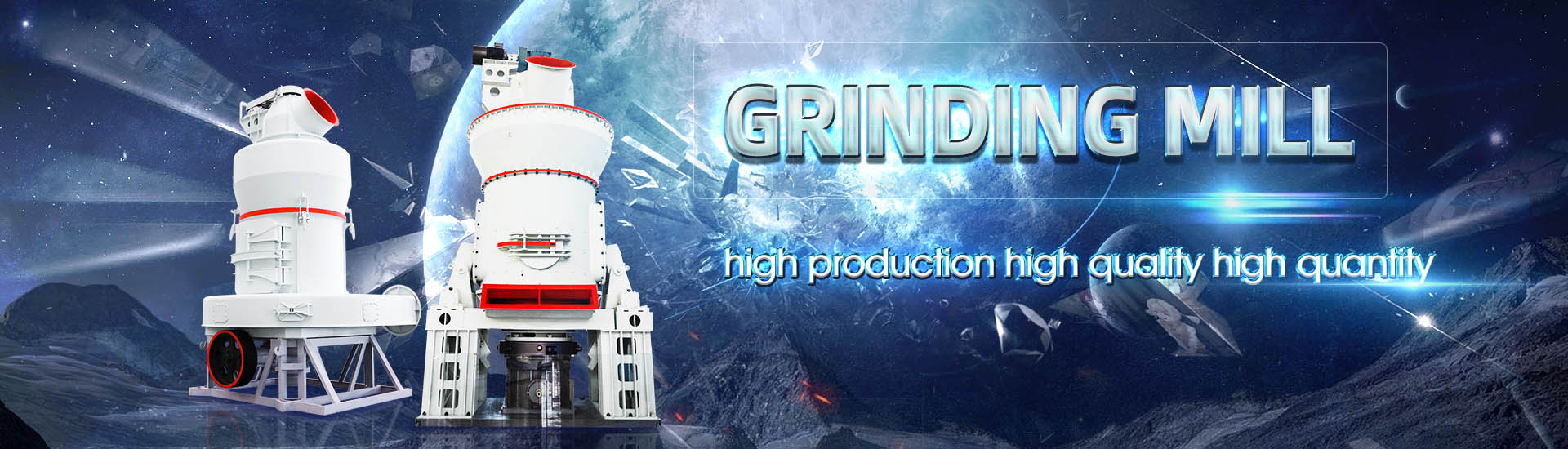
High frequency grinding mill energy consumption
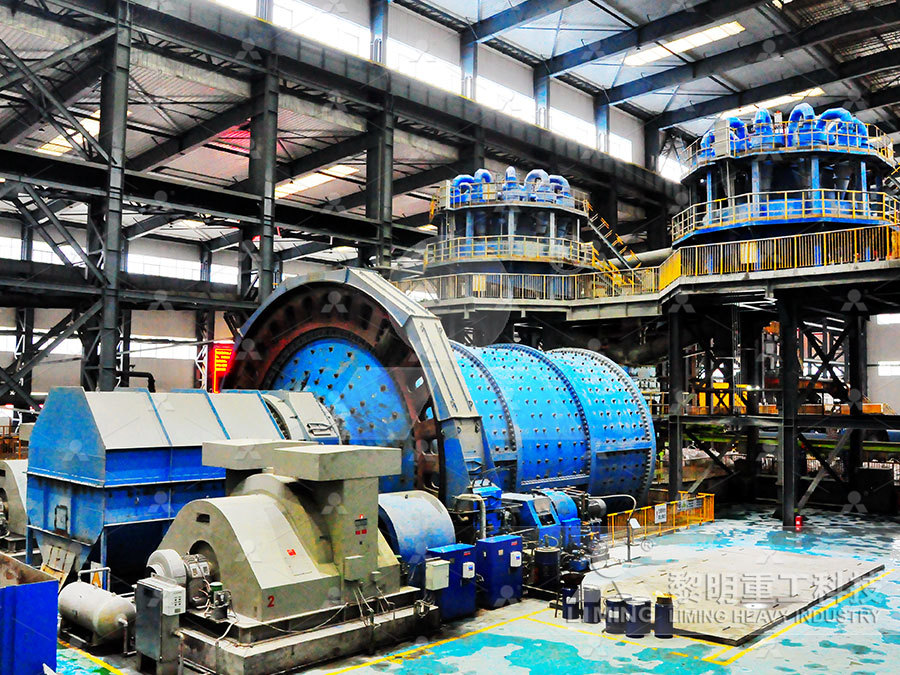
Breaking Down Energy Consumption in Industry Grinding Mills
This paper reports the results of an investigation targeting two objectives: (1) characterising energy outputs in industrial grinding mill circuits, and (2) identifying the potential for recovering 2018年1月1日 Specific energy consumption was determined as a function of material removal rate and compared to results of milling and turning processes The key influence factors on Energy efficiency of stateoftheart grinding processes2023年11月1日 This paper demonstrates the feasibility of using a ceramic medium stirring mill to reduce the energy consumption of grinding operations through an industrial verification Energy conservation and consumption reduction in grinding Grinding mills are infamous for their extremely low energy efficiency It is generally accepted that the energy required to produce new mineral surfaces is less than 1% of the electricityBREAKING DOWN ENERGY CONSUMPTION IN INDUSTRIAL
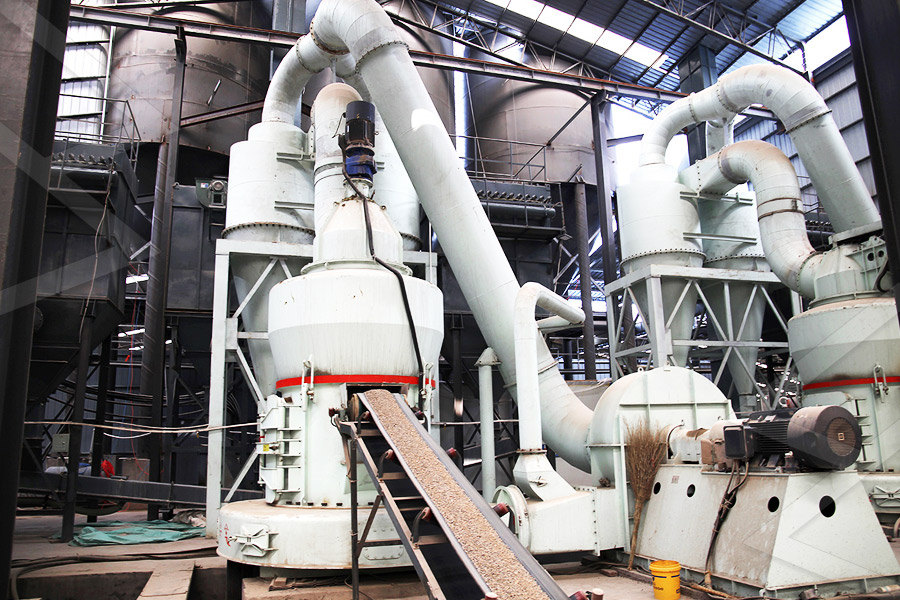
Breaking Down Energy Consumption in Industrial Grinding Mills
2019年1月1日 This paper reports the results of an investigation that characterized energy outputs in industrial grinding mill circuits It identifies and discusses the potential for recovering Datadriven machine learning approaches have emerged as effective solutions, enabling energy consumption prediction and optimization These methods offer valuable insights to improve the Predicting Grinding Mill Power Consumption in Mining: A 2017年7月1日 This paper analyses how properly designed control systems allow a better usage of the capacity of grinding circuits, and a reduction of the specific energy consumption even Reducing the energy footprint of grinding circuits: the process Assessment of comminution energy intensity has traditionally been confined to the crusher and mill motor power consumption However, a measure of the embodied energy consumed through media wear is required to compare Energy Curve Enhancement Blog 7: Including grinding
