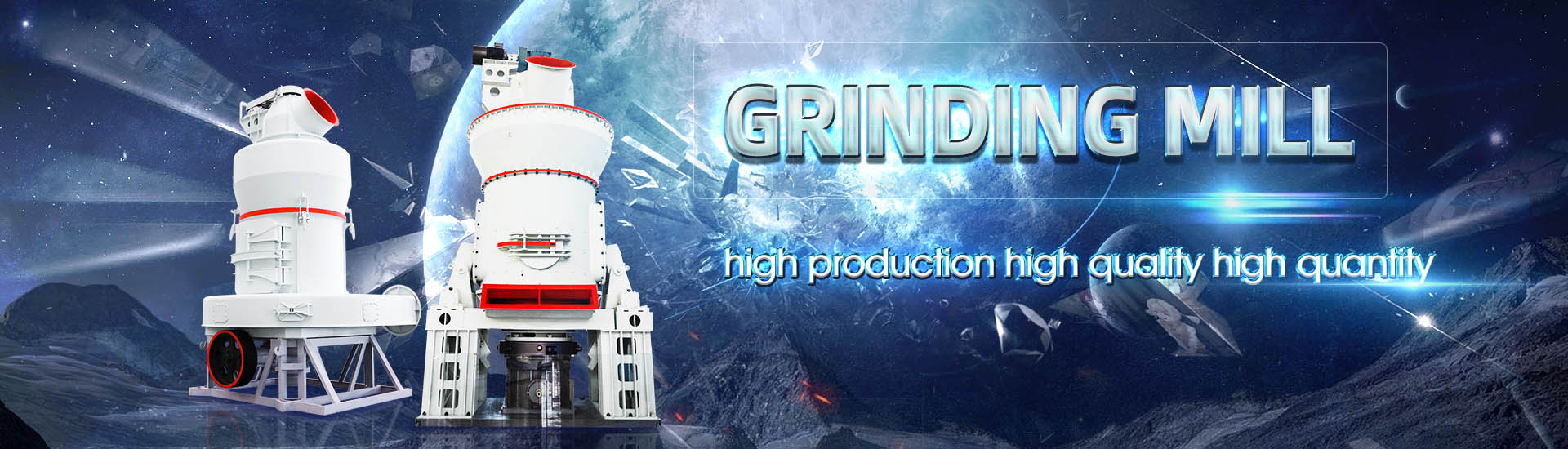
Iron selection ball mill
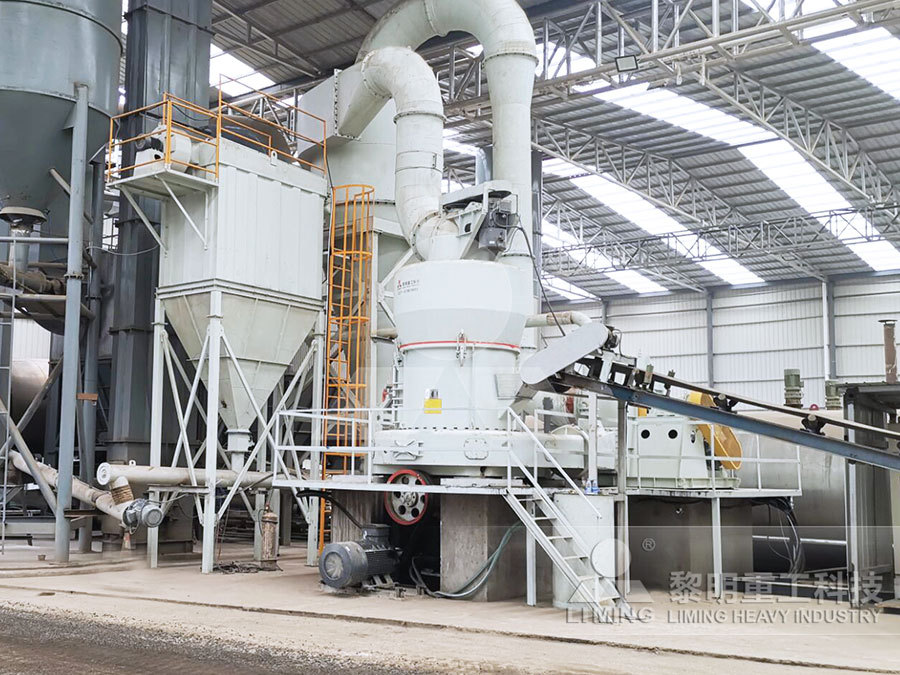
Calculate and Select Ball Mill Ball Size for Optimum
2013年8月3日 In Grinding, selecting (calculate) the correct or optimum ball size that allows for the best and optimum/ideal or target grind size to be achieved 2014年1月1日 An analysis of the kinetics of dolomite grinding in a dry ball mill reveals that the following approximations apply for the parameters of the batch grinding model: the size discretized selection Population balance model approach to ball mill We are manufacturer and supplier of ball mills since 1980 400 installations worldwide with closed and open circuits ball mill for cement, limestone, iron ore and coal Corporate Video ; Your Blog Contact Us Career HOME Selection Closed and Open Circuits Ball Mill for Cement, 2024年1月1日 One attractive alternative is the model proposed by Herbst and Fuerstenau (1980), which is based on a population balance model and relies exclusively on parameters estimated from batchgrinding tests on a mill equipped with a torque sensorThe method allows capturing variations in mill filling and mill speed, whereas effects such as ball size distribution Simulating largediameter industrial ball mills from batch
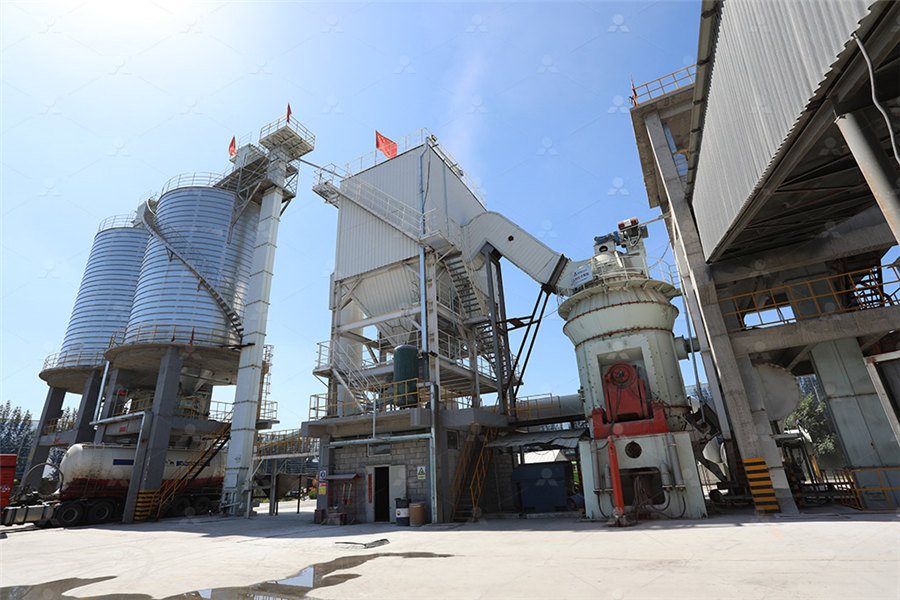
Research progress on synthesis mechanism and performance
2024年6月3日 The pretreatment of ball milled biochariron based materials includes: (1) impregnating iron salt solution; and (2) direct mixing The former initially immerses the original biomass in an iron 2023年10月27日 The ball mill is a rotating cylindrical vessel with grinding media inside, which is responsible for breaking the ore particles Grinding media play an important role in the comminution of mineral A Review of the Grinding Media in Ball Mills for Mineral Processingother two mills were used in this investigation: a pilotscale ball mill (0416 m diameter) and Vale’s industrial mill (518 m diameter), in operation in Vitoria, Espírito Santo, Brazil The pilotscale and the batch mills used were those installed in the Mineral Processing Laboratory at the University of Utah ISSN 21763135 227POPULATION BALANCE MODEL APPROACH TO BALL MILL OPTIMIZATION IN IRON 2013年8月3日 In Grinding, selecting (calculate) the correct or optimum ball