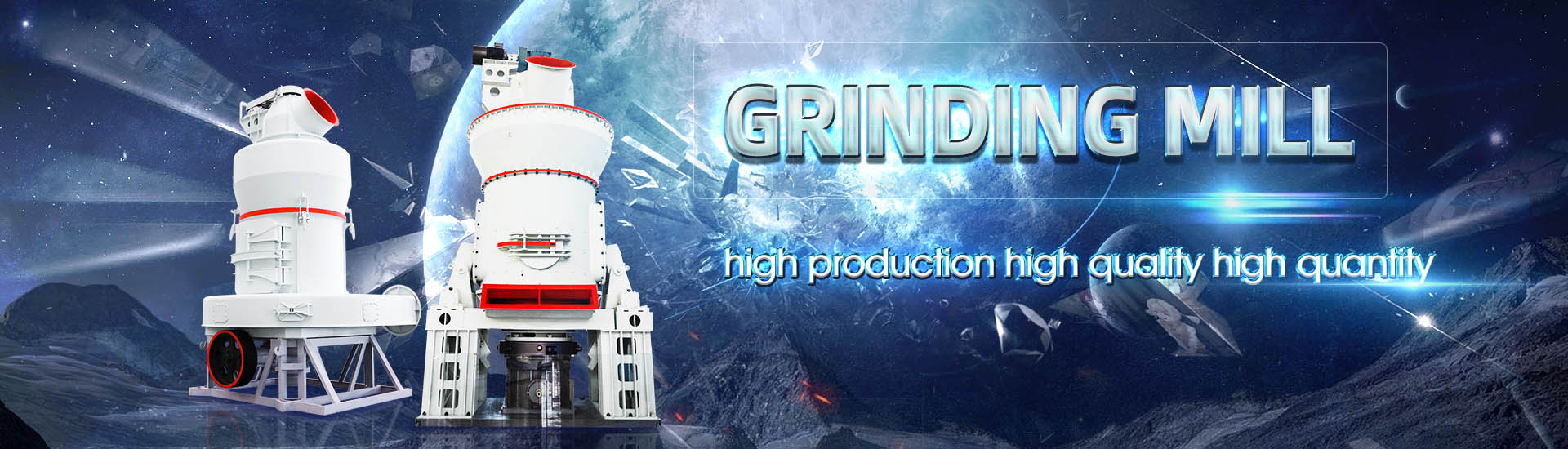
How to improve 3 2m x 13m cement mill production
.jpg)
Cement Mill Optimization: Practical Strategies for Enhanced
Optimizing the operation of cement mills is essential to maximize productivity, reduce energy consumption, and improve the quality of the final cement product In this article, we will delve 2023年2月21日 To improve cement mill production, consider increasing the mill's capacity, optimizing operating parameters, improving the grinding process, enhancing separatorHow can we improve cement mill production? LinkedIn1987年8月1日 Optimizing control for ball mills enabled us to increase the mill throughput by 35% and to reduce the specific power consumption by 35% But after we integrated these Optimization of Cement Manufacturing Process ScienceDirect2 BALL MILLS INTERNATIONAL CEMENT REVIEW FEBRUARY 2021 aim of delivering a target mill discharge size at the end of the chamber, with a maximum residue of five per cent >2mm BALL MILLS Ball mill optimisation Holzinger Consulting
.jpg)
How to Improve Cement Ball Mill Performance
There are two methods for clinker pretreatment: precrushing and pregrinding 1) The precrushing uses a crusher to crush the clinker before grinding, which can reduce the diameter of 2019年7月30日 Here are six categories of cement production that have potential for optimization Raw Materials The first step in the cement process is the recovery of the 6 Points in the Production Process to Optimize Cement MakingThe document discusses a case study of diagnostic studies conducted to optimize cement mill performance at a cement plant in India Key findings from the study include uneven grinding Diagnostic Study For Cement Mill Optimization PDF ScribdAdditives are highly effective in reducing the overall energy consumption CO2 emission of cement production due to clinker substitution! o At higher dosage (> 02% by weight), early Improvements in New Existing Cement Grinding Mills by Tim
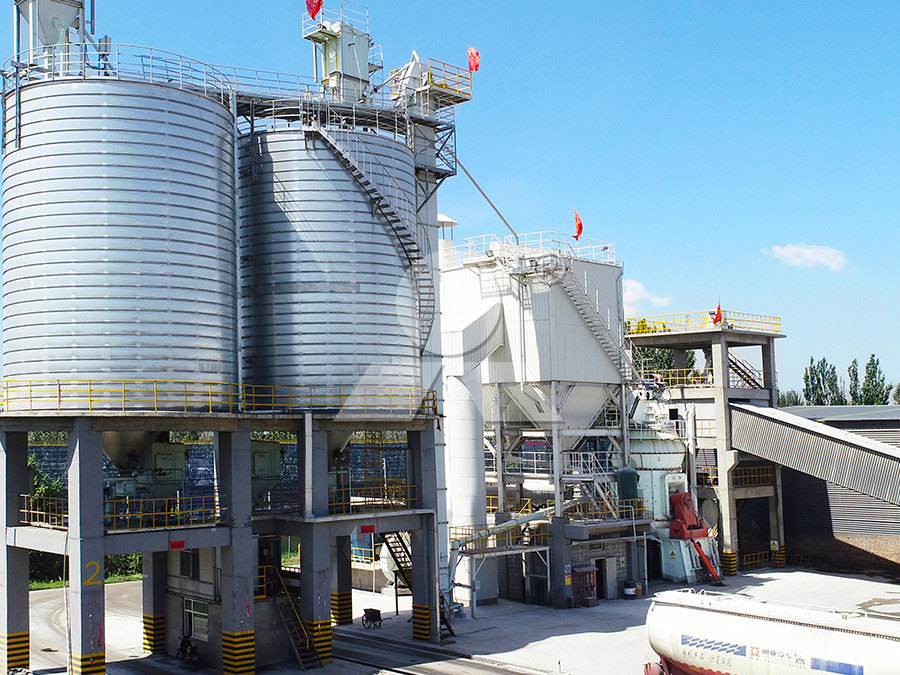
IMPROVING PRODUCTIVITY BASED ON THE MOVEMENT OF
The aim of this research is to increase the production per hour of the cement mill Z1 by increasing the total surface area of the grinding balls with increasing the number of balls whichCement and clinker production and how to improve them to optimize manufacturing costsCement Production: Focus on what really counts Endress+Hauser2023年12月28日 The ball mill for cement is a crucial equipment in the cement production process, designed to grind hard clinker into fine powder, playing a pivotal role in shaping the quality of cement products Its main structure How To Improve Working Efficiency Of Ball Mill For 1 The document discusses optimizing cement grinding circuits It presents tools like the Bond method and population balance models that can be used to analyze and optimize cement grinding 2 It provides details on the typical cement Cement Grinding Optimization PDF Mill (Grinding)
