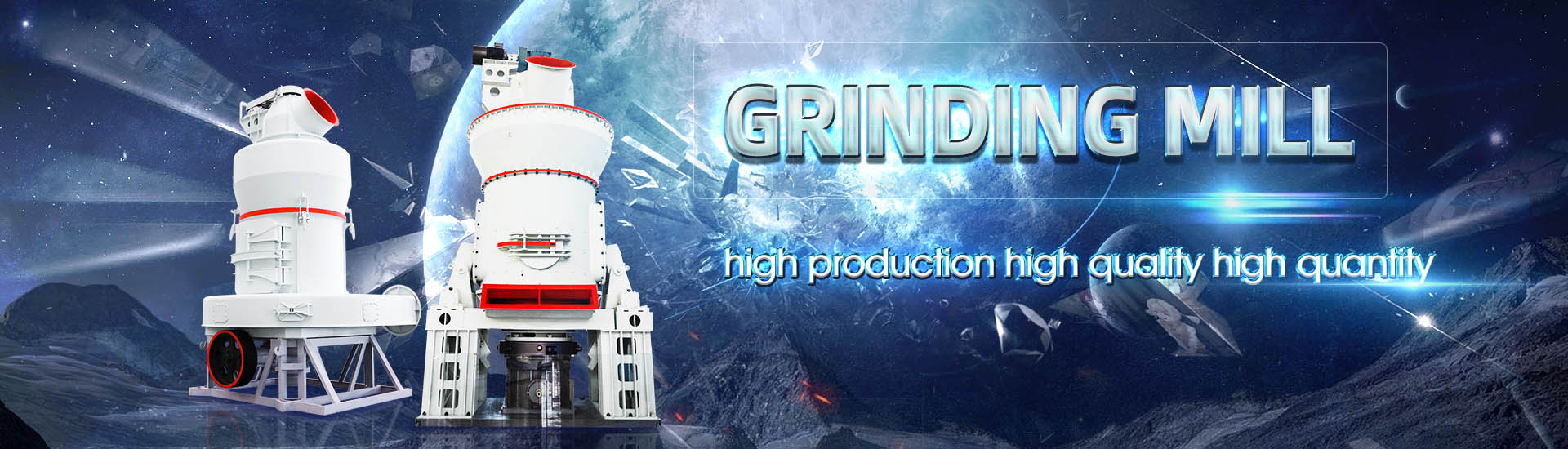
Clinker for cement plants
.jpg)
Cement Clinker: Types and Uses of Cement Clinker JK Cement
Cement clinker is a type of substance formed during the cementmaking process It is created by heating a mixture of limestone and clay at extremely high temperatures in a kiln This pebble Higher the AM, lighter the color of clinker (cement) Normal range of SM is 125 MgO is commonly present in raw meal Some of the MgO (2%) is accommodated into the clinker mineral structure, while as extra MgO forms a crystal called Clinkerization Cement Plant Optimization2020年9月29日 Alternative fuels and raw materials are increasingly used to minimise cementrelated CO 2 emissions, and increased plant efficiency is desirable from both economic and environmental perspectivesAn overview of alternative raw materials used in From a technical perspective, how does one lower the clinker content of cement? Lowering the clinkertocement ratio requires the use of Supplementary Cementitious Materials (SCMs) CLINKER SUBSTITUTION IN THE CEMENT INDUSTRY CEMBUREAU
.jpg)
Process characteristics of clinker and cement production SINTEF
• ETHZ has simulated and adapted the CAP system to different cementplant flue gases; • New ratebased model was developed and used to validate fullscale CAP simulations for cement The cement clinker manufacturing process traditionally involves intimate mixing and the subsequent heat treatment of a blend of calcareous rock, such as chalk or limestone, and Cement Clinker Production an overview ScienceDirect Topics2024年9月16日 Cement clinker is an intermediary product produced during the manufacturing of cement It looks solid and dark grey in colour It is collected as lumps or nodules appear in Cement Clinker: Its Types, Uses and CompositionThis study assessed 40 industrial clinkers from 16 cement plants, determining their physical, chemical, and mineralogical properties and the corresponding cements' strength development Unveiling the key factors for clinker reactivity and cement
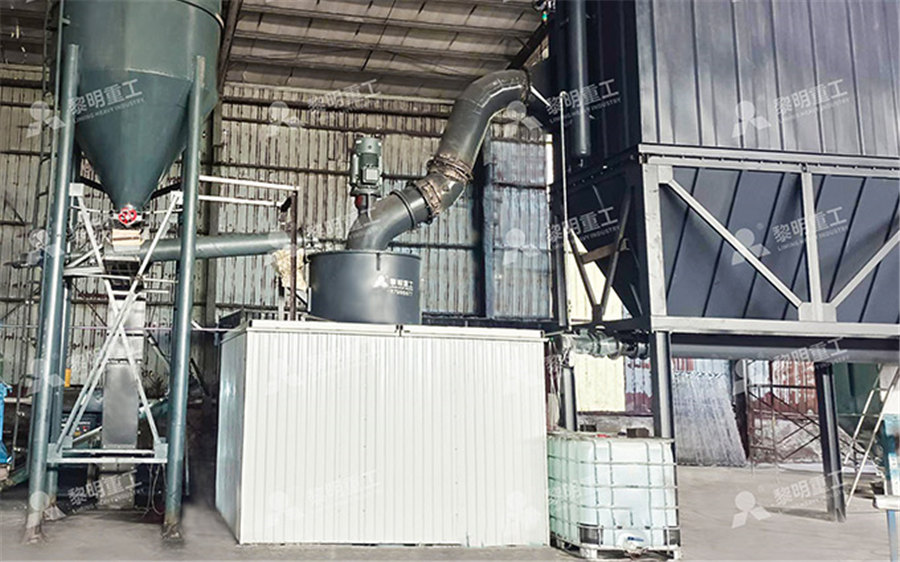
Cement Kiln, Cement Plant Kiln, Kiln In Cement Plant
Cement kiln is used to calcine cement clinker in the cement plant, also known as cement plant kiln Like we all know, cement production line include three main steps: preparation of cement raw materials, clinker production, and finished AGICO Cement is one of the leading cement plant manufacturers that offers cement kilns and other cement equipment, our cement rotary kiln has been widely applied to many cement plants Based on 60+ year’s experience and Rotary Kiln Manufacturer 1805,000t/d Cement Plant9 Clinker Discharge Dust Suppression 10 Conversions and Refurbishments 11 AUMUND Services Clinker Storage Systems The AUMUND Group Equipment