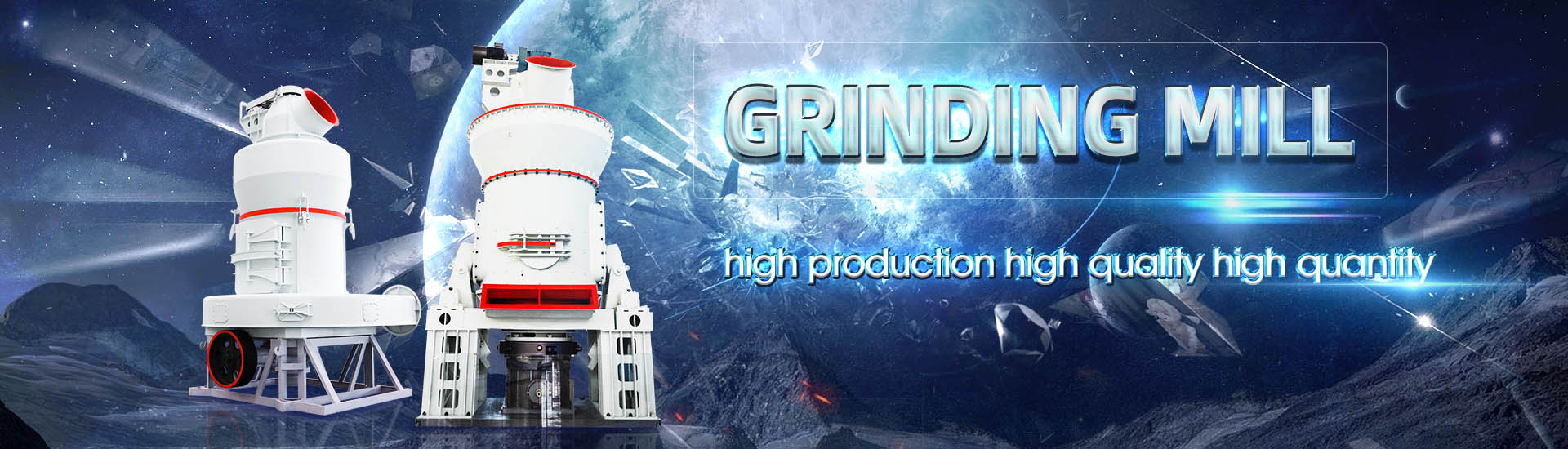
Coal powder ore Coal powder ore Coal powder ore
.jpg)
Reduction behavior of iron ore powder by highvolatile coal in
2023年12月8日 The reduction behavior of iron ore powder by highvolatile coal was investigated, and its kinetic mechanism was clarified The effect of volatiles in coal on the reduction reaction The ultrafine iron ore powder produced through mechanical activation is a crucial technology for achieving lowtemperature ironmaking This study employs thermogravimetric analysis to The characteristics and mechanism of ultrafine iron ore powder Morphologies and structures of pulverized coal and iron ore powder after mechanical activation were studied by SEM, XRD, FTIR and laser particle sizer The microcrystalline structure of Effect of mechanical activation on the structure of pulverized coal 2018年9月28日 Crushing and grinding process in mineral processing industry is high energy consuming but it is essential for generating required sized ore with improved liberation, which Generation of low ash fine clean coal powder by autogenous
.jpg)
(PDF) Coproduction of DRI Powder and Semicoke
2015年11月26日 Effective utilization of low grade iron ore and low rank coal by excessive coalbased direct reduction process to coproduce DRI powder and semicoke can be one of the solutions to cut the2020年2月14日 Of the total iron in the ore, 8561% was recovered as iron powder (grade: 920 mass%) Use of this process could reduce CO2 emissions by approximately 10% Direct Highly Efficient Beneficiation of LowGrade Iron Ore via Ore–Coal 2016年1月15日 Coproduction of DRI Powder and Semicoke from Siderite Ore and Low Rank Coal by Excessive Coalbased Direct Reduction in Rotary Kiln[PDF] Coproduction of DRI Powder and Semicoke from Siderite the reaction of the manganese ore with 5 vol % H 2 and with coal powder at 900 °C, the catalytic and OC effect of manganese ore on coal gasification, the reaction efficiency and reaction Investigation on the ChemicalLooping Reaction Characteristics of
.jpg)
Reduction characteristics and mechanism of mechanically
The gradual diminution in the mass of iron ore powder finds its genesis primarily in the continual dissipation of oxygen constituents encapsulated within iron oxide and the steadfast carbon cent of the nation’s land area Coal reserves are split between the Eastern and Western states — the most important coal deposits in the East are in Appalachia, which includes portions of nine states The West contains the Wyodak coalbed, which is nation’s the leading source of coal and part of the Powder River Basin of Wyoming and MontanaFACTS ABOUT COAL AND MINERALS National Mining 2018年1月1日 Ring formation as a troublesome problem for gratekiln production of ironore oxide pellet makes the quality of pellet declining, production efficiency reducing, and production cost increasing Pellet powder and coal ash are the raw material of ring Bonding strength, microstructure and composition of coal ash, ironore pellet powder, and their mixed powder Effect of coal ash on ring behavior of ironore pellet powder in Powder River Basin Background • More than 40% of the coal produced in the US comes from the Powder River Basin 1,2 • Original coal resource estimated at 116 trillion short tons 1,2, with the majority of the resource in the Paleocene Tongue River Member of the Fort Union Formation • Surface mine extraction from thick coal seams (>50ft)Powder River Basin CORECM: AdvancingStrategies for Carbon Ore
.jpg)
