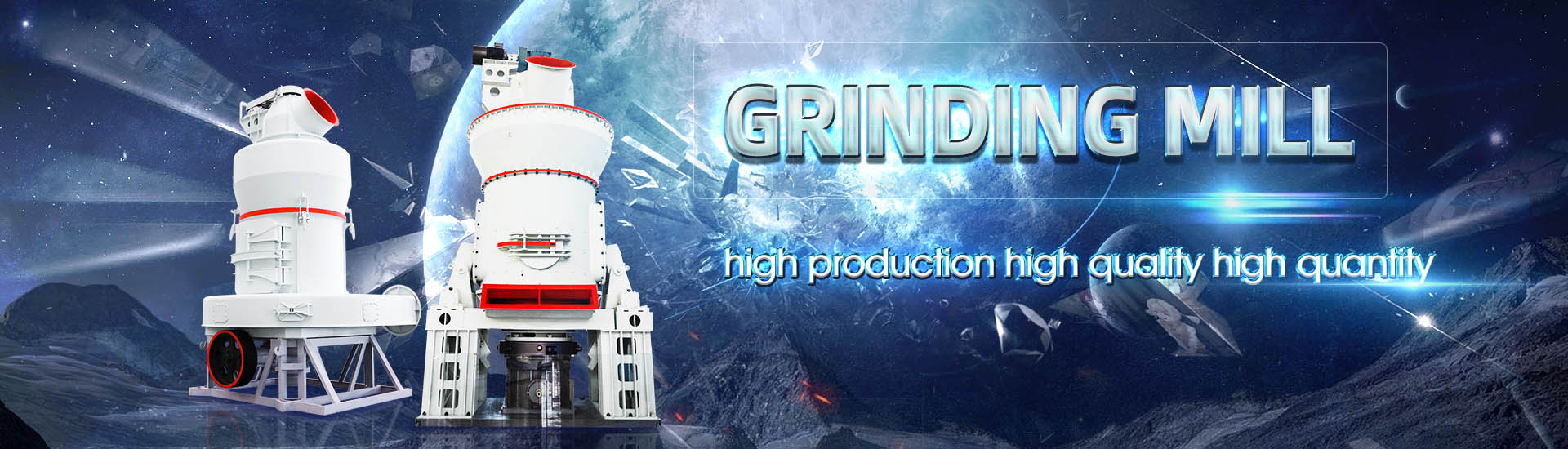
What are the danger sources of ore grinding mill
.jpg)
Environmental Protection Measures in the Grinding Production
2019年1月8日 Here is a brief introduction of how to take environmental protection measures to reduce the pollution of this mill production line First of all, for dust pollution, it is a The performance of a ball mill can be affected by a number of factors, including the type of ore being processed, the milling medium, and the milling speed The type of ore being processed Factors affecting ores grinding performance in ball mills2023年3月21日 An ore processing plant presents numerous safety hazards throughout its various stages of operation, including haulage, primary stockpiles, crushing, screening, Hazards associated with an ore processing Plant2020年6月17日 There is a clear link between duration of exposure to grinding environment and associated medical risk which begins as early as within the first 3 to 4 years without any Health risks associated with the grinding process ResearchGate

Understanding the operation of grinding mills in the mining and
1 Grindability: The grindability of the ore affects the efficiency of the grinding mill Harder ores require more energy and longer grinding times, which can impact the mill's performance and 2023年7月20日 There are several impact factors of the grinding operation (1) Structure parameters of grinding mill, including its specifications, model, aspect ratio, ore discharging Ore Grinding SpringerLink2014年2月1日 Mining techniques influence the distribution of mine operating costs Savings in milling costs will significantly affect total mine operating cost Coarse particle flotation may Mine operating costs and the potential impacts of energy and 2020年10月13日 Grinding is the highest energy consumer in all the unit processes of mineral beneficiation The performance of grinding mills depends on many operating factors among THE EFFECTS OF PROCESS VARIABLES ON THE GRINDING OF
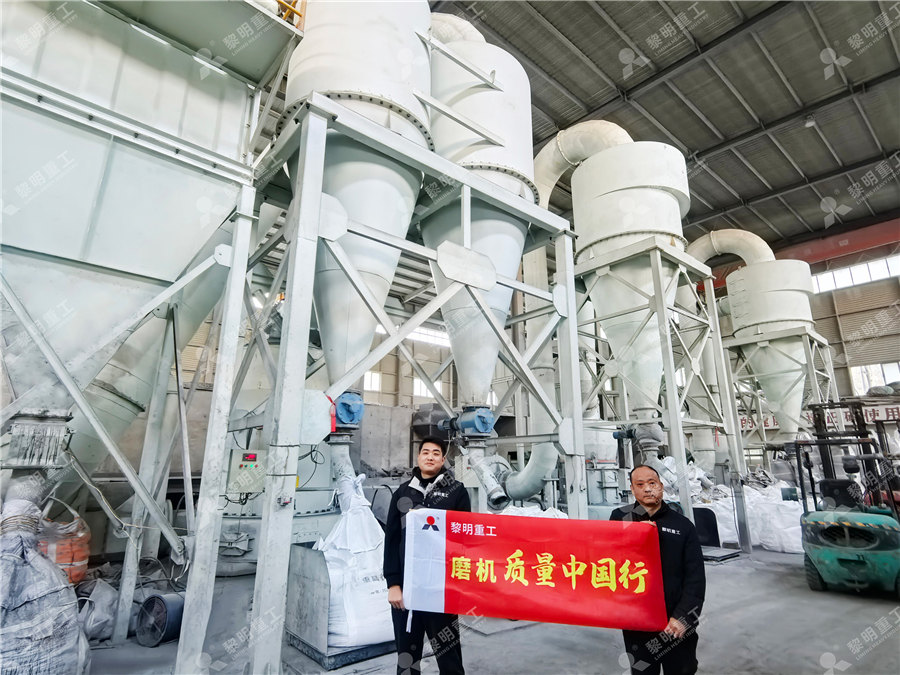
Grinding Hazards and Precautions HSE STUDY GUIDE