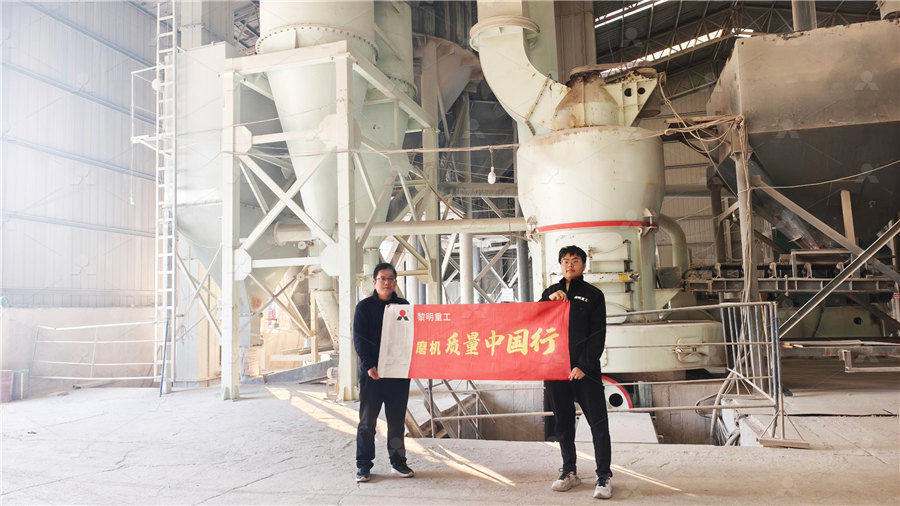
C E M E N T CEMENT MILL TEST REPORTS: What producers
3; (4) calcium oxide, CaO; (5) magnesium oxide, MgO; (6) sulfur trioxide, SO 3; (7) sodium oxide, Na 2 O; and (8) potassium oxide, K 2 0 Cements with a higher Fe 2 O 3 c o n tent tend to be darker as a rule For example, a cement with an Fe 2 O 3 c o n tent of 38% is often darker than a cement with an Fe 2 O 3 content of 30% C E M E N 2012年8月4日 required for the production of cement from aro und 5 700kJ/kg in the old wet processes to 3 100 kJ/kg3 600 kJ/kg in modern plants [Zur Strassen, 1957; Johansen Kouznetsova, 1992; Popescu et al An Overview of Cement production: How “green” and sustainable How to improve production of cement mill Crusher Unit, > How to improve production of cement mill How to improve production of cement mill Go to Product Center increase ball mill production rate Crusher South Africa, Cement mill Wikipedia, the free encyclopedia Ball mill to increase production and quality – ourcompany Heavy how to improve cement mill production2015年12月1日 The reason for the very limited additional potential savings of thermal energy is the necessary heat for the clinker production process Fig 1 shows the heat flows, the thermal input, the use for clinkering and drying, and the remaining waste heat flows that might be utilised However, the remaining waste heat is already used to a high degree, indicated by the already Process technology for efficient and sustainable cement production
G[R.jpg)
To study how to improve the productivity of yarn and fabric production
100 Factors affecting productivity in a spinning mill 27 101 Raw material 27 102 labour 27 103 Machinery 28 104 Maintenance 29 105 Energy issue 30 110 Interview of company 1 30 120 Production Analysis 33 121 Cost Analysis 36 130 Fabric production 36 131 Warping process 36 132 Sizing 37 133 Drawing in 年6月24日 Limestone may be the main ingredient of cement production, but minor constituents can play a major role Keeping material variability down and setting the right targets improves the performance of Replacement of the mill liners and returning the separator to original specifications restored the +200µm feed fraction to below Better and cheaper cement: Optimising raw material propertiesThe document summarizes key aspects of ball mill fundamentals: 1) Ball mills reduce materials