Magnetite Iron Ore Powder, For Coal Washery IndiaMART
DJ Enterprises Ltd Offering Magnetite Iron Ore Powder, For Coal Washery at Rs 17000/ton in Gondia, Maharashtra Get Iron Ore Powder at lowest price ID: The siderite iron ore was reduced by coal at over dosage to produce good quality DRI powder Whilst the over dosage inferior coal was upgraded in the reduction process to generate high value semicoke as by product that is a relatively cleaner solid fuelCoproduction of DRI Powder and Semicoke from Siderite Ore pulverized coal injection plays a significant influence on the deposit formation of rotary kiln The incomplete burnt pulverized coal containing residual carbon and a large amount of coal ash was mixed with preheated pellet powder, which would produce local reducing atmosphere to form lowmeltingtemperature compounds by residual carbon The Deposit Formation Mechanism in CoalFired Rotary Kiln for Iron Ore 2024年6月13日 An essential objective of the Powder River Basin carbon Ore, rare earth, and critical mineral (CORECM) project is to provide an economic benefit to the people who live and work in the Powder River Basin of Wyoming and Montana by stimulating new resource development centered around the nation’s largest coal minesPowder River Basin CORECM: Advancing Strategies for Carbon Ore
.jpg)
Investigation on the ChemicalLooping Reaction Characteristics of
the reaction of the manganese ore with 5 vol % H 2 and with coal powder at 900 °C, the catalytic and OC effect of manganese ore on coal gasification, the reaction efficiency and reaction products under different mass ratios of OC to coal (O/C), and the effect of multiple cycles on the reaction performance of the manganese oreAdditionally, the maximum reaction rate was 157 times that of coal powder reduction, and the final reaction fraction was 17–20 % higher than that of coal powder and coke powder H ICCB were prepared by using iron ore powder and heattreated waste wood from a steel plant as experimental raw materials and adding some bindersStudy on strength and reduction characteristics of iron ore powder 22 Procedure of Experiment The test flow sheet of excessive coalbased direct reduction process to coproduce DRI powder and semicoke is presented in Fig 2Firstly, siderite lump ore was charged into a rotary kiln (bench scale: ϕ120×200 mm, pilot scale: ϕ1000×500 mm) for reductionThe amount of coal required for reduction was determined by designed C/Fe mass Coproduction of DRI Powder and Semicoke from Siderite Ore Obtaining [edit edit source] Breaking [edit edit source] Coal ore itself can be obtained by mining it with any pickaxe enchanted with Silk TouchWhen mined without Silk Touch, it drops one coalIt is affected by the Fortune enchantment, dropping 1–2, 1–3, or 1–4 coal respectively with Fortune I, II, and III It also drops 0–2 when mined Fortune does not affect the amount of Coal Ore – Minecraft Wiki
.jpg)
Preparation, characteristics and mechanisms of the composite
DOI: 101016/jconbuildmat2019 Corpus ID: ; Preparation, characteristics and mechanisms of the composite sintered bricks produced from shale, sewage sludge, coal gangue powder and iron ore tailings2018年9月28日 Request PDF Generation of low ash fine clean coal powder by autogenous grinding process Crushing and grinding process in mineral processing industry is high energy consuming but it is Generation of low ash fine clean coal powder by autogenous 2020年5月1日 When coal powder is used as reductant to reduce iron ore, the amount of reductant is determined