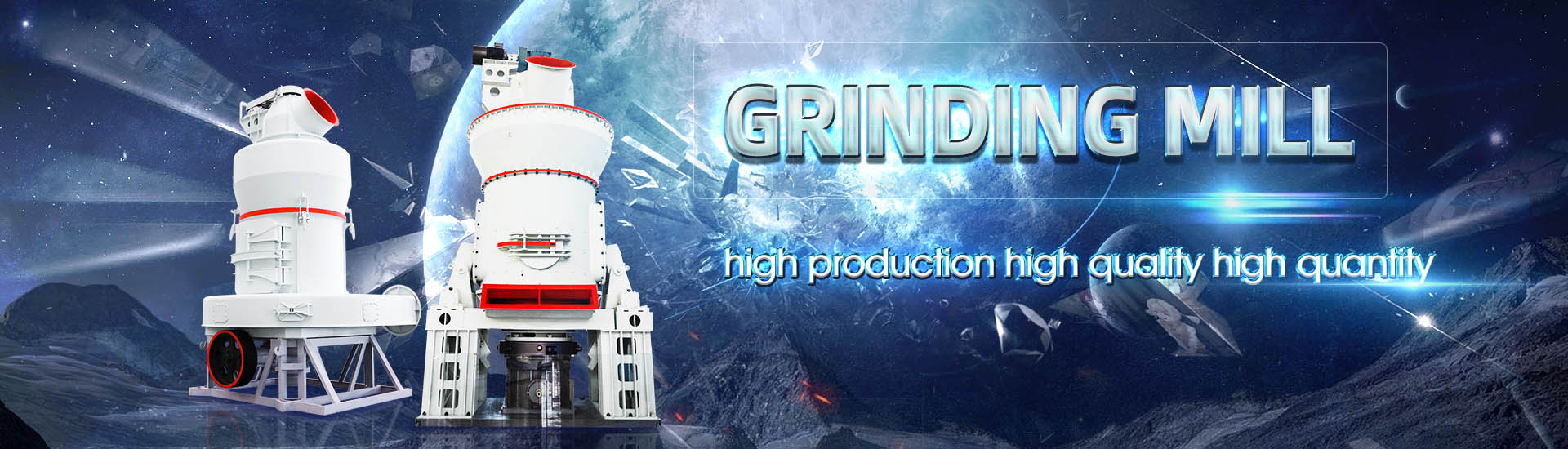
Cement plant raw material grinding process flow chart
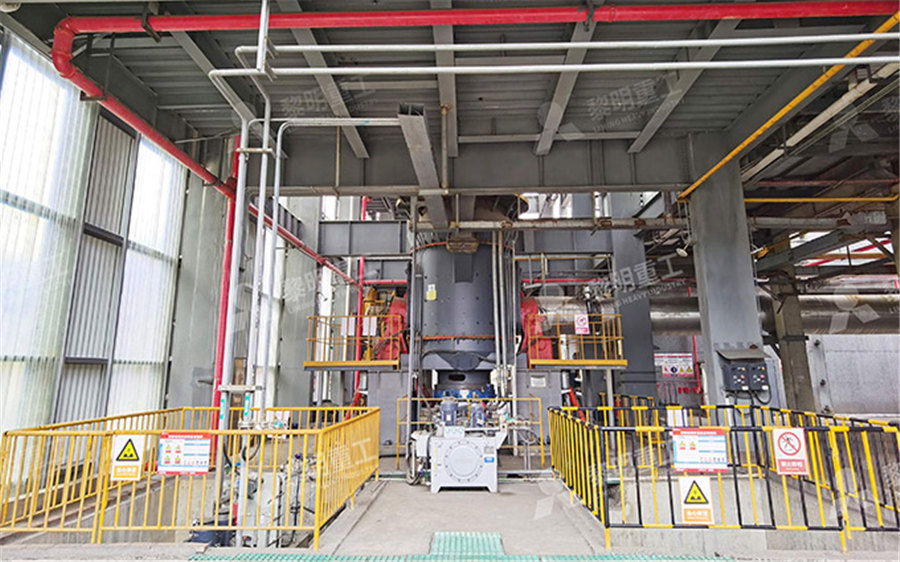
Cement Manufacturing PDF Cement Mill (Grinding)
The document summarizes the cement manufacturing process used by Mangalam Cement Limited It begins with raw material handling such as The whole process of cement manufacturing in Messebo Cement plant which consists of two separate Cement Production lines can be summarized into the following processes ;as can be CEMENT PRODUCTION AND QUALITY CONTROL A Cement Process flow diagram for the cement manufacturing process, showing electricity and heat consumption or inputs [39] The paper presented herein investigates the effects of usingProcess flow diagram for the cement manufacturing The cement manufacturing process involves 3 main steps: 1) Extraction of raw materials like limestone, chalk, and clay from quarries These materials are crushed and stored 2) The raw Cement Manufacturing Process: Step 1: Extraction of Raw
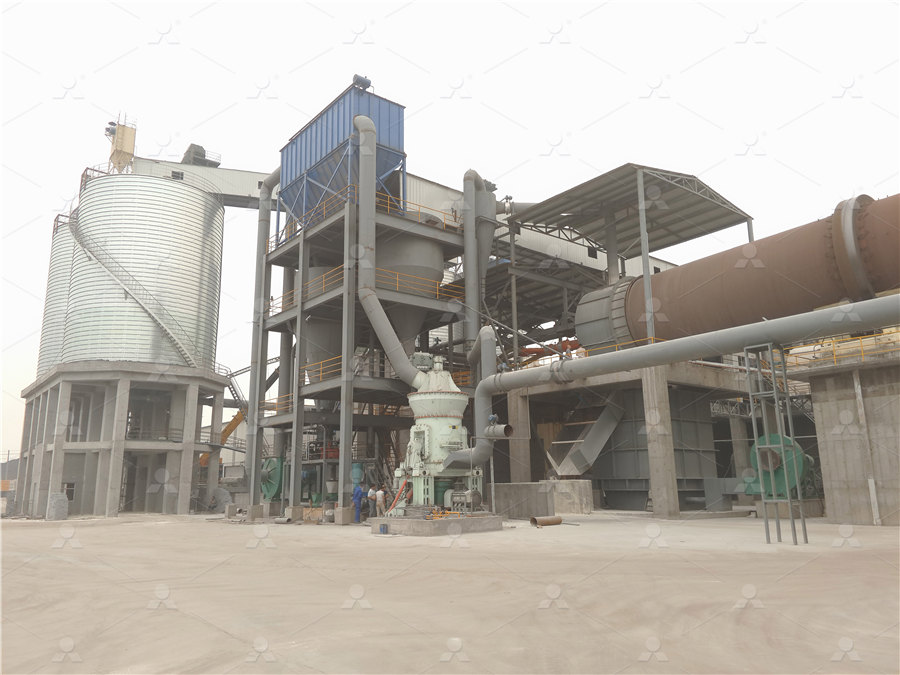
Cement Manufacturing Process Flowsheet (Flow Chart)
Download scientific diagram Cement Manufacturing Process Flowsheet (Flow Chart) from publication: Cement Manufacturing – Process Modeling and TechnoEconomic Assessment (TEA) using2012年8月30日 Cement Manufacturing Process Phase II: Proportioning, Blending Grinding The raw materials from quarry are now routed in plant laboratory where, they are analyzed and proper proportioning of limestone Cement Manufacturing Process Engineering Intro2021年11月27日 This document presents information on the cement manufacturing process and process optimization in the cement industry It discusses the key stages in cement production, including crushing, raw Cement manufacturing process PPT SlideShareraw materials, burning, grinding and quality control are supported by a range of chapters addressing critial topics such as maintenance and plant reporting, alongside a detailed The Cement Plant Operations Handbook International Cement
.jpg)
Cement Plant: The Manufacturing Process 4 5 World Cement
together in a raw mill to a particle size of 90 micrometres, producing “kiln feed” Cement Plant: The Manufacturing Process worldcementassociation 1 Limestone (CaCO3) is taken from a Maintenance – 17 Process – 18 Materials analysis –19 Plant capacity summary – 20 Storage capacity 15 Cement plant construction and valuation 244 1 New plant construction – 2 Project management – 3 Cement plant investment costs – 4 Project phases – 5 Plant valuation Section B – Process calculations and miscellaneous The Cement Plant Operations Handbook International Cement 1971年8月17日 116 Portland Cement Manufacturing 1161 Process Description17 Portland cement is a fine powder, gray or white in