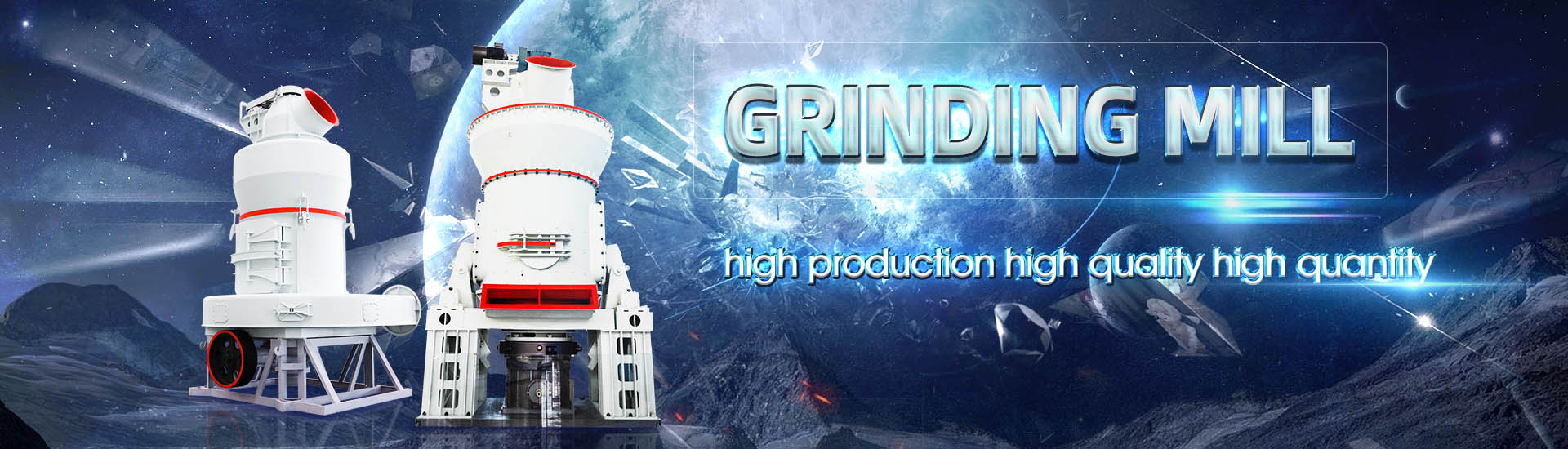
What is the general diameter of the coal output from the coal mill
.jpg)
Coal Mill an overview ScienceDirect Topics
Coal mills or pulverizers play a very essential part in the coalfired power production system Coal mills grind the coal into fine powder, and the primary air entering the mill dries and drives the coal into the power plant furnace for combustion Mills can be a bottleneck for the power generation The first is that the CO 2 concentration in the flue gas is noticeably higher in a cement plant (Cement Plant2019年5月8日 • Heat input per burner is assumed to be to 75 MW for a low slagging coal and 40 MW for a severely slagging coal, With intermediate values for intermediate slagging potentials TPS Coal Mills and Fan Performance PPT SlideShare2012年11月17日 The document discusses coal mill/pulverizers used in thermal power plants It describes how pulverized coal is dried, ground, circulated, and classified within the mill to Coal mill pulverizer in thermal power plants PPT SlideShare
.jpg)
Pulveriser Mill Performance Analysis Optimisation in Super
In both systems, the air is admitted below the pulverizer bowl into an area known as the mill side The mill side is at a positive gauge pressure as air is supplied by a primary air (PA) fan From Coal mill is an important component of the thermal power plant It is used to grind and dry the moisturized raw coal and transport the pulverized coal – air mixture to the boiler Poor dynamic Modeling and Control of Coal Mill2012年1月23日 • General Capacity of A Coal Mill : 15 – 25 tons/hour • Power Consumption: 200 – 350 kW Performance Calculations • Several performance parameters are calculated for the PERFORMANCE ANALYSIS OF COAL MILLS SlideServeThe paper presents development and validation of coal mill model (including the action of classifier) to be used for improved coal mill control The model is developed by using the mass (PDF) Modeling and Control of Coal Mill Academia
.jpg)
An investigation of performance characteristics and energetic
2020年8月12日 Obtained results indicate that grinding pressure, primary air (PA) temperature and mill motor current have a tendency to rise by increasing coal feeding mass flow rates for 2009年9月20日 This paper presents a novel coal mill modeling technique using genetic algorithms (GAs) based on routine operation data measured onsite at a National Power (NP) Modeling and Parameter Identification of Coal Mill ResearchGate2015年11月1日 Coal mills are bottleneck in coal–fired power generation process due to difficulty in developing efficient controls and faults occurring inside the mills In this paper, a dynamic A unified thermomechanical model for coal mill operationLargediameter boreholes Smalldiameter core holes give very little indication of the differences in washability for different size fractions, how the material will break with handling and crushing, and if crushing will liberate more coal Largediameter cores are often drilled to obtain such information, which is particularlySampling the coal chain SciELO
CFB石灰石脱硫剂制备64.jpg)
Typical layout of the coalfired power plant
