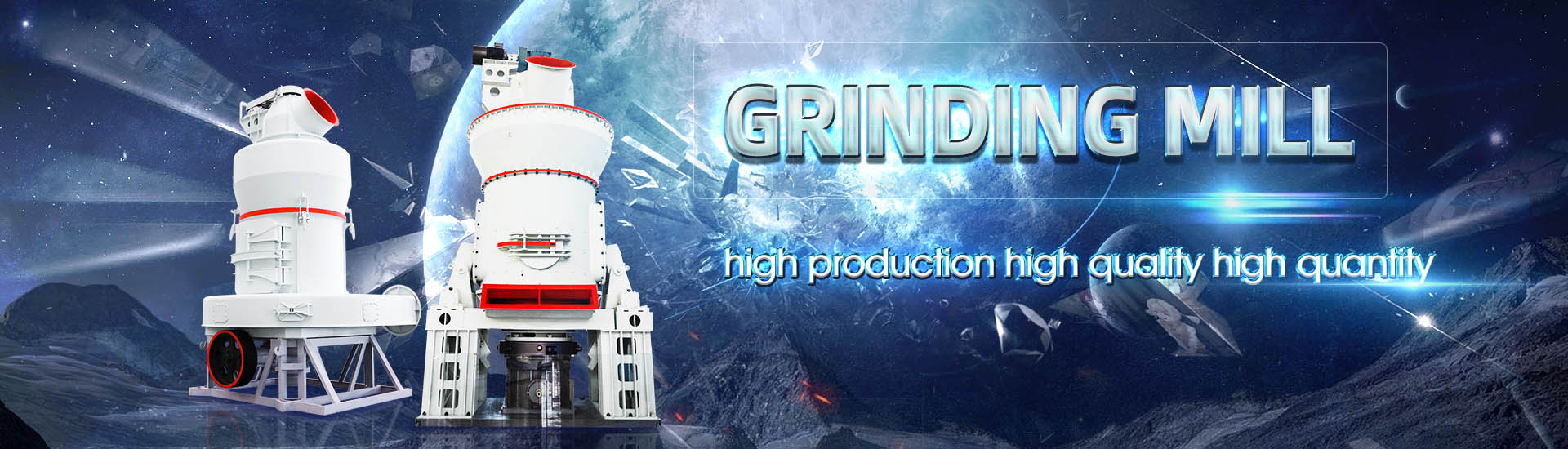
Slag vertical mill cooling water circulation system
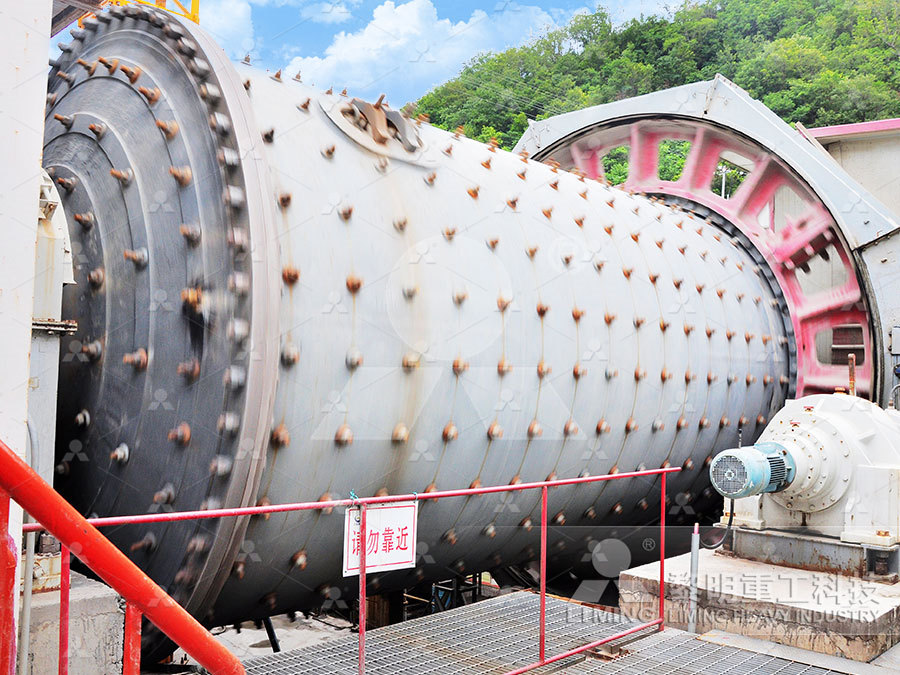
Breaking boundaries in slag waste heat recovery: Review and
2024年11月1日 The maximum cooling rate reached 2400 ℃/min to ensure the investigation of BFS crystallization The local heat transfer coefficient, average cooling rates and crystalline Contribute to sbm2023/sbm development by creating an account on GitHubsbm/sbm slag vertical mill cooling water circulation systemmd at 2019年8月9日 With a waste heat recovery and utilization system involving water cooled slag being discharged from a 400 t/h CFB (Circulating Fluidized Bed) boiler serving as a prototype, Slag Cooler Waste Heat Supply System and Energy Saving Analysis2014年2月19日 The slag undergoes accelerated cooling under controlled water flow, thus forming vitreous solidified slag sand The most popular process for hot stage slag treatment of Current Development of Slag Valorisation in China
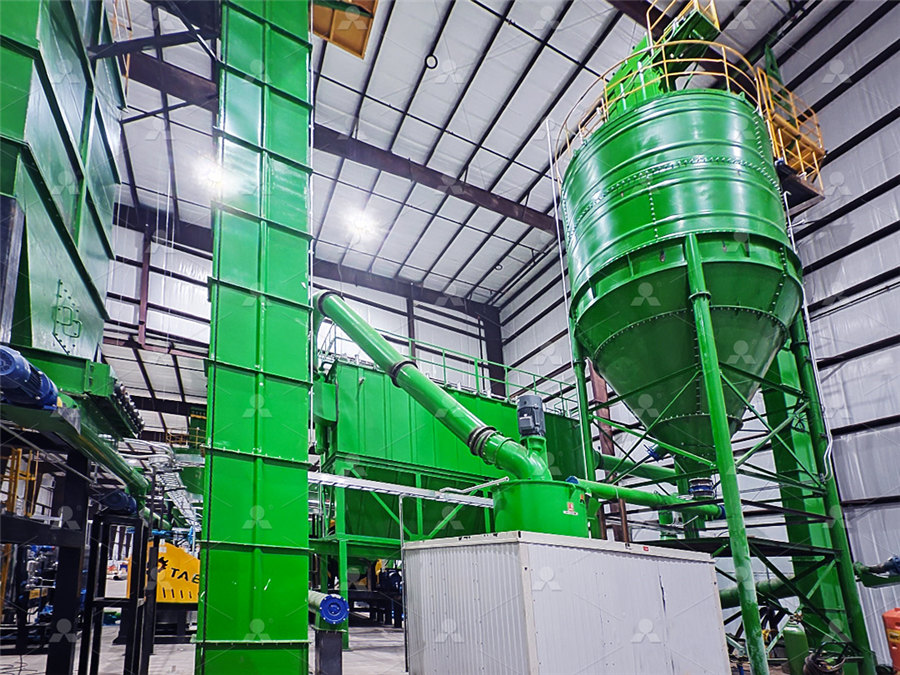
Dry Slag Granulation – The Future Way to Granulate Blast Furnace
2023年9月6日 • When slag is quenched with water, the high energy potential of the hot liquid slag is wasted (heating and evaporation of water • For granulation, the circulated water has to First of all, the slowcooling of copper slag in slag ladle is an extremely complex process, which can be divided into two stages of aircooling and forced cooling with water from the Numerical simulation for heat transfer behavior of copper slag 2007年11月1日 After 25 years of mainly producing slag cement, the vertical roller mill MPS 3750 C near Hannover and supplied by Gebr Pfeiffer AG was equipped with a modern outer MPS vertical roller mills for slag and slag cementsMilling and froth flotation methods are quite common when dealing with slowcooled slags Before flotation, the slag needs to be cooled in a controlled manner There are multiple options for Effect of Cooling Rate and Slag Modification on the Copper Matte
.jpg)
Process Concept for the Dry Recovery of Thermal Energy of Liquid
