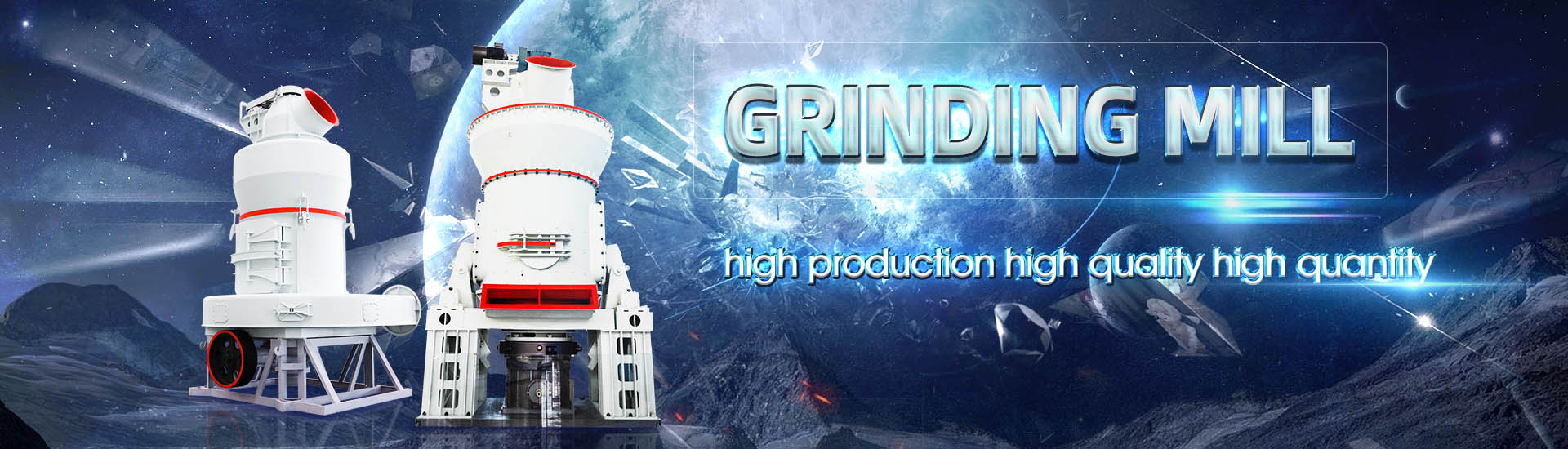
Iron oxide green powder grinding equipment process
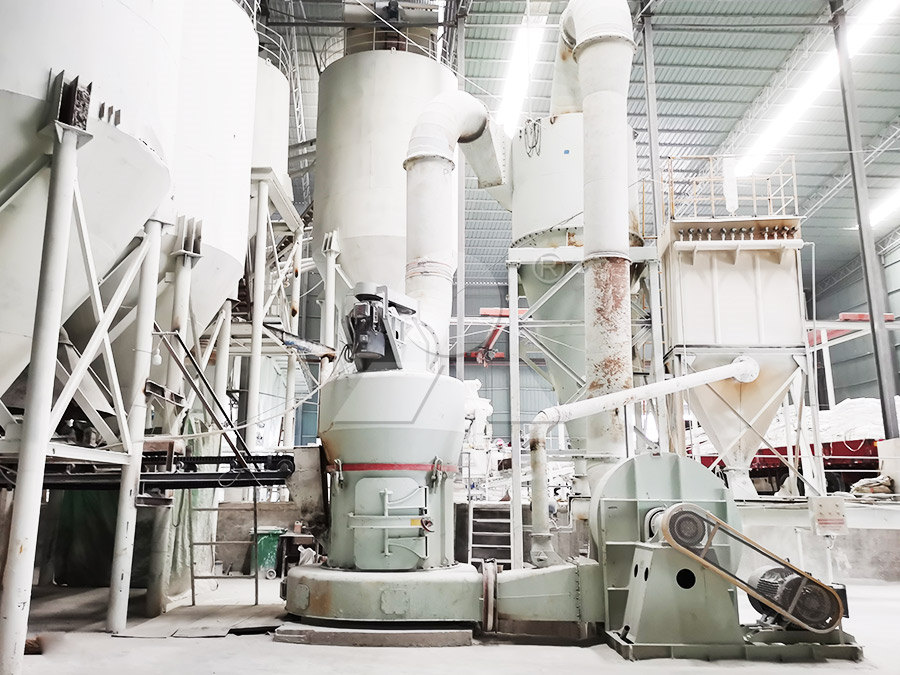
Iron Oxide Grinding Production Line With HGM80 Ultrafine Mill
2024年11月28日 Process Flow: 1 Raw Material Preparation Input Material: Iron oxide Initial Size: ≤20 mm Moisture Content: ≤6% (predrying required if higher) 2 Grinding Process Core Equipment: HGM80 Ultrafine Grinding Mill Output Size: 1250 mesh (D97 ≤ 10µm) Capacity: Chemical Milling, Custom Processing, Custom Pulverizing, Micronizing, and Grinding from Iron Oxide Micronization : Jet Pulverizer2024年11月6日 In this iron oxide grinding project, the mill meets the customer’s micropowder Clirik Roller Mill Into The Iron Oxide Grinding Line2020年10月18日 In pelletizing plants, different features of iron ore concentrate such as The effects of iron ore concentrate grinding methods (HPGR and
.jpg)
New Processing Route for Production of Fine Spherical Iron Powder
In this paper the powder properties and sintering results of a fine spherical iron powder which is 2011年1月1日 Grinding mills typically used in the process include the attrition jet, planetary, Preparation of iron oxide nanoparticles by mechanical milling2022年3月19日 An iron ore concentrate sample was ground separately in a pilotscale HPGR Grinding iron ore concentrate by using HPGR and ball mills and In this study, the reaction process of the ICCB occurred in the contact between the solid green Study on strength and reduction characteristics of iron ore powder
.jpg)
Development of a Novel Grinding Process to Iron Ore Pelletizing
Modern iron ore pelletizing process operations may be divided into two main process sections: Choose from 11 Iron Oxide Powder types for pigments, polishing, magnetic media process efficiency, and emissions reduction Unique glass materials for melting, processing, shaping, and fabrication for glass applications Green Technology Handpicked materials for the development and implementation of green technologies Lithium Ion Iron Oxide Powder Goodfellow221 