2023年9月15日 Here are some common grinding hazards: Flying Debris : The highspeed rotation of the grinding wheel can cause fragments to break off, posing a risk to your eyes 2020年10月13日 The results of the analyses clearly show that using a sieve of +180µm and its bottom180µm, the best time for grinding 05kg of Itakpe iron ore with 3kg of grinding media and a mill speed of 92 THE EFFECTS OF PROCESS VARIABLES ON THE GRINDING OF IRON ORE 2015年7月29日 As you increase the volume of the through put, the time that the ore has to react to the grinding media is lessened As you add ore to the mill you are also adding WATER and changing density which affects the slurry rheology and workings of the grinding action inside that mill This water is one of the main controls that you have over your grindEffect of Water Density on Grinding Mill 911MetallurgistEffect of mill type on ore grinding performance Ball mills are widely used in the mining and metallurgical industries for the grinding of ores and other materials There are a wide variety of mill types available, each with its own advantages and disadvantages The Factors affecting ores grinding performance in ball mills
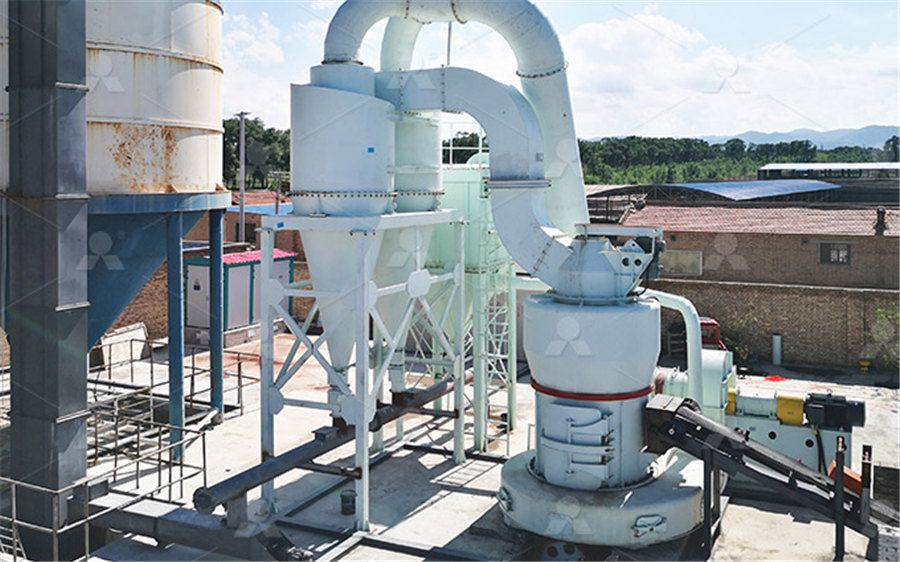
Understanding the operation of grinding mills in the mining and
1 Grindability: The grindability of the ore affects the efficiency of the grinding mill Harder ores require more energy and longer grinding times, which can impact the mill's performance and operational costs 2 Media andliner Wear: The condition of the grinding media and liners affects the mill's efficiencyThe Autogenous Mill, also known as AG Mill, is a type of grinding mill used in the mining industry This machine uses ore and rock itself as grinding media to perform its job Unlike other types of mills that use steel balls or rods for grinding materials, the Autogenous Mill relies on the material being ground to break itself into smaller piecesUnderstanding the SAG Mill in Copper Ore Mining Process2020年10月18日 An iron ore concentrate sample was ground separately in a pilotscale HPGR mill in multiple passes and a dry opencircuit ball mill to increase the specific surface area of particlesThe effects of iron ore concentrate grinding methods (HPGR and 2015年3月15日 For the grinding tests, a Loesche mill LM45 (table diameter 045 m) is used (Fig 2a) This pilot scale mill is a special development for ore grinding, which is reflected by several features The mill has four rollers, which are able to stress the particle bed with grinding pressures of up to 5000 kN/m 2Research of iron ore grinding in a verticalrollermill