2021年6月24日 The heat exchangers extract thermal energy from the slag and transfer it to water or oil The first module cools the slag from the tapping temperature of about 1500 °C 2024年7月1日 Physical recovery of waste heat from blast furnace slag (BFS) by a moving bed is a promising solution The heat recovery of BFS is mainly achieved through gas–solid heat Waste heat recovery of blast furnace slag in moving bed: 2 The power consumption of vertical mill system is 20% lower than ball mill For many cement enterprises, the high energy consumption of ball mill system is such a big headache But the new type of vertical mill is a kind of energysaving and environmentfriendly grinding equipment Compared with ball mill system, vertical mill can save 30%50 Steel Slag Vertical Mill CHAENGcontroller (Eurotherm, Ashburn, VA, USA) The vertical furnacewas equipped with four (4) silicon carbide (SiC) heating elements The working tube was made of impervious pure alumina (AL 23; Friatec AG, Germany) with dimensions of 45/38mmOD/IDOntopofthefurnace,afurnaceheadwitha watercooling system included an inlet for an Stype Pt/PtEffect of Cooling Rate and Slag Modification on the Copper Matte
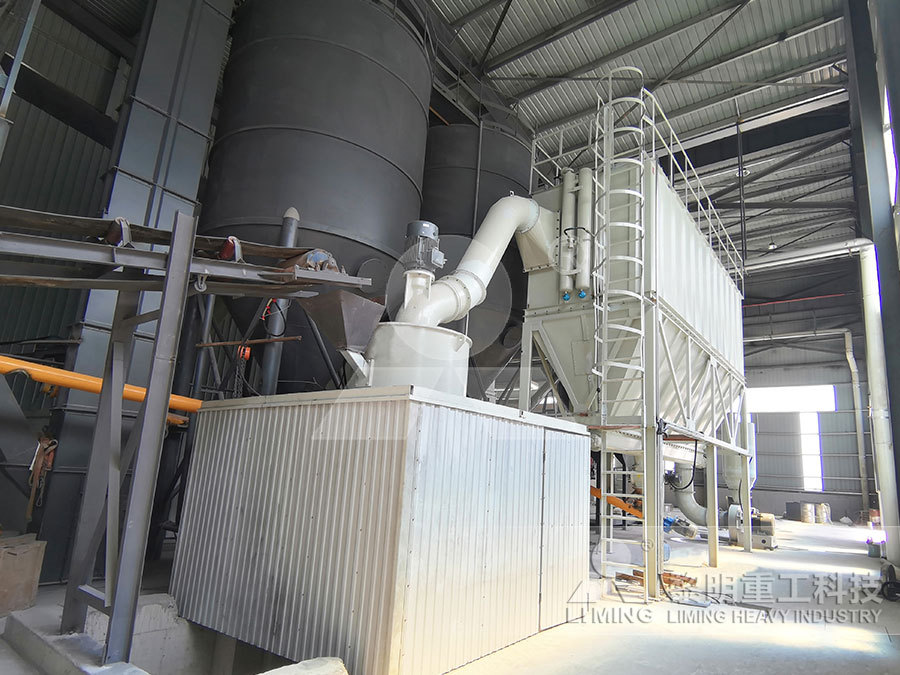
Cooling Water Circulation Equipment [For Device
Cooling Water Circulation Equipment [For Device Cooling] RKS JM Series MidGrade Model, Compact Chiller with BuiltIn Water Tank ORION can propose a system that meets your application needs We are always available for Advanced technology system: a Vertical mill can adopt external cycle process, Raymond mill can not use external cycle process b The position of the main motor, air inlet, air outlet, feed port and slag discharge port can be adjusted according to the requirements of the and can also use thin oil circulation cooling and lubrication, What is the difference between vertical mill and Raymond mill?At present, we can produce the supporting raw material vertical mill, coal vertical mill, and cement vertical mill that can cater to 3005000 t/d cement production line, and