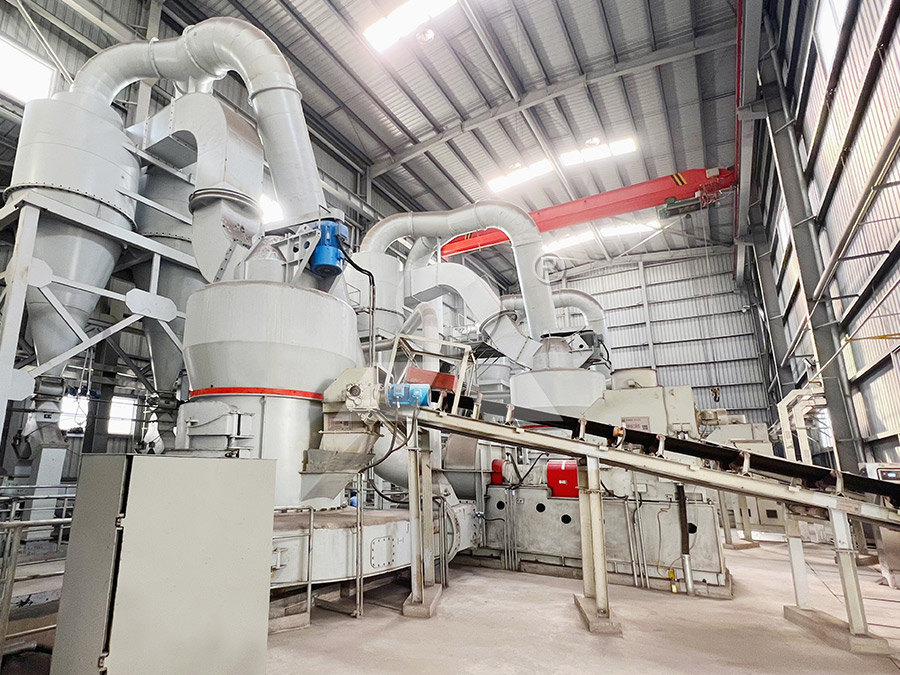
Breaking down energy consumption in industrial grinding mills
2019年11月15日 It was reported that 36% of the energy in mining was consumed by comminution processes (Ballantyne et al, 2012) A survey of three (SAG)/ball mill circuits by 2023年4月24日 Grinding is the final stage of comminution, which reduces particle size to micron size level The size reduction is achieved by attrition, abrasion, and impact between the ore itself and between the ore particles and grinding media []According to Swart et al [], ball mills are mostly used because of their very high size reduction ratio, although they have a very low Grinding Media in Ball MillsA Review [v1] Preprints2013年7月15日 Increasing capacity and efficien cy of grinding circuits with high frequency determining the specific energy requirement of tumbling mill (grinding) higher specific energy consumption(PDF) Energy Efficient Ball Mill Circuit – Equipment optimum for a certain value of rotor frequency Keywords: biomass grinding, hammer mill, energy consumption, rotor frequency Introduction Lately, decreasing greenhouse gas emissions to the atmosphere and the independence of global economy from fossil fuels are the main arguments to use renewable resources for energy production [1]ASPECTS REGARDING GRINDED SALIX VIMINALIS DISTRIBUTION AND ENERGY
.jpg)
Highefficiency and energyconservation grinding technology using
2022年1月1日 Recently, to overcome the problems of high energy consumption, large medium consumption and iron pollution in traditional grinding operation [5–7], Northeastern University has innovatively developed a special ceramicmedium stirred mill (as shown in previously published article by Zhang et al [8]) with small pitch, high speed and low energy consumption2020年3月15日 As reported by Dundar [5], the better classification efficiency achieved with high frequency screens, assisted to reduce the circulating load and provided a more homogenous particle size distribution returning to the mill, leading to lower