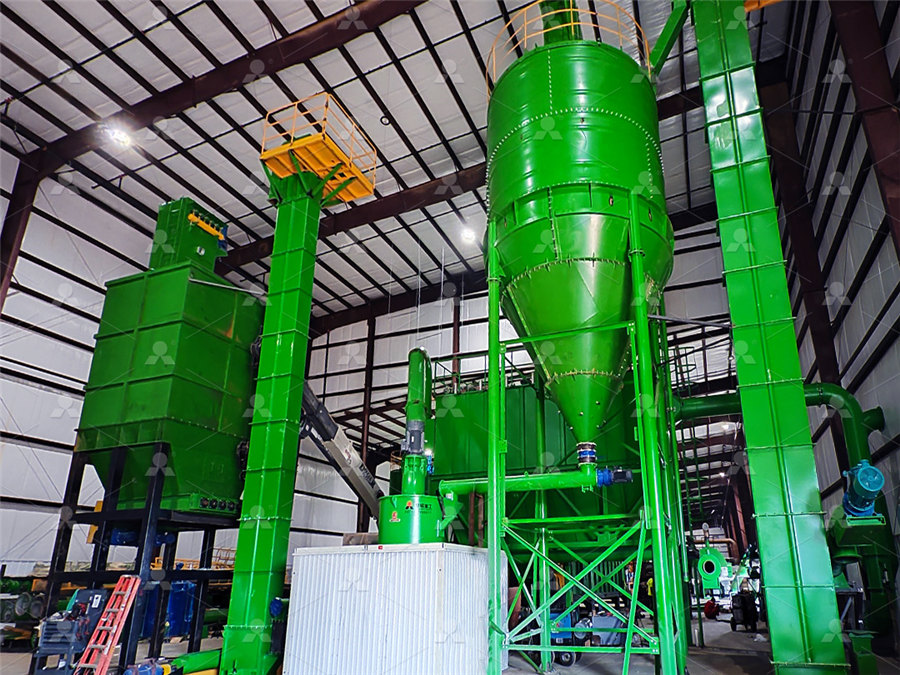
(PDF) Optimizing Grinding Time for Hematite Liberation in Iron Ores
The present work was used to find the total grinding retention time of each ore in the mill Based on the total retention time of each ore, the optimum grinding time for each ore was identified to obtain the desired P80 passing particle size with acceptable hematite liberationIn the mill, the mixture of medium, ore, and water, known as the mill charge, is intimately mixed, the medium comminuting the particles by any of the above methods Apart from laboratory testing, grinding in mineral processing is a continuous process, material being fed at a controlled rate into one end of the mill and discharging at the other end after a suitable dwell (residence) timeGrinding Mill an overview ScienceDirect Topics2016年1月1日 In wet grinding practice, highstress abrasion occurs over a small region when ore particles are trapped between the grinding balls and the mill liner, and the load is sufficient to fracture A comparison of wear rates of ball mill grinding mediaSuccessful inauguration of the New Steel Pilot Plant with a LOESCHE Ore Grinding Plant (OGPmobile) in Ouro Preto, MG, Brazil Ouro Preto – The company New Steel has developed a revolutionary new process for iron ore Mills for minerals and ores Loesche
.jpg)
Steadystate and dynamic simulation of a grinding mill using
2020年6月15日 Since grinding mills have a significant impact on the final economic performance of a mineral processing plant (McIvor and Finch, 1991, SosaBlanco et al, 2000), it is important to operate them at the point which will optimize the economic performance of the plant (Cramer, 2008, Matthews and Craig, 2013)Grinding mill processes are difficult to control as the control operated an ultra fine grinding (UFG) circuit to supplement its roaster capacity for the treatment of the refractory gold flotation concentrate A second UFG mill was installed in 2002 taking the total UFG capacity to over 20tph while grinding to 1112 microns and achieving over 90% gold recovery A development program in 2002/3 involving plantUltra Fine Grinding A Practical Alternative to Oxidative 2021年5月31日 Ore blending is an essential part of daily work in the concentrator Qualified ore