the series slag vertical mills with annual production capacity of 02 million tons, 03 million, 045million tons, 06 million rons,09 million tons and 12million tonsslag grinding plant,vertical roller mill,slag mill,grinding millTRM Slag grinding system is one fan grinding system Slag is fed to vertical roller mill by belt conveyor and through double air clock valve With rotation of grinding table, slag is brought from ring will be rejected to external circulation system After metal separation, it will, together with new feed slag, be fed to verticalTRM SERIES SLAG VERTICAL ROLLER MILL TRM SERIES SLAG
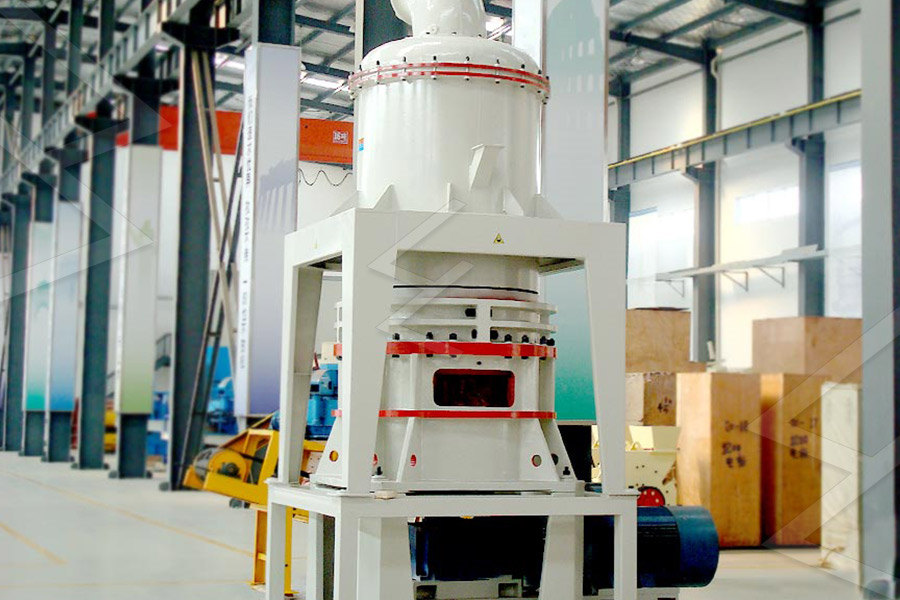
Dry Slag Granulation – The Future Way to Granulate Blast Furnace Slag
2023年9月6日 • When slag is quenched with water, the high energy potential of the hot liquid slag is wasted (heating and evaporation of water • For granulation, the circulated water has to be recooled in cooling towers or with other cooling methods Mainly cooling towers are equipped with electrically powered fans and also the cooling water circulationIn a closed recirculating water system, water circulates within a closed loop, continuously moving through the system and undergoing cooling or heating processes before being reused Closed recirculating cooling systems optimize industrial processes while reducing water consumption and environmental impacts, and play a key role in sustainable water managementWater Handbook Closed Recirculating Cooling Systems Veolia2001年5月15日 Using compatible chemicals that come in contact with the mill coolant also will make the process more predictable Thorough system cleaning before charging also will benefit you Finally, a comprehensive system maintenance plan not only includes a review of existing situations but also implements necessary changes with followupMill coolant system design The FabricatorWater cooling The cases of water cooling were simulated in the same manner as air cooled cases, with an additional variable of the water spraying rate G [kg/(m2∙s)]InNumerical modelling of slag cooling ResearchGate