volume to be pumped (energy savings), improved grinding energy efficiency (energy savings) and increasing the circuit Investigating the benefits of replacing hydrocyclones with high 2012年12月29日 Energy efficient comminution circuits (efficient classification) 1525% reduction in grinding energy by replacing cyclones with screens (Jankovic and Valery, 2012) CO 2 savings associated with The Impact Of Classification On The Energy Efficiency Of Grinding 2020年10月1日 Effect of grinding aids on the kinetics of fine grinding energy consumed of calcite powders by a stirred ball mill Adv Powder Technol , 20 ( 4 ) ( 2009 ) , pp 350 354 View PDF View article View in Scopus Google ScholarEvolution of grinding energy and particle size during dry ball
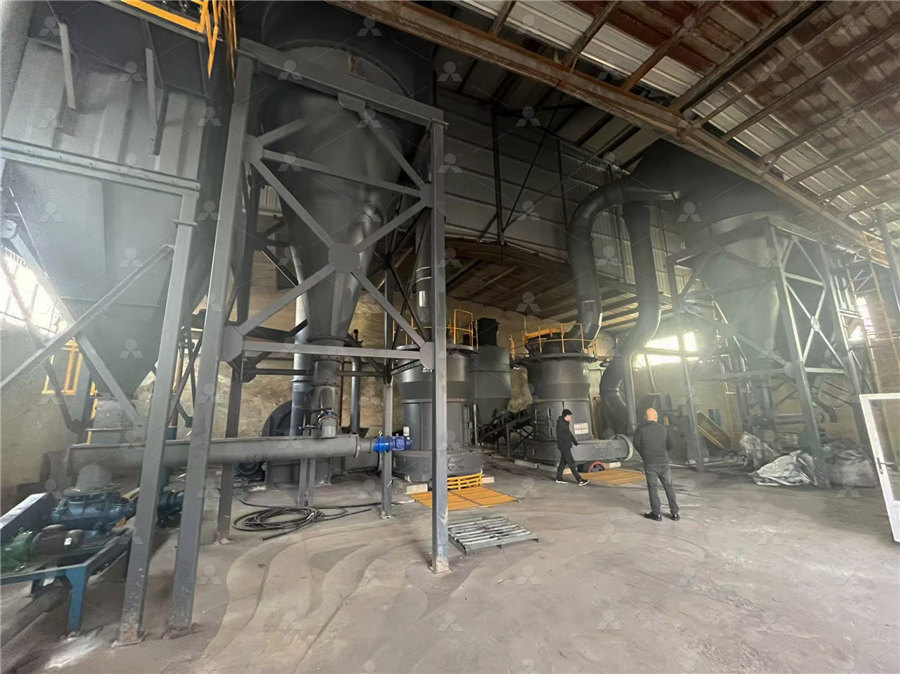
High Frequency Grinding Alpha Industrial
Power consumption: 11,1 kVA: 14,9 kVA: 18,5 kVA: 23,8 kVA: 30,7 kVA: 34,4 kVA: 52 FEIN highfrequency power tools can also be used as portable devices on the construction site or on stationary grinding stations Highfrequency costeffective energy and maintenance costs, highfrequency power tools are much more costeffective than A growing demand within the minerals industry for sustainable development and the introduction of carbon taxes have resulted in a significant focus on improving the energy efficiency of comminution circuits However, in this drive for improved energy efficiency the role of classification has been overlooked Inefficient classification and large recirculating loads The Impact of Classification on the Energy Efficiency of Grinding The alternative circuit uses highfrequency screens instead of cyclones with the same size semiautogenous grinding (SAG) and the ball mill The capacity of the grinding circuit being evaluated is 1875 t/h and the circuit is required to deliver a final product with a P80 of 75 μmThe Impact Of Classification On The Energy Efficiency Of Grinding HighFrequency Screen in the Grinding ircuit LeadZinc Grinding ircuit E Sarp ZENCIRCIa, H Melik Çiftçia, Binnur Kırıma, Berat Bük a, tonnage of the mill is 47 tph The unit energy consumption is 1359 kWh/ton and is constant The parameters of the sampling conditions are presented in Error!The use of the TwoStage lassification System Developed by the