Download scientific diagram Typical layout of the coalfired power plant from publication: Using Energy and Exergy Analysis to Compare Different CoalFired Power Plants This study compared coal seam is always to leave the coal in the ground and extract it later if prices are assumed to be likely to increase The owner of a seam with extraction cost c per ton should delay mining as long as E(pt+1 −c) ≥(pt −c)(1+r) (1) where pt is the price of coal in year t, and r is the rate of return on capital (pt – c) is the amountCoal and the Industrial Revolution, 17401869 UC DavisInput and Output constraints of MPC for pulverised coal flow control REFERENCES Parameter Input Raw coal flow Output Pulverised coal flow Minimum 0 kg/sec Maximum 10 kg/sec 0 kg/sec 8 kg/sec FanG, NRees, “Modelling of vertice spindle mills in coal fired power plants,” Proceedings of electrical engineering congress, 1994 HwiBeom Shin, XinlanLi, InYoung (PDF) Modeling and Control of Coal Mill Academia2022年2月24日 The study reveals that the lowest specific energy consumption is achieved when the relative rotational speed of the mill is between 081 and 087; the weighted average diameter of the balls ranges Improving the efficiency of the coal grinding process in ball drum
.jpg)
What is Core? Coal, Kentucky Geological Survey, University of
2023年1月5日 The diameter of cores ranges from 1 to 35 inches, depending on the drill bit used Standard coal exploration cores are usually 25 to 35 inches in width The length of core obtained depends on the type of information needed Typical coal exploration core Back to "Coal Logging Home"The direct cost of coal grinding is a function of the wear and tear of the powdered coal mill , which in turn is influenced by the expected particle size spectrum of the coal dust and thus of the mill settings, eg hopper load, mill speed and separator adjustment Therefore, a costPowerGen 2008, Orlando, USA Online measurement of coal fineness 2020年10月1日 In the past 30 years, more than 70% of China’s primary energy consumption annually was the coal (Tang et al, 2017)It is already acknowledged that the cause of PM 25 can be attributed mostly to the large amount of coal consumption (Wang et al, 2017a)Furthermore, the continuous high dependence on coal also leads China to being the largest carbon emitter, Unraveling effects of coal output cut policy on air pollution abatement 2015年7月1日 The Australia coal preparation industry, in particular, has developed a variety of coal preparation technologies that have been adopted by the global fleet Some of the most important of these innovations include highcapacity multislope (banana) screens, largediameter dense medium cyclones, and highefficiency hydraulic classifiers [4], [5]A review of stateoftheart processing operations in coal preparation
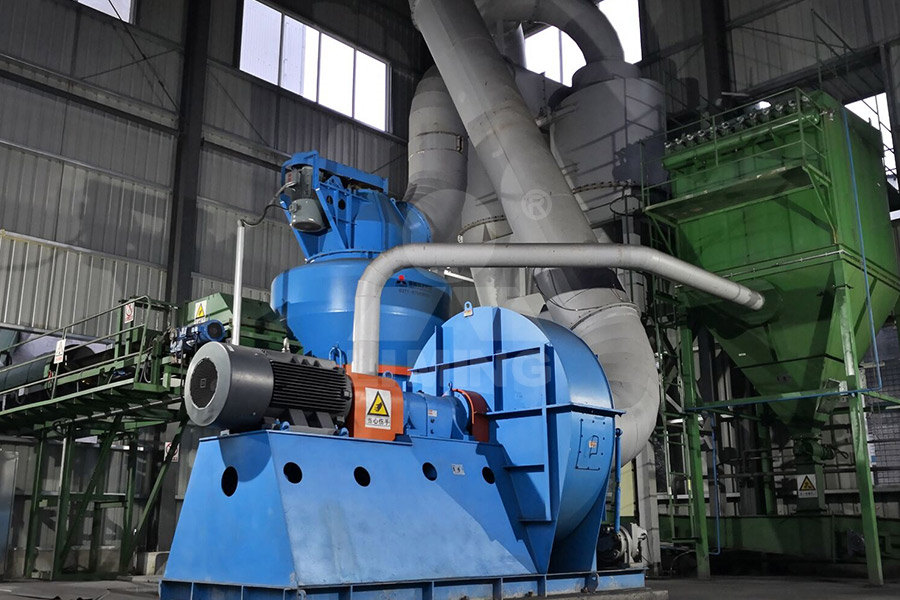
Understanding Coal Sizes Bull's Supply
2023年9月11日 Anthracite coal is available in various sizes, each catering to specific needs and heating appliances In this article, we'll explore the different sizes of anthracite coal and the applications they are best suited for 1 Pea Coal: Pea coal is one of the smallest sizes of anthracite coal, typically ranging from 13/16 to 9/16 inches in diameter2021年8月1日 pressure is not less than 28Mpa(5)Low quality coal causes insu fficient output of coal mill Fault treatment and improvement and Optimization: (1) check the operation status of primary fan,(PDF) Fault analysis and optimization technology of HP2006年1月1日 If these particles are small enough they will be lifted through and into the power plant furnace by the primary air flow, since these