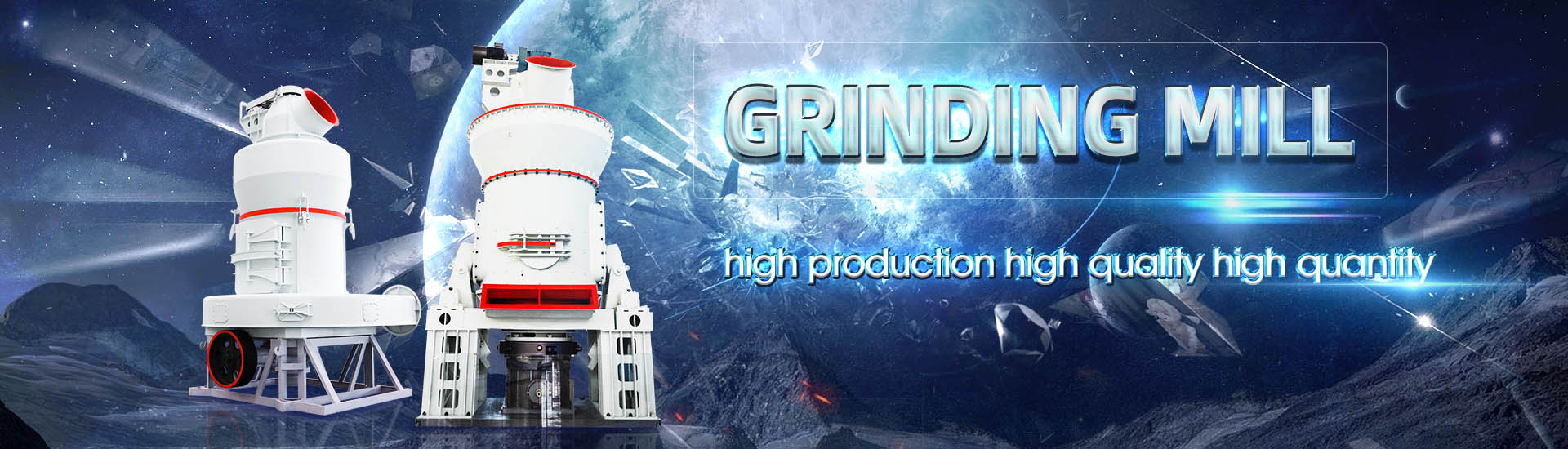
Use of mdd ore grinding mill
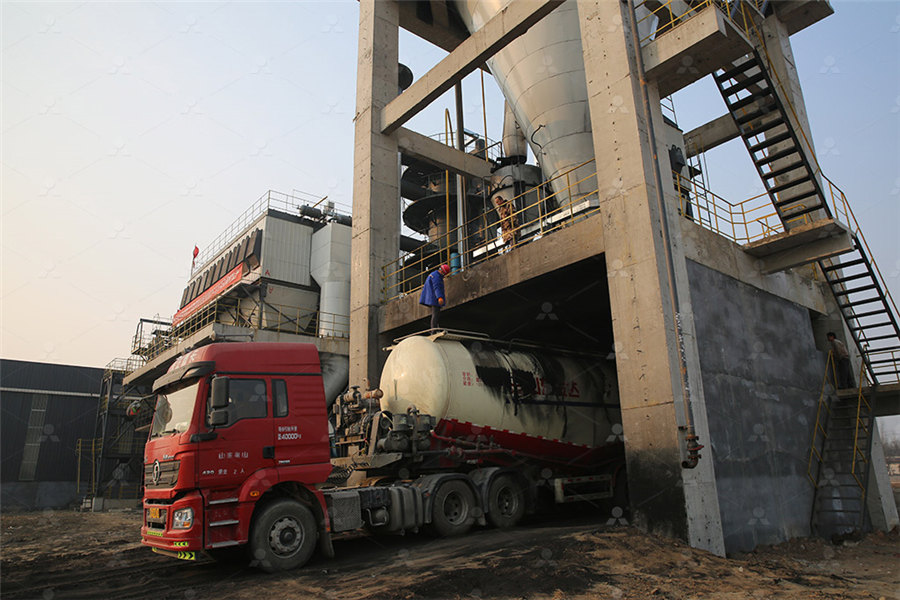
ReviewStirred media mills in the mining industry: Material
2020年6月1日 Stirred media mills are used by the mining industry for ultrafine grinding to enhance liberation, and to decrease particle sizes of industrial minerals to tailor functional properties2023年10月27日 Grinding media play an important role in the comminution of mineral ores in these mills This work reviews the application of balls in mineral processing as a function of the A Review of the Grinding Media in Ball Mills for Mineral Processing 2023年11月24日 Grinding media play an important role in the comminution of mineral ores in these mills 1 Introduction The mining industry has been battling decreased head grades and Grinding Media in Ball Mills for Mineral ProcessingA simple and novel nonlinear model of a runofmine ore grinding mill circuit, developed for process control and estimation purposes, is validated The model makes use of the minimum Analysis and validation of a runofmine ore grinding mill circuit
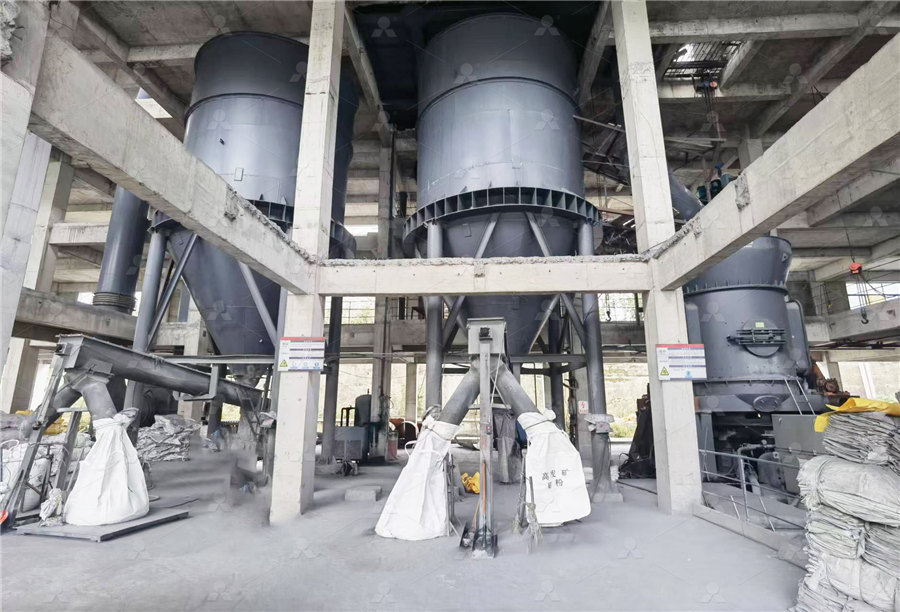
Fine Grinding as Enabling Technology – The IsaMill
Stirred milling was developed for fine grained ores that required an economic grind to sub 10 micron sizes The first examples were lead zinc deposits – McArthur River, George Fisher and 2024年8月7日 After crushing, grinding refines ore into a fine powder to liberate valuable minerals Key types include Ball Mills, which grind ore using steel balls in a rotating cylinder; Mineral Processing Equipment for Mining Industry2013年12月18日 Fine grinding, to P80 sizes as low as 7 μ m, is becoming increasingly important as mines treat ores with smaller liberation sizes This grinding is typically done using stirred Energy Use of Fine Grinding in Mineral Processing2013年8月1日 In this study, the current understanding of the factors affecting the consumption of steel media in comminution systems in mineral processing are reviewed, together with models Consumption of steel grinding media in mills – A review