.jpg)
Energy consumption of twostage fine grinding of Douglasfir
2018年3月12日 The energy consumption of hammer mill grinding increases exponentially as PF × t for 3phase delta connection, where V is the line voltage, I the line current, PF the power factor, and t the grinding time When the frequency was less than 60 Hz the hammer mill’s lowenergy and highvolume production capacity in the coarse their high specific energy consumption; a mill filled with balls, working idle, consumes approximately as much energy as at fullscale capacity, ie, during the grinding of materialA Comparative Study of Energy Efficiency in Tumbling Mills with High capacity Low energy consumption Reduced noise level The patented, closed rotor design can save up to 20% in energy consumption compared to traditional rotor designs Feed system for uniform screen load Low consumption – high performance The closed, aerodynamic rotor design directs the material straight out towards the screen,Hammer mills Highperformance grinding ANDRITZ2024年11月11日 In evaluating ore grinding energy consumption using the Bond ball mill work index, discrepancies were identified As a result, an investigation into the determination method of Hou Ying (HY) wet ball milling work index (WHY) for Gongchangling magnetite ore was conducted to determine the correlation between WHY and grinding energy consumption at varying Exploring the Link between HY Wet Ball Mill Work Index and Grinding
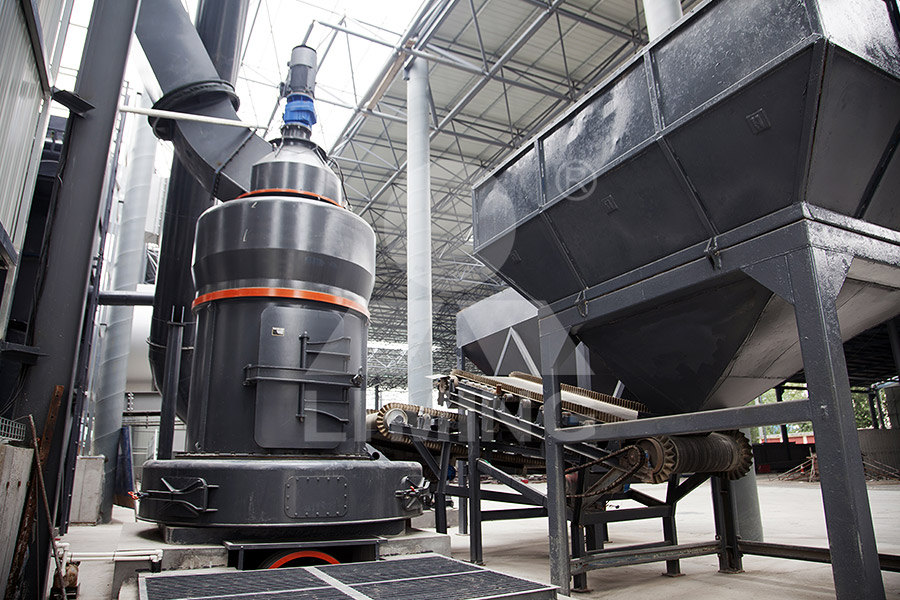
Grinding Media in Ball MillsA Review ResearchGate
Figure 1 Showing electrical energy and embodied energy for different types of tumbling mills Adapted from [2] Recently, it was realised that highgrade ores are depleting fast and are almost 2018年5月23日 So, specific energy consumption for grinding using a hammer mill can reach 50–65 kJ/kg for harvested Miscanthus biomass, and 35–50 kJ/kg for dried energetic