particles are too heavy 2 THE COAL MILL The work presented in this paper, is based on a Babcock MPS 212 coal mill used at Elsam's Nordjyllandsværktet Unit 3ESTIMATION OF MOISTURE CONTENT IN COAL IN COAL MILLS2020年8月12日 Ultimately, the energetic efficiency of coal mill has been investigated and performance value has been found to be a maximum value of 962% KEYWORDS: Vertical roller coal mill; energetic performance; coalfired power plant; Output Ci =: Coal inlet Co =: Coal outlet M =: Motor CLS =: Classifier Log in via your institutionAn investigation of performance characteristics and energetic
.jpg)
Review of control and fault diagnosis methods applied to coal
2015年8月1日 Mill problems originate mainly due to poor controls or faults occurring within the milling system As discussed by GQ Fan and NW Rees [3], the control of mills remains very simple in most of the power plants due to the fact that the mill system is highly nonlinear with strong coupling among the variables and it is very difficult to measure some important Coalfired power generation plants are most commonly based on pulverised coal combustion (PCC) systems, in which heat from combustion of the coal is used to raise high pressure superheated steam that drives a steam turbine generator Steam turbine plants have been in use for over a hundred years, and have reached supercritical conditions withUnderstanding coalfired power plant cycles ICSC2012年11月17日 20 131Fineness Fineness is an indicator of the quality of the pulverizer action Specifically, fineness is a measurement of the percentage of a coal sample that passes through a set of test sieves usually designated at 50, 100, and 200 mesh A 70% coal sample passing through a 200 mesh screen indicates optimum mill performance The mill wear and Coal mill pulverizer in thermal power plants PPT SlideShare2021年2月15日 Fig 2 General Cause and Effect Diagram of Output System of Under optimum conditions of +60 mm material suitable for a 100 mm ball diameter, The coal mill model was developed and the System dynamics model of output of ball mill ResearchGate
.jpg)
The influence of flow velocity on coal fines output and coal
2017年10月26日 Some very small coal fines, with a diameter in the range of 008–09 μm, are produced from the coal cores at the flow velocity of 0015 cm 3 /s, indicating that the very small coal fines can easily flow through the pore system of a coal core at a low fluid flow velocity, increasing the coal core permeability2020年3月1日 In a vertical coal mill, coal is often ground at the bottom of the classifier and then the pulverized coal particles are blown up to the rotating impeller mounted at the top So far, most of the experimental measurements and numerical simulations have been conducted only at a given inlet condition of the incoming twophase flow from the bottom of the air classifier [[29], Classification performance of model coal mill classifiers with Coal mills have a significant influence on the reliability, efficiency, and safe operation of a coalfired power plant Coal blockage is one of the main reasons for coal mill malfunctionThe monitoring indicator of coal mill under normal condition2021年3月11日 Answer:•the coal output has fluctuated from 1990 to 2000•there is an overall decline•the highest peak of the coal output was in 1993•lowest peak of coal output what is the general atmospheric condition of a dayDescribe the coal output from the sor range coalfied from