through comminution mechanisms like fracture, chipping, and abrasion caused by ball movement inside the rotating mill 2) Ball movement patterns like cascading and cataracting depend on factors like mill speed and design 3) Size reduction efficiency is influenced by mill parameters, Cement Mill Ball Mill Dynamics PDF Mill (Grinding) Heat 32*13m Slag Mill, Find Details and Price about cement machinery cement production line from 32*13m Slag Mill Jiangsu Pengfei Group Co, Ltd Print This Page Home Manufacturing Processing Machinery Mining Machinery Mining Mill32*13m Slag Mill China cement machinery and cement production
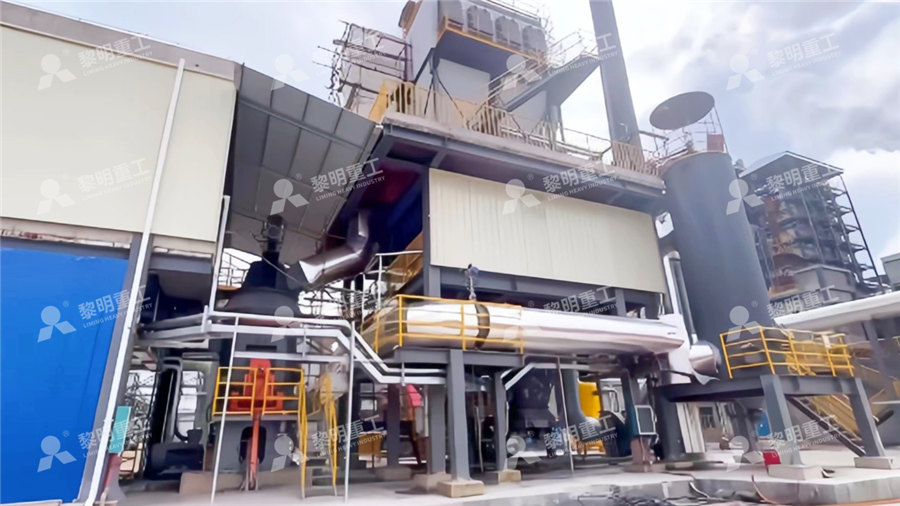
VRPM Vertical PreGrinding Mill Circuit flow diagram
2020年8月15日 VRPM Vertical PreGrinding Mill Circuit flow diagram Cement production increased by 30 to 40%VRPM gives better performance (Grinding capability) Without t10 Grinding Mill Investigation 25 11 Tromp Curve Calculation and Significance 27 12 Electrical Engineering 30 13 Fan Engineering 31 in the cement 3 Alumina Modulus/Alumina iron ratio (AM) AM = Al 2O 3 Fe 20 3 Typical Range : 10 – 15 Clinker with higher Alumina modulus results in cement with high early strength 4CEMENT FORMULAE HANDBOOK Green Business CentreThe proven classical option for cement grinding Whether employed as a twocompartment separator mill in an independent grinding system, or in combination with a high pressure grinding roll, the Ball Mill is a robust and reliable alternative for cement and granulated blast furnace slag grinding Used in combination with the sepol® highefficiency separator, ball mills can reliably Ball Mill thyssenkrupp PolysiusThis document provides an overview of cement production including: The types of cement and their raw material compositions The schematic diagram of the cement production process and descriptions of the bins and mill components Factors that affect cement quality such as Blaine value and moisture content Comparisons between cement mill and raw mill grinding as well Cement Mill Report
.jpg)
Dia 3*13m Ball Mill in Different Production Line China Cement
Dia 3*13m Ball Mill in Different Production Line, Find Details and Price about Cement Machinery Cement Mill from Dia 3*13m Ball Mill in Different Production Line Jiangsu Pengfei Group Co, Ltd Automatic Production Line: Comprehensive: Certification: CE, ISO: Flexible Production: Intelligent Manufacturing: Rhythm: Flow Production Line:2024年4月18日 Brief introduction to parameters of φ35m×13m ball mill: It is a highfine grinding mill with specifications of φ35×13m It has three warehouses, a total loading capacity of 160t, edge drive ⌀35m×13m cement ball mill 