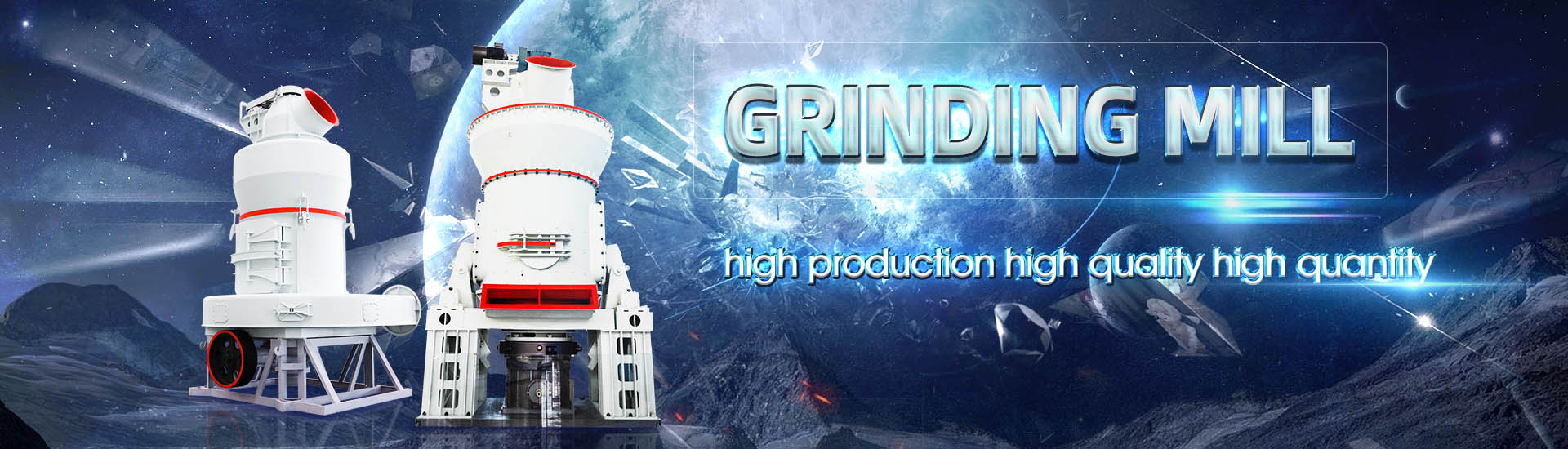
Vertical shear ore mill
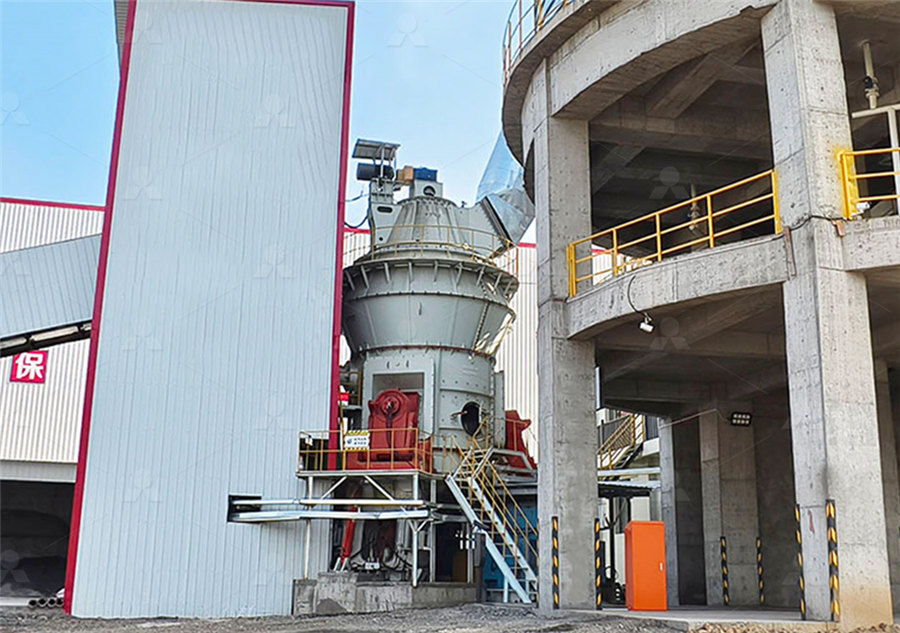
Vertical Roller Mills used for the comminution of mineral ores
Vertical roller mill (VRM) is an established technology in cement and slag grinding applications and Boliden and Gebr Pfeiffer have been collaborating on the application of this technology in 2015年3月15日 Verticalrollermills (VRM) are an energyefficient alternative to conventional grinding technology One reason is the dry inbed grinding principle Results of extensive test Research of iron ore grinding in a verticalrollermillAfter inventing the vertical roller mill (VRM) in 1928, LOESCHE was the first to introduce the technology into the power, cement, steel, ore and minerals industry Today more than 2,300 GET FIT FOR THE FUTURE Loesche2024年5月1日 An industrialscale vertical wet stirred media mill (HIGMill) was simulated via a population balance model (PBM) Feed and product particle size distributions (PSDs) of copper ore were measured at various steadystate conditions The PBM incorporated 1large–2smalltanks model and powerlaw specific breakage rate function S iPBM of an industrialscale vertical wet stirred media mill (HIGMill
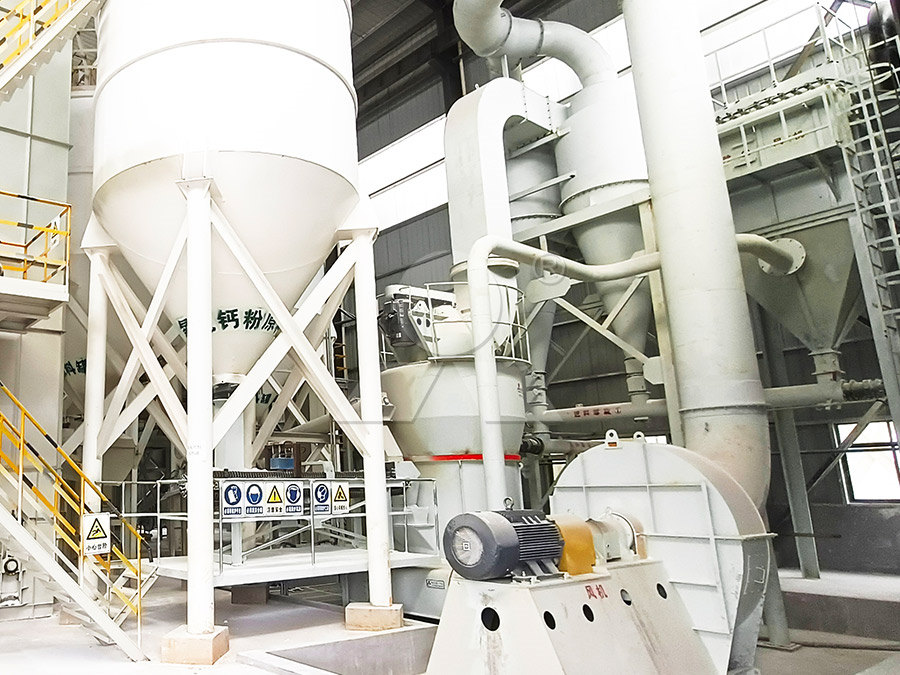
Analysis of vertical roller mill performance with changes in
2022年5月31日 The vertical roller mill (VRM), including powder separation and crushing subsystems, is used extensively for intermediate crushing of minerals in several industries such as cement, electric power, and chemical Compression crushing is also the main crushing mechanism in the VRM, but there is also shear force between grinding roller and particlesThe IsaMill™, as shown in Figure 815, is a horizontal stirred mill consisting of a series of 7–8 rotating grinding disks mounted on a cantilevered shaft that is driven through a motor and gearbox The disks operate at tip speeds of 21–23 m/s, resulting in energy intensities of up to 300 kW/m 