.jpg)
TECHNOLOGY SELECTION OF STIRRED MILLS FOR ENERGY
These methods and strategies will focus specifically on the two major stirred mill machine types; namely, gravityinduced (VERTIMILLTM grinding mill and NippionEirich tower mill) and Grinding mills are crucial equipment in the mining and mineral processing industry, used primarily for the reduction of ore and mineral particles The proper functioning of grinding mills is vital for Understanding the operation of grinding mills in the mining and 2013年4月1日 A simple and novel nonlinear model of a runofmine ore grinding mill circuit, developed for process control and estimation purposes, is validatedAnalysis and validation of a runofmine ore grinding mill circuit In the mill, the mixture of medium, ore, and water, known as the mill charge, is intimately mixed, the medium comminuting the particles by any of the above methods Apart from laboratory testing, grinding in mineral processing is a continuous process, material being fed at a controlled rate into one end of the mill and discharging at the other end after a suitable dwell (residence) timeGrinding Mill an overview ScienceDirect Topics
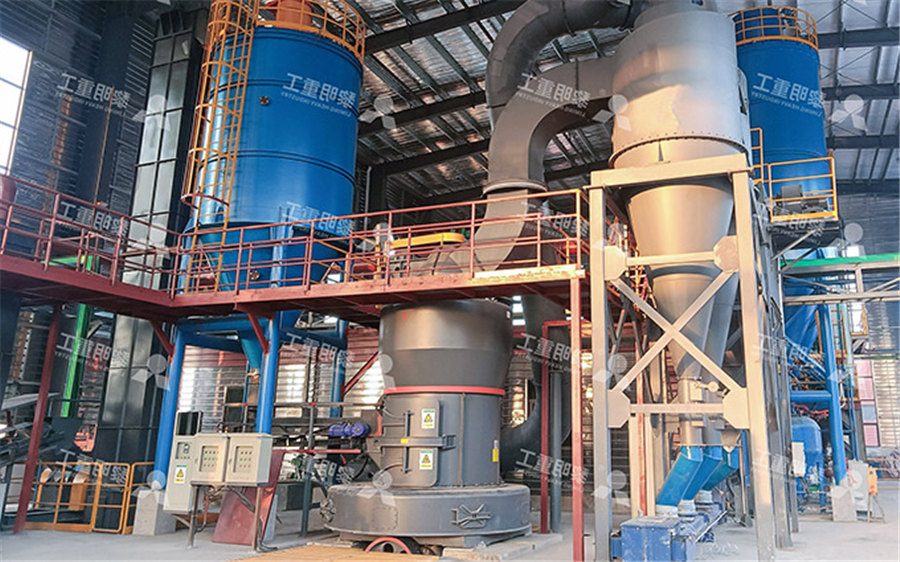
Ultra Fine Grinding A Practical Alternative to Oxidative
UFG mills overcome these limitations by the use of rotating stirrers inside a stationary mill shell Ultra fine grinding mills have been in use for many years in a large number of every day applications such as pharmaceuticals, dyes, clays, paint and pigments before being used in the mineral processing industry2015年8月6日 There are basically two groups of Grinding Mill Liners Ones with a HIGH PROFILE and those with a LOW PROFILE The high profile liner is designed to give the The amount of unground material will slowly increase until the mill can no longer grind the bigger oreGrinding Mill Liners 911Metallurgistwhich use both ore and steel balls as grinding