willow, using a 10 mm orifice sieve Aspects regarding grinded Salix viminalis distribution and energy The power input P to one section of the grinding ball mill was recorded at 3000 kW, while the specified ball mill capacity q stood at 275 t/h Then, according to Eq 4, the calculated grinding energy consumption W c of the ball mill amounts to 109091 kW h/t Further, applying the Bond correction coefficient, the corresponding grinding power Exploring the Link between HY Wet Ball Mill Work Index and Grinding A VibroEnergy Grinding Mill (Type AM100) containing 5 tonnes of High Density Alumina media wears at 00017% per hour when grinding Zircon Sand – one of the hardest minerals used in the ceramic industryGrinding Machines Designed and Manufactured by William
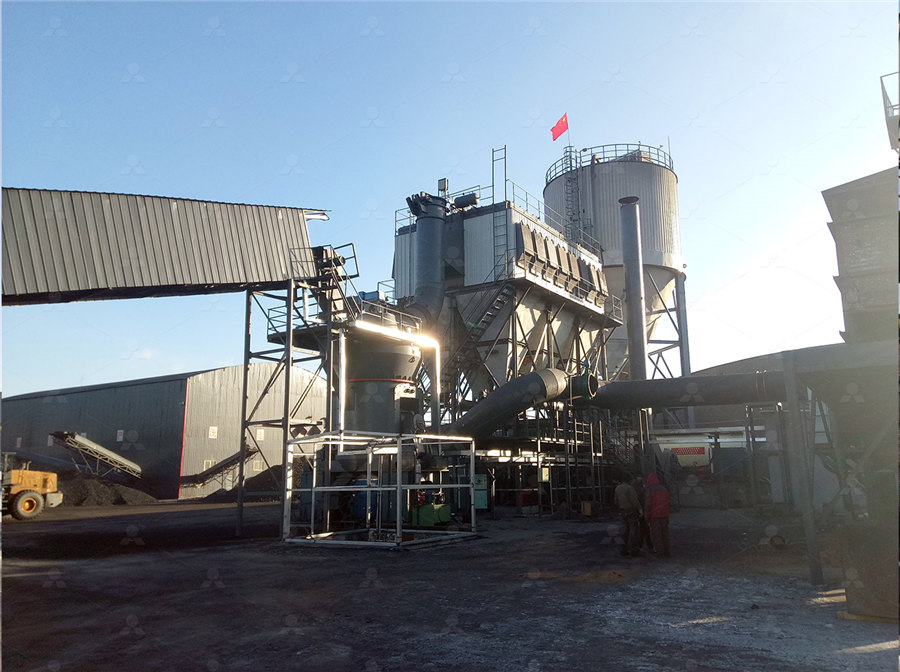
Empirical mode decomposition based hybrid ensemble model
2019年5月1日 The electrical energy consumption of the cement grinding process is the time series that should be forecasted We regard the time series as x t, t = 1, 2,, N, and x ̂ t + m is the mstepahead forecasting in period tIn terms of previous models and algorithms described above, the EMD LSSVRQES model is formulated as illustrated in Fig 3The energy consumption of hammer mill grinding increases exponentially as a function of decreasing screen mesh size [13, 14] In addition, SEC was affected by the material feed rate; a high feed rate will use less energy per unit mass than a low feeding rate TheEnergy consumption of twostage fine grinding of Douglasfir 2020年3月1日 Lower bypass and sharper separation provided by highfrequency screens are the major factors affecting the capacity of the circuit and the results showed that 13% more throughput is achieved with Investigating the benefits of replacing hydrocyclones with high Retsch High Energy Ball Mill EMAX with 2 Grinding Stations; Previous Retsch XRDMill McCrone, 100240 V, 50/60 Hz £528000 The High Energy Ball Mill Emax combines highfrequency impact, Power consumption ~ 3100W (VA) Retsch High Energy Ball Mill EMAX with 2 Grinding
.jpg)