color, that consists of a mixture of hydraulic cement materials comprising primarily calcium silicates, aluminates and aluminoferrites More than 30 raw materials are known to be used in the manufacture of portland cement, and these116 Portland Cement Manufacturing US EPAA dryinggrinding process often encountered in America, is raw material drying in the mechanical air separator The flow chart of this arrangement is shown in Fig 410 Such a plant dries raw material with a moisture content of 68 % Higher Drying of raw materials INFINITY FOR CEMENT
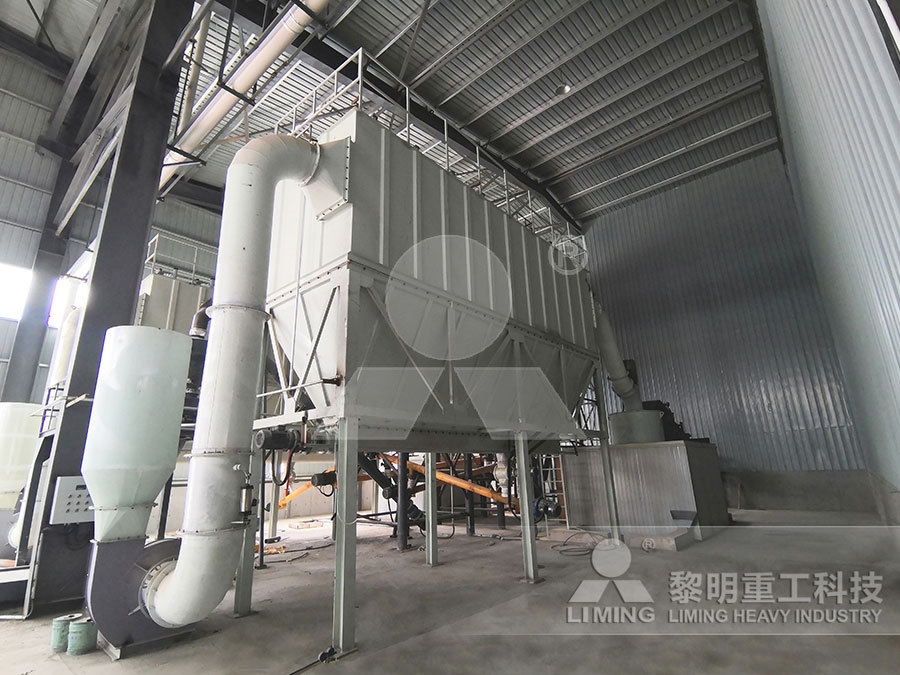
Flow chart of raw meal production Download Scientific Diagram
Download scientific diagram Flow chart of raw meal production from publication: Modeling of Raw Materials Blending in Raw Meal Grinding Systems The objective of the present study is to build a The document describes the cement manufacturing process used by Lafarge, a French industrial company The process involves 5 main steps: 1) mining of raw materials like limestone and clay, 2) crushing and storing the materials, 3) drying, grinding and mixing the materials into raw meal, 4) firing the raw meal in a kiln to produce cement clinker, and 5) grinding the clinker together Cement Manufacturing Process PDF Mill (Grinding) ScribdDownload scientific diagram Flow chart of the grinding and blending process from publication: Effective Optimization of the Control System for the Cement Raw Meal Mixing Process: I PID Tuning Flow chart of the grinding and blending process;as can be seen in the process and Quality flow diagram below; 1 Quarrying and Crushing 2 Raw material Storage and Transportation 3 Proportioning 4 Raw material Grinding and Transportation 5 Raw meal storage, homogenization and Kiln feeding 6 Pyroprocessing (Raw meal preheating, calcination Clinkerization, clinker cooling,CEMENT PRODUCTION AND QUALITY CONTROL A Cement manufacturing Process
.jpg)
Analysis of material flow and consumption in cement production process
2016年1月20日 In the surveyed cement plant, three balances are established between input and output material in the raw mill, clinker production, and cement grinding system 248 t, 469 t, and 341 t of materials are required to produce a ton of the product in raw material preparation, clinker production, and cement grinding stages; waste gases account for the largest proportion of the What Is Cement Vertical Mill The cement vertical mill is a type of grinding equipment that merges fine crushing, drying, grinding, and powder separating into a single, which simplifies the production process and has many irreplaceable advantages, such as high grinding efficiency, large feeding size, low power consumption (2030% less power than a cement ball mill), large Cement Vertical