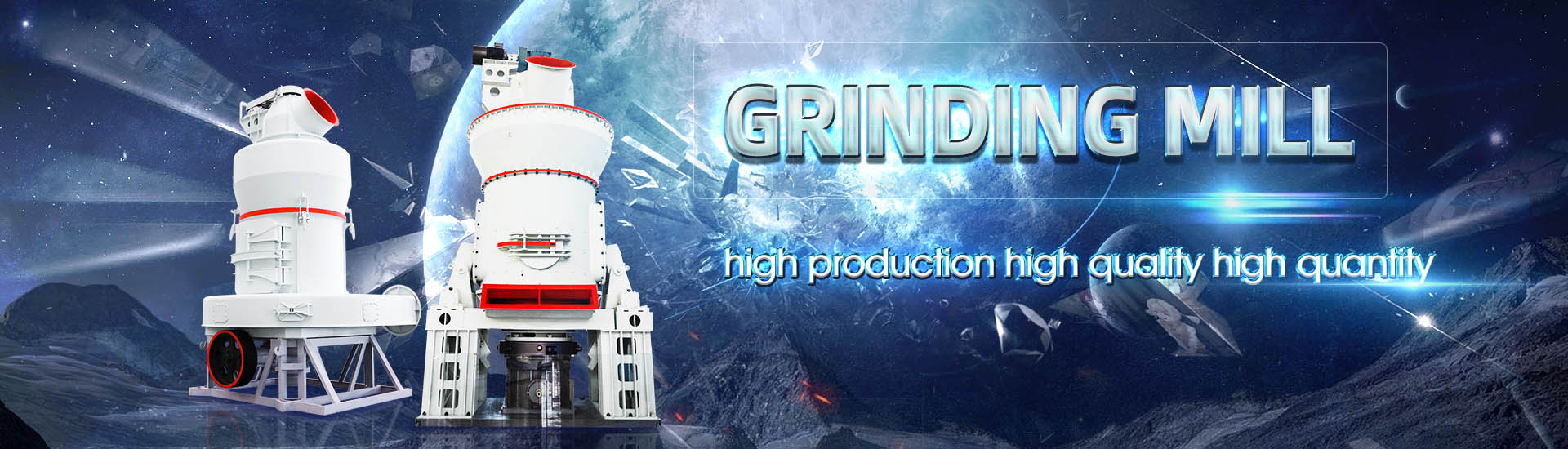
Rotary kiln firing zone cylinder temperature
.jpg)
What Is The Temperature Zone In A Rotary Kiln? 5 Key Factors To
The temperature zone in a rotary kiln is controlled and varies according to the specific process requirements Typically, it ranges from 800 to 2,200°F (427 to 1204°C) The kiln is designed to maintain different temperature profiles along its length to facilitate various stages of material The rotary kiln is the key component in a cement plant It is a long steel cylinder, lined with refractory brickwork to protect the outer shell from the very high temperatures of the interior TEMPERATURE MEASUREMENTS IN Land Instruments InternationalTHE BURNING ZONE Also known as the firing zone, the burning zone is at the lower end of the rotary kiln, where the cement components are heated to about 1300 to 1450 °C (2372 to 2642 CRITICAL MEASUREMENTS IN CEMENT MANUFACTURE2022年7月2日 Depending on the temperature range, there are different thermal zones inside the kiln (preheaters and rotary kiln) What are the thermal zones and transformation of the cement kiln?Chapter 10: Rotary Kiln Clinkerization and Thermal
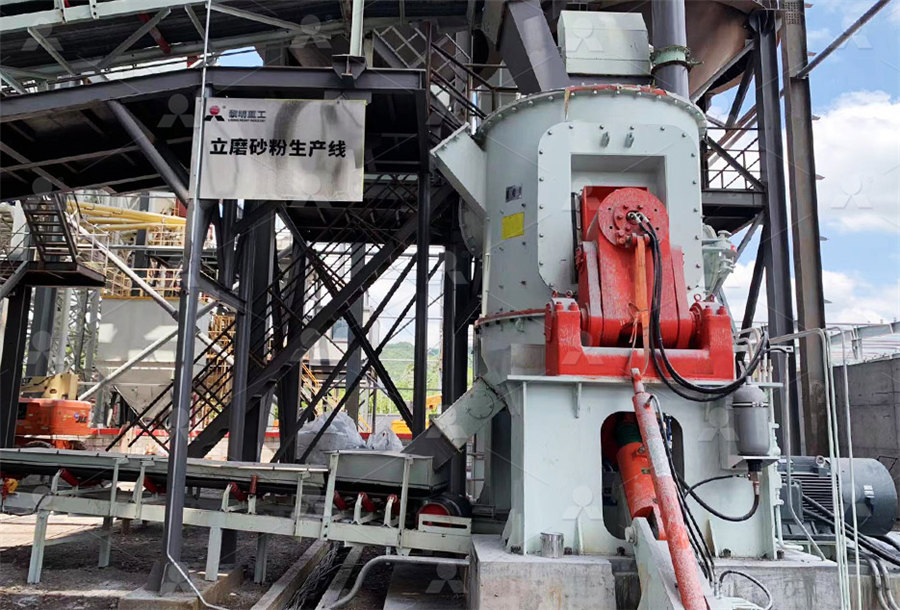
Novel method for temperature prediction in rotary kiln process
2024年4月15日 Effectively predicting and optimally controlling the temperature field within rotary kilns emerges as a crucial strategy to address this pressing challenge In a pioneering effort, 2023年2月25日 The rotary kiln is a slightly inclined steel cylinder that rests on supports (bearing rollers) with an interior lining; it is equipped with a rotating motor that induces a turning motion Rotary kiln process: An overview of physical mechanisms, models The value of 518°C obtained for the smoking chamber indicated that the temperature in the burning zone was between 1000 and 1100°C; which corresponds to a good range for calcination process asSchematic of temperature profile zone of the rotary kilnInfrared thermal cameras can be used to measure shell temperatures which can provide valuable insights for safe and efficient rotary kiln operation Identifying shell hot spots can prevent Rotary Kiln Monitoring with Shell Temperature Visualization and