THE BENEFITS OF HIGH CLASSIFICATION EFFICIENCY IN CLOSED BALL MILL
2013年1月1日 The specific energy consumptions of the grinding equipment and the standard bond work indexes, used 100μm screen, of raw materials are given belowCircuitBond work index (kWh/t)Specific energy area in the cement mill grinding process: A method combining dualfrequency principal component reducing system energy consumption However, due to the complexity of the cement grinding process, highfrequency variable data is greater than 100, the cumulative variance hardly increases; Prediction of cement specific surface area in the cement mill grinding 2023年7月10日 The present literature review explores the energyefficient ultrafine grinding of particles using stirred mills The review provides an overview of the different techniques for size reduction and the impact of energy requirements on the choice of stirred mills It also discusses the factors, including the design, operating parameters, and feed material properties, EnergyEfficient Advanced Ultrafine Grinding of Particles UsingIn contrast, large grinding media collide with each other considerably more frequently with high collision energy The mill uses more The outcome of the grinding process is significantly influenced by the frequency, energy, and type of grinding 30 Liu, G Energy Consumption in Common Fine Grinding Mills; DuPont’s EnergyEfficient Advanced Ultrafine Grinding of ProQuest
.jpg)
Increasing Throughput Reducing Energy Consumption and Minimizing
PDF On Sep 1, 2015, Marcelo Perrucci and others published Increasing Throughput Reducing Energy Consumption and Minimizing Wear on Grinding Mills Find, read and cite all the research you need 2020年3月18日 The assessment of engineering objects in terms of energy consumption is an important part of sustainable development Many materials, including those from the energy sector, need to undergo earlier processing, eg, grinding Grinding processes still demand a significant amount of energy, whereas current energy assessment methods do not take into The Integrated Energy Consumption Index for Energy Biomass