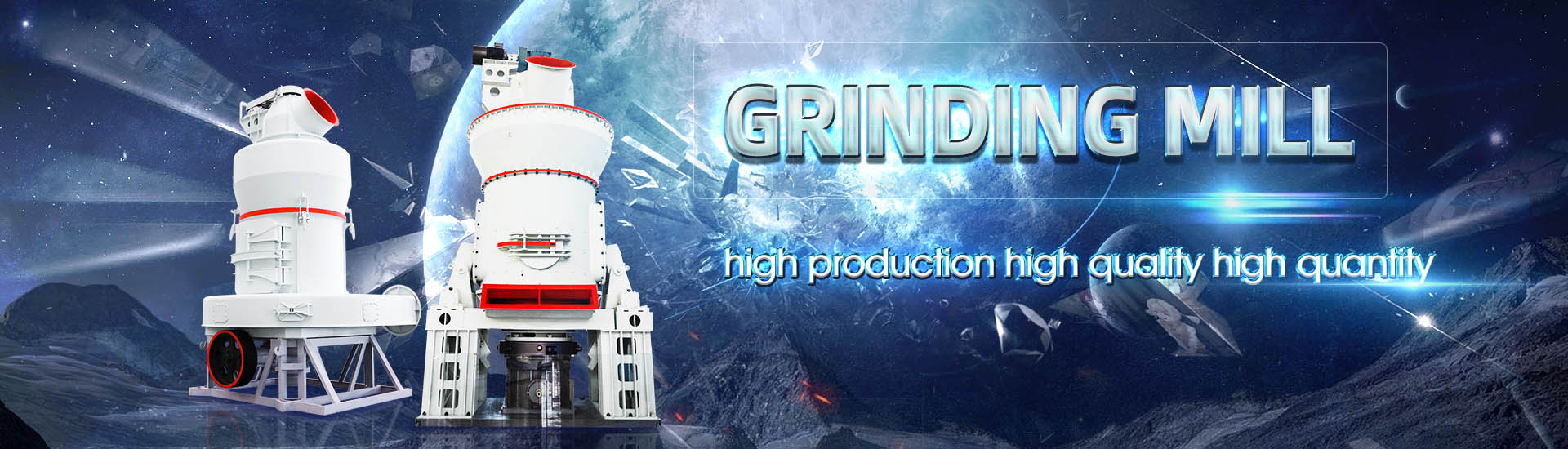
A word on coal mill selection
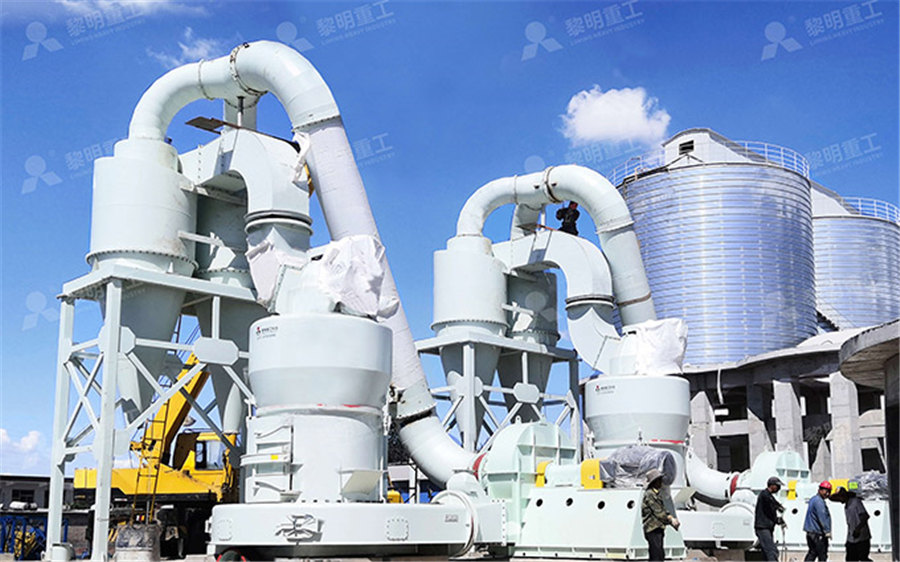
Coal Mill an overview ScienceDirect Topics
The coal properties such as volatile components, ash content, hardness, humidity and grinding fineness are the decisive factor for selecting the required mill Basically, coal pulverisers can be divided into three assembly groups, impact mills, gravityforce mills and external force millsCoal mill is an important component of the thermal power plant It is used to grind and dry the moisturized raw coal and transport the pulverized coal – air mixture to the boiler Poor dynamic (PDF) Modeling and Control of Coal Mill AcademiaThe selection of an appropriate coal mill is vital for the efficient and costeffective operation of a cement plant This article outlines the key criteria for selecting a coal mill in the cement Selection Criteria for Coal Mills in Cement Industries: A Coal mill is an important component of the thermal power plant It is used to grind and dry the moisturized raw coal and transport the pulverized coal – air mixture to the boiler Poor dynamic Modeling and Control of Coal Mill
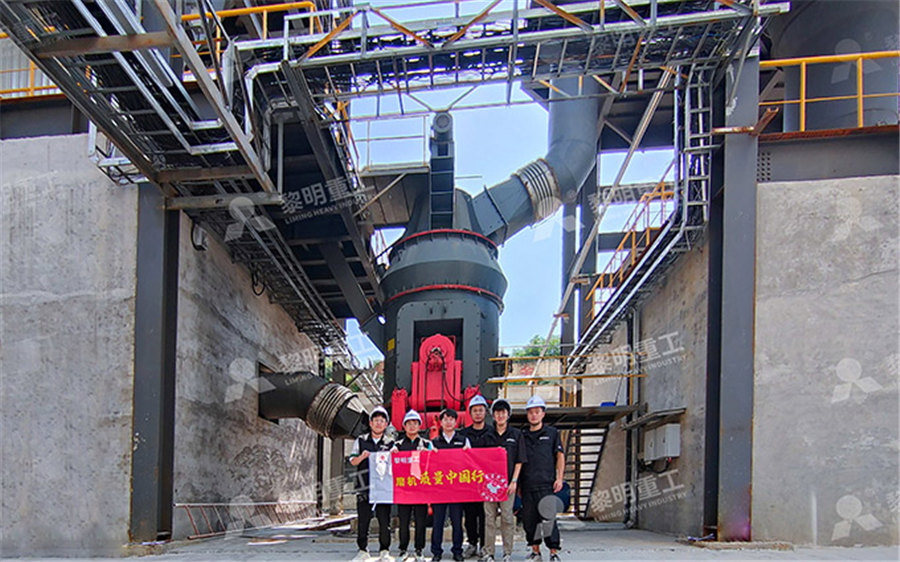
Coal Selection an overview ScienceDirect Topics
The first step in selecting new coal sources is to review the fuel specifications Coal quality parameters can be compared against the design coal (or coal basket) and any coals 2012年5月1日 The paper presents development and validation of a coal mill model to be used for improved mill control, which may lead to a better load following capability of power plants Derivation and validation of a coal mill model for controlThere are many types of coal mill, according to the speed of the grinding working parts of the coal mill equipment selection category can be divided into three types, namely: lowspeed coal mill, How to choose coal grinding equipment? What are the basis for The production of 200 mesh coal powder requires the selection of an appropriate vertical mill that meets the specific requirements of the application The choice of vertical mill should be based Choosing the right vertical mill for 200 mesh coal powder
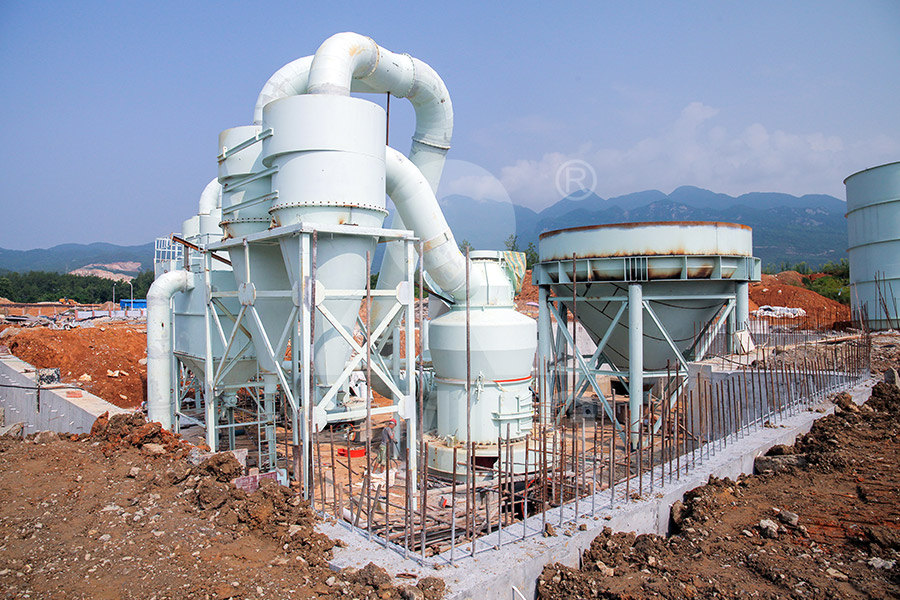
Modeling of complex equipment coal mill in power plant ICJE
For a complex equipment with seventeen inputs and six outputs, a power plant coal mill is used as a target to study and model using two methods: least squares linear regression and multilayer 2010年10月13日 There are three main steps in designing a good crushing plant: process design, equipment selection, and layout The first two are dictated by production requirements and Coal Mill: Crushing Plant Design and Layout ConsiderationsThis document provides a draft design guide for inerting medium speed vertical spindle