.jpg)
Slag System an overview ScienceDirect Topics
Pyrometallurgical options for recycling spent lithiumion batteries: A comprehensive review Brian Makuza, Dawei Yu, in Journal of Power Sources, 2021 3221 Smelting slag system design Slag system design is vital for a successful smelting operation [34]The most commonly used slag system is CaO–SiO 2 –Al 2 O 3, in which SiO 2, along with CaO, is chosen as a slag former, Study of the circulation theory of the cooling system in vertical evaporative cooling generator 361 away by cooling water, and the coolant’s inner energy, specific volume and kinetic energy decrease 13 Descending pipe ()22 44 33 4 3 4 3 1 2 qu−∆ =pv−pv+gz−z+ c−cStudy of the circulation theory of the cooling system in vertical 2007年2月1日 Granulated blast furnace slag is moist, abrasive, fine grained and difficult to grind It also needs to be ground very finely There are several grinding systems on the market meeting the requirements for slag grinding, but no other grinding system has gained so much importance during the last decade as the vertical roller mill Polysius roller Slag grinding with the Polysius Roller Mill in ChinaThe document discusses Gebr Pfeiffer AG's MPS vertical roller mills for grinding slag and their effectiveness It notes that since 1980, an MPS 3750 C mill in Hannover has been producing cement with 4080% slag content Currently an MPS 5600 BC able to produce 120t/h of slag at 5000cm2/g fineness is being installed The MPS series uses a 3roller system and classifier to 2006 Slag Grinding With MPS Vertical Roller Mills PDF Mill
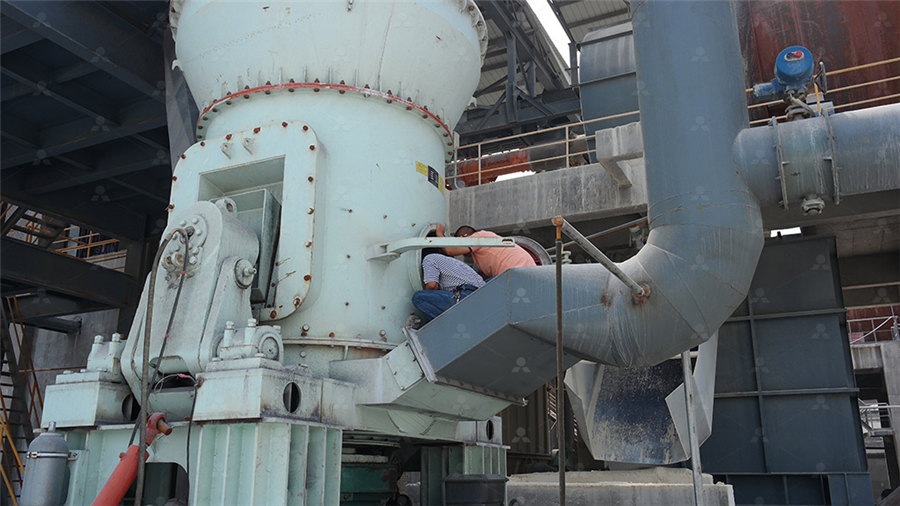
Efficient and reliable handling of GBFS and GGBFS at Global Slag
2008年3月3日 After the slag is ground, typically in a vertical mill, the finished material generally known as GGBFS must be raised to silo storage before blending or direct dispatch The handling characteristics of the ground slag are very similar to that of finished cement and in this situation Aumund is able to use the BWGtype belt bucket elevatorsa