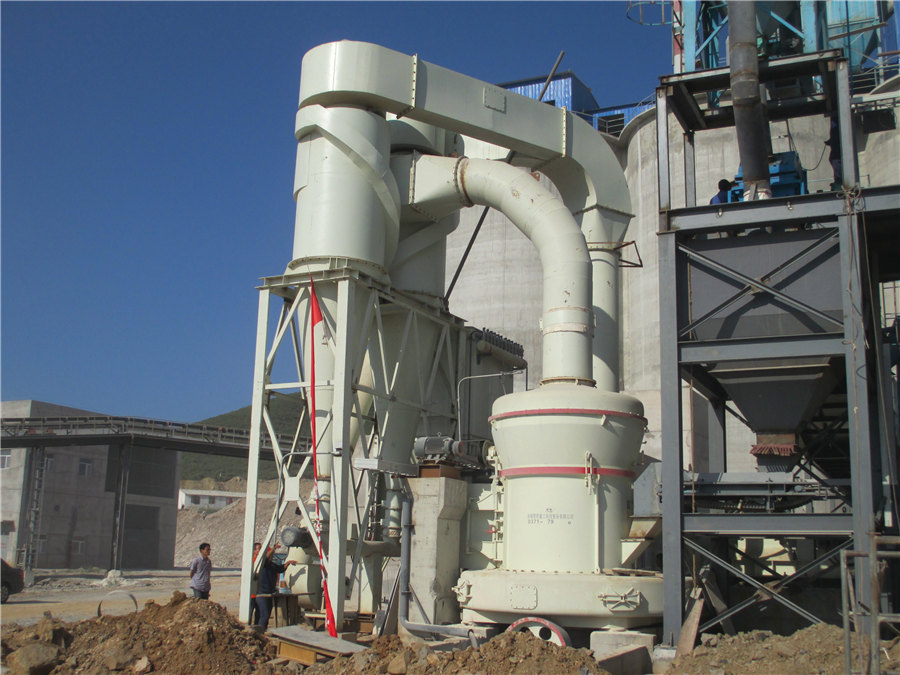
Heat transfer from flames in a rotary kiln Springer
1983年1月18日 Heat flow in the flame zone of a directfired rotary kiln has been modeled mathematically The flame has been assumed to be cylindrical in shape, backmixed radially, Burning zone temperature directly determines the characteristics of the clinker Presently, in most of the cement plants, burning zone temperature measurement is obtained using radiation Burning Zone Temperature Estimation of Rotary Kiln Using Flame 2015年1月1日 Rotary kiln at high temperature seems a black box, according to steadystate heat transfer across a cylinder, roasted from 750 o C when entering to 1300 o C in firing zone, Monitoring the Ring Formation in Rotary Kiln for Q=Qsh (2) By solving equation (1), temperature Tst and Trt can be modeled as follows: st sh st sh st sh (3) rt st rt sh rt rt st rt rt rt 2 0 0 (4) Where st is thermal conductivity of steel plate MONITORING THE RING FORMATION IN ROTARY KILN FOR PELLET FIRING
.jpg)
TEMPERATURE MEASUREMENTS IN Land Instruments
into a rotary kiln which raises their temperature to approximately 1370 oC (about 2500 oF) 3 6 As they progress along the rotary kiln towards the firing zone, the raw materials lose moisture and other components and form a rocklike substance called clinker, mineral lumps roughly 25 mm (1 inch) in diameter 4 Upon leaving the kiln, the hot THE BURNING ZONE Also known as the firing zone, the burning zone is at the lower end of the rotary kiln, where the cement components are heated to about 13001450 °C (23722642 °F), forming clinker Accurate temperature measurements are critical for product quality, environmental performance and kiln lifetime KILN 3TEMPERATURE MEASUREMENTS IN Land Instruments 2023年12月26日 Unlike heat treat and glasswork, which require a greater level of specificity, potters deal in predefined temperature ranges – which correspond with pyrometric conesBefore the advent of modern programmable digital kiln controllers, kiln temperature control relied on manual kilns and the use of pyrometric cones and