size that allows for the best and optimum/ideal or target grind size to be achieved by your ball mill is an important thing for a Mineral Processing Engineer AKA Metallurgist to do Often, the ball used in ball mills is oversize “just in case” Well, this safety factor can cost you much in recovery and/or mill liner Calculate Ball Mill Ball Size for Optimum Grinding
.jpg)
Population balance model approach to ball mill optimization in iron
2014年10月20日 An analysis of the kinetics of dolomite grinding in a dry ball mill reveals that the following approximations apply for the parameters of the batch grinding model: the size discretized selection 2017年11月1日 To understand the friction and wear of working mediums in iron ore ball mills, experiments were conducted using the ball cratering method under dry and wet milling conditions, which mimic the operating conditions in ball mills The liner sample is made of Mn16 steel, the ball had a diameter of 25 mm and was made of GCr15 steel, and the iron ore powder was Friction and wear of liner and grinding ball in iron ore ball mill 2023年10月27日 The ball mill is a rotating cylindrical vessel with grinding media inside, which is responsible for breaking the ore particles Grinding media play an important role in the comminution of mineral ores in these mills This work reviews the application of balls in mineral processing as a function of the materials used to manufacture them and the mass loss, as A Review of the Grinding Media in Ball Mills for Mineral 2020年7月9日 The ball mill liners and grinding media are the largest consumption of wearresistant iron and steel parts with an annual consumption of 2 million tons in China With the development of China’s economic Ball Mill Liners Material Selection And Application
.jpg)
Grinding Media in Ball Mills for Mineral Processing
2023年11月24日 Although the selection of grinding media is generally based on wear, it is also influenced by other parameters, such as the mineralogy, and glass, this section is going to focus on cast iron and steel grinding media, together with their applicability in ball mills Cast iron carbon content is generally between 2 and 4 wt %, Table 1 Chemical composition of typical grinding media (% wt) Adapted from [24] 211 Cast Iron Cast iron can be grey cast iron or white cast