Mill Vertical Grinding Mill Vertical Mill AGICOcement manufacturing PPT Free download as Powerpoint Presentation (ppt / pptx), PDF File (pdf), Text File (txt) or view presentation slides online The document summarizes the cement manufacturing process used by Mangalam Cement Limited It begins with raw material handling such as limestone mining and crushing The materials then undergo quality checks, blending, Cement Manufacturing PDF Cement Mill (Grinding)Manufacturing process flow 1 Quarrying and Crushing The quarry (where the mining activity is performed) is located 07 km away from the plant and has the main raw materials such as Limestone and shale that is estimated to last for 100 years, then carried to the clinker feed bin in cement grinding plant b means of belt conveyor 9 Cement Manufacturing process flow 1 Quarrying and Crushing Messebo Cement

Stages in cement production flow chart [43] ResearchGate
Download scientific diagram Stages in cement production flow chart [43] from publication: A review on kiln system modeling The purpose of this study is to evaluate performance cement of Raw material blending is an important process affecting cement quality The aim of this process is to mix a variety of materials such as limestone, shale (clay), sandstone and iron to produce The cement raw material blending process and its control systemThis flow sheet and sampling map shows the process flow for a cement plant Key components include: 1) Raw materials like iron sand, silica sand, limestone, clay and gypsum being fed into crushers and mills 2) Processed materials being fed into kiln systems for heating and clinkering 3) Clinker being stored and transported to other cement plants or customers 4) A coal mill and Flow Sheet Kiln, Raw Mill N Coal Mill PDF Cement ConcreteCement production process , each producing one ton of Portland cement grinding at least 3 tons of materials ( including raw materials , fuel, clinker , mixed materials , gypsum ) , according to statistics , the dry process cement production line grinding operations need to consume power accounts for over 60% of the whole power plant , where raw material grinding accounted for Flow Chart Of Cement Industry { Dry Process } Blogger
.jpg)
Analysis of Material Flow and Consumption in Cement Production Process
This document summarizes a research article that analyzed material flows and consumption in the cement production process The researchers established material flow routes for cement manufacturing and built mass balances for the three main production stages using plant data They calculated the material efficiency and waste recycling rates for each stage and 2014年6月10日 Evolution of the cement Process • Wet process easiest to control chemistry better for moist