dressing products can make the ore dressing more smoothly The existing ore blending modeling usually only (PDF) A Method of Ore Blending Based on the Quality of 2023年9月13日 To promote angle grinding safety, safety measures must be put in place to control the danger these sparks pose If you are working in the vicinity of flammable or explosive substances, there is a serious risk of these sparks creating a fire or explosion in the workplace if the correct safety precautions aren’t takenGrinding Hazards What are the Dangers of Grinding Wheels?
.jpg)
The effects of ore blending on comminution behaviour and
2018年8月17日 The concept of ore blending is a very relevant notion in modern high tonnage production mines It is not only essential for the prolongation of the mine life of the concerned mine but as well as a Download scientific diagram Corn grinding mill modified for ore grinding from publication: Sustainable smallscale gold mining in Ghana: Setting and strategies for sustainability In Ghana Corn grinding mill modified for ore grindingGrinding media gets consumed during grinding and poses a danger of contamination in subsequent processes The specific consumption of grinding media depends on the microstructure of the media, the Grinding Media in Ball MillsA Review ResearchGate2023年10月17日 Factors for choosing a suitable ore powder grinding mill 1 Raw material characteristics: Different raw materials have different hardness, humidity and grinding and crushing properties, and the corresponding ore powder grinding mill needs to be selected to meet the processing requirements 2 Production capacity: Determine the required processing How to choose a suitable ore powder grinding mill?
.jpg)
Effect of grinding media on the milling efficiency of a ball mill
2022年1月1日 The size of grinding media is the primary factor that affects the overall milling efficiency of a ball mill (eg power consumption and particle size breakage)2022年12月31日 OPTIMIZATION OF LATERITE ORE GRINDING PROCESS USING BALL MILL WITH RESPONSE SURFACE METHOD December 2022; Metalurgi 37(3) Source DF Sum of squares Mean square F Value P OPTIMIZATION OF LATERITE ORE GRINDING from the ores The grinding of ore is a highly energyintensive process [1–4] In this process, the size of the particle obtained depends on the energy