Grinding 2024年10月16日 Presumably, at higherenergy grinding conditions, the transfer coefficient α starts to decrease: for example, because more energy is transferred to heat or consumed through other channels Indeed, the aggregate chargeability suffers a kink at the same point at which the particle size ceases to behave properly: a change in the grinding mechanism apparently Particle aggregation and the grinding limit in high energy ball mill2023年4月24日 Grinding is the final stage of comminution, which reduces particle size to micron size level The size reduction is achieved by attrition, abrasion, and impact between the ore itself and between the ore particles and grinding media []According to Swart et al [], ball mills are mostly used because of their very high size reduction ratio, although they have a very low Grinding Media in Ball MillsA Review [v1] Preprints
.jpg)
(PDF) Energy Efficient Ball Mill Circuit – Equipment
2013年7月15日 Increasing capacity and efficien cy of grinding circuits with high frequency determining the specific energy requirement of tumbling mill (grinding) higher specific energy consumptionoptimum for a certain value of rotor frequency Keywords: biomass grinding, hammer mill, energy consumption, rotor frequency Introduction Lately, decreasing greenhouse gas emissions to the atmosphere and the independence of global economy from fossil fuels are the main arguments to use renewable resources for energy production [1]ASPECTS REGARDING GRINDED SALIX VIMINALIS DISTRIBUTION AND ENERGY 2022年1月1日 Recently, to overcome the problems of high energy consumption, large medium consumption and iron pollution in traditional grinding operation [5–7], Northeastern University has innovatively developed a special ceramicmedium stirred mill (as shown in previously published article by Zhang et al [8]) with small pitch, high speed and low energy consumptionHighefficiency and energyconservation grinding technology using 2020年3月15日 As reported by Dundar [5], the better classification efficiency achieved with high frequency screens, assisted to reduce the circulating load and provided a more homogenous particle size distribution returning to the mill, leading to lower volume to be pumped (energy savings), improved grinding energy efficiency (energy savings) and increasing the circuit Investigating the benefits of replacing hydrocyclones with high