coal pulverizers It discusses inerting system design considerations such as inerting media selection, steam source considerations, and steam piping Inerting Steam For Coal Mill Fire PDF2018年5月2日 Coal mill malfunctions are some of the most common causes of failing to keep the power plant crucial operating parameters or even unplanned power plant shutdowns Therefore, an algorithm has been developed that Detection of Malfunctions and Abnormal Working
.jpg)
Two Coal Mill Operation PDF Coal Scribd
121 TWO COAL MILL OPERATION Free download as Word Doc (doc), PDF File (pdf), Text File (txt) or read online for free This document provides standard operating procedures for operating a boiler with two coal mills at partial load 2015年11月1日 As presented by Andersen et al (2009) and Odgaard, Stoustrup, and Mataji (2007), coal moisture imposes limit on the maximum load at which a coal mill can be operated and the load gradient (how fast the mill may change its operating point), if it is desired that the pulverized coal entering the furnace has moisture content less than or equal to a certain value A unified thermomechanical model for coal mill operation2021年11月9日 We previously reported the milling characteristics of blends of coal and wood pellets (WPs) without torrefaction treatment using the neutral sugar present only in plant biomass, but not in coal, as a tracer in a roller mill 20 In that study, the WPs were selectively accumulated inside the roller mill and discharged with a particle size larger than that of the coal particlesMilling Characteristics of Coal and Torrefied Biomass Blends in a XXV INTERNATIONAL MINERAL PROCESSING CONGRESS (IMPC) 2010 PROCEEDINGS / BRISBANE, QLD, AUSTRALIA / 6 10 SEPTEMBER 2010 1065 INTRODUCTION Coal pulverisation in power plants is an immense INVESTIGATION OF THE CLASSIFICATION OPERATION IN A COAL
.jpg)
Review of control and fault diagnosis methods applied to coal
2015年8月1日 Mill problems originate mainly due to poor controls or faults occurring within the milling system As discussed by GQ Fan and NW Rees [3], the control of mills remains very simple in most of the power plants due to the fact that the mill system is highly nonlinear with strong coupling among the variables and it is very difficult to measure some important The mill is one of six mills supplying the 650k (steam production of 650 t/h) boiler However, the proposed method in this chapter is so generic that it can be applied to other types of coal mills The coal mill is illustrated in Figure 1 The coal is fed to the coal mill through the central inlet pipe, where it is pulverized by a seriesDetection of Malfunctions and Abnormal Working Conditions of a Coal MillSOP startup Shutdown and operation of Coal Mill Free download as Word Doc (doc / docx), PDF File (pdf), Text