consumption of the ball mill The major challenge encountered in the process of iron ore grinding is to maintain the desired product particle size distribution (PSD) with sufficientEstimation of Grinding Time for Desired Particle Size Distributionfrom the ores The grinding of ore is a highly energyintensive process [1–4] In this process, the size of the particle obtained depends on the energy consumption of the ball mill The major challenge encountered in the process of iron ore grinding is to maintain the desired product particle size distribution (PSD) with sufficientEstimation of Grinding Time for Desired Particle Size Distribution
.jpg)
Electric Drives for Large Ore Grinding Mills 911Metallurgist
2019年4月19日 Ore grinding mills are really just slowly rotating barrels, or some 60% of the 200 megawatts supplied to a large iron ore concentrator, are for grinding Mill Power Transmission Arrangements Softstart of a large mill drive is a must for either utility or selfgeneration source of power At new ore locations, 2021年1月14日 standard Bond crushing, and rod mill work indices, abrasion indices and by Dawson for Bond Ball Mill Work Index tests using crushed feed, and Standard Autogenous Grinding Design (SAGDesign) Tests, patented by Outokumpu (See reference 8 below) The comparison of these results gives context to how the various measurements relate to eachComparison of Ore Hardness Measurements for Grinding Mill The performance of grinding mills depends on many operating factors among which are the time of grinding, mill speed, grinding mediatoore ratio, and filling ratioEffect of Grinding MediaOre Ratio Download Scientific Diagram2015年4月9日 Some mills are compartmentalized with each subsequent section having a smaller ball size The material can pass through to the proceeding section, but the balls cannot This ensures that the smaller particles are attacked by the smaller grinding media Ball mill is a versatile grinding mill and has a wide range of applicationsGrinding Mills and Their Types – IspatGuru
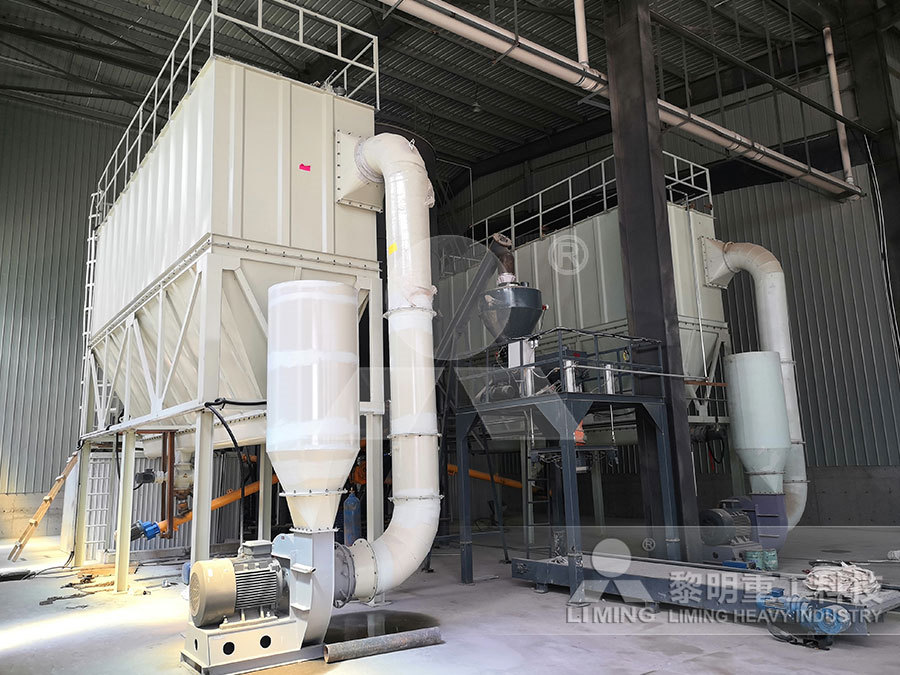
MeasurementBased Modelling of Material Moisture and Particle