Loesche mill, with a grinding track diameter of only 11 metres, was used as long ago as 1935 However, the breakthrough in grinding this type of material on the vertical roller mill did not take place until the beginning of the 1990’s 1935 The first Loesche mill for grinding cement clinker, an LM 11, was commissioned in Joao Pessao, Brazil2 µm 5 µm Loesche2020年7月31日 The amount of copper flash smelting slag has increased during the recent years along with an increasing slagtometal ratio During slag tapping, some copper sulfide is mechanically entrained As a result, it is necessary to recover copper matte from the slag by suitable methods At present, the most common way is slow, controlled cooling in a transfer Effect of Cooling Rate and Slag Modification on the Copper HCMilling(Guilin Hongcheng) provides exclusive Water Slag Vertical Roller Mill equipment with customers for grinding Water Slag powder It is a kind of advanced pulverizing equipment integrated with drying, pulverizing, powder selecting and conveying Its fineness can achieve 200325 mesh (7544μm) The production capacity is 5200T/H It is applied as a good solution to Water Slag HLM Vertical Roller Mill
.jpg)
Optimize Flow with Coolant Circulation Systems by
Optimal Circulation for Closed or Open Style WaterCooling Systems EMSCO Coolant Circulation Systems (Pump Modules) are engineered to support the circulation of closed and open style watercooling systems Installation and Common cooling water issues Cooling water has many enemies Sometimes they work alone In other instances, they team up and compound the problem For example, algae growth creates the perfect environment for corrosion to take hold Here’s a quick look at the major sources of cooling water fouling Scale and scalelike deposits include calciumThe Cooling Water Handbook Buckmancontroller (Eurotherm, Ashburn, VA, USA) The vertical furnacewas equipped with four (4) silicon carbide (SiC) heating elements The working tube was made of impervious pure alumina (AL 23; Friatec AG, Germany) with dimensions of 