File (txt) or read online for free This document provides the standard operating procedure for starting up, operating, and shutting down Coal Mill 1 2 It outlines the specific sequence that equipment should be started and stopped in to avoid material SOP Startup Shutdown and Operation of Coal MillCoal characteristics are integral to pulverizer system selection, sizing and performance The production capaci ty for each mill depends upon the following feed properties: In general,the coal entering a mill system should be crushed to a size no larger than Maximum Feed Size —A Comparison of Three Types of Coal Pulverizers Babcock Power
.jpg)
The Research on Design Parameters of Fan Mill Direct Pulverizing System
Energy Procedia 17 ( 2012 ) 1620 – 1626 18766102 2012 Published by Elsevier Ltd Selection and/or peerreview under responsibility of Hainan University doi: 101016/jegypro201202289 2012 International Conference on Future Electrical Power and Energy Systems The Research on Design Parameters of Fan Mill Direct Pulverizing System Xiaoke Guo, Anlong Lv,Feng Xiao 2020年4月2日 The study examines the impact of the power sector reforms on the electricity generation industry at the state level in India through a case study of the state of GujaratAnalysis of the Coal Milling Operations to the Boiler operation of the roller mill and an effective reduction in the size of the coal−TP blend, the selection and use of uniformly and sufficiently torrefied wood pellets are important INTRODUCTIONMilling Characteristics of Coal and Torrefied Biomass Blends in a 2009年9月20日 A control oriented model was then developed by Fan (1994) and Fan and Rees (1994) In 2009, coal flow and outlet temperature of mill were modelled using mass and heat balance equations for startup Modeling and Parameter Identification of Coal Mill
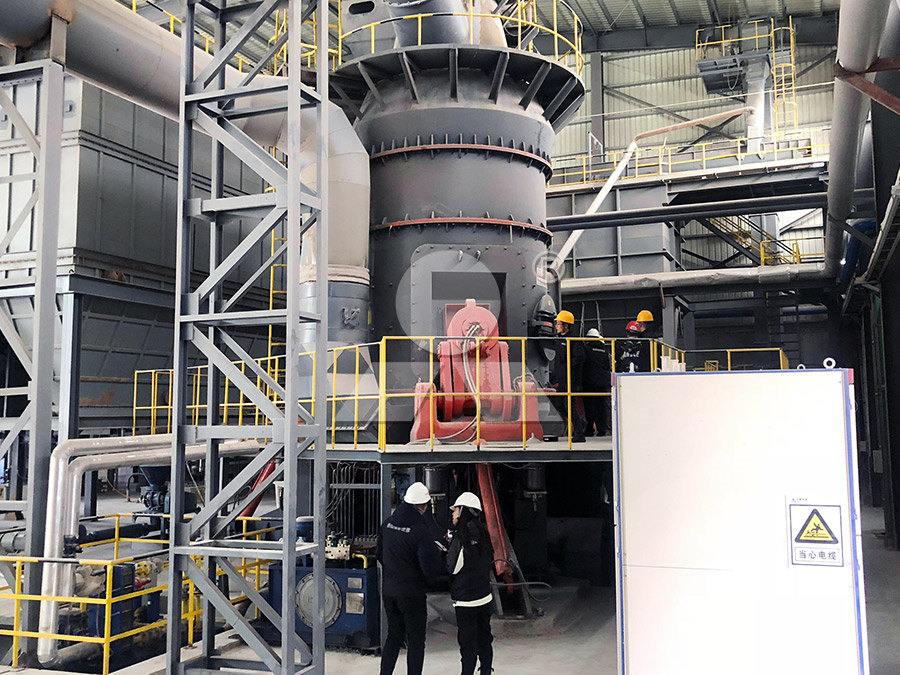
28 SOP of Coal Mill Coal Feeder PDF Pump Scribd
28 SOP of Coal Mill Coal Feeder Free download as Word Doc (doc / docx), PDF File (pdf), Text File (txt) or read online for free This standard operating procedure outlines the steps for starting up and shutting down the coal mill and coal feeder system at the Singareni Thermal Power Plant's 2x600 MW power plant The procedure describes the line up process, startup, 2009年1月1日 Download Citation Selection of coal mill reject handling system for thermal power plants This paper aims at providing some guideline to plant engineers and consultants for selecting the Selection of coal mill reject handling system for ResearchGateAt best, coal mill safety is not well understood and, at worst, it is ignored When it comes to coal mill systems, most cement plant operators just presume that the supplier of the equipment knows all of the standards and rules and is 100% capable of making