iron, but white cast irons are commonly used in Grinding Media in Ball MillsA Review ResearchGate2019年6月18日 Important advances have been made in the last 60 years or so in the modeling of ball mills using mathematical formulas and models One approach that has gained popularity is the population balance Optimization of Solids Concentration in Iron Ore Ball Milling 2019年6月18日 Important advances have been made in the last 60 years or so in the modeling of ball mills using mathematical formulas and models One approach that has gained popularity is the population balance model, in particular, when coupled to the specific breakage rate function The paper demonstrates the application of this methodology to optimize solids concentration in Optimization of Solids Concentration in Iron Ore Ball Milling
.jpg)
Simulating largediameter industrial ball mills from batch
2024年1月1日 Simulating largediameter industrial ball mills from batchgrinding tests Author links open overlay panel Edward Mavhungu a, Very distinct breakage and selection functions appeared when comparing PGMs and itabirite iron ores Optimization of solids concentration in iron ore ball milling through modeling and simulation the rate of breakage of fine particles decreases It demonstrates that the breakage and specific selection (breakage rate) functions generally are a function of the size distribution existing within the mill, as well as of the operating conditions The variable that can be more readily controlled in a wet ball mill in operation in industry isOptimization of Solids Concentration in Iron Ore Ball Milling 2024年8月8日 The selection of grinding media is a critical decision in the ball milling process, affecting not only the efficiency of the operation but also the quality of the final product Several key factors must be considered to ensure the optimal performance and costeffectiveness of the milling processBall Mill Success: A StepbyStep Guide to Choosing the Right 2024年11月5日 This review comprehensively examines recent advancements in the synthesis and environmental applications of ironbased materials (IBMs), with a particular focus on the enhancements achieved through mechanical ball milling IBMs, including zerovalent iron (ZVI) and its composites, have garnered significant attention for their potential in environmental IronBased Materials Synthesized by Mechanical Ball Milling for