Pretreatment process of Iron Ore Fines In the pretreatment process, iron ore fines are ground into finer size, suitable for green ball formation Dry or wet grinding process is adopted for grinding the iron ore fines In dry grinding process, equipment ie drier, ball mill,SAFETY GUIDELINES FOR IRON STEEL SECTOR MINISTRY OF 2023年2月9日 develop a new understanding of iron ore dissolution kinetics and a novel electrochemical regeneration scheme that enhances iron ore dissolution and increases the efficiency of iron extraction Instead of heating and smelting the iron ore, Electra’s process dissolves the ore in a waterbased acid solution Next, electricity is used to Producing green iron with a zeroCarbon electrochemical Process S
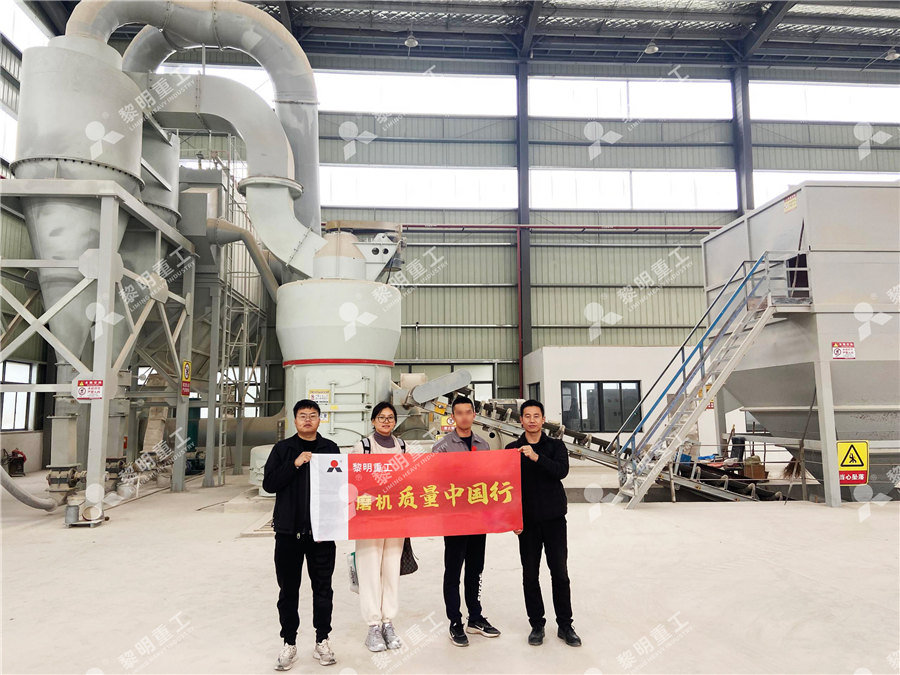
Iron Oxide Pigments 911Metallurgist
2021年1月4日 Until the late 19th century iron oxide pigments were obtained wholly from natural materials, generally with little alteration other than physical purification In some cases roasting or calcination was also carried out However, beginning in the first part of the 20th century, chemical methods were developed for synthetic production of commercial iron oxides2019年8月23日 Stage grinding, stage selection, coarsefine separation, gravitymagnetic separationreverse flotation process have been applied in China’s mixed iron ore dressing plant 3 Fine screening and grinding process Features The fine sieving and regrinding process is an effective method to improve the grade of iron concentrateIron Processing Equipment, Process Flow, Cases JXSC Machine2021年11月2日 Gold Alloy Gold is a relatively soft material Slowspeed handpieces Technique consists of the following steps: (1) Contour carbide burs, green stones (silicone carbide), or heatless stones (2) Finish pink stones (aluminum oxide), or mediumgrade abrasive impregnated rubber wheels and points (brown and green) (3) apply fine abrasive Materials and processes for cutting, grinding PPT SlideShare1 A hard brittle layer of pure metal which is subsequently