3The mill is filled with suitable grinding media, and the space between each of the disks Stirred Mill an overview ScienceDirect Topics2023年7月4日 The vertical roller mill has the advantages of low energy consumption, high output, easy maintenance, etc, and has been widely applied in cement, steel and power industry, the preparation of nonmetallic ore ultrafine powder, manganese ore Roller Mill SpringerLink2024年3月5日 Research of iron ore grinding in a verticalrollermill To this range of power modelling efforts, one more is added through the development of a shear based power for s 03Apr2015 Best Practice and Benchmarking for ecoefficient comminutionHPGR CEEC (Coalition for Eco Efficient Comminution)
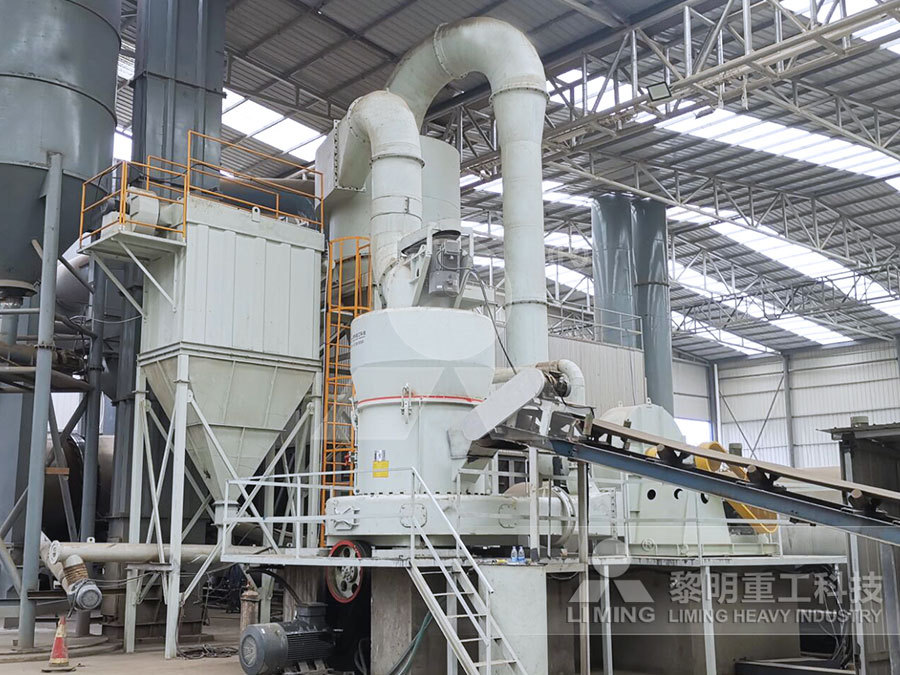
vertical roller mill Archives International Mining
A new LOESCHE vertical roller mill is in the process of being assembled at Aluminium Corp of China’s (Chinalco) copper smelting plant in the southern Chinese province of Fujian The threeroller mill will be operated by Chinalco’s Southeast Copper Ltd subsidiary and is able to grind 100 t/h of copper matte to a fineness of 20% with a sieving residue of 0074 mm, according to 2021年1月22日 Impact of ball filling rate and stirrer tip speed on milling iron ore by wet stirred mill: Analysis and prediction of the particle size distribution Author links open overlay panel Wang Guo a b, Yuexin Han a b, Yanjun Li a b, [47], using a vertical stirred media mill, that the PSD uniformity is generally independent of the φGM, Impact of ball filling rate and stirrer tip speed on milling iron ore the mill in vertical direction Those are the most active grinding zones in a vertical stirred mill Different operating parameters such as stirrer rotational speed, slurry solid content and slurry viscosity have an influence on mill performance Simulation results show that operating the millDEM SIMULATION AND ANALYSIS OF OPERATING PARAMETERS 2022年10月1日 This study investigated a mathematical model for an industrialscale vertical roller mill(VRM) at the Ilam Cement Plant in Iran The model was calibrated using the initial survey's data, and the (PDF) A cement Vertical Roller Mill modeling based on