raw materials • Wet process high fuel requirements fuel needed to evaporate 30+% slurry water • Dry process kilns less fuel requirements • Preheater/Precalciner further enhance fuel efficiency allow for high production ratesCement manufacturing process PPT SlideShareDownload scientific diagram The flowchart of cement grinding, A, Bsampling points (evacuation stacks) [37] from publication: Dust Emission Monitoring in Cement Plant Mills: A Case Study in The flowchart of cement grinding, A, Bsampling points Fly Ash Processing Plant Flow Chart Concrete Cement After grinding, with an ideal content of 40% Using fly ash as raw material to make cement has been quite common in cement plants, and the technology is relatively mature The ideal content can Fly Ash Processing Plant Cement Equipment Manufacturing
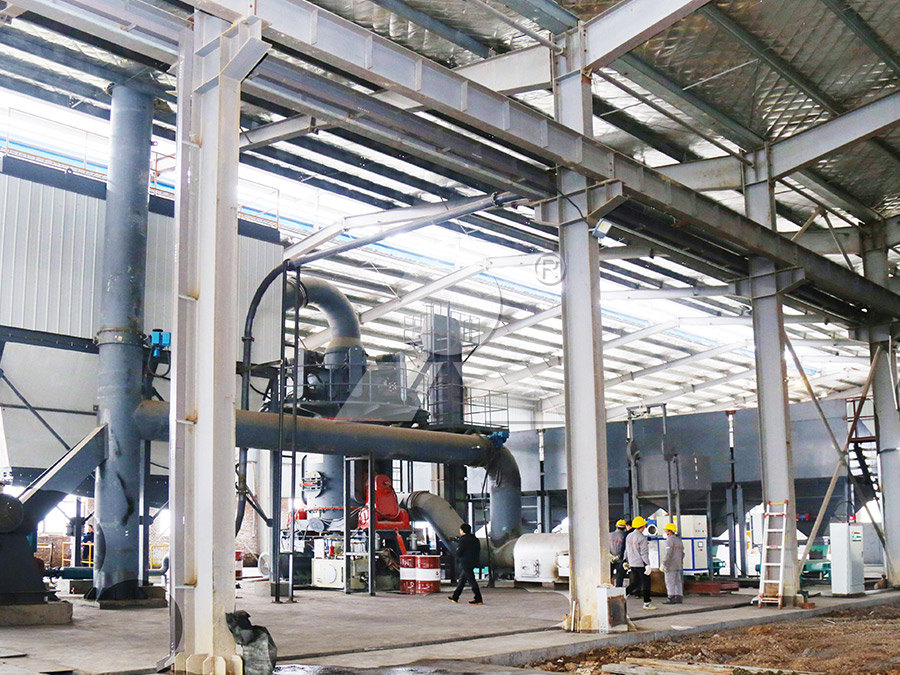
Cement Grinding Plant Overview Cement Grinding Unit AGICO Cement
2019年10月11日 AGICO Cement is a cement grinding plant manufacturer, we'd like to helps you learn more about cement grinding plant and cement grinding machines Skip to content +86 The cement manufacturing process consists of the following stages as explained in the following flow chart Quarrying Raw material The main raw material required for cement manufacturing is limestone extracted from 40km away Production Process INSEE Cement : Sri Lanka’s Bovine skin was incubated with plant enzymes bromelain (B) and zingibain (Z) at the level of 0, 5, 10, 15, 20 and 25 unit/g of skin and gelatin was extracted at 60 °C for 6 hFlow chart for different grinding processAGICO Cement is a cement equipment manufacturer supplies EPC projects for cement grinding station with a simple process, easy operation it will be sent to the stable flow weighing bin of the cement mill by the following seven Cement Grinding Unit Cement Grinding Plant

ShapedByConcrete – How Cement is Made
The material then moves through the preheater tower, starting at the top and moving to the bottom The preheater tower helps make the kiln process more efficient by adding heat generated from the plant to the raw materials, starting the chemical reaction Doing this makes the cement process more efficientFor drying the wet raw material it is necessary that prior to the mill start up the grinding plant isheated for some timeOtherwise the cold grinding plant would take away too much heat from the drying process and the finish product would not be dry – handling problems in the meal transport and silo extraction would followPROCESS TRAINING for operators of Vertical RAW MillsEVERYTHING YOU NEED TO KNOW ABOUT ESTABLISHING CEMENT GRINDING PLANT 1MTY the plant layout and flow process Plant Capacity The plant will have a capacity to produce 10 million tonnes of cement per