for the Cement Industry is being applied worldwide in more than 10,000 plants Design, implementation and modernisation of clinker storage installations, customised as per requirement, achieve maximumClinker Storage Systems AumundSignificant amounts of electricity are then required during the milling (grinding) of clinker and other constituents to produce cement – the main binder in concrete For integrated cement plants, energy in the form of heat is required to raise the kiln temperature to over 1,450 degrees Celsius required to produce clinkerEnergy Use Cement
.jpg)
Alternative Clinker Technologies for Reducing Carbon Emissions
Reaction (1), the decarbonation of limestone, is the cause behind the largest source of CO 2 emissions in cement production Thus, reducing the amount of CaO in the binder results directly in a reduction of CO 2 emissions The second one is the hydraulic ability, or reactivity, of the phases that are present in the CaOSiO 2 system Besides the main oxides, CaO and SiO 2, in their Electrostatic precipitator (ESP), also known as high voltage electrostatic precipitator, electrostatic dust collector, is a dust collector using electric powerIt is one of the commonly used environmental protection equipment for dust gas purification It is widely used in electric power, metallurgy, building materials, chemical industry, and other industriesESP Electrostatic Precipitator Cement PlantCement grinding unit is also called the cement grinding plant dust collector, belt conveyor, bucket elevator, cement silo, powder concentrator, etc AGICO provides highquality clinker grinders and advanced cement grinding technology Skip to content Blog Contact About Cases Factory CONTACT US info@cementplantequipment CALL US Cement Grinding Unit Clinker Grinder AGICO CementThe clinker cooler, also known as grate cooler or cement cooler, it is a necessary equipment of cement clinker productionThe clinker cooler is mainly used to cool and transport the cement clinker At the same time, cement cooler also provide hotair for rotary kiln and calciner, it is the main equipment of heat recovery for burning system The cooler will make a sufficient heat Clinker Cooler Cement Plant
.jpg)
Cement kiln Wikipedia
Portland cement clinker was first made (in 1825) in a modified form of the traditional static lime kiln [2] [3] [4] The basic, eggcup shaped lime kiln was provided with a conical or beehive shaped extension to increase draught and thus obtain the higher temperature needed to make cement clinkerFor nearly half a century, this design, and minor modifications, remained the only 2024年11月23日 Cement Extraction, Processing, Manufacturing: Raw materials employed in the manufacture of cement are extracted by quarrying in the case of hard rocks