milled to obtain powder (eg iron powder) 2 A soft, spongy substance which is loosely adherent and easily removed by scrubbing 3 A direct powder deposit from the electrolyte that collects at the bottom of the cell Factors promoting powder deposits are, high current density, low metalPowder metallurgy – basics applications IIT Guwahati
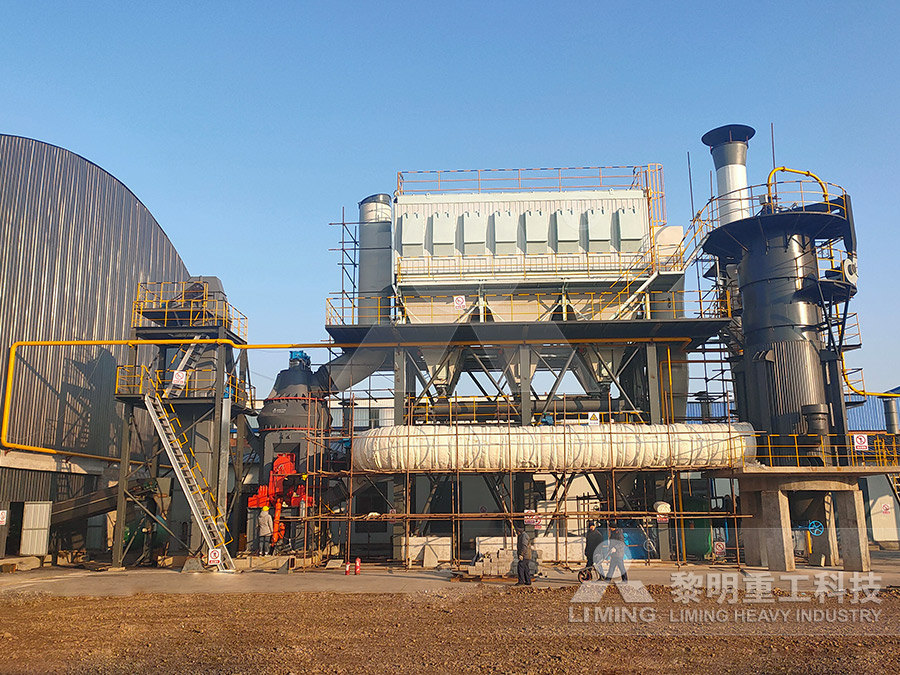
Fine Iron Oxide Powder as a Raw Material of Soft Ferrites†
Using Fine Iron Oxide Powder Fine iron oxide having a specific surface area of 129 104 m2/kg and 770 ppm of Cl, and conventional spray roasted iron oxide JCCPW (manufactured by JFE Chemical) prepared by the sprayroasting method, having a specific surface area of 49 103 m2/kg and 770 ppm of Cl were used as the raw materials for ferrites2021年12月1日 Request PDF Grinding behavior of VP50IM steel using green and black silicon carbide compared to aluminum oxide wheel under different feed rates Technological advances and the development of Grinding behavior of VP50IM steel using green and black silicon 2023年11月8日 This review focuses on green methods for synthesizing iron oxide nanoparticles using bacteria, fungi, yeasts, plant extract, and organic waste In addition, IONP’s prospective(PDF) Iron Oxide Nanoparticles: Green Synthesis andThere are several types of grinding media generally used in the Attritor They are, to name a few, carbon steel, chrome steel, stainless steel, tungsten carbide, ceramic, alumina, zirconium oxide, glass, (flintstones,) and specials such as silicone nitride and silicone carbide The carbon steel grinding media (Spgr 78) is most commonly usedATTRITOR GRINDING AND DISPERSING EQUIPMENT by A Union Process
.jpg)
Acid Regeneration Plant Tenova
Fluidized Bed Process Under high temperature and continuous operation the process regenerates HCl acid (18%wt) and permits to sinter oxide forming grey granules up to 2 mm in size The iron oxide granules are free of dust and contain almost no chlorides2023年11月15日 Poveromo, JJ, 2014 Future trends in Ironmaking, prepared for