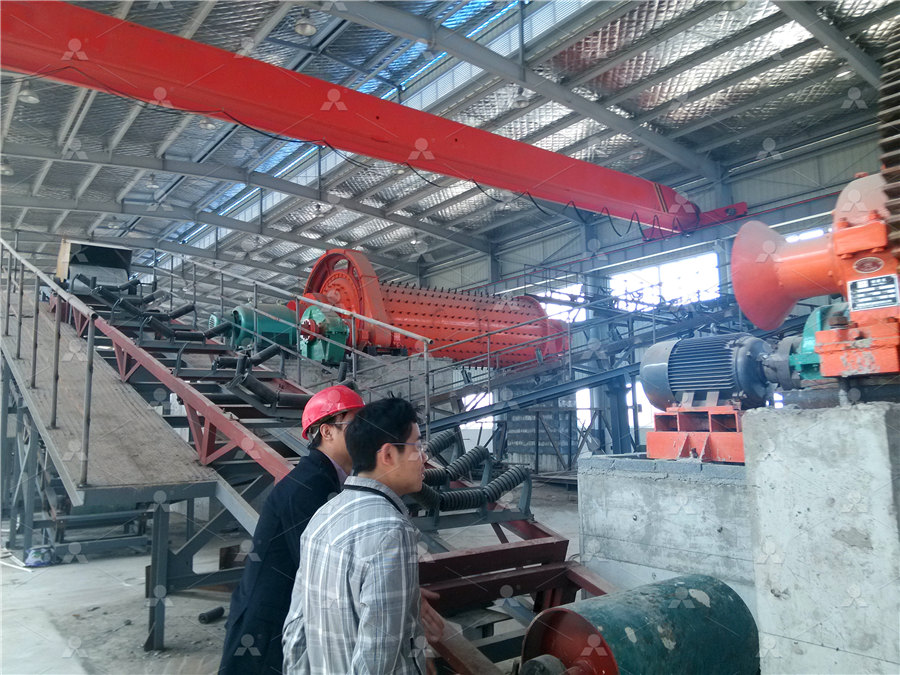
(PDF) Industrial Vertical Stirred Mills Screw Liner Wear Profile
2021年4月10日 Data from a vertical stirred mill screw liner wear measurement obtained in a fullscale mill ar e used to correlate with simulation results The results indicate a relative agreement with industrial2021年7月22日 Vertical wet stirring mill equipment is mainly divided into mixing mill (tower mill) and sand mill The barrel of the stirring mill is thicker and the spindle angular velocity is lower The grinding medium can be either a sphere Vertical wet stirring millVertical wet stirring mill 2023年2月23日 Francis, B Scaleup and Operations of a Vertical Stirred Mill, Master’s Thesis, The University of British Columbia, Vancouver, BC, Canada, 2014 Minerals 2023 , 13 , 315 16 of 16(PDF) Performance Comparison of the Vertical and2023年9月21日 Ball Mill: ball mill offers relatively limited control over the final particle size distribution The size reduction is primarily achieved through impact and attrition, and the final product may have a broader particle size distribution Vertical Roller Mill: vertical roller mill provides better control over the final particle size distributionA Comparative Analysis: Vertical Roller Mill vs Ball Mill
.jpg)
Mechanistic modeling and simulation of a batch vertical stirred mill
2020年9月1日 Application of mechanistic modelling approach to batch wet vertical mills Stirrer rotation frequency and solids concentration effects captured by the modeling approach • Contribution of shear energy losses as function of solids concentration Good agreement between experimental and simulated particle size distribution for grinding of a copper ore and 2023年7月10日 The present literature review