such as limestones, slates, and some shales, with the aid of blasting when necessary Some deposits are mined by underground methods Softer rocks such as chalk and clay can be dug directly by Cement Extraction, Processing, Manufacturing Britannica2020年10月15日 This research focused the role to study the effects and ways to control the chemical composition of clinker for better cement production Cement is a substance produced by grinding a mixture of a Effects and Control of Chemical Composition of The grate cooler is a quenching type cement cooler apply for clinker production in the cement manufacturing plant AGICO CEMENT offers highefficiency grate cooler and other types of clinker cooler as you need, send inquiry now! Skip to Grate Cooler In Cement Plant Clinker Cooler,
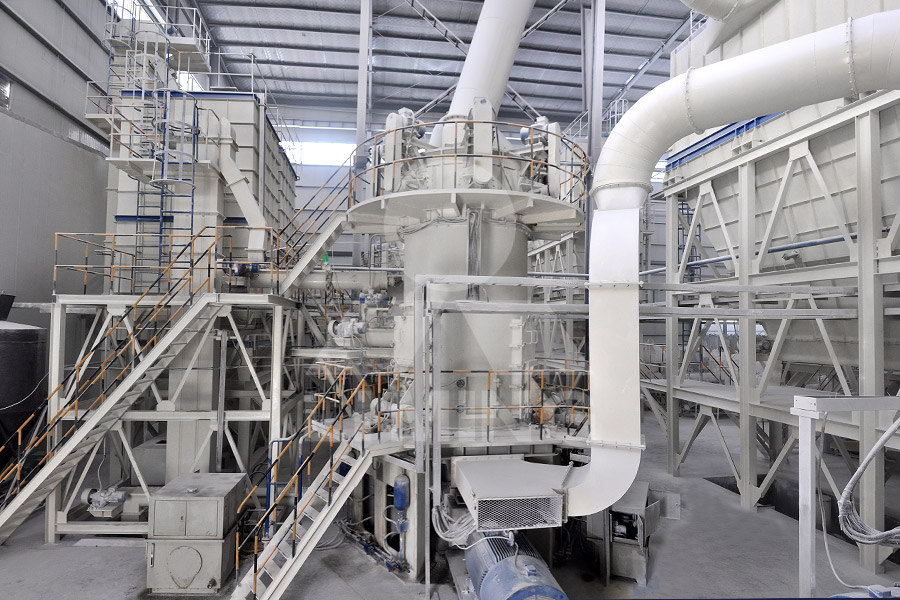
Process characteristics of clinker and cement production SINTEF
Continuous high temperature process in the cement industry: Calcination and cement clinker burning Calcination of raw material CaCO 3 => CaO + CO 2 Process emissions of raw material: = 054 t CO 2 /t clinker Endotherm reaction at 950 °C ca 1700 MJ/t clinker ≈ 50% of energy Cement clinker burning at 1450 °C formation of hydraulicIt is sometimes misunderstood for an integrated cement plant which also manufactures the clinker The integrated plant process involves very high temperatures and the emission of high volumes of particulates and gaseous effluent This is not the case for a straightforward CGP as in the present proposed projectEVERYTHING YOU NEED TO KNOW ABOUT ESTABLISHING CEMENT GRINDING PLANT 2024年11月26日 To meet the anticipated increase in cement demand, Cahya Mata Cement is developing a 10 million MT per annum grinding plant adjacent to the Mambong clinker plant Construction of the new RM1900 million plant began in 2014 and cement production is set to commence by the first half of 2016 (1H 2016)Cahya Mata Sarawak CementAGICO is a trusted cement plant manufacturer from China provides a flexible EPC project for cement plant, we also offer cement equipment rotary kiln, cement roller press, cement dryer, clinker cooler, cement silo, and related cement plant equipment AGICO CEMENT is a service provider for cement engineering integrated solutions Since 2000 Cement Plant, Cement Equipment Cement Plant Manufacturer
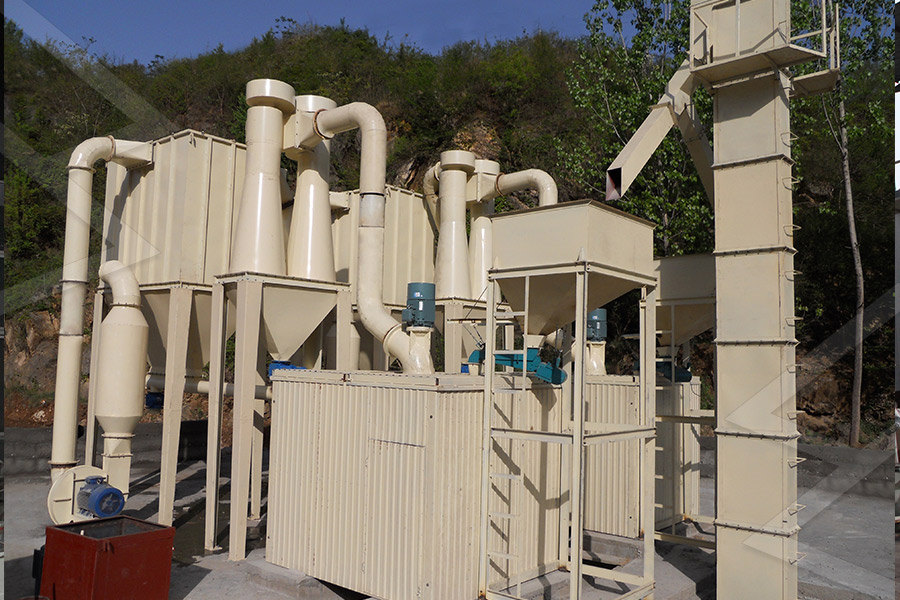
Baghouse Dust Collector Pulsejet Dust Filter In Cement Plant