.jpg)
Operational parameters affecting the vertical roller mill
2016年9月1日 Furthermore, VRM separator speed (rpm) is one of the key operational parameters that determines product particle size Increasing the classi er rotor speed from 60 to 80 rpm decreases the particle 2022年12月1日 The test material was plates made of high manganese cast steel that acts as a beater on a MWk 12 (FPM SA Mikołów, Poland) beater mill for coal grinding (Fig 1)The diameter of the beater mill rotor was 2186 mm, 10 beaters were installedThe wear mechanism of mill beaters for coal grinding madeup from the pit of a surface mine is considered to be raw coal even when breaking and crushing facilities are provided in the pit 38 runofmine (ROM) coal—in the case of an underground mine, it is that coal delivered to the surface by a slope belt, hoist, etc In the case of a surface mine, it is that coal as it existsStandard Test Method for Performing the Sieve Analysis of Coal 2019年9月1日 Coal is generally found as coal seams and are formed through the metamorphic process, which subjects peat like deposits to physical and chemical changes following to increasing temperatures and pressures upon burial (Van Krevelen, 1993; Smith and Cook, 1980)The different degrees of pressure and heat over a time period causes the difference in Coal composition and structural variation with rank and its
.jpg)
(PDF) Particle Size Distribution Analysis of Ground Coal By
2012年9月24日 Particle sizes smaller than 9 pixels, which is about 17 µm equivalent diameter or smaller, vary with coal and mill types Machine vision methods based particle size distribution of ball and Section of coal bowl mill Table 1 Guaranteed coal conditions for mill performance evaluation Coal Moisture % 20 Coal HGI 55 Mill Outlet Temperarure °C 80 Mill Air Flow T/hr 102 Coal Fineness (% passing trough 200 mesh) 70% passing through 200 mesh and 90% passing through 50 mesh Differental Pressure 300 mmwc Coal Output from Mill 609 t/hrA Study on 500 MW Coal Fired Boiler Unit’s Bowl Mill HOW ELECTRICITY IS PRODUCED AT A COALFIRED POWER STATION An overview of power generation at a modern coalfired power station 221m in diameter and weighs a massive 259tons The operational pressure stages contributes to the total 618MW output of the generator The HP turbine delivers 154,5MW (25%), the IP turbine 278,1MW HOW ELECTRICITY IS PRODUCED AT A COALFIRED POWER mill level or inventory Therefore, the mill output is controlled by the mill’s rating damper; controlling the primary air to the mill By increasing the primary air through the mill, more coal can be transported The level of coal in the mill is maintained by the volumetric feeders In order to control the mill, a good indication forCombustion, Reliability, and Heat Rate Improvements through Mill
.jpg)
Study of the law of gradual change of the influence of hydraulic