media (Wei and Craig, 2009b) In the case of a ball mill the ore is crushed before it enters the mill, whereas a SAG mill receives runofmine (ROM) ore directly (Stanley, 1987) A SAG mill in a singlestage closed circuit con guration, as shown in Fig 1, is considered for this study A descriptionAnalysis and validation of a runofmine ore grinding mill circuit 2023年7月20日 Therefore, the rod mill is mostly used for coarse grinding of the previous period of ball mill, or grinding of brittle materials and materials against overcrushing, such as tungsten and tin ore before gravity separation; and (3) autogenous mill – it refers to the materials which themselves are collided and ground mutually to be crushed when the grinding mill rotates, and Ore Grinding SpringerLink
.jpg)
Optimization and Experimental Study of Iron Ore Grinding
2024年9月26日 Energy savings and consumption reduction of ball mills are crucial for industrial production The grinding medium is an important component of a ball mill In theory, using higherdensity grinding media can yield better grinding results However, for materials with varying grindability, employing grinding media of different densities can reduce energy consumption grinding balls perform for longer hours, it is advisable to subject these types of ores to grinding balls, which can withstand the higher energy that the ores possess (Yusupov et al, cations: 2007) interaction between grinding media and mineral in Selection of Grinding Media for Use in the Gold Processing Table 1 Chemical composition of typical grinding media (% wt) Adapted from [24] 211 Cast Iron Cast iron can be grey cast iron or white cast iron, but white cast irons are commonly used in Grinding Media in Ball MillsA Review ResearchGate2016年11月7日 In Fig 13 is shown a large ball mill, designed for the dry grinding of limestone, dolomite, quartz, refractory and similar materials; this type of mill being made in a series of sizes having diameters ranging from about 26 in to 108 in, with the corresponding lengths of drum ranging from about 15 in to 55 inGrinding Mills Common Types 911Metallurgist