McMaster blast furnace ironmaking course, May 11 – 16, 2014(PDF) IRON ORE PELLETIZING PROCESS ResearchGateRainbow Ming's powder metallurgy gear manufacturing and sintering process in powder metallurgy The bronze powder, brass powder, etc) into a forming mold, and the powder is pressed into green parts under a set Workpieces are placed in a hightemperature environment to react with water vapor to form blueblack iron oxide on the Powder Metallurgy Gear Manufacturing and Sintering Process2023年9月1日 The effect of process parameters such as leaves extracts volume, salt precursor concentration, contact time and calcination temperature were investigated on the surface area of iron oxide nanoparticle synthesis The green synthesized iron oxide nanoparticles were characterized using UV–Visible spectrophotometer, Xray powder diffraction (XRD Green synthesis of iron oxide nanoparticles by Taguchi design of
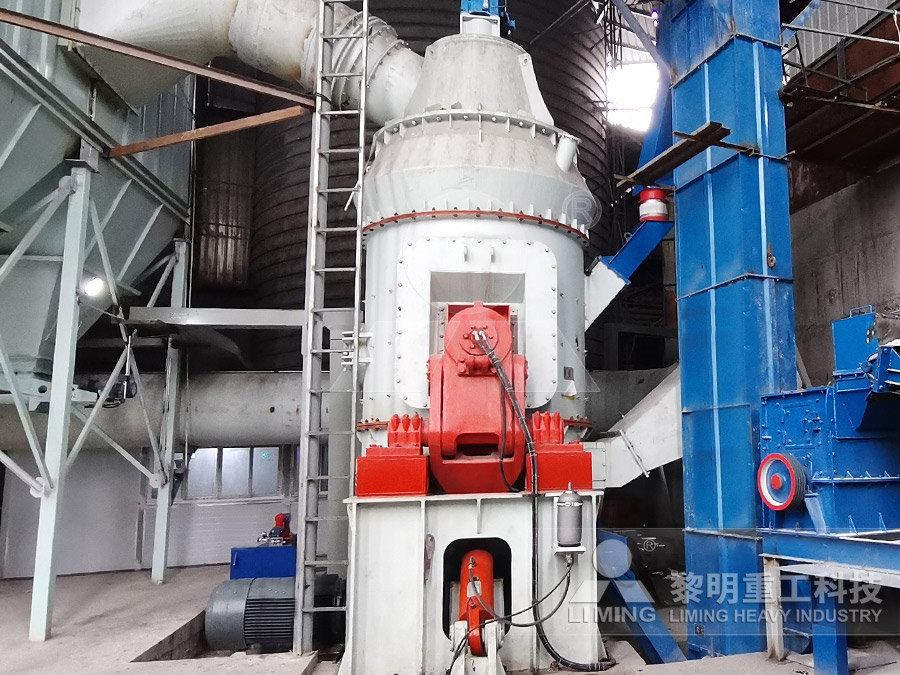
iron oxide greeniron oxide green pigmentsConstruction grade iron
Construction grade iron oxide green is recommended for paving stones, color concrete blocks, interlocking bricks, split brick, color harder, roofing tiles, rubber bessel, slurry, color asphalts, permeable asphalt concrete, sports racetracks, woodplastic floor WPC etc iron oxide green sample iron oxide green C835 iron oxide green C年1月1日 The most common inorganic pigment is red iron oxide World production of iron oxide pigments is about 600 thousand tons per year and greatly exceeds the production of other color pigments, with Development of technology for the production of natural red iron oxide In this process copper ore is mined, crushed, ground, concentrated, smelted and refined The mining, crushing and grinding portions of the processing are extremely energy intensive since the rock must be reduced essentially to talcum powder fineness in order to separate the copperbearing minerals from itHow Hydrometallurgy and the SX/EW Process Made Copper the "Green2023年3月9日 Powder Preparation First, manufacturers