32x13m cement clinker mill2020年12月1日 With the increase of cement mill specifications and the requirement of energy saving, high yield, and high quality of cement grinding plant, the closedcircuit grinding is an inevitable trend of cement grinding unitThe essential equipment of a closedcircuit grinding system is a cement classifier, also known as a cement separatorThe function of the cement How To Measure Your Cement Mill And Cement Classifier? AGICO CEMENTJiangsu yangzi cement co, LTD 42 13m cement mill with the original osepa separator, Taiwan output of about 150t/h, eventually make the phi 42 x 13 m cement grinding machine production stable at 190 t/h (PO 425), finished product specific surface area more than 360 ~ 380 m2 / 42 13m large cement mill has been successfully fitted Jiangsu

Φ 32 * 13m Ball Mill for Cement Grinding and Mine Grinding Mill
Φ 32× 13m high fineness cement mill A): Main technical parameter performances 1, specification: Φ 32× 13m 2, production capacity: 5560t/h (Open circuit current general Portland cement, specific surface area≥ 320m2/kg, feeding size≤ 10mm, feeding moisture≤ 05%, feeding temperature≤ 50° C, air speed in mill1112m/s)2021年1月29日 Cement production is one of the most energyintensive manufacturing industries, and the milling circuit of cement plants consumes around 4% of a year's global electrical energy productionIncrease productivity of vertical roller mill using seven Abstract An improved differential evolutionary cement mill operation index decision algorithm based on constraint control and selection strategy is proposed to address the problem that the operation index is usually decided by manual experience in the cement mill operation process, which causes unqualified cement specific surface area and excessive cement mill power The Decision Algorithm of Cement Mill Operation Index BasedImprove the thermal load of the rotary kiln: It has been found through research and practice that increasing the coal consumption of the rotary kiln head can potentially exploit the production capacity of the rotary kiln, thereby increasing How to Improve Output Of Cement Rotary Kiln
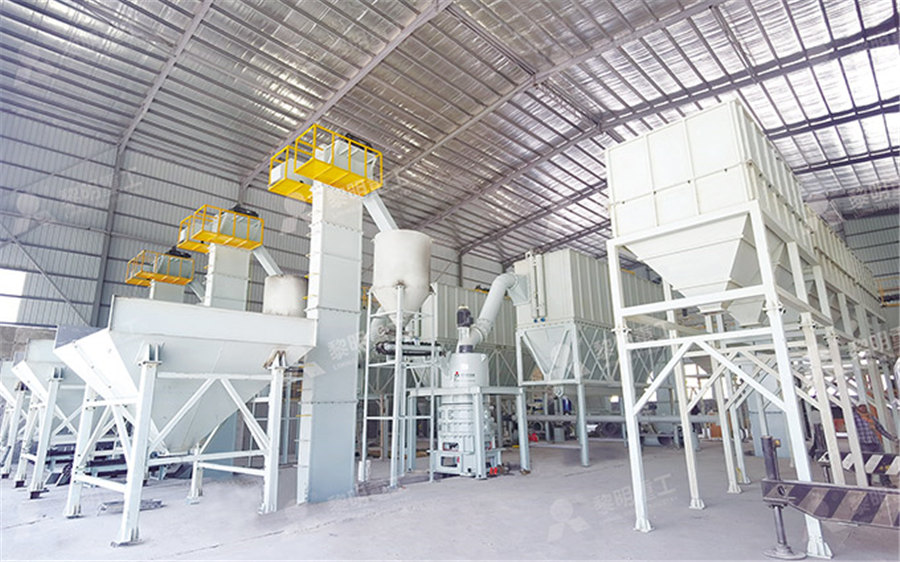
Heat Integration in a Cement Production ResearchGate
2018年10月10日 Heat transfer in cement production with raw mill considering the minimum temperature difference 1Hot composite curve; 2cold composite curve, 3heat exchangers (developed after [30])sea defenses and wind farms However, cement production is also responsible for up to 8% of global CO 2 emissions1 providing a significant opportunity to improve environmental output Decarbonizing cement manufacture is an increasingly