according to the oxygen content of iron oxide in the ore Previous studies have shown that the reduction rate and metallization rate of reducing materials were significantly increased with the increase of reductant dosage in a certain rangePowder Technology2010年12月1日 To determine the temperature range of iron ore reduction, the mixture of Datong bituminite and iron ore powder was reduced, and this process was measured by nonisothermal thermogravimetryThermogravimetric analysis for direct reduction of iron ore powder by coal
.jpg)
Preparation, characteristics and mechanisms of the composite
Iron ore tailings and coal gangue powder are the main sources of industrial solid wastes, the dispose of which has become severe and urgent with the increasing demand of environmental harmony The present study firstly proposed a reasonable way to deal with the large amount of iron ore tailings and coal gangue powder by making them as the sintered bricks with sewage Coproduction of DRI Powder and Semicoke from Siderite Ore and Low Rank Coal by Excessive Coalbased Direct Reduction in Rotary Kiln Yanhong Luo 1), In this paper, an integrated process was developed to beneficiate low grade siderite ore and upgrade inferior coal simultaneously to yield DRI powder and semicokeCoproduction of DRI Powder and Semicoke from Siderite Ore Mineral Processing Extractive Metallurgy Review, (ISSN: 08827508), vol 31, issue 2, Jan 2010, pp 7385 EFFECTS OF BINDER ON THE PROPERTIES OF IRON ORE COAL COMPOSITE PELLETSMineral Processing Extractive Metallurgy Review, (ISSN: 0882 iron ore lumps (60% fe or more)60% fe or more but below 62% fe Coal; briquettes, ovoids and similar solid fuels manufactured from coal coal, whether or not pulverised, but not agglomerated: anthraciteJay Jagannath Steel And Power Limited Manufacturer of Anthracite Coal
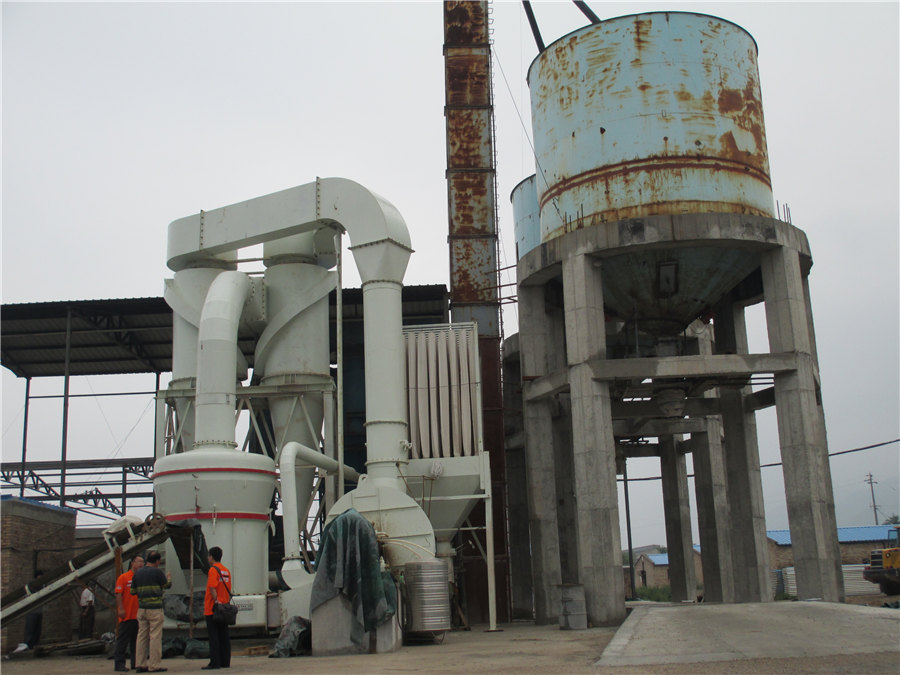
Effect of coal ash on ring behavior of ironore pellet powder in
2018年1月1日 Coal ash was employed to research ring behavior of ironore pellet powder • Ring formation process in coalfired kiln was analyzed • Insufficiency Fe 2 O 3 recrystallization makes pellet powder can't form original ring Glassy silicon oxides and liquation substances make powders form original ringIron ore–coal mixture Here iron ore fines of comparatively bigger size (2–5 mm) are mixed with coal fines 0–3 mm and charged in the container Such system avoids extra cost associated with grinding of ore particles to fine powder (\150 lm) for making composite pellets Composite layer Here iron ore coal mixture is used asReduction Efficiency of Iron Ore–Coal Composite Pellets in Tunnel 2021年12月2日 Powder River Basin CORECM: Advancing Strategies for Carbon Ore, Rare Earth Element, and Critical Mineral Resource Development in the Nation's Largest Coal Producing Basin DEFE USEA CONSENSUS Webinar December 2, 2021 Project Lead: Erin Phillips, Senior Research Scientist University of Wyoming School of Energy Powder River Basin CORECM: Advancing Strategies for Carbon OreAbstract Most previous studies on iron ore–coal pellets (ICPs) have focused on their reduction, but studies on their sticking behavior have not been reported The sticking behavior of iron ore–coal pellets (ICPs) at high temperatures under a load of 01 MPa was studied Temperature was determined to be an important factor that affects the sticking behavior: the sticking Sticking behavior of iron ore–coal pellets and its inhibition,Powder
.jpg)
How to Process Coal into Pulverized Coal in 5 Steps?