create the ferrite powder—a carefully measured blend of iron oxide and other elements The powder mixture is determined by weight and is held to extremely high purity standards; even slight fluctuations in purity can significantly impact the finished productFerrite Core Grinding: A Guide Quartzite Processing Inc
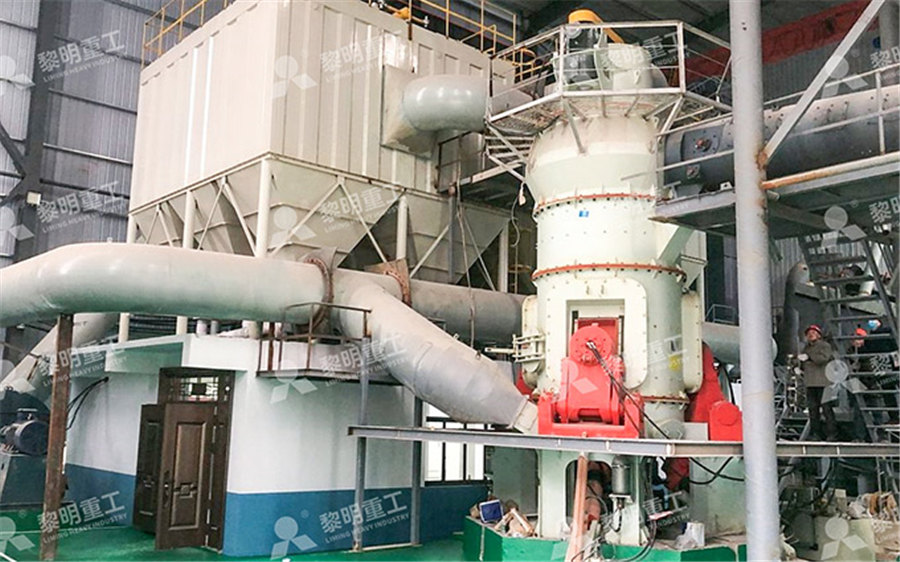
Producing Metal Powder from Machining Chips Using Ball Milling Process
2023年6月27日 The process of ball milling involves the grinding and mixing of metal particles within a ball mill, which is a type of equipment used for grinding, with the aim of producing a fine powder This method has been widely employed in the manufacturing of metal powders from diverse sources, including metals, alloys, and intermetallic compounds2023年8月21日 In cement manufacturing, the grinding process is of utmost significance, as it entails the comminution of clinker, a raw material composed of calcium carbonate, silica, alumina and iron oxide This pivotal process CuttingEdge Grinding Solutions Indian Cement ReviewThe red iron oxide or ferric oxide glaze is one of those prevalent glazes that act as a much more common colorant for the glazing mixture With its easy availability, it offers a beautiful color to the glazing when fired inside the kiln Everything You Wanted to Know About Iron Oxide surface of the iron powder The main ingredients of these powders are pure iron powder (reduced iron powder) or atomized iron powder, and alloyed steel powder, which are blended with submaterials (copper powder, graphite powder, etc) and lubricants according to the customer’s specifications In addition to the excellent properties ofJIP® Iron Powder Products and Technical Trends in Powder
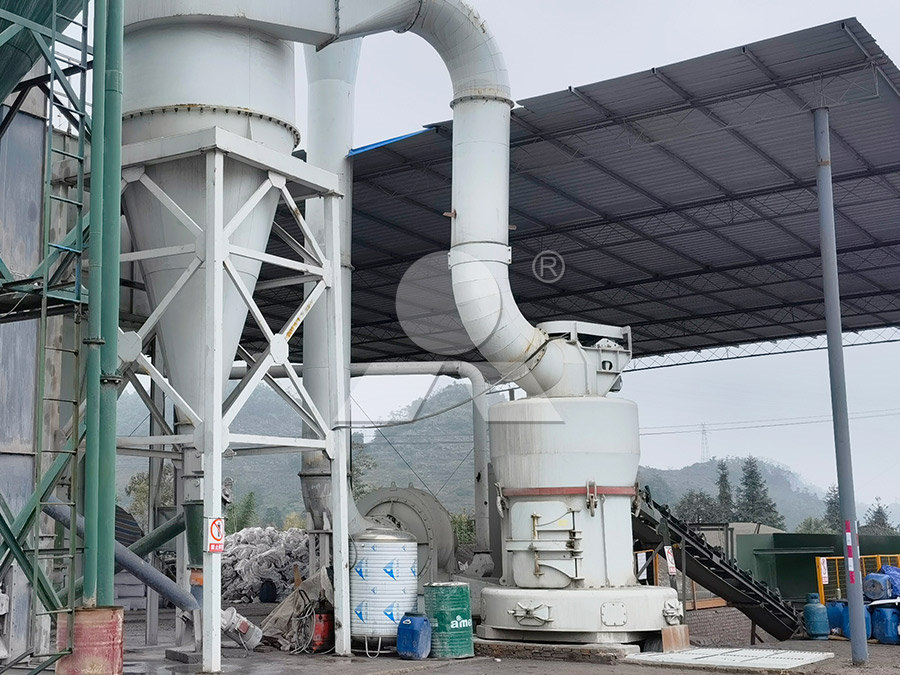
Iron Ore Pellets and Pelletization Process IspatGuru