kiln sitters to measure when the proper kiln Complete Guide to Kiln Firing Temperatures SDS IndustriesThe temperature of the flue gas in the solution firing zone is about 1700 degrees, and the temperature of the kiln material is above 1300 degrees Generally, you should adopt refractory bricks with a high softening temperature and resistant to kiln material solution Such fire bricks are dense and have a high thermal conductivity Refractory Refractory Lining In Cement Rotary Kiln
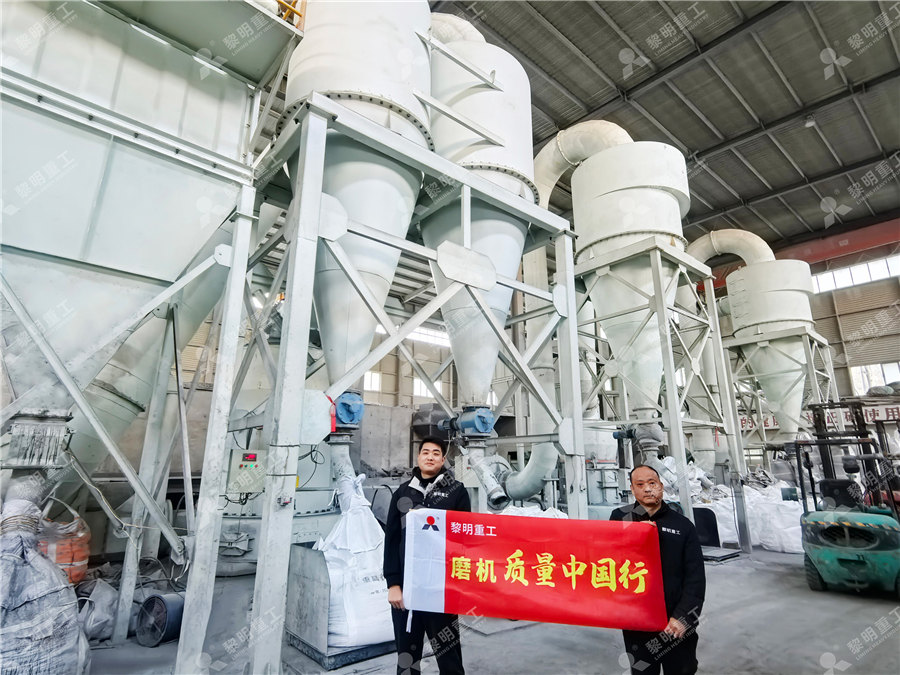
Cement kilnsdesignfeaturesofrotarykilns PDF SlideShare
2021年4月22日 This page lists these and describes their evolution Rotary kiln terminology The Kiln Shell The shell of the kiln is made of mild steel plate Mild steel is the only viable material for the purpose, but presents the problem that the maximum temperature of the feed inside the kiln is over 1400°C, while the gas temperatures reach 1900°CThe rotary kiln is used in many solid processes, including drying, incineration, heating, cooling, humidification, calcination and reduction This widespread application can be attributed to factors such as the ability to handle varied loads, with large variations in particle size [1]The rotary kiln is a slightly inclined steel cylinder that rests on supports (bearing rollers) with an Rotary Kiln an overview ScienceDirect Topics2015年3月15日 Figure 4 shows the axial temperature distributions of rotary kiln inner roasted from 750 o C when entering to 1300 o C in firing zone, steadystate heat transfer across cylinder with the Monitoring the Ring Formation in Rotary Kiln for Pellet Firing2024年1月9日 Although the thermal expansion coefficient of the kiln shell is greater than that of the kiln bricks, However, the temperature of the kiln shell is generally around 280–450 °C, while the temperature of the kiln bricks is generally above 800°C, and the temperature in the firing zone is more than 1,300°CThe Effects and Selection of Fire Brick Refactory Bricks For Rotary Kiln
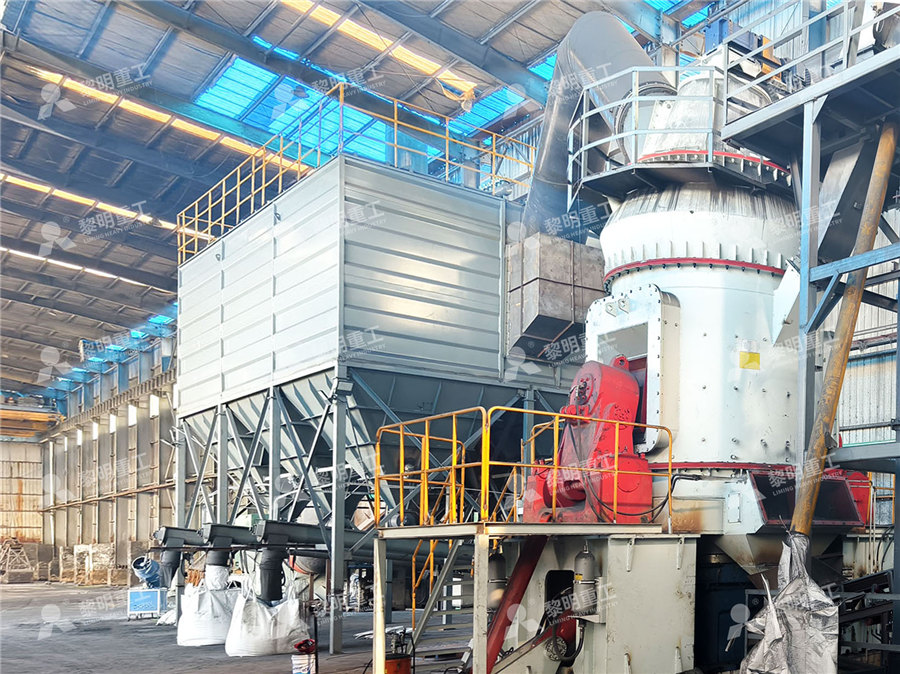
Temperature Measurements in Cement Manufacture