PPC type baghouse dust collector is widely used in building materials, cement, metallurgy, machinery, chemical industry, and refractory industry, especially for dust collection system of cement plant crusher, cement packaging machine, warehouse top, clinker cooler, and various cement grinding machine (or dust removal system), it has a wide applicationRaw Materials Crushing, Storing and Grinding Clinker calcination is the most crucial part of the whole process of cement manufacturing At this stage, ground raw materials will be sent into the cement kiln and be heated at a high temperature to produce chemical reactions with each other, eventually forming clinker In addition, clinkers that just complete the calcination will have a Cement Clinker Calcination in Cement Production Process AGICO Cement Reducing cement plant GHG emissions and product carbon intensity are important goals for both the cement industry and its customers To assist the US cement industry in evaluating its efforts to decarbonize, EPA calculated the 2019 carbon intensities for the intermediate and final products of cement plants: clinker and cementUS Cement Industry Carbon Intensities (2019) USPrecalciner forms the clinker calcining system in the new dry process cement plant together with cement preheater, rotary kiln, and cement cooler In addition to cement calciner, AGICO also provides other highquality clinker calcination equipment, such as cyclone preheater, cement rotary kiln, grate cooler, rotary cooler, etcPrecalciner – Calciner In Cement Plant, Cement Calciner Calciner

Cement Clinker Grinding Plant ball mills supplier
25195tph clinker grinding plant, best option for start up at low cost Cement clinker grinding unit with ball mill, roll press or VRM 24×7 Consulting Support2023年11月1日 Cement plants of tomorrow will have to implement all CO 2 abatement and saving measures to the best extent possible Reducing the clinker factor, optimising the reactivity of the clinker, substituting fossil fuels by alternative fuels and using alternative raw materials are pathways which will still play a growing role in future cement productionThe cement plant of tomorrow ScienceDirectAGICO Cement is a cement plant manufacturer supplies shaft kiln, vertical shaft kiln and other kinds forming a strong wind and raw materials to ensure yield and quality of cement clinker Highquality clinker, the cement linker has a 3 Shaft kiln Cement PlantCement plants often use hammer mills, impact crushers and even jaw crushers We manufacture many types of hammers adaptables to crushers from brands such as Thyssenkrupp® Polysius®, Flsmidth® Grates and liner segments are also manufactured, as well as complete rotorsSpare and wear parts for cement plants Aceros y Suministros SL
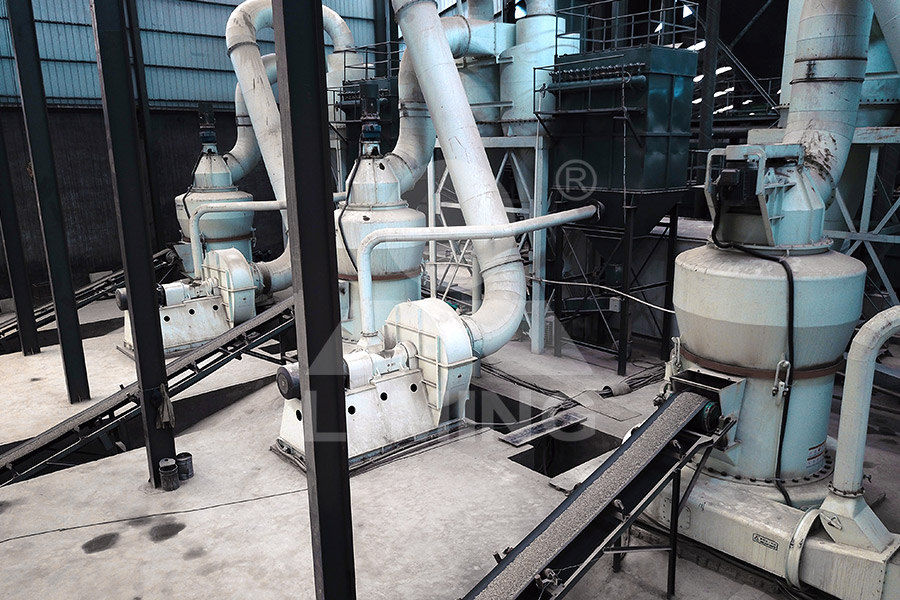
Sustainable transition towards biomassbased cement industry: A