2014年11月26日 Iron Ore Pellets and Pelletization Process satyendra; November 26, 2014; 0 Comments ; bentonite, binder, Grate kiln, induration, Pelletization Pellets, straight grate,; Iron Ore Pellets and Pelletization Process Pelletizing of iron ore was started in the 1950s to facilitate the utilization of finely ground iron ore concentrates in steel production2018年7月11日 The iron ore production has significantly expanded in recent years, owing to increasing steel demands in developing countries However, the content of iron in ore deposits has deteriorated and lowgrade iron ore has been processed The fines resulting from the concentration process must be agglomerated for use in iron and steelmaking This chapter Iron Ore Pelletizing Process: An Overview Semantic ScholarIntroductionPowder grinding mill is a new type of grinding equipment for making super fine powder through more than 20 times of test and improvement,mainly suitable for the super fine powder processing of non explosive brittle materials with medium and low hardness,and Mohs hardness below 6 degree,such as calcite,chalk and other 100 kinds of materials,finished sbm micro powder grinding iron powder millmd2018年7月11日 The iron ore production has significantly expanded in recent years, owing to increasing steel demands in developing countries However, the content of iron in ore deposits has deteriorated and lowgrade iron ore has been processed The fines resulting from the concentration process must be agglomerated for use in iron and steelmaking This chapter Iron Ore Pelletizing Process: An Overview IntechOpen
.jpg)
Iron Alloys Powder: A Complete Guide Additive Manufacturing
2023年10月8日 Iron alloys powder refers to powder metallurgy forms of iron mixed with alloying elements like nickel, chromium, manganese, and carbon Iron powder metallurgy allows the manufacture of parts and components with controlled density, porosity, strength, magnetic and other properties by compacting and sintering ironbased powder mixes2024年5月15日 Recently, iron powder has been proposed as a high energy density, easily storable, and CO2free energy carrier During the iron combustion, thermal energy is released as heat The combusted products, the iron oxide particles, are captured and cyclically