.jpg)
Grinding Mill Power 911Metallurgist
2017年5月8日 Grinding Mill Power ScaleUp Probably one of the most comprehensive experimental investigations of the power demands of the ball or tube mill is that carried out by one of the present authors, with a worker, Rose 2018年7月1日 A hybrid nonlinear model predictive controller (HNMPC) is developed for a runofmine ore grinding mill circuit A continuoustime grinding mill circuit model is presented with a hydrocyclone cluster as the primary classifier The discretetime component is the switching of hydrocyclones in the hydrocyclone clusterHybrid nonlinear model predictive control of a runofmine ore Speed also plays a role in ore grinding; too high of a speed can cause damage to the mill gears and other components, while too low of a speed can cause excessive wear on these same components It is important to find a balance between these two variables in order to achieve optimal grinding performanceFactors affecting ores grinding performance in ball millsDrivers of grinding energy transfer to ore in ball mills • Charge density –charge shape and liner design • Charge surface area • Pulp density rheology • Media mass • Classifier efficiency How can we increase the grinding surface area? 1 Increase the grinding surface • Smaller ball media, or • Different media shape 2Rethinking Grinding Efficiency in Ball Mills
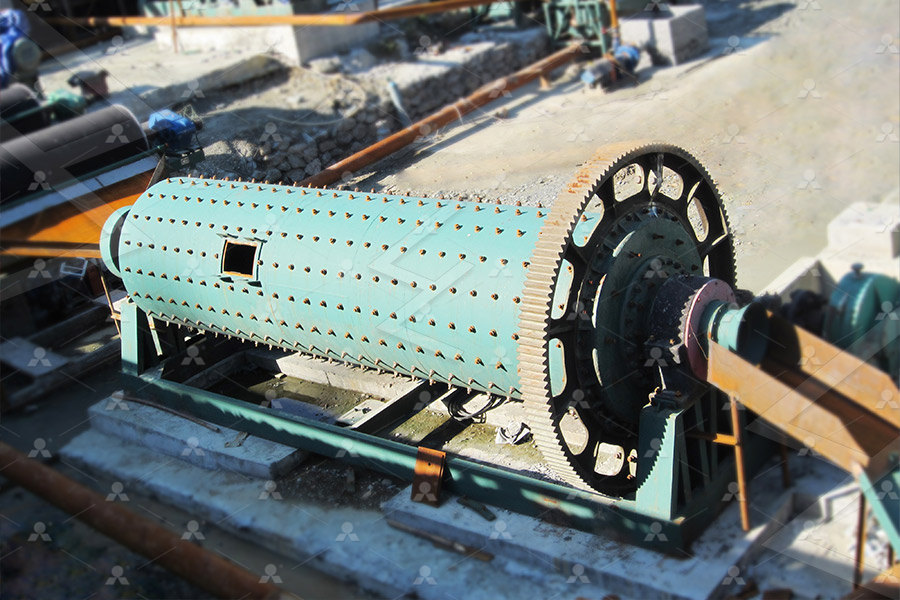
OneMine How to Use Hard Ore Components as Grinding Media
2012年10月29日 How to use hard ore components as grinding media, in Proceedings 11th AusIMM Mill OperatorsÆ Conference, pp 3136 (The Australasian Institute of Mining and Metallurgy: Melbourne) The commonly used SAB, SABC and runofmine (ROM) ball mill circuits can achieve high throughputs with good operating stabilityThis study investigates the use of kinetic model to predict the particle size of ore grinding process A new