pressing environmental goal that also presents an opportunity to improve production economics LowerCostefficient strategies for sustainable cement productionPFG180140 roller press and ϕ42*13m cement mill are used in Anhui Wanwei Group Co, Ltd which will greatly reduce the production cost and improve the competitiveness of wanwei cement market Anhui wanwei high tech materials Co, Ltd is the core enterprise of Wanwei Group Co, Ltd (hereinafter referred to as wanwei group)Cement Production Line, Cement machinery, Rotary kiln, Cement Tube mill 2021年11月18日 That is smaller than a grain of beach sand! This process consumes approximately 40 kWh per ton of cement, accounting for the most electrical power consumption in the production of cement Cemex is using “ModelBased Optimization”, which consists of using machine learning to generate models that predict the performance of the millImproving cement production through Artificial Intelligence

Ventilation Prediction for an Industrial Cement Raw Ball Mill by
2021年6月10日 1 Introduction In the cement industry, grinding is one of the most consuming energy stages in the production units Around 65% of the total used electrical energy in a cement plant has to be utilized to grind raw materials, coal, and clinker [1,2]Through the process, many variables can affect the efficiency and productivity of this dry grinding procedure, such as the CCR Guide Free download as Powerpoint Presentation (ppt / pptx), PDF File (pdf), Text File (txt) or view presentation slides online The document discusses cement mill process control and operation It first introduces cement production and outlines the key functions of vertical roller mills (VRMs) used in cement grinding grinding, drying, separation, and transportDepartment:Production: Cement Mill Process Control and 2015年8月1日 The results show that approximately 248t, 469t, and 341t of materials are required to produce a ton of the product in raw material preparation, clinker production, and cement grinding stages (PDF) Analysis of material flow and consumption in cement production 2023年12月28日 The ball mill for cement is a crucial equipment in the cement production process, designed to grind hard clinker into fine powder, playing a pivotal role in shaping the quality of cement products Its main structure How To Improve Working Efficiency Of Ball Mill For
.jpg)
Cement Grinding Optimization PDF Mill (Grinding)