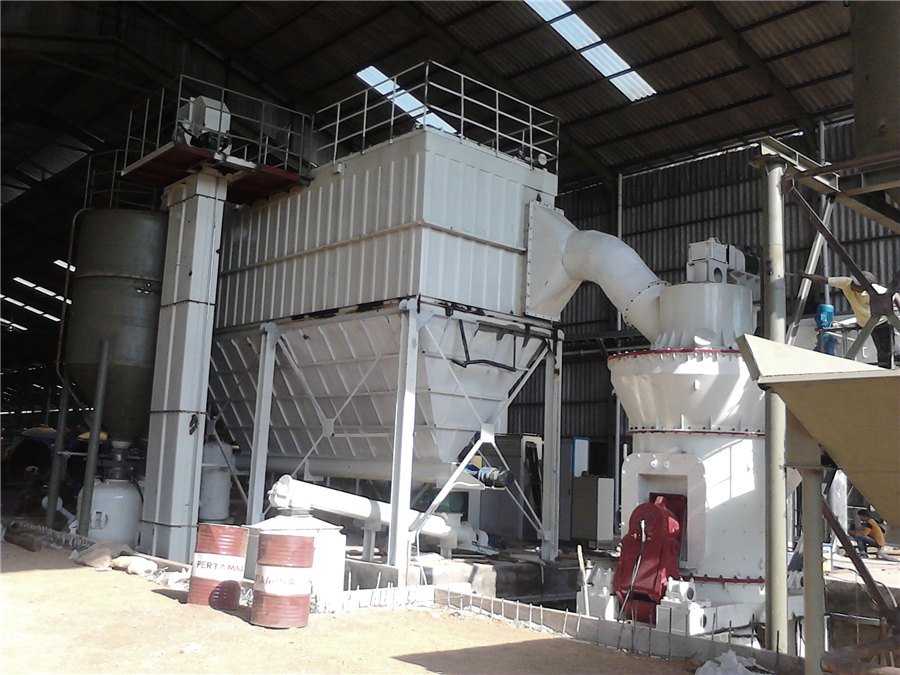
Ball Mills 911Metallurgist
2017年2月13日 Mill Selection The first step in mill design is to determine the power needed to produce the desired grind in the chosen ore The above considerations apply also to the linings of ball and rod mills Liners of castiron can be substituted for chrome or manganese steel, 2023年4月24日 This review paper is mainly going to focus on the effect of grinding media on ball mill performance Grinding media directly affects energy consumption, product size and consequently the grinding costs [11] Proper selection of the grinding media reduces energy and material consumption in a ball mill Different performances are achieved whenGrinding Media in Ball MillsA Review Preprints2024年2月19日 The ball mill steel ball is the medium for grinding materials in the ball mill equipment Reasonable selection of the gradation of ball mill steel balls is an indispensable measure to improve the output and quality of ball mills Ball Mill Steel Balls: Quality And Gradation JXSC An iron powder ball mill is used to grind iron powder directly, as some industries don't require high iron content and prefer coarser iron powder The iron powder ball mill grinds the iron powder to a certain size, typically 100200 mesh, which Iron Fine Powder Ball Mill Application Scope
.jpg)
Friction and wear of liner and grinding ball in iron ore ball mill
2017年11月1日 An iron ore mill relies on the grinding and impact of grinding balls to complete iron ore crushing The operating process of an iron ore mill is as follows: first, the ores are poured into the mill, and both the ores and the grinding balls are lifted by the lifting bar arranged on the wall of the cylinder body to a certain height, after which they fall onto the bottom of the mill to 2014年11月1日 The sample of coarse iron ore was characterized in laboratory tests carried out in a small batch ball mill Selection and breakage function parameters were determined from the laboratory testsVertical mill simulation applied to iron ores ResearchGateChoose from our selection of ball end mills in a wide range of styles and sizes In stock and ready to ship BROWSE CATALOG Made of highspeed steel, these end mills are for