annum (10 MTPA) Since the moisture content of the raw materials fed to the grinding mill must be controlled, EVERYTHING YOU NEED TO KNOW ABOUT ESTABLISHING CEMENT GRINDING PLANT 2024年9月5日 2 Raw material grinding After crushing, the raw materials are carried to a grinding mill and made into a fine powder This is done using equipment such as ball mills or vertical roller mills The grinding process ensures the correct particle size of raw material and its homogeneous constitution, which is so critical for product quality 3 A Comprehensive Guide to the Cement Manufacturing Process
.jpg)
Manufacturing of Portland Cement – Process and Materials
1 天前 The manufacture of Portland cement is a complex process and done in the following steps: grinding the raw materials, mixing them in certain proportions depending upon their purity and composition, and burning them to sintering in a kiln at a temperature of about 1350 to 1500 ⁰C During this process, these materials partially fuse to form nodular shaped clinker by 2021年3月9日 In this study the process flow diagram for the cement production was simulated using Aspen HYSYS 88 software to achieve high energy optimization and optimum cement flow rate by varying the flow rate of calcium oxide and silica in the clinker feed Central composite Design (CCD) of Response Surface Methodology was used to design the ten experiments for Simulation and Optimization of an Integrated Process Flow Sheet with the extraction of raw materials and ending with the finished product From raw materials to cement Extracting raw materials Crushing and transportation Raw material preparation I: Storage and homogenisation Raw material preparation II: Drying and raw grinding Burning The burning of the raw meal at approx 1,450°C is carried outFrom raw materials to cementMaintenance – 17 Process – 18 Materials analysis –19 Plant capacity summary – 20 Storage capacity 15 Cement plant construction and valuation 244 1 New plant construction – 2 Project management – 3 Cement plant investment costs – 4 Project phases – 5 Plant valuation Section B – Process calculations and miscellaneous The Cement Plant Operations Handbook International Cement
.jpg)
116 Portland Cement Manufacturing US EPA
1971年8月17日 116 Portland Cement Manufacturing 1161 Process Description17 Portland cement is a fine powder, gray or white in color, that consists of a mixture of hydraulic cement materials comprising primarily calcium silicates, aluminates and aluminoferrites More than 30 raw materials are known to be used in the manufacture of portland cement, and theseA dryinggrinding process often encountered in America, is raw material drying in the mechanical air separator The flow chart of this arrangement is shown in Fig 410 Such a plant dries raw