a system that conforms to these and is therefore safeIn discussion: Coal Mill Safety Coal Mill Safety, Explosion and 2019年5月8日 7 Maintenance Strategy Maintenance Significant Item Inspection / Execution Task Coal Measure HGI (hard grove index), moisture content, abrasiveness and size of coal fed to mill Pulverised fuel (PF) Measure particle size distribution, PF velocity and temperature Grinding media (Balls and Rings) Measure ball diameter, ring depth profile and material TPS Coal Mills and Fan Performance PPT SlideShare
.jpg)
Dual fault warning method for coal mill based on ScienceDirect
2024年5月1日 Coal mill is one of the important auxiliary equipment of thermal power units [6] An early fault detection method for induced draft fans based on MSET with informative memory matrix selection ISA Trans, 102 (2020), pp 325334, 101016/jisatra2020020182024年5月1日 The coal mill operating status variables are measured by pressure sensors, RTD temperature sensors, and so An early fault detection method for induced draft fans based on MSET with informative memory matrix selection ISA Trans (2020) Zhao H et al Anomaly detection and fault analysis of wind turbine components based on deep Dual fault warning method for coal mill based on ScienceDirect2003年1月1日 Wei et al [11] proposed a multisegment coal mill model that covers six milling processes (startup, standard milling, shutdown, idle and transit periods) with parameters identified in each processCoal mill modeling by machine learning based on onsite measurements Coal Mill, Feeder PULV 1 Free download as Word Doc (doc / docx), PDF File (pdf), Text File (txt) or read online for free The document provides a standard operating procedure for coal mill changeover at the Jaypee Nigrie Coal Mill, Feeder PULV 1 PDF Valve Power Station
制粉项目-2023.11.17.jpg)
Grinding Characteristics of Wood Pellet and Coal Mixtures in a Roller Mill
Request PDF On Dec 15, 2020, Kiyoshi Sakuragi and others published Grinding Characteristics of Wood Pellet and Coal Mixtures in a Roller Mill Find, read and cite all the research you need on Coal mill is an important part of the pulverizing system and an important auxiliary power equipment in power plant Its main task is to break and grind coal into pulverized coal to provide boiler equipment, its configuration will directly affect How to choose coal grinding equipment? What are the basis for coal mill This paper was brief, but hopefully has shown the importance of one aspect, mill performance, on many coal quality related issues At first glance one might not consider the influence mill fineness has on mill capacity, slagging and opacity; this paper has shown that it does indeed, and mill performance is only one of many areas of considerationCoping With Coal Quality Impacts on Power Plant Coal 2020年8月12日 In a power plant, the coal mill is the critical equipment, whose effectiveness impacts the overall power plant efficiency Uniform coal feeding mass flow rate and required particle size and temperature at the outlet channel throughout with better classifier performance are crucial indicators that characterize the coal mill performanceAn investigation of performance characteristics and energetic