general purpose milling in most material, such as aluminum, brass, bronze, iron, and steel Cubic Boron Nitride Ball End MillsBall End Mills McMasterCarr2012年6月1日 The Selection and Design of Mill Lin ers – In: Advances in Comminution S K Kawatra, Ed Ball mills can grind a wide range of materials, including metals, ceramics, Grinding in Ball Mills: Modeling and Process Control
.jpg)
Vertical mill simulation applied to iron ores ScienceDirect
2015年4月1日 Eq (5) is used to describe the selection function of a vertical mill of any scale, pilot or industrial [10]Three samples of iron ore (pellet feed), here named samples A, B and C, were tested in a pilot vertical mill The samples were also characterized in order to generate parameters for Eqs2024年1月10日 Ball and rod mills are widely used grinding equipment in mineral processing plants Home » News » Ball Mill VS Rod Mill: Difference Selection Contact Now +86 Published time:10 January 2024 Ball and rod mills are widely used grinding equipment in mineral processing plantsBall Mill VS Rod Mill: Difference Selection JXSC Machine2014年1月1日 An analysis of the kinetics of dolomite grinding in a dry ball mill reveals that the following approximations apply for the parameters of the batch grinding model: the size discretized selection Population balance model approach to ball mill We are manufacturer and supplier of ball mills since 1980 400 installations worldwide with closed and open circuits ball mill for cement, limestone, iron ore and coal Corporate Video ; Your Blog Contact Us Career HOME Selection Closed and Open Circuits Ball Mill for Cement,
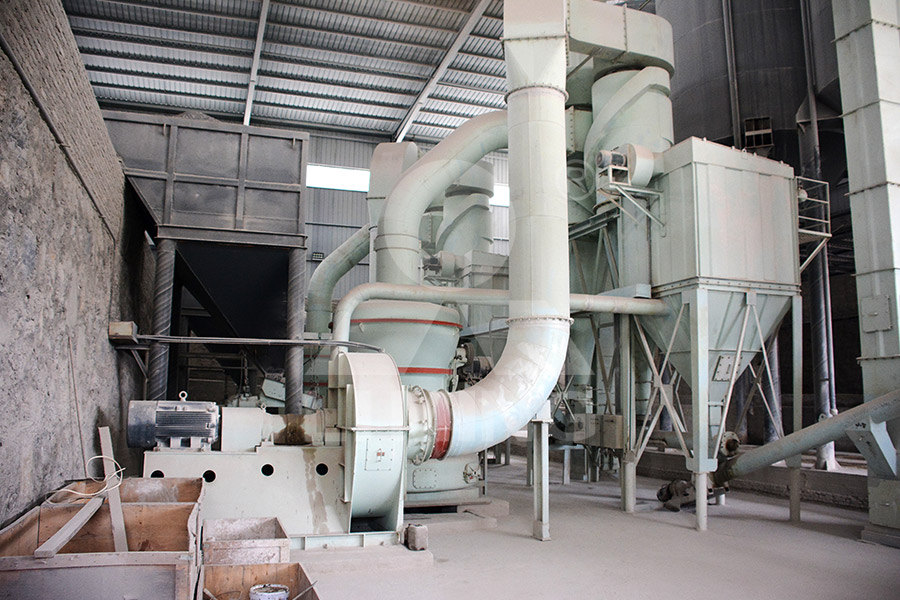
Simulating largediameter industrial ball mills from batch
2024年1月1日 One attractive alternative is the model proposed by Herbst and Fuerstenau (1980), which is based on a population balance model and relies exclusively on parameters estimated from batchgrinding tests on a mill equipped with a torque sensorThe method allows capturing variations in mill filling and mill speed, whereas effects such as ball size distribution 2024年6月3日 The pretreatment of ball milled biochariron based materials includes: (1) impregnating iron salt solution; and (2) direct mixing The former initially immerses the original biomass in an iron Research progress on synthesis