2024年1月11日 Ore dressing aims to remove impurities to further enhance the quality of the coal powder We know about two common methods are: Physical separation: Utilizing techniques like air classification or magnetic separation to physically separate the impurities from the Iron ore tailings and coal gangue powder are the main sources of industrial solid wastes, the dispose of which has become severe and urgent with the increasing demand of environmental harmony The present study firstly proposed a reasonable way to deal with the large amount of iron ore tailings and coal gangue powder by making them as the sintered bricks with sewage Preparation, characteristics and mechanisms of the composite Reduction behavior of iron ore powder by highvolatile coal in thermogravimetric–gas chromatographic 93 123 In order to further explore the effect of volatile on the reduction of iron ore, the pyrolysis solid product of GH coal that was heated at 1100 C for 2 h under Ar atmoReduction behavior of iron ore powder by highvolatile coal in 2010年4月1日 For e xperimental work, iron orecoal composite pellets were prepared using coals from two different sources having four different Fe tot /C fix ratios The details are presented in the Table 1Effects of Binder on the Properties of Iron OreCoal Composite Pellets
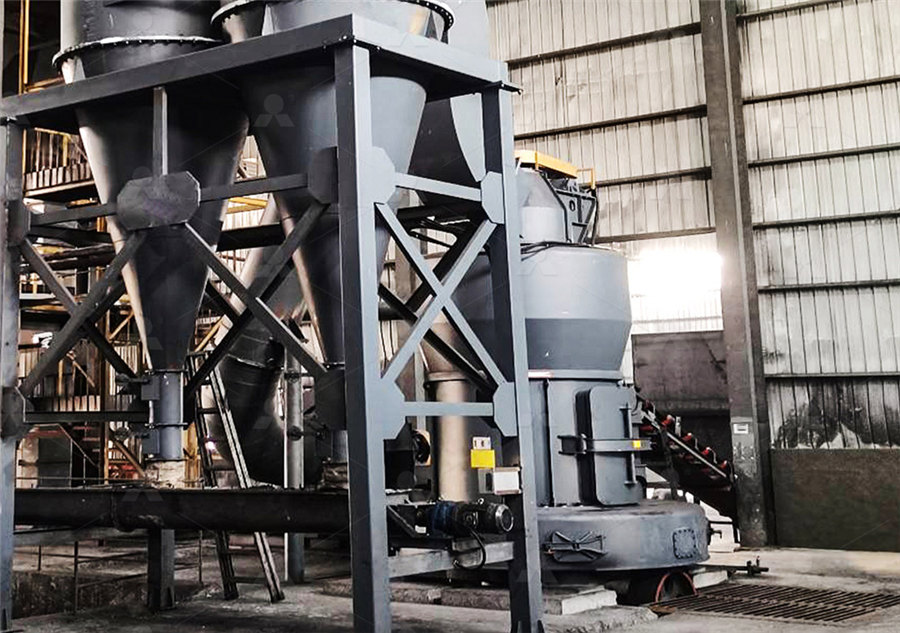
Coproduction of DRI Powder and Semicoke from Siderite Ore
Effective utilization of low grade iron ore and low rank coal by excessive coalbased direct reduction process to coproduce DRI powder and semicoke can be one of the solutions to cut the high cost of DRI powder and solve the problem of DRI cent of the nation’s land area Coal reserves are split between the Eastern and Western states — the most important coal deposits in the East are in Appalachia, which includes portions of nine states The West contains the Wyodak coalbed, which is nation’s the leading source of coal and part of the Powder River Basin of Wyoming and MontanaFACTS ABOUT COAL AND MINERALS National Mining 2018年1月1日 Ring formation as a troublesome problem for gratekiln production of ironore oxide pellet makes the quality of pellet declining, production efficiency reducing, and production cost increasing Pellet powder and coal ash are the raw material of ring Bonding strength, microstructure and composition of coal ash, ironore pellet powder, and their mixed powder Effect of coal ash on ring behavior of ironore pellet powder in Powder River Basin Background • More than 40% of the coal produced in the US comes from the Powder River Basin 1,2 • Original coal resource estimated at 116 trillion short tons 1,2, with the majority of the resource in the Paleocene Tongue River Member of the Fort Union Formation • Surface mine extraction from thick coal seams (>50ft)Powder River Basin CORECM: AdvancingStrategies for Carbon Ore