reduced back into iron powder in a process that is powered by renewable energyCyclic reduction of combusted iron powder: A study on the 2023年2月1日 Request PDF A novel powdermetallurgical ecofriendly recycling process for tool steel grinding sludge This work comprehensively investigates the reuse of AISI D2 tool steel grinding sludge as A novel powdermetallurgical ecofriendly recycling process for Choose from 11 Iron Oxide Powder types for pigments, polishing, magnetic media process efficiency, and emissions reduction Unique glass materials for melting, processing, shaping, and fabrication for glass applications Green Technology Handpicked materials for the development and implementation of green technologies Lithium Ion Iron Oxide Powder Goodfellow
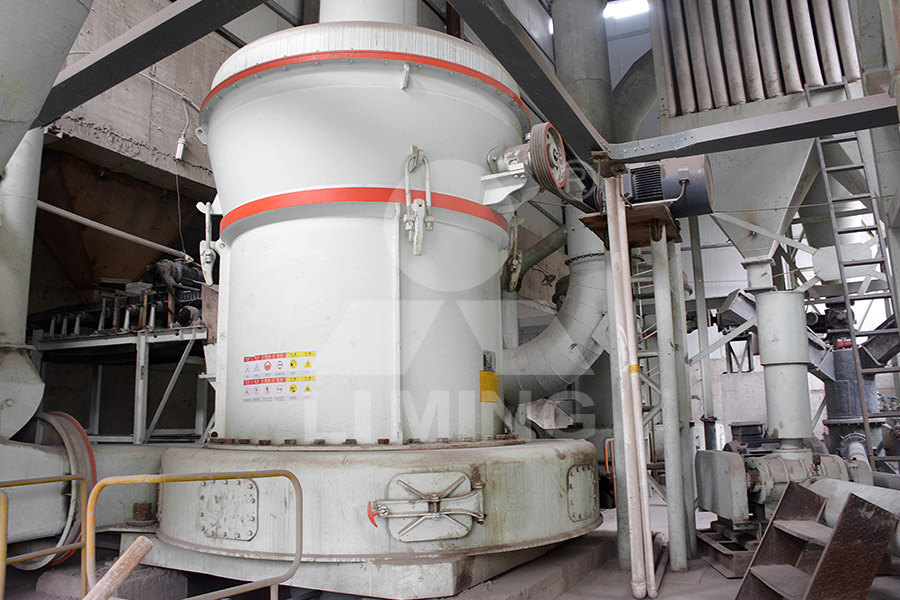
SAFETY GUIDELINES FOR IRON STEEL SECTOR MINISTRY OF
221 Pretreatment process of Iron Ore Fines In the pretreatment process, iron ore fines are ground into finer size, suitable for green ball formation Dry or wet grinding process is adopted for grinding the iron ore fines In dry grinding process, equipment ie drier, ball mill,2023年2月9日 develop a new understanding of iron ore dissolution kinetics and a novel electrochemical regeneration scheme that enhances iron ore dissolution and increases the efficiency of iron extraction Instead of heating and smelting the iron ore, Electra’s process dissolves the ore in a waterbased acid solution Next, electricity is used to Producing green iron with a zeroCarbon electrochemical Process S2021年1月4日 Until the late 19th century iron oxide pigments were obtained wholly from natural materials, generally with little alteration other than physical purification In some cases roasting or calcination was also carried out However, beginning in the first part of the 20th century, chemical methods were developed for synthetic production of commercial iron oxidesIron Oxide Pigments 911Metallurgist2019年8月23日 Stage grinding, stage selection, coarsefine separation, gravitymagnetic separationreverse flotation process have been applied in China’s mixed iron ore dressing plant 3 Fine screening and grinding process Features The fine sieving and regrinding process is an effective method to improve the grade of iron concentrateIron Processing Equipment, Process Flow, Cases JXSC Machine