2018年12月14日 The burning zone The kiln shell The clinker cooler The Rotary Kiln The rotary kiln is the key component in a cement plant It is a long steel cylinder, lined with refractory brickwork to protect the outer shell from the high 5 Figure 3: Granular flow regimes and the Froude number associated with each bed movement [13] Yin et al [14] stated that the flow into the active layer depends mainly on both the Froude number (Fr = ω2R/g, where ω is the angular velocity of rotation and g the acceleration of gravity) and size ratio ( O= ã/ , where ã is the particle diameter and the radius of the kiln cylinder)Rotary kiln process: An overview of physical mechanisms, models 2021年4月13日 in a rotary kiln and heated wall of a rotary cylinder with initial moisture content of 27% of mass of the dry the solids Ghoshdastidar and Unni [12] also developed a simulation model based on steady state heat transfer of drying and preof moisture solids in the nonreacting zone of a cement rotary kiln In anotherThermal Investigation of an Indirectly Heated Rotary Kiln2016年1月1日 The followings were examined: solid phase, gas and coating temperature change in a rotary kiln Rotary kiln operating conditions studied (a) Layers of walls in cement rotary kiln firing; (b Modeling of Rotary Kiln in Cement Industry ResearchGate
.jpg)
The Refractory Lining of Rotary Kiln and the Factors Affecting Its
1) Prevent hightemperature materials, flames, and airflow from directly damaging the cylinder, protect the kiln cylinder, and avoid hightemperature deformation of the kiln cylinder 2) Prevent liquid phase clinker and harmful substances such as CO, Cl2, and SO2 from directly eroding the cylinder during the firing processmonitoring kiln operation, accurate measurement of zone temperature, reducing emission and fuel consumption A highly qualified development team and a cement manufacturer has addressed these challenges together and has developed and tested in real environment an artificial intelligencebased control algorithm for the rotary kiln in a pilot projectAI Kiln Solution For Optimized Control How To Reduce EnergyRequest PDF On Nov 19, 2022, Xin Xu and others published Prediction of Temperature in Firing Zone of