explores the energyefficient ultrafine grinding of particles using stirred mills The review provides an overview of the different techniques for size reduction and the impact of energy requirements on the choice of stirred mills It also discusses the factors, including the design, operating parameters, and feed material properties, EnergyEfficient Advanced Ultrafine Grinding of Particles Using 2015年3月15日 This pilot scale mill is a special development for ore grinding, which is reflected by several features The mill has four rollers, which are able to stress the particle bed with grinding pressures of up to 5000 kN/m 2 Various different roller geometries are available for grinding to generate different shear stress ratiosResearch of iron ore grinding in a verticalrollermill2014年10月20日 Rio Paracatu regrind circuit Santos Júnior et al (2011) presented some data on the Paracatu Vertical Mill circuit process, as well as its comparison to the plant's conventional ball millRegrind of metallic ores with vertical mills: An overview of the
.jpg)
PREDICTING THE PRODUCT PARTICLE SIZE DISTRIBUTION FROM A VERTICAL
The Colorado School of Mines offers courses in chemistry, geology, and physics, with a focus on mining geology and astroparticle physicswhich is subjected to pressure and shear force It has the advantages of a large processing capacity, easy adjustment of product particle divided into vertical roller mill, horizontal cylinderrollermill,highpressurerollermill,Raymond mill, and column of nonmetallic ore ultrafine powder, manganese ore fine grinding, and other fieldsRoller Mill SpringerA compact coal mill solution for grinding virtually any type of raw coal Our ATOX® Coal Mill is a compact vertical roller mill that can grind almost any type of raw coal The coal mill utilises compression and shear force generated between the large rollers and the rotating table to crush and grind raw coal, removing the need for a separate piece of