2021年1月19日 1 Introduction Grinding is one of the most important technological processes used in many branches of industry For example, in the construction industry, grinding is used to crush components of building materials; in metallurgy–for metal ores; in the chemical and pharmaceutical industries–for substrates and reaction products; in the food industry–for food Iron ore is an important industrial source, is an iron oxide ore, a mineral aggregate containing iron elements or iron compounds that can be economically utilized, and there are many types of iron ore Among them, the iron smelting products mainly include Magnetite, siderite, and hematite and so on Iron exists in nature as a compound, and iron ore can be gradually selected after Iron ore grinding mill Grinding plants for Iron Ore2017年11月1日 An iron ore mill relies on the grinding and impact of grinding balls to complete iron ore crushing The operating process of an iron ore mill is as follows: first, the ores are poured into the mill, and both the ores and the grinding balls are lifted by the lifting bar arranged on the wall of the cylinder body to a certain height, after which they fall onto the bottom of the mill to Friction and wear of liner and grinding ball in iron ore ball mill 2020年10月13日 The results of the analyses clearly show that using a sieve of +180µm and its bottom180µm, the best time for grinding 05kg of Itakpe iron ore with 3kg of grinding media and a mill speed of 92 THE EFFECTS OF PROCESS VARIABLES ON THE GRINDING OF IRON ORE
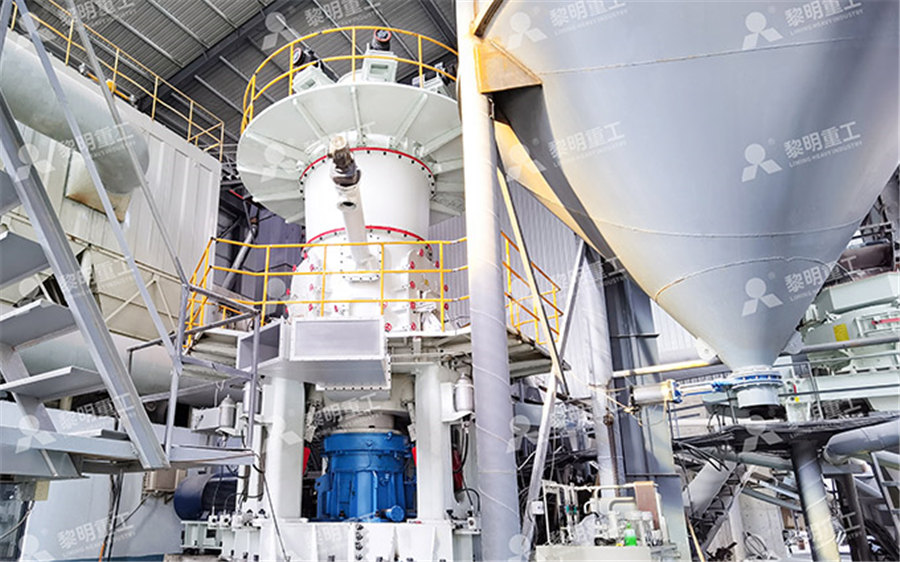
Effect of Water Density on Grinding Mill 911Metallurgist
2015年7月29日 As you increase the volume of the through put, the time that the ore has to react to the grinding media is lessened As you add ore to the mill you are also adding WATER and changing density which affects the slurry rheology and workings of the grinding action inside that mill This water is one of the main controls that you have over your grindEffect of mill type on ore grinding performance Ball mills are widely used in the mining and metallurgical industries for the grinding of ores and other materials There are a wide variety of mill types available, each with its own advantages and disadvantages The Factors affecting ores grinding performance in ball mills1 Grindability: The grindability of the ore affects the efficiency of the grinding mill Harder ores require more energy and longer grinding times, which can impact the mill's performance and