Cement Rotary Kiln with Nonlinear Autoregressive Neural Network Model Find, read and cite Prediction of Temperature in Firing Zone of Cement Rotary Kiln 2023年2月25日 YL Wu et al (2018) studied a pilotscale rotary kiln that can be directly heated and found a characteristic Ushaped in temperature distribution around the kiln's cylinder Show abstract The global annual production of steel is approximately 2 billion tons, accounting for 8 % of the world's energy demand and 7 % of carbon dioxide (CO 2 ) emissions in the energy sectorRotary kiln process: An overview of physical mechanisms, models
.jpg)
Cement rotary kiln temperature prediction based on timedelay
2023年8月15日 Cement rotary kiln temperature prediction based on timedelay calculation and residual network and bidirectional novel gated recurrent unit multimodel fusion Moreover, Lu [5] applied wavelet analysis and a kernel limit learning machine to model the firing zone temperature of cement rotary kilns2024年4月15日 On the same lines, Zheng Li [24] employed SVM to construct a regression model for the firing zone of a rotary kiln However, the predictive efficacy was hindered by the Establishment of an optimal model for rotary kiln temperature field soft measurement by comparing the fitting characteristics of different machine learning Novel method for temperature prediction in rotary kiln process shell temperatures along the length of the kiln Figure 1: Simplified illustration of a rotary lime kiln with a thermal camera measuring the shell temperature Traditionally, temperature sensors at the firing end of the kiln have been used for fuel control while feed end temperature sensors have been used for induced draft fan control [8]Rotary Kiln Monitoring with Shell Temperature Visualization and 2019年5月19日 The rotary kiln of calcined active lime is generally divided into three kinds of kilns, such as 300t/400t/100t, etc The temperature of calcining zone is about 1350 °C The rotary kiln can be divided into discharge end, cooling zone, firing belt, preheating zone, feed end and temperature range from 1000 to 1350 °CAnalysis and Design of Key Parameters in Intelligent System of