equipment for crushingRoller mill ATOX® COAL FLSmidth DorrOliver Eimco vertical 2020年9月1日 DEM has been successfully used to predict mill power in a pilotscale vertical stirred mill operating at different stirrer speeds once the contribution of tangential dissipated energy was incorporated by backfitting a fraction of the DEM collision shear component Deviations below 35% between simulations and experiments were then obtainedMechanistic modeling and simulation of a batch vertical stirred mill
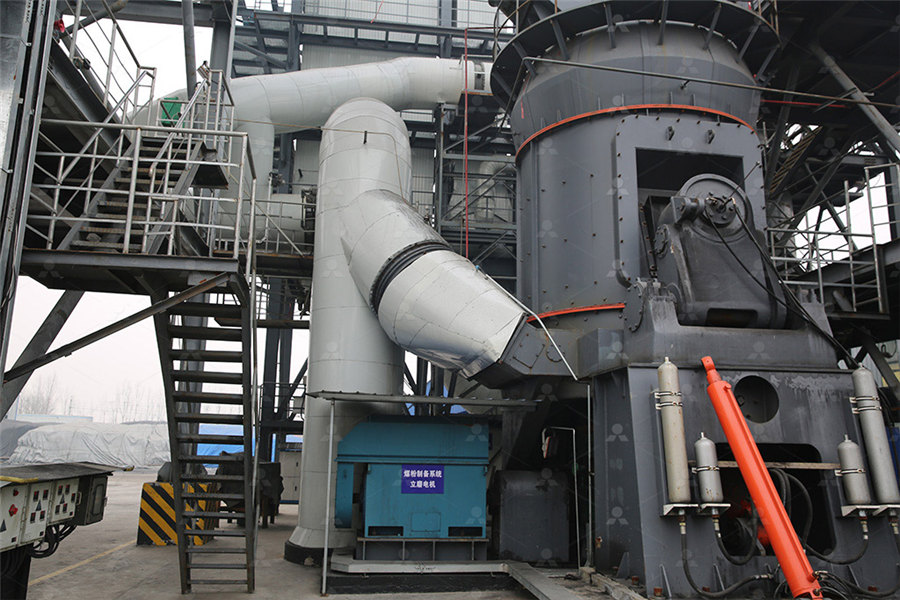
Research of iron ore grinding in a verticalrollermill دانشیاری
Fig 1), which can be adjusted while the mill is running Furthermore, roller geometry and dam ring height are important design features in a Loesche mill, which can be adapted to the grinding task Several characteristics of VRM’s are advantageous for the challenges in ore industry, especially in comparison to conventional grinding technologyThe application of vertical roller mills (VRMs) for ore grinding is a part of the strategies against rising energy consumption (Reichert et al, 2015) The VRM technology was introduced in the mid'90s for grinding clinker and slag by LOESCHE (Schaefer, 2001) Fig 1 illustrates the grinding parts of a Loesche vertical roller millModeling and simulation of vertical roller mill using population 2016年1月1日 Table 1 Fig 1: Layout of the No 2 HotStrip Mill of Usiminas at startup Mill equipment The line consists of a 4high reversing roughing mill (R2) equipped with hydraulic gap control and a vertical edger at the entry side (Figure 2) Longstroke, hydraulic automatic width control (HAWC) is applied to ensure high width accuracy and simple HotStrip Mill at Usiminas: Superior Mill Performance Metals For the mining industry utilising VRM dry grinding technology in the Iron Ore, the secondary effect being the horizontal shear force, among others, a roller arm, New Vertical Pipe Production Plant in Somersby, NSW Australia; Contact Us Ph: +61 2 4372 1234Vertical Roller Mills Ammermann Pty Ltd