45/38mmOD/IDOntopofthefurnace,afurnaceheadwitha watercooling system included an inlet for an Stype Pt/PtEffect of Cooling Rate and Slag Modification on the Copper Matte 2023年1月10日 As the core equipment in the production process of slag grinding, the LM slag vertical roller mill of SBM integrates fine crushing, grinding, drying, powder selection and transportation, ensuring the continuity and stability of slag powder production and improving the efficiency of slag grinding 1Slag Vertical Roller Mill
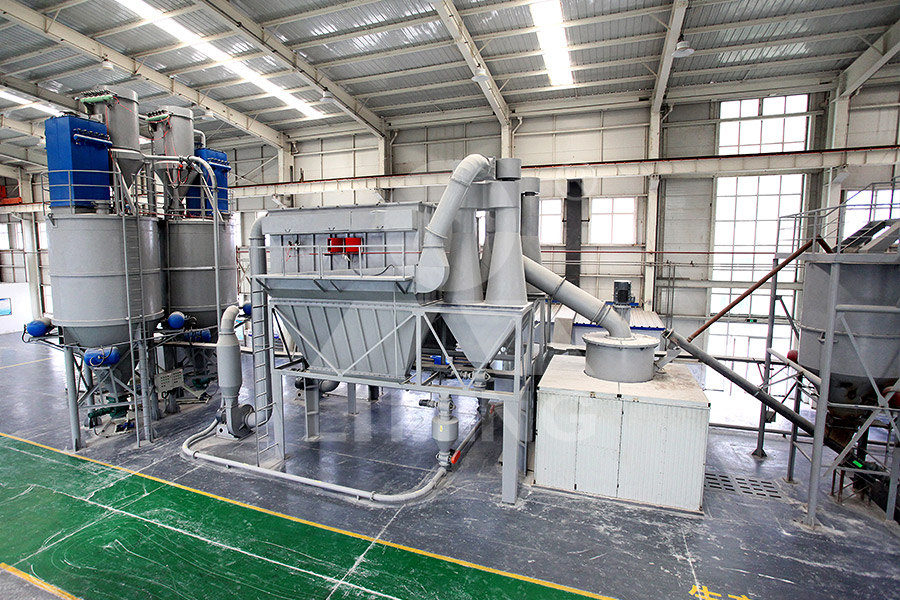
Cement grinding Vertical roller mills VS ball mills
Vertical roller mills and ball mills represent two clearly distinct technologies However, with proper adjustments to the operational parameters of the vertical roller mill almost identical cement properties can be achieved by the two mills that satisfy the cement user’s demandsNevertheless, the two types of mills have their distinctive merits2007年11月1日 The first industrialscale vertical roller mill for slag cement, an MPS 3750 C, went into operation in Hannover 25 years ago 1 and is still in operation today (Figure 3) The capacity of this mill ranges from 60t/h slag with 4100cm²/g to 70t/h CEM III A or 45t/h CEM III B with slag content between 50–80% and fineness of 3600cm²/g and 4300cm²/gMPS vertical roller mills for slag and slag cements%PDF14 %âãÏÓ 1527 0 obj > endobj 1561 0 obj >/Encrypt 1528 0 R/Filter/FlateDecode/ID[0AD3D0BE256B4BDCBFD60B44F>8E724C755FB6EB1D8021AB3C19>]/Index PROCESS OPTIMISATION FOR LOESCHE GRINDING PLANTSIn order to speed up the recycling of water slag, the use of water slag vertical grinding machine powder equipment can widely improve the resource utilization rate of water slag, and create profits and market value for enterprisesThe traditional cement production process is to mix the cement clinker and some mixed materials including water slag into the ball mill for grindingWhat is water slag, and the characteristics of water slag vertical mill
.jpg)
Effect of Cooling Rate and Slag Modification on the Copper Matte