2019年7月1日 Permeability enhancement of low permeability coal seams is a key tool in coal mine gas extraction and utilization Numerical investigations are used to analyze the geometric parameters of the Largediameter boreholes Smalldiameter core holes give very little indication of the differences in washability for different size fractions, how the material will break with handling and crushing, and if crushing will liberate more coal Largediameter cores are often drilled to obtain such information, which is particularlySampling the coal chain SciELODownload scientific diagram Typical layout of the coalfired power plant from publication: Using Energy and Exergy Analysis to Compare Different CoalFired Power Plants This study compared Typical layout of the coalfired power plantcoal seam is always to leave the coal in the ground and extract it later if prices are assumed to be likely to increase The owner of a seam with extraction cost c per ton should delay mining as long as E(pt+1 −c) ≥(pt −c)(1+r) (1) where pt is the price of coal in year t, and r is the rate of return on capital (pt – c) is the amountCoal and the Industrial Revolution, 17401869 UC Davis
.jpg)
(PDF) Modeling and Control of Coal Mill Academia
Input and Output constraints of MPC for pulverised coal flow control REFERENCES Parameter Input Raw coal flow Output Pulverised coal flow Minimum 0 kg/sec Maximum 10 kg/sec 0 kg/sec 8 kg/sec FanG, NRees, “Modelling of vertice spindle mills in coal fired power plants,” Proceedings of electrical engineering congress, 1994 HwiBeom Shin, XinlanLi, InYoung 2022年2月24日 The study reveals that the lowest specific energy consumption is achieved when the relative rotational speed of the mill is between 081 and 087; the weighted average diameter of the balls ranges Improving the efficiency of the coal grinding process in ball drum 2023年1月5日 The diameter of cores ranges from 1 to 35 inches, depending on the drill bit used Standard coal exploration cores are usually 25 to 35 inches in width The length of core obtained depends on the type of information needed Typical coal exploration core Back to "Coal Logging Home"What is Core? Coal, Kentucky Geological Survey, University of The direct cost of coal grinding is a function of the wear and tear of the powdered coal mill , which in turn is influenced by the expected particle size spectrum of the coal dust and thus of the mill settings, eg hopper load, mill speed and separator adjustment Therefore, a costPowerGen 2008, Orlando, USA Online measurement of coal fineness
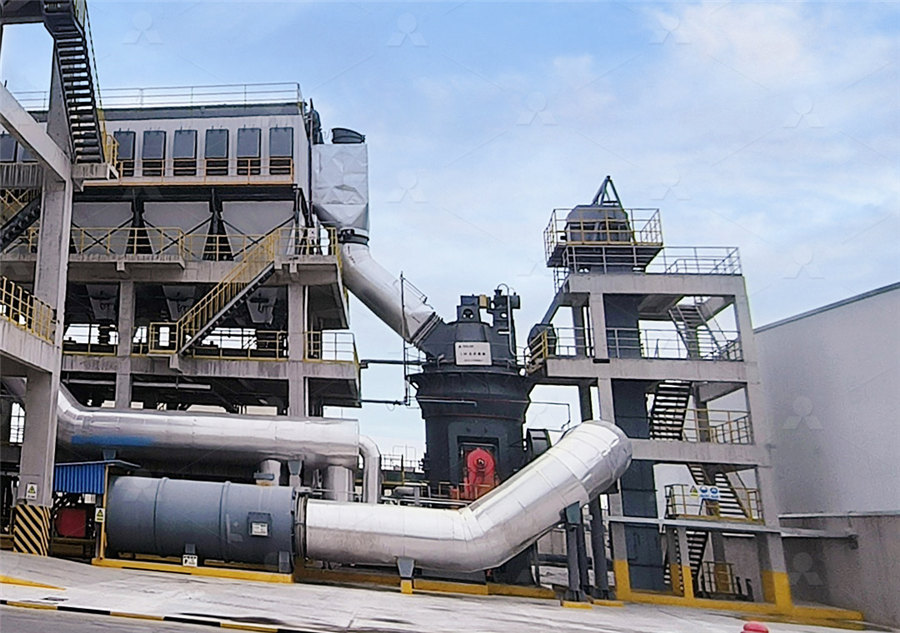
Unraveling effects of coal output cut policy on air pollution abatement
2020年10月1日 In the past 30 years, more than 70% of China’s primary energy consumption annually was the coal (Tang et al, 2017)It is already acknowledged that the cause of PM 25 can be attributed mostly to the large amount of coal consumption (Wang et al, 2017a)Furthermore, the continuous high dependence on coal also leads China to being the largest carbon emitter, 2015年7月1日 The Australia coal preparation industry, in particular, has developed a variety of coal preparation technologies that have been adopted by the global fleet Some of the most important of these innovations include highcapacity multislope (banana) screens, largediameter dense medium cyclones, and highefficiency hydraulic classifiers [4], [5]A review of stateoftheart processing operations in coal preparation 2023年9月11日 Anthracite coal is available in various sizes, each catering to specific needs and heating appliances In this article, we'll explore the different sizes of anthracite coal and the applications they are best suited for 1 Pea Coal: Pea coal is one of the smallest sizes of anthracite coal, typically ranging from 13/16 to 9/16 inches in diameterUnderstanding Coal Sizes Bull's Supply