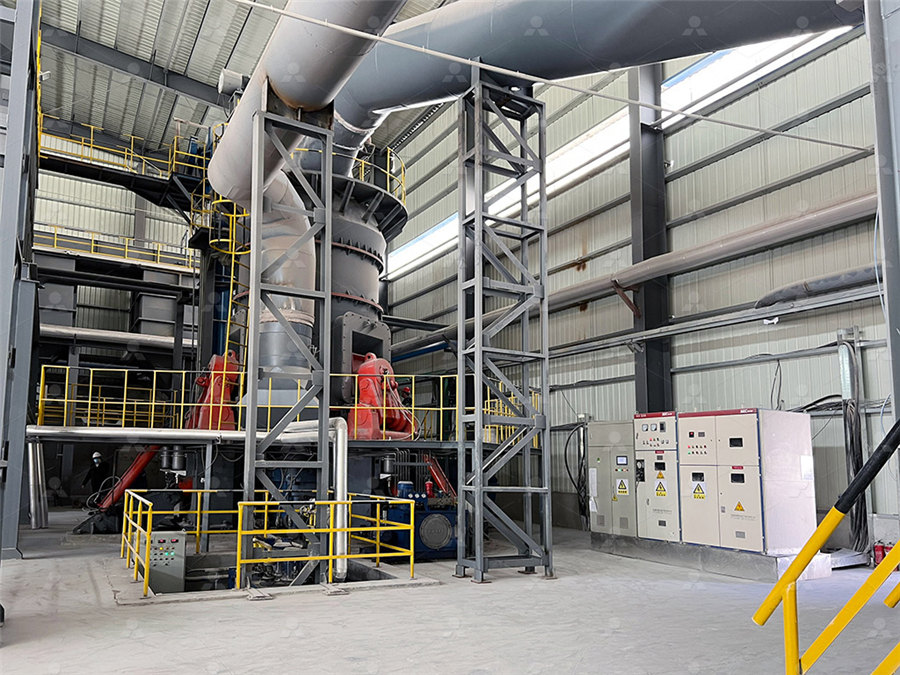
Basic Rotary Kiln different Heating zone of Pyroprocessing
2021年8月4日 Lecture5 : Basic Rotary Kiln different Heating zone of Pyroprocessing system by Dr K MohanDr K Mohan is an internationally renowned and an acclaimed cemePrevious Post Next Post Contents1 EVERYTHING YOU NEED TO KNOW ABOUT REACTIONS ZONES IN THE ROTARY KILN11 The term uppertransition zone12 The sintering zone13 The cooling (or Lowertransition) zone 14 LONG WETPROCESS KILNS15 THE DRYPROCESS KILN16 THE SEMIDRY (LEPOL) KILN17 THE PREHEATER AND PRECALCINER KILNS EVERYTHING YOU NEED TO KNOW ABOUT REACTIONS ZONES IN THE ROTARY KILNIndex Terms Burning zone temperature, Cement rotary kiln, Dynamic softsensor, Casebased reasoning, Digital filter I INTRODUCTION Rotary kiln is a kind of large scale sintering device widelyIntelligent Dynamic Modeling for Online Estimation of Burning Zone 2018年6月22日 1 The document provides answers to questions about cement rotary kilns, including the maximum safe shell temperature, differences between hot spots and red spots, factors affecting when a red spot would force a kiln to stop, oxygen enrichment technology, classifying precalciners, factors affecting the number of cyclone stages, the significance of Cement rotary kiln PDF Free Download SlideShare
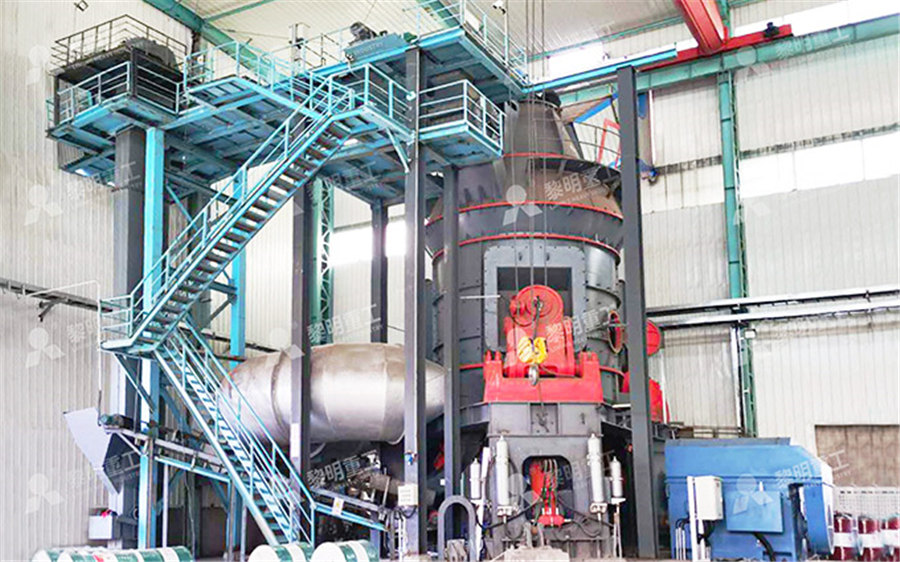
The FEECO Rotary Kiln Handbook FEECO International Inc
A rotary kiln is comprised of a rotating cylinder (called the drum), sized speciically to meet the temperature and retention time requirements of the material to be processed The kiln is set at a slight angle, in order to allow gravity to assist in moving material through the rotating cylinder Rotary kilns can be either of the directired cement rotary kiln process is presented in the following paragraphs For example [10] uses CFD to model threedimensional steady state model to predict the flow and heat transfer in a rotary kiln Others like [11] used commercial CFD code Fluent6326 to model and carried out for a full scale rotary cement kiln with multichannel coal burnerNumerical Modelling and Study of Combustion Behaviour of Rotary (1) brick