ball will hit the material more times, the grinding large, and the filling rate is too high, which will easily cause the steel ball to move Changes have taken place to reduce the impact on largeparticle materials 4 Reasonable steel 9 ways tell you how to improve ball mill efficiency2024年8月1日 3 Types of Ball Mill Media for Black Powder When producing black powder using a ball mill, the type of grinding media used plays a crucial role in the efficiency and quality of the final product Different types of media have various advantages and disadvantages, affecting the grinding process and the characteristics of the black powderEffective Ball Mill Media for Superior Black Powder Production
.jpg)
How to add load steel balls of ball mill ? Reduce wear damage
2021年6月9日 For example, MQG1500×3000 ball mill, its larger ball loading capacity is 95~10t, the initial ball loading should be 75~8t, the remaining steel balls of steel forging will be added after the ball mill is driven for 3~4 days; the weight ratio of the ball loading is Φ100 mm Accounted for 40%, Φ80 mm accounted for 30%, Φ60 mm accounted for 15%, and Φ40mm accounted I want to ball mill 60 gm of Al powder in steel jar with 10mm diameter ball size it is challenging to ball mill pure Al at room temperature because you risk to splat the metal on the balls How to calculate ball to powder ratio? ResearchGate2024年1月28日 2 Liners: An abrasionresistant material such as manganese steel or rubber typically lines the inner surface of the cylindrical shell to protect it from wear due to the grinding action 3 Balls: They place steel or ceramic balls, typically used as grinding media in a ball mill, inside the shell and rotate them with it 4 Feed and Discharge: Entering the hollow shell at the Ball mill: Principles, construction, working, uses, merits, and 2021年1月1日 Comchambered with the design of Φ 35 × 13m threechamber ball mill, the design process of ball mill is described in detail General arrangement of the mill Filling rate of grinding body in each (PDF) Design of Threechamber Ball Mill ResearchGate
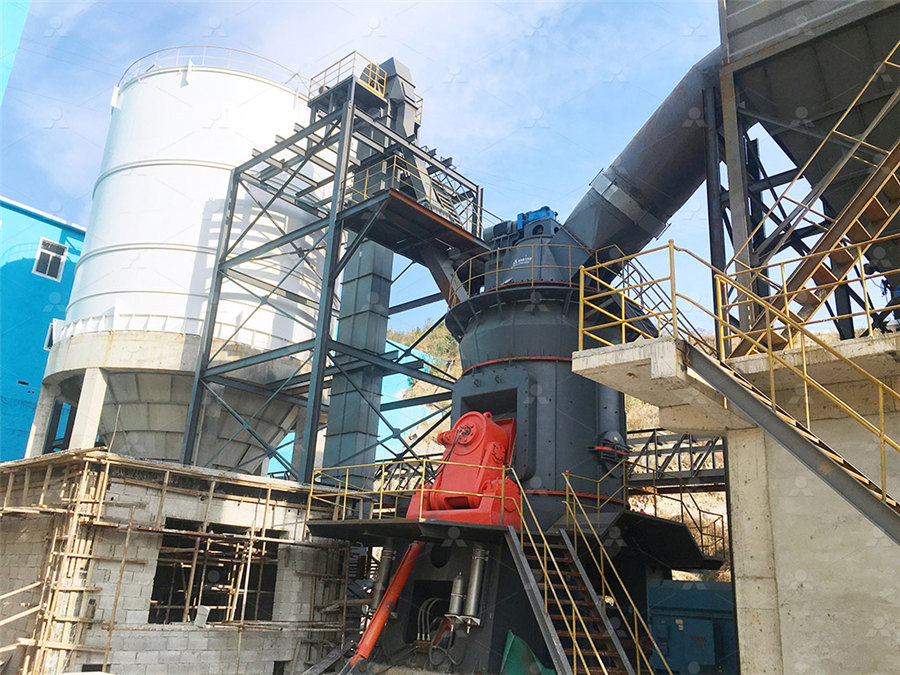
Effects of Mill Speed and Air Classifier Speed on Performance of
2021年6月29日 Nowadays, ball mills are widely used in cement plants to grind clinker and gypsum to produce cement The research focuses on the mill speed as well as air classifier speed effect on the two OPTIMUM BALL MILL SETUP The success of a ball milling application depends on the correct selection of accessories and process parameters This includes jar sizes, jar materials, ball sizes, number of balls, particle size, material fill level, speed Three rules for the optimum ball mill setup RETSCH