mechanism and performance2023年10月27日 The ball mill is a rotating cylindrical vessel with grinding media inside, which is responsible for breaking the ore particles Grinding media play an important role in the comminution of mineral A Review of the Grinding Media in Ball Mills for Mineral Processingother two mills were used in this investigation: a pilotscale ball mill (0416 m diameter) and Vale’s industrial mill (518 m diameter), in operation in Vitoria, Espírito Santo, Brazil The pilotscale and the batch mills used were those installed in the Mineral Processing Laboratory at the University of Utah ISSN 21763135 227POPULATION BALANCE MODEL APPROACH TO BALL MILL OPTIMIZATION IN IRON
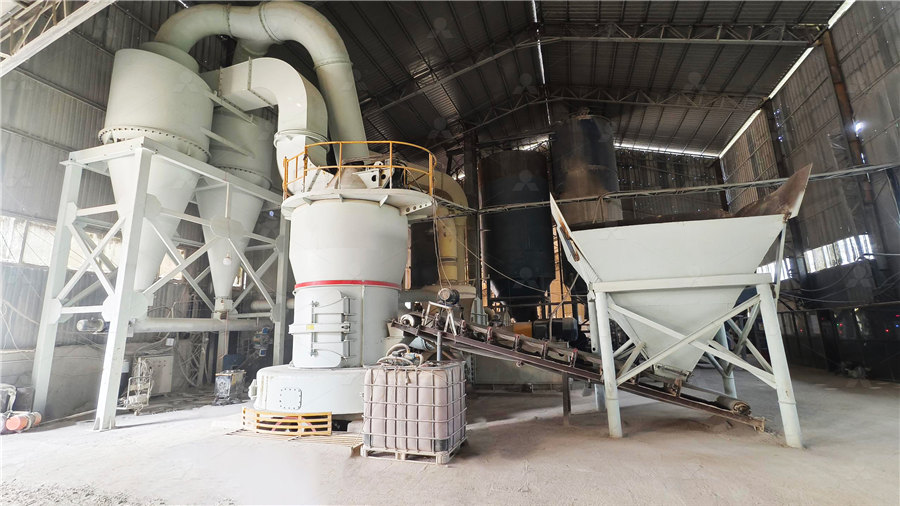
Calculate Ball Mill Ball Size for Optimum Grinding
2013年8月3日 In Grinding, selecting (calculate) the correct or optimum ball size that allows for the best and optimum/ideal or target grind size to be achieved by your ball mill is an important thing for a Mineral Processing Engineer AKA Metallurgist to do Often, the ball used in ball mills is oversize “just in case” Well, this safety factor can cost you much in recovery and/or mill liner 2014年10月20日 An analysis of the kinetics of dolomite grinding in a dry ball mill reveals that the following approximations apply for the parameters of the batch grinding model: the size discretized selection Population balance model approach to ball mill optimization in iron 2017年11月1日 To understand the friction and wear of working mediums in iron ore ball mills, experiments were conducted using the ball cratering method under dry and wet milling conditions, which mimic the operating conditions in ball mills The liner sample is made of Mn16 steel, the ball had a diameter of 25 mm and was made of GCr15 steel, and the iron ore powder was Friction and wear of liner and grinding ball in iron ore ball mill 2023年10月27日 The ball mill is a rotating cylindrical vessel with grinding media inside, which is responsible for breaking the ore particles Grinding media play an important role in the comminution of mineral ores in these mills This work reviews the application of balls in mineral processing as a function of the materials used to manufacture them and the mass loss, as A Review of the Grinding Media in Ball Mills for Mineral