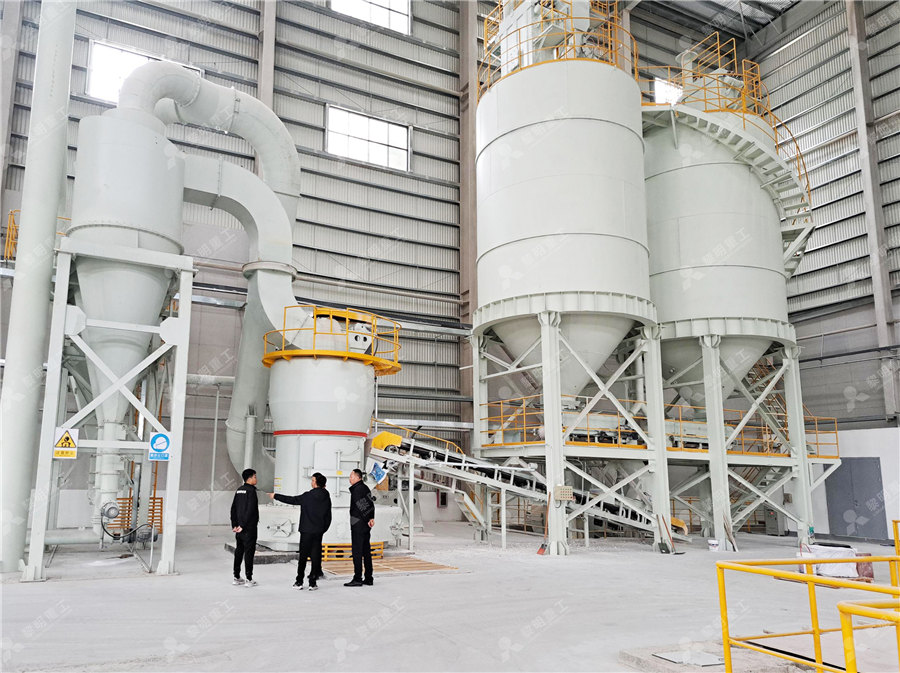
Magnetite Iron Ore Powder, For Coal Washery IndiaMART
DJ Enterprises Ltd Offering Magnetite Iron Ore Powder, For Coal Washery at Rs 17000/ton in Gondia, Maharashtra Get Iron Ore Powder at lowest price ID: The siderite iron ore was reduced by coal at over dosage to produce good quality DRI powder Whilst the over dosage inferior coal was upgraded in the reduction process to generate high value semicoke as by product that is a relatively cleaner solid fuelCoproduction of DRI Powder and Semicoke from Siderite Ore pulverized coal injection plays a significant influence on the deposit formation of rotary kiln The incomplete burnt pulverized coal containing residual carbon and a large amount of coal ash was mixed with preheated pellet powder, which would produce local reducing atmosphere to form lowmeltingtemperature compounds by residual carbon The Deposit Formation Mechanism in CoalFired Rotary Kiln for Iron Ore 2024年6月13日 An essential objective of the Powder River Basin carbon Ore, rare earth, and critical mineral (CORECM) project is to provide an economic benefit to the people who live and work in the Powder River Basin of Wyoming and Montana by stimulating new resource development centered around the nation’s largest coal minesPowder River Basin CORECM: Advancing Strategies for Carbon Ore
.jpg)
Investigation on the ChemicalLooping Reaction Characteristics of
the reaction of the manganese ore with 5 vol % H 2 and with coal powder at 900 °C, the catalytic and OC effect of manganese ore on coal gasification, the reaction efficiency and reaction products under different mass ratios of OC to coal (O/C), and the effect of multiple cycles on the reaction performance of the manganese oreAdditionally, the maximum reaction rate was 157 times that of coal powder reduction, and the final reaction fraction was 17–20 % higher than that of coal powder and coke powder H ICCB were prepared by using iron ore powder and heattreated waste wood from a steel plant as experimental raw materials and adding some bindersStudy on strength and reduction characteristics of iron ore powder