2020年7月31日 Typical analysis process of the polished copper slag cross sections: (a) macrograph of the sectioned crucible, (b) vertical crosssection of the crucible, and (c) microstructure of the slagGrinding Rollers: Grinding roller is the main part for crushing and grinding materials The grinding roller is composed of cast steel roller sleeve, forging shaft and wearresistant surfacing bushing The grinding roller is installed on the rocker arm of the water slag vertical roller mill, under the action of external force, it is pressed tightly on the material of the grinding table, as the Water slag vertical roller mill2 The power consumption of vertical mill system is 20% lower than ball mill For many cement enterprises, the high energy consumption of ball mill system is such a big headache But the new type of vertical mill is a kind of energysaving and environmentfriendly grinding equipment Compared with ball mill system, vertical mill can save 30%50 Steel Slag Vertical Mill CHAENGcontroller (Eurotherm, Ashburn, VA, USA) The vertical furnacewas equipped with four (4) silicon carbide (SiC) heating elements The working tube was made of impervious pure alumina (AL 23; Friatec AG, Germany) with dimensions of 45/38mmOD/IDOntopofthefurnace,afurnaceheadwitha watercooling system included an inlet for an Stype Pt/PtEffect of Cooling Rate and Slag Modification on the Copper Matte
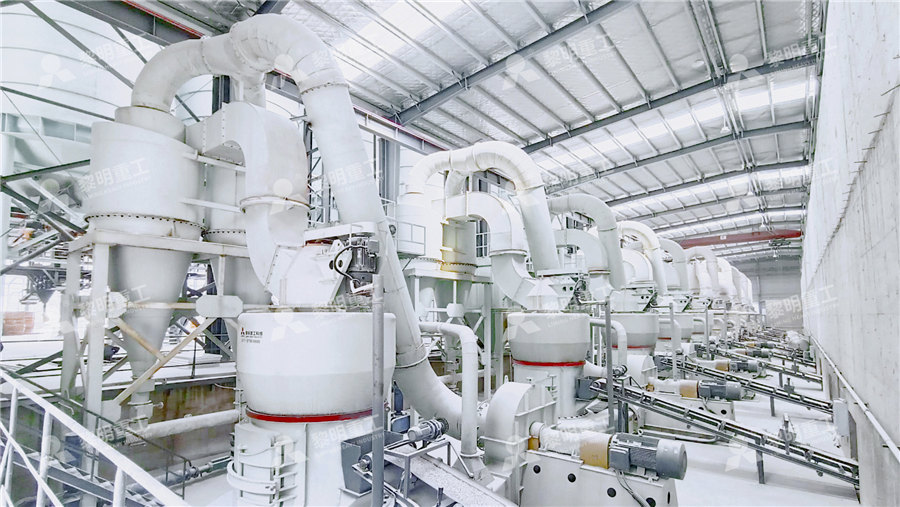
Cooling Water Circulation Equipment [For Device
Cooling Water Circulation Equipment [For Device Cooling] RKS JM Series MidGrade Model, Compact Chiller with BuiltIn Water Tank ORION can propose a system that meets your application needs We are always available for Advanced technology system: a Vertical mill can adopt external cycle process, Raymond mill can not use external cycle process b The position of the main motor, air inlet, air outlet, feed port and slag discharge port can be adjusted according to the requirements of the and can also use thin oil circulation cooling and lubrication, What is the difference between vertical