1 The document discusses optimizing cement grinding circuits It presents tools like the Bond method and population balance models that can be used to analyze and optimize cement grinding 2 It provides details on the typical cement 3; (4) calcium oxide, CaO; (5) magnesium oxide, MgO; (6) sulfur trioxide, SO 3; (7) sodium oxide, Na 2 O; and (8) potassium oxide, K 2 0 Cements with a higher Fe 2 O 3 c o n tent tend to be darker as a rule For example, a cement with an Fe 2 O 3 c o n tent of 38% is often darker than a cement with an Fe 2 O 3 content of 30% C E M E N C E M E N T CEMENT MILL TEST REPORTS: What producers 2012年8月4日 required for the production of cement from aro und 5 700kJ/kg in the old wet processes to 3 100 kJ/kg3 600 kJ/kg in modern plants [Zur Strassen, 1957; Johansen Kouznetsova, 1992; Popescu et al An Overview of Cement production: How “green” and sustainable How to improve production of cement mill Crusher Unit, > How to improve production of cement mill How to improve production of cement mill Go to Product Center increase ball mill production rate Crusher South Africa, Cement mill Wikipedia, the free encyclopedia Ball mill to increase production and quality – ourcompany Heavy how to improve cement mill production
.jpg)
Process technology for efficient and sustainable cement production
2015年12月1日 The reason for the very limited additional potential savings of thermal energy is the necessary heat for the clinker production process Fig 1 shows the heat flows, the thermal input, the use for clinkering and drying, and the remaining waste heat flows that might be utilised However, the remaining waste heat is already used to a high degree, indicated by the already 100 Factors affecting productivity in a spinning mill 27 101 Raw material 27 102 labour 27 103 Machinery 28 104 Maintenance 29 105 Energy issue 30 110 Interview of company 1 30 120 Production Analysis 33 121 Cost Analysis 36 130 Fabric production 36 131 Warping process 36 132 Sizing 37 133 Drawing in 38To study how to improve the productivity of yarn and fabric production 2021年6月24日 Limestone may be the main ingredient of cement production, but minor constituents can play a major role Keeping material variability down and setting the right targets improves the performance of Replacement of the mill liners and returning the separator to original specifications restored the +200µm feed fraction to below Better and cheaper cement: Optimising raw material propertiesThe document summarizes key aspects of ball mill fundamentals: 1) Ball mills reduce materials through comminution mechanisms like fracture, chipping, and abrasion caused by ball movement inside the rotating mill 2) Ball movement patterns like cascading and cataracting depend on factors like mill speed and design 3) Size reduction efficiency is influenced by mill parameters, Cement Mill Ball Mill Dynamics PDF Mill (Grinding) Heat