material with a moisture content of 68 % Higher Drying of raw materials INFINITY FOR CEMENT Download scientific diagram Flow chart of raw meal production from publication: Modeling of Raw Materials Blending in Raw Meal Grinding Systems The objective of the present study is to build a Flow chart of raw meal production Download Scientific DiagramThe document describes the cement manufacturing process used by Lafarge, a French industrial company The process involves 5 main steps: 1) mining of raw materials like limestone and clay, 2) crushing and storing the materials, 3) drying, grinding and mixing the materials into raw meal, 4) firing the raw meal in a kiln to produce cement clinker, and 5) grinding the clinker together Cement Manufacturing Process PDF Mill (Grinding) Scribd
.jpg)
Flow chart of the grinding and blending process
Download scientific diagram Flow chart of the grinding and blending process from publication: Effective Optimization of the Control System for the Cement Raw Meal Mixing Process: I PID Tuning ;as can be seen in the process and Quality flow diagram below; 1 Quarrying and Crushing 2 Raw material Storage and Transportation 3 Proportioning 4 Raw material Grinding and Transportation 5 Raw meal storage, homogenization and Kiln feeding 6 Pyroprocessing (Raw meal preheating, calcination Clinkerization, clinker cooling,CEMENT PRODUCTION AND QUALITY CONTROL A Cement manufacturing Process2016年1月20日 In the surveyed cement plant, three balances are established between input and output material in the raw mill, clinker production, and cement grinding system 248 t, 469 t, and 341 t of materials are required to produce a ton of the product in raw material preparation, clinker production, and cement grinding stages; waste gases account for the largest proportion of the Analysis of material flow and consumption in cement production process What Is Cement Vertical Mill The cement vertical mill is a type of grinding equipment that merges fine crushing, drying, grinding, and powder separating into a single, which simplifies the production process and has many irreplaceable advantages, such as high grinding efficiency, large feeding size, low power consumption (2030% less power than a cement ball mill), large Cement Vertical Mill Vertical Grinding Mill Vertical Mill AGICO
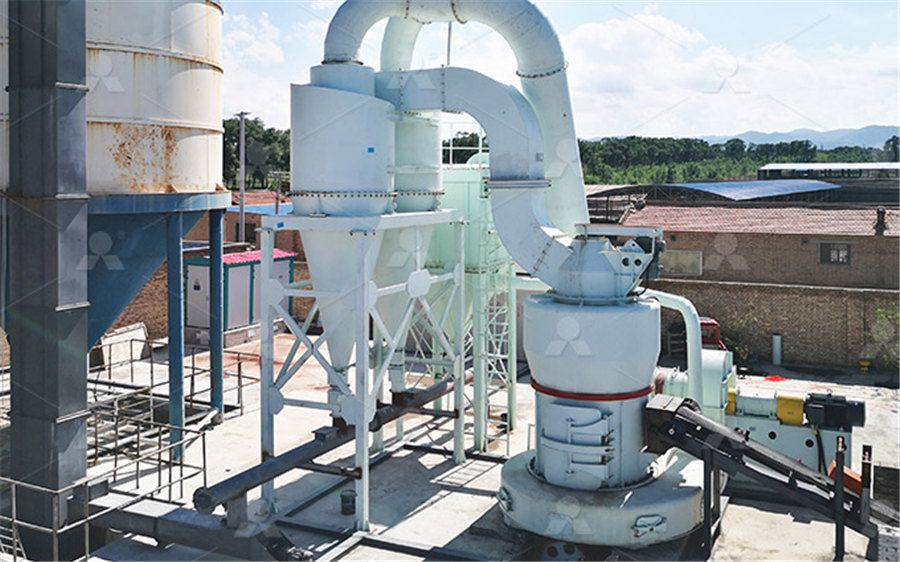
Cement Manufacturing PDF Cement Mill (Grinding)
cement manufacturing PPT Free download as Powerpoint Presentation (ppt / pptx), PDF File (pdf), Text File (txt) or view presentation slides online The document summarizes the cement manufacturing process used by Mangalam Cement Limited It begins with raw material handling such as limestone mining and crushing The materials then undergo quality checks, blending,