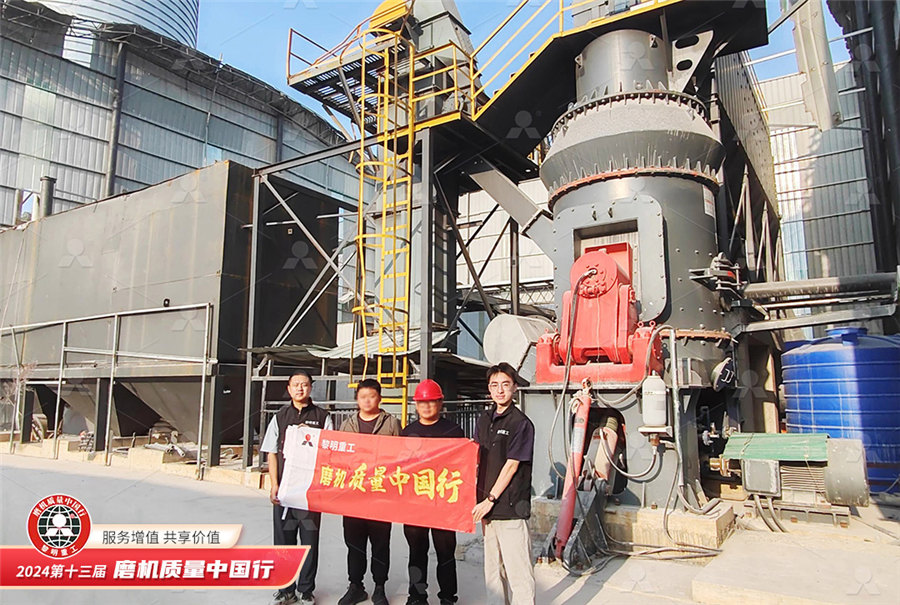
The Impact Of Classification On The Energy Efficiency Of Grinding
2012年12月29日 Energy efficient comminution circuits (efficient classification) 1525% reduction in grinding energy by replacing cyclones with screens (Jankovic and Valery, 2012) CO 2 savings associated with 2020年10月1日 Effect of grinding aids on the kinetics of fine grinding energy consumed of calcite powders by a stirred ball mill Adv Powder Technol , 20 ( 4 ) ( 2009 ) , pp 350 354 View PDF View article View in Scopus Google ScholarEvolution of grinding energy and particle size during dry ball Power consumption: 11,1 kVA: 14,9 kVA: 18,5 kVA: 23,8 kVA: 30,7 kVA: 34,4 kVA: 52 FEIN highfrequency power tools can also be used as portable devices on the construction site or on stationary grinding stations Highfrequency costeffective energy and maintenance costs, highfrequency power tools are much more costeffective than High Frequency Grinding Alpha IndustrialA growing demand within the minerals industry for sustainable development and the introduction of carbon taxes have resulted in a significant focus on improving the energy efficiency of comminution circuits However, in this drive for improved energy efficiency the role of classification has been overlooked Inefficient classification and large recirculating loads The Impact of Classification on the Energy Efficiency of Grinding
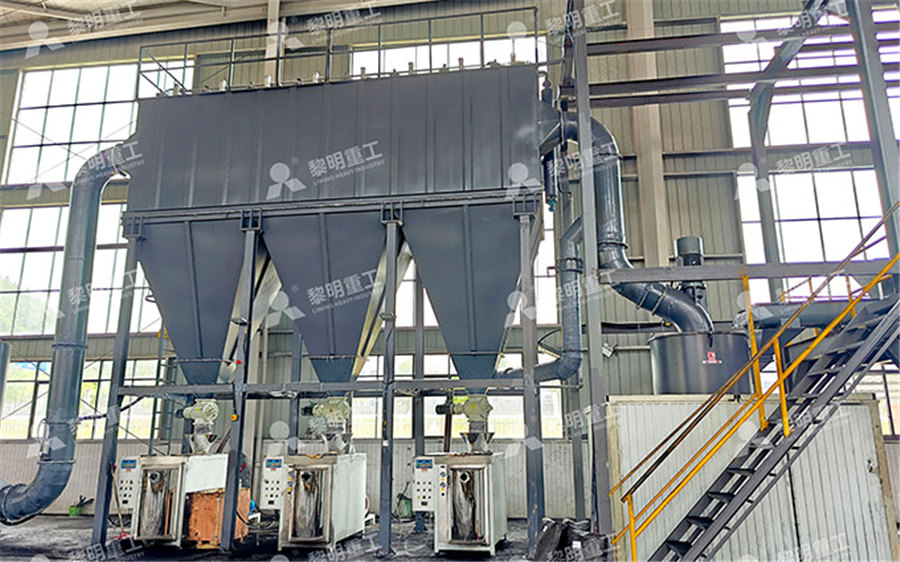
The Impact Of Classification On The Energy Efficiency Of Grinding
The alternative circuit uses highfrequency screens instead of cyclones with the same size semiautogenous grinding (SAG) and the ball mill The capacity of the grinding circuit being evaluated is 1875 t/h and the circuit is required to deliver a final product with a P80 of 75 μm