2022年7月1日 Cement plants undertake various measures to reduce CO 2 emissions These include upgrading to newer kiln technologies, clinker substitution, fuel substitution, process optimisation, and recently carbon capture and storage2020年5月14日 Future cement plants could leapfrog competitors by combining digital technology and more sustainable operations Finally, incorporating alternative fuels such as waste and biomass to replace fossil fuels, a multidecade trend in the industry, could reduce emissions by nearly 10 percent by 2050 2 Technology roadmap: Lowcarbon transition in the cement Laying the foundation for zerocarbon cement McKinsey31 Cement clinker production It is true that cement plants have become the main contributors of energy and natural resource consumption as well as CO 2 emissions, especially in developing countries (Aprianti et al, 2015; Oh et al, 2014; Shi et al, 2011)Cement Clinker Production an overview ScienceDirect TopicsClinker cooler is also called cement cooler It is the main equipment in the cement clinker manufacturing process Rotary cooler and the grate cooler are the most commonly used coolers in cement plants Skip to content Blog Contact About Cases Factory CONTACT US info@cementplantequipment CALL US +86 REQUEST A QUOTE Clinker Cooler Cement Cooler AGICO Cooler In Cement Plant
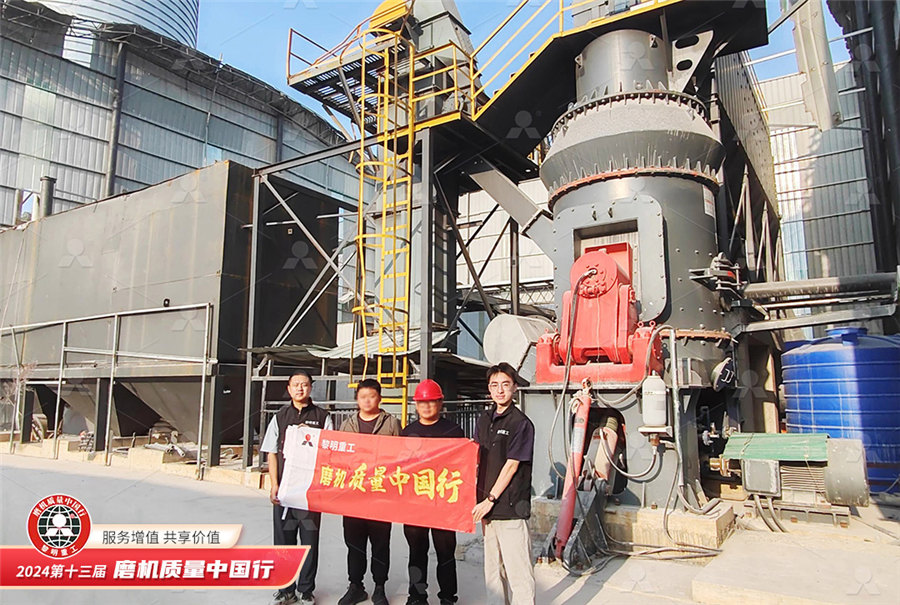
Better and cheaper cement: Optimising the right clinker properties
2021年5月24日 Large clinker nodules (Figure 2) are difficult to cool, transport and grind into cement Clinker should ideally have a smaller average nodule size and a narrow nodule size range More uniformly sized clinker is more evenly distributed into the cooler and has more consistent bed porosity, which enables more stable cooler and kiln operationAGICO Cement supplies cement preheater, preheater in cement plant as you need! Skip to content +86 s about blog contact EN ES RU Menu Menu Home; Cement Equipment and prepare for the clinker production Why cement preheater is necessary for rotary kiln cement plant Cyclone Preheater Cement PlantCement kiln is used to calcine cement clinker in the cement plant, also known as cement plant kiln Like we all know, cement production line include three main steps: preparation of cement raw materials, clinker production, and finished Cement Kiln, Cement Plant Kiln, Kiln In Cement Plant AGICO Cement is one of the leading cement plant manufacturers that offers cement kilns and other cement equipment, our cement rotary kiln has been widely applied to many cement plants Based on 60+ year’s experience and Rotary Kiln Manufacturer 1805,000t/d Cement Plant
.jpg)
Clinker Storage Systems Aumund