.jpg)
Analysis of vertical roller mill performance with changes in
2022年5月31日 The vertical roller mill (VRM), including powder separation and crushing subsystems, is used extensively for intermediate crushing of minerals in several industries such as cement, electric power, and chemical Compression crushing is also the main crushing mechanism in the VRM, but there is also shear force between grinding roller and particles1 LM Vertical slag mill integrates drying, grinding, powder selection and conveying together, simple system, compact layout, the area is about 50% of the ball milling system Reduce the cost of investment, low energy consumption, compared with the ball mill system, the energy consumption is 30% ~ 40%LM Vertical slag mill2021年7月1日 Vertical stirred mills may be classified according to the speed of the stirrer in two groups: gravityinduced or fluidized mills [[1], [2], [3]]In the gravityinduced mills, the stirrer, generally of the screw type, turns so that the grinding charge exhibits an ascending convective motion at the center, descending from the edges of the screw and close to the mill shell, owing Predicting the effect of operating and design variables in 2020年9月1日 Request PDF Mechanistic modeling and simulation of a batch vertical stirred mill Vertical stirred mills are now widely used in the minerals industry and the increasing variety of models from Mechanistic modeling and simulation of a batch vertical stirred mill
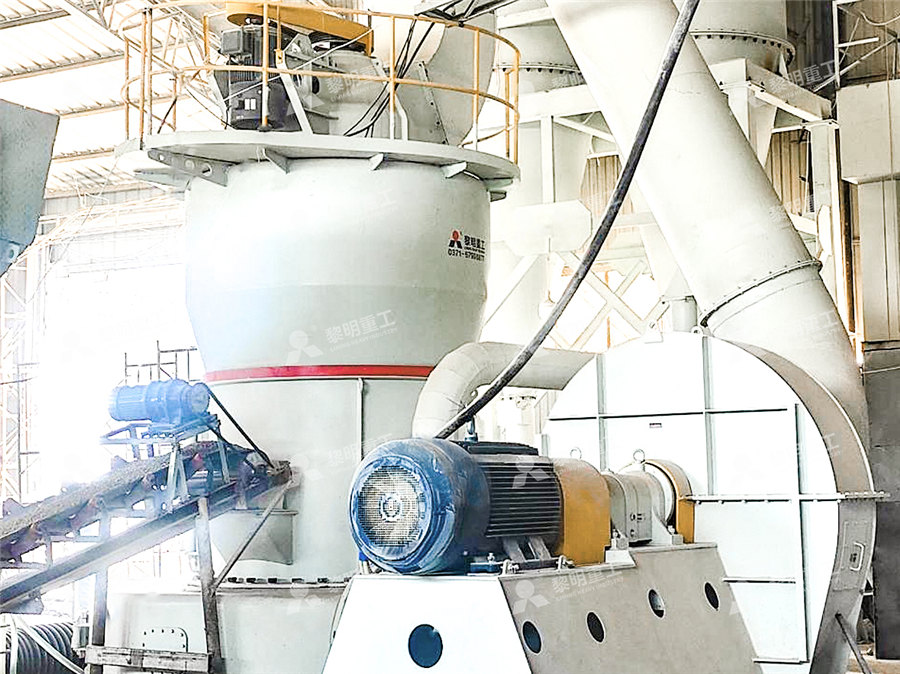
Numerical Investigation of Vertical Roller Mill Operation Using
2023年12月4日 21 Vertical Roller Mill The VRM shall have three or four rollers and a table The rollers were pressed against the ore and table using hydraulic cylinders during operation The table is rotated by an external drive train, and rollers are counterrotated due to the friction between the roller and material