damage caused by high temperature calcination NSP precalciner kiln flame temperature can reach more than 1700 ℃, the other transition zone which, throat and high temperature firing zone, cooling zone, kiln hood, cooler and the nozzle outer part of the operating temperature is far higher conventional kiln at a temperature How to Extend the service life of refractory in cement rotary kilnTemperature differences between the top and bottom of the kiln may cause the kiln to warp, and refractory is damaged It is therefore normal to provide an auxiliary drive for use during power cuts This may be a small electric motor with an independent power supply, or a diesel engineRotary kiln chemeurope
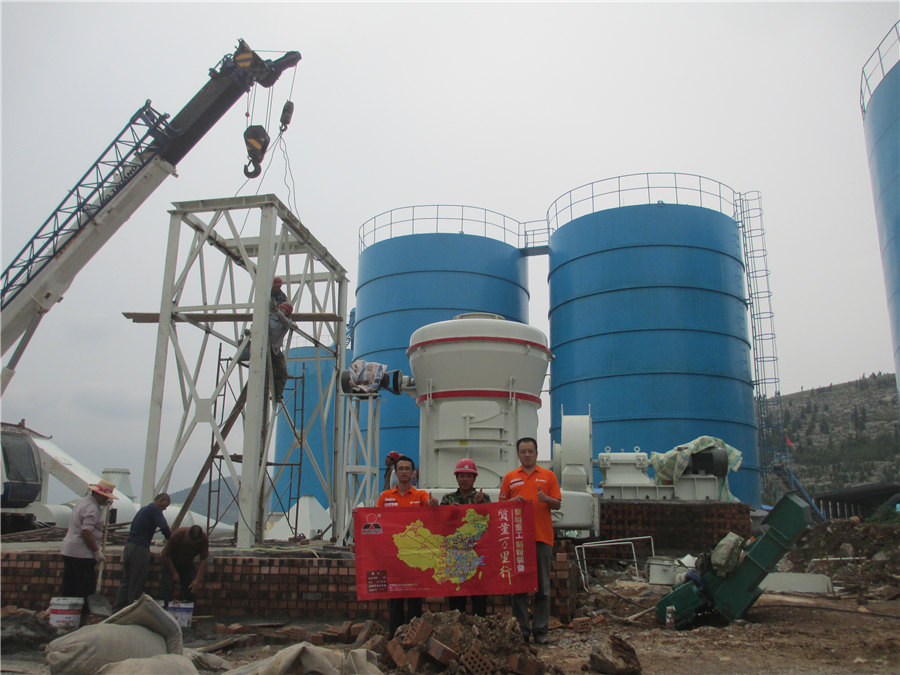
Monitoring the Ring Formation in Rotary Kiln for
2015年1月1日 Rotary kiln at high temperature seems a black box, according to steadystate heat transfer across a cylinder, roasted from 750 o C when entering to 1300 o C in firing zone, Q=Qsh (2) By solving equation (1), temperature Tst and Trt can be modeled as follows: st sh st sh st sh (3) rt st rt sh rt rt st rt rt rt 2 0 0 (4) Where st is thermal conductivity of steel plate MONITORING THE RING FORMATION IN ROTARY KILN FOR PELLET FIRINGinto a rotary kiln which raises their temperature to approximately 1370 oC (about 2500 oF) 3 6 As they progress along the rotary kiln towards the firing zone, the raw materials lose moisture and other components and form a rocklike substance called clinker, mineral lumps roughly 25 mm (1 inch) in diameter 4 Upon leaving the kiln, the hot TEMPERATURE MEASUREMENTS IN Land Instruments THE BURNING ZONE Also known as the firing zone, the burning zone is at the lower end of the rotary kiln, where the cement components are heated to about 13001450 °C (23722642 °F), forming clinker Accurate temperature measurements are critical for product quality, environmental performance and kiln lifetime KILN 3TEMPERATURE MEASUREMENTS IN Land Instruments
.jpg)
Complete Guide to Kiln Firing Temperatures SDS Industries