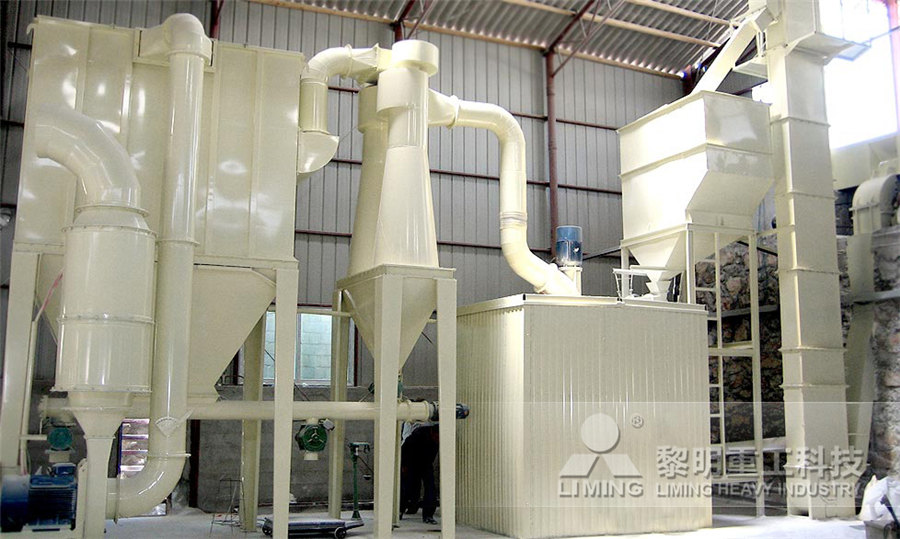
Materials and processes for cutting, grinding PPT SlideShare
2021年11月2日 Gold Alloy Gold is a relatively soft material Slowspeed handpieces Technique consists of the following steps: (1) Contour carbide burs, green stones (silicone carbide), or heatless stones (2) Finish pink stones (aluminum oxide), or mediumgrade abrasive impregnated rubber wheels and points (brown and green) (3) apply fine abrasive 1 A hard brittle layer of pure metal which is subsequently milled to obtain powder (eg iron powder) 2 A soft, spongy substance which is loosely adherent and easily removed by scrubbing 3 A direct powder deposit from the electrolyte that collects at the bottom of the cell Factors promoting powder deposits are, high current density, low metalPowder metallurgy – basics applications IIT GuwahatiUsing Fine Iron Oxide Powder Fine iron oxide having a specific surface area of 129 104 m2/kg and 770 ppm of Cl, and conventional spray roasted iron oxide JCCPW (manufactured by JFE Chemical) prepared by the sprayroasting method, having a specific surface area of 49 103 m2/kg and 770 ppm of Cl were used as the raw materials for ferritesFine Iron Oxide Powder as a Raw Material of Soft Ferrites†2021年12月1日 Request PDF Grinding behavior of VP50IM steel using green and black silicon carbide compared to aluminum oxide wheel under different feed rates Technological advances and the development of Grinding behavior of VP50IM steel using green and black silicon
.jpg)
(PDF) Iron Oxide Nanoparticles: Green Synthesis and
2023年11月8日 This review focuses on green methods for synthesizing iron oxide nanoparticles using bacteria, fungi, yeasts, plant extract, and organic waste In addition, IONP’s prospective