modeling framework is proposed where a discretized macroscale model and a mesoscale kinetic model are combined to predict the grinding product particle size The key idea is to divide the mill into several connected virtual submills, and each submill is simulated using kinetic A Mesoscale Endpoint Predictive Model of Ore Grinding Particle 2007年7月1日 Adjustment to ball size could lead to significant improvement in grinding mill throughput (McIvor, 1997)The Bond’s equation for ball sizing (McIvor, 1997) can help in selecting the ball size for a given ore and grinding millBall mill simulations with ball wear modelling can also be used to identify the optimum ball size (Concha et al, 1992) for a given applicationShould the slurry density in a grinding mill be adjusted as a 2012年10月30日 The ballmill data were analyzed by means of the orespecific breakage distribution function determined from pendulum tests and a multisegment ballmill model, enabling a scaleup relationship to How to Use Hard Ore Components as Grinding Media
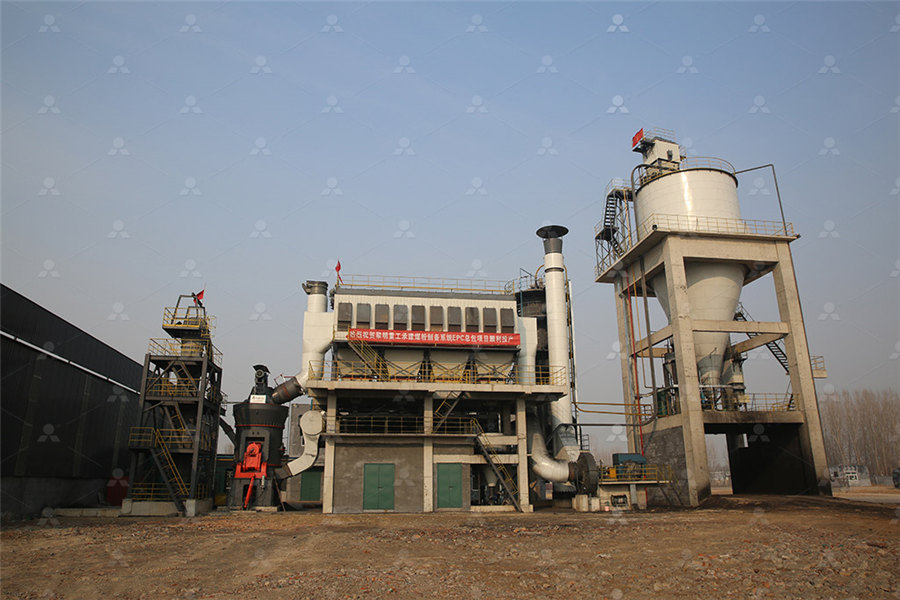
Consumption of steel grinding media in mills – A review
2013年8月1日 Wet grinding was beneficial for the energy efficiency for both ores and promoted the selectivity of flotation particularly with sulphidic ore The wear of the mill and grinding media seemed more 2016年1月1日 In wet grinding practice, highstress abrasion occurs over a small region when ore particles are trapped between the grinding balls and the mill liner, and the load is sufficient to fracture A comparison of wear rates of ball mill grinding media2018年7月1日 The mill is the most power intensive element in a grinding mill circuit and the power draw of the mill motor is represented by P mill (Matthews and Craig, 2013) The slurry mixture of ground ore and water in the mill is discharged into the sump through an enddischarge screen that limits the particle size of the discharged slurryHybrid nonlinear model predictive control of a runofmine ore 2013年8月1日 Apart