mill and Raymond mill?At present, we can produce the supporting raw material vertical mill, coal vertical mill, and cement vertical mill that can cater to 3005000 t/d cement production line, and the series slag vertical mills with annual production capacity of 02 million tons, 03 million, 045million tons, 06 million rons,09 million tons and 12million tonsslag grinding plant,vertical roller mill,slag mill,grinding millTRM Slag grinding system is one fan grinding system Slag is fed to vertical roller mill by belt conveyor and through double air clock valve With rotation of grinding table, slag is brought from ring will be rejected to external circulation system After metal separation, it will, together with new feed slag, be fed to verticalTRM SERIES SLAG VERTICAL ROLLER MILL TRM SERIES SLAG
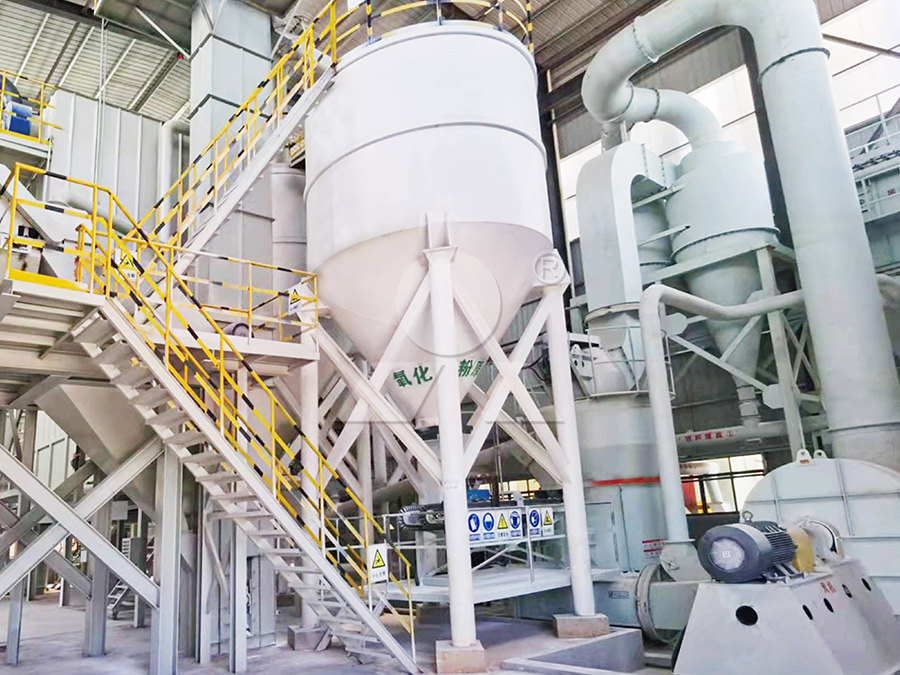
Dry Slag Granulation – The Future Way to Granulate Blast Furnace Slag
2023年9月6日 • When slag is quenched with water, the high energy potential of the hot liquid slag is wasted (heating and evaporation of water • For granulation, the circulated water has to be recooled in cooling towers or with other cooling methods Mainly cooling towers are equipped with electrically powered fans and also the cooling water circulationIn a closed recirculating water system, water circulates within a closed loop, continuously moving through the system and undergoing cooling or heating processes before being reused Closed recirculating cooling systems optimize industrial processes while reducing water consumption and environmental impacts, and play a key role in sustainable water managementWater Handbook Closed Recirculating Cooling Systems Veolia2001年5月15日 Using compatible chemicals that come in contact with the mill coolant also will make the process more predictable Thorough system cleaning before charging also will benefit you Finally, a comprehensive system maintenance plan not only includes a review of existing situations but also implements necessary changes with followupMill coolant system design The Fabricator