2023年12月26日 Unlike heat treat and glasswork, which require a greater level of specificity, potters deal in predefined temperature ranges – which correspond with pyrometric conesBefore the advent of modern programmable digital kiln controllers, kiln temperature control relied on manual kilns and the use of pyrometric cones and kiln sitters to measure when the proper kiln The temperature of the flue gas in the solution firing zone is about 1700 degrees, and the temperature of the kiln material is above 1300 degrees Generally, you should adopt refractory bricks with a high softening temperature and resistant to kiln material solution Such fire bricks are dense and have a high thermal conductivity Refractory Refractory Lining In Cement Rotary Kiln2021年4月22日 This page lists these and describes their evolution Rotary kiln terminology The Kiln Shell The shell of the kiln is made of mild steel plate Mild steel is the only viable material for the purpose, but presents the problem that the maximum temperature of the feed inside the kiln is over 1400°C, while the gas temperatures reach 1900°CCement kilnsdesignfeaturesofrotarykilns PDF SlideShareThe rotary kiln is used in many solid processes, including drying, incineration, heating, cooling, humidification, calcination and reduction This widespread application can be attributed to factors such as the ability to handle varied loads, with large variations in particle size [1]The rotary kiln is a slightly inclined steel cylinder that rests on supports (bearing rollers) with an Rotary Kiln an overview ScienceDirect Topics
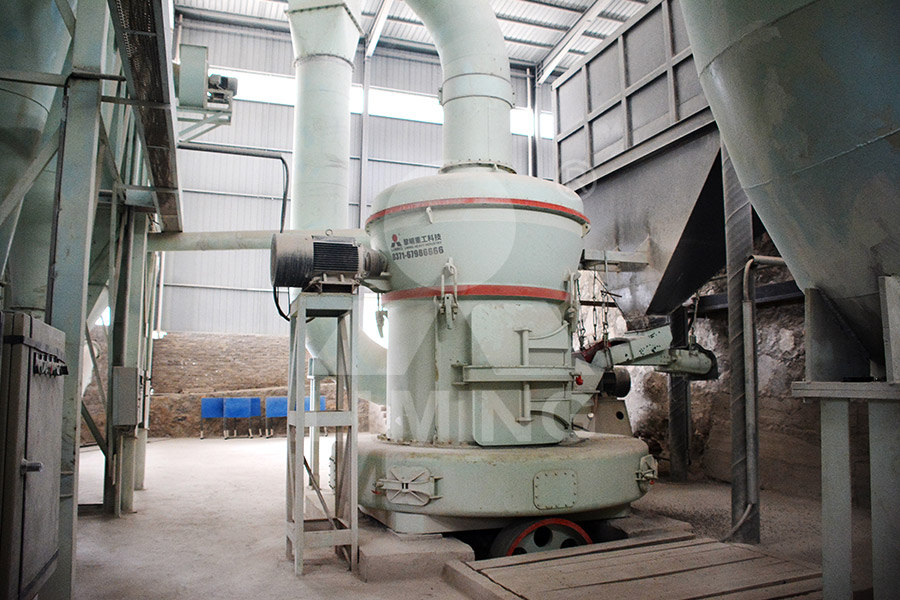
Monitoring the Ring Formation in Rotary Kiln for Pellet Firing
2015年3月15日 Figure 4 shows the axial temperature distributions of rotary kiln inner roasted from 750 o C when entering to 1300 o C in firing zone, steadystate heat transfer across cylinder with the 2024年1月9日 Although the thermal expansion coefficient of the kiln shell is greater than that of the kiln bricks, However, the temperature of the kiln shell is generally around 280–450 °C, while the temperature of the kiln bricks is generally above 800°C, and the temperature in the firing zone is more than 1,300°CThe Effects and Selection of Fire Brick Refactory Bricks For Rotary Kiln