operational costs 2 Media andliner Wear: The condition of the grinding media and liners affects the mill's efficiencyUnderstanding the operation of grinding mills in the mining and The Autogenous Mill, also known as AG Mill, is a type of grinding mill used in the mining industry This machine uses ore and rock itself as grinding media to perform its job Unlike other types of mills that use steel balls or rods for grinding materials, the Autogenous Mill relies on the material being ground to break itself into smaller piecesUnderstanding the SAG Mill in Copper Ore Mining Process
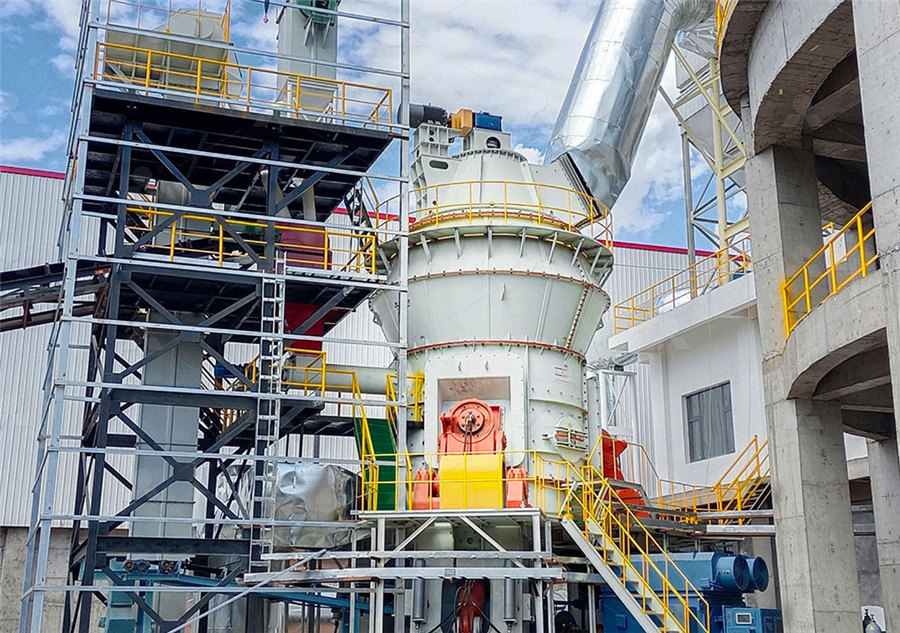
The effects of iron ore concentrate grinding methods (HPGR and
2020年10月18日 An iron ore concentrate sample was ground separately in a pilotscale HPGR mill in multiple passes and a dry opencircuit ball mill to increase the specific surface area of particles2015年3月15日 For the grinding tests, a Loesche mill LM45 (table diameter 045 m) is used (Fig 2a) This pilot scale mill is a special development for ore grinding, which is reflected by several features The mill has four rollers, which are able to stress the particle bed with grinding pressures of up to 5000 kN/m 2Research of iron ore grinding in a verticalrollermillThe present work was used to find the total grinding retention time of each ore in the mill Based on the total retention time of each ore, the optimum grinding time for each ore was identified to obtain the desired P80 passing particle size with acceptable hematite liberation(PDF) Optimizing Grinding Time for Hematite Liberation in Iron OresIn the mill, the mixture of medium, ore, and water, known as the mill charge, is intimately mixed, the medium comminuting the particles by any of the above methods Apart from laboratory testing, grinding in mineral processing is a continuous process, material being fed at a controlled rate into one end of the mill and discharging at the other end after a suitable dwell (residence) timeGrinding Mill an overview ScienceDirect Topics
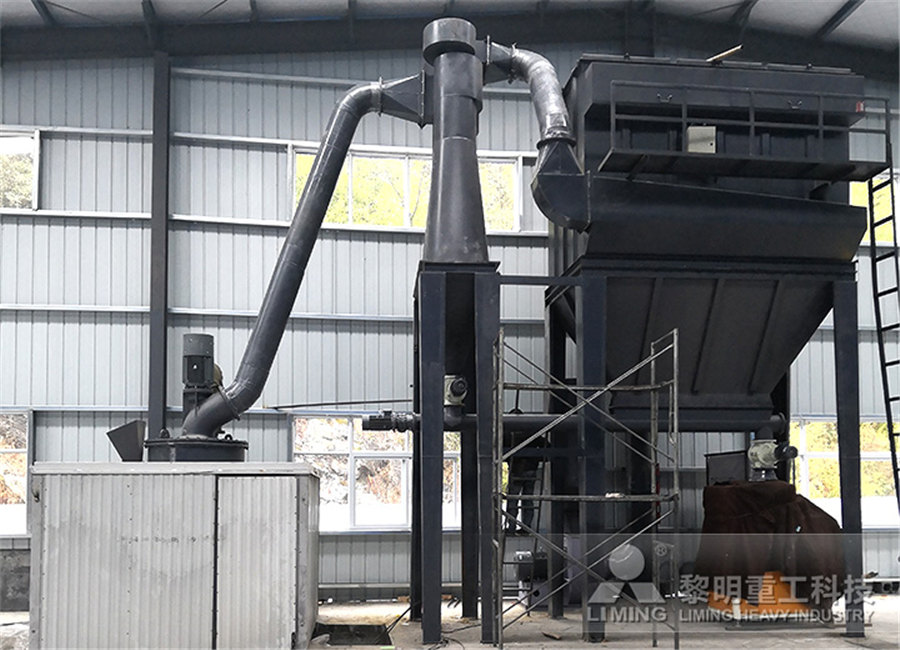
A comparison of wear rates of ball mill grinding media
2016年1月1日 In wet grinding practice, highstress abrasion occurs over a small region when ore particles are trapped between the grinding balls and the mill liner, and the load is sufficient to fracture