9 Clinker Discharge Dust Suppression 10 Conversions and Refurbishments 11 AUMUND Services Clinker Storage Systems The AUMUND Group Equipment for the Cement Industry is being applied worldwide in more than 10,000 plants Design, implementation and modernisation of clinker storage installations, customised as per requirement, achieve maximumSignificant amounts of electricity are then required during the milling (grinding) of clinker and other constituents to produce cement – the main binder in concrete For integrated cement plants, energy in the form of heat is required to raise the kiln temperature to over 1,450 degrees Celsius required to produce clinkerEnergy Use CementReaction (1), the decarbonation of limestone, is the cause behind the largest source of CO 2 emissions in cement production Thus, reducing the amount of CaO in the binder results directly in a reduction of CO 2 emissions The second one is the hydraulic ability, or reactivity, of the phases that are present in the CaOSiO 2 system Besides the main oxides, CaO and SiO 2, in their Alternative Clinker Technologies for Reducing Carbon Emissions Electrostatic precipitator (ESP), also known as high voltage electrostatic precipitator, electrostatic dust collector, is a dust collector using electric powerIt is one of the commonly used environmental protection equipment for dust gas purification It is widely used in electric power, metallurgy, building materials, chemical industry, and other industriesESP Electrostatic Precipitator Cement Plant
.jpg)
Cement Grinding Unit Clinker Grinder AGICO Cement
Cement grinding unit is also called the cement grinding plant dust collector, belt conveyor, bucket elevator, cement silo, powder concentrator, etc AGICO provides highquality clinker grinders and advanced cement grinding technology Skip to content Blog Contact About Cases Factory CONTACT US info@cementplantequipment CALL US The clinker cooler, also known as grate cooler or cement cooler, it is a necessary equipment of cement clinker productionThe clinker cooler is mainly used to cool and transport the cement clinker At the same time, cement cooler also provide hotair for rotary kiln and calciner, it is the main equipment of heat recovery for burning system The cooler will make a sufficient heat Clinker Cooler Cement PlantPortland cement clinker was first made (in 1825) in a modified form of the traditional static lime kiln [2] [3] [4] The basic, eggcup shaped lime kiln was provided with a conical or beehive shaped extension to increase draught and thus obtain the higher temperature needed to make cement clinkerFor nearly half a century, this design, and minor modifications, remained the only Cement kiln Wikipedia2024年11月23日 Cement Extraction, Processing, Manufacturing: Raw materials employed in the manufacture of cement are extracted by quarrying in the case of hard rocks such as limestones, slates, and some shales, with the aid of blasting when necessary Some deposits are mined by underground methods Softer rocks such as chalk and clay can be dug directly by Cement Extraction, Processing, Manufacturing Britannica