.jpg)
Development of a Multisegment Coal Mill Model Using an
2007年8月20日 This paper presents a multisegment coal mill model that covers the whole milling process from mill startup to shutdown This multisegment mathematical model is derived through analysis of energy transferring, heat exchange, and mass flow balances The work presented in the paper focuses on modeling Etype vertical spindle coal mills that are widely used in coal DOI: 101016/jmeasurement2022 Corpus ID: ; A BranNew Performance Evaluation Model of Coal Mill Based on GAIFCMIDHGF Method @article{Xu2022ABP, title={A BranNew Performance Evaluation Model of Coal Mill Based on GAIFCMIDHGF Method}, author={Wentao Xu and Yaji Huang and Siheng Song and Gehan Cao and Mengzhu Yu and A BranNew Performance Evaluation Model of Coal Mill Based on 2021年8月1日 Yukio et al [7] proposed a model consisting of blending, grinding and classifying processes for pulverizer control Agarawal et al [8] differentiated coal powder into ten size groups, divided the bowl mill into four zones, and developed a unified model Palizban et al [9] derived nonlinear differential mass equations of raw coal, recirculation coal and suspension coal in Coal mill model considering heat transfer effect on mass Coal grinding mills are essential components of power plants, responsible for converting raw coal into fine coal powder that is essential for efficient combustion in power plant boilers Coal grinding mills can also be used to grind biomass and other alternative fuels, providing a more sustainable and renewable energy source for power generationWhat is a Coal Grinding Mill

Inerting Steam For Coal Mill Fire PDF
This document provides a draft design guide for inerting medium speed vertical spindle coal pulverizers It discusses inerting system design considerations such as inerting media selection, steam source considerations, and steam piping 2018年5月2日 Coal mill malfunctions are some of the most common causes of failing to keep the power plant crucial operating parameters or even unplanned power plant shutdowns Therefore, an algorithm has been developed that Detection of Malfunctions and Abnormal Working 121 TWO COAL MILL OPERATION Free download as Word Doc (doc), PDF File (pdf), Text File (txt) or read online for free This document provides standard operating procedures for operating a boiler with two coal mills at partial load Two Coal Mill Operation PDF Coal Scribd2015年11月1日 As presented by Andersen et al (2009) and Odgaard, Stoustrup, and Mataji (2007), coal moisture imposes limit on the maximum load at which a coal mill can be operated and the load gradient (how fast the mill may change its operating point), if it is desired that the pulverized coal entering the furnace has moisture content less than or equal to a certain value A unified thermomechanical model for coal mill operation
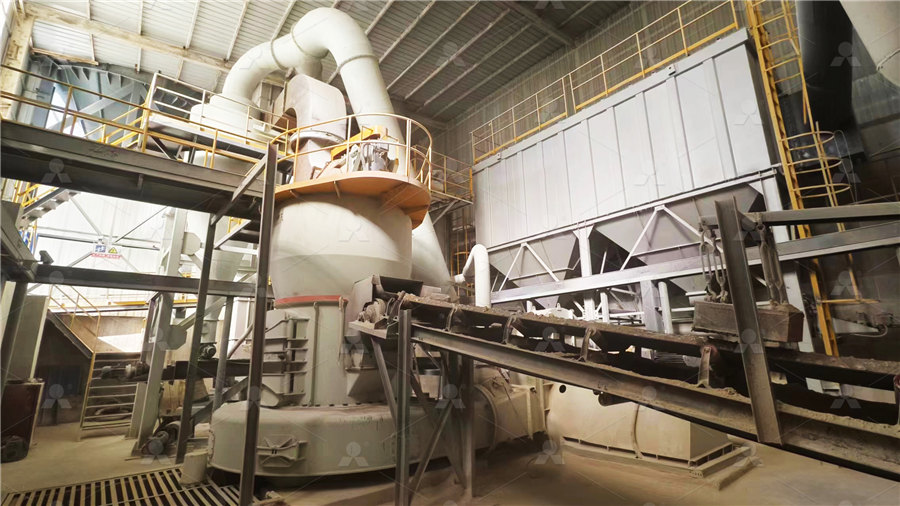
Milling Characteristics of Coal and Torrefied Biomass Blends in a
2021年11月9日 We previously reported the milling characteristics of blends of coal and wood pellets (WPs) without torrefaction treatment using the neutral sugar present only in plant biomass, but not in coal, as a tracer in a roller mill 20 In that study, the WPs were selectively accumulated inside the roller mill and discharged with a particle size larger than that of the coal particlesXXV INTERNATIONAL MINERAL PROCESSING CONGRESS (IMPC) 2010 PROCEEDINGS / BRISBANE, QLD, AUSTRALIA / 6 10 SEPTEMBER 2010 1065 INTRODUCTION Coal pulverisation in power plants is an immense INVESTIGATION OF THE CLASSIFICATION OPERATION IN A COAL 2015年8月1日 Mill problems originate mainly due to poor controls or faults occurring within the milling system As discussed by GQ Fan and NW Rees [3], the control of mills remains very simple in most of the power plants due to the fact that the mill system is highly nonlinear with strong coupling among the variables and it is very difficult to measure some important Review of control and fault diagnosis methods applied to coal The mill is one of six mills supplying the 650k (steam production of 650 t/h) boiler However, the proposed method in this chapter is so generic that it can be applied to other types of coal mills The coal mill is illustrated in Figure 1 The coal is fed to the coal mill through the central inlet pipe, where it is pulverized by a seriesDetection of Malfunctions and Abnormal Working Conditions of a Coal Mill
.jpg)
SOP Startup Shutdown and Operation of Coal Mill
SOP startup Shutdown and operation of Coal Mill Free download as Word Doc (doc / docx), PDF File (pdf), Text File (txt) or read online for free This document provides the standard operating procedure for starting up, operating, and shutting down Coal Mill 1 2 It outlines the specific sequence that equipment should be started and stopped in to avoid material Coal characteristics are integral to pulverizer system selection, sizing and performance The production capaci ty for each mill depends upon the following feed properties: In general,the coal entering a mill system should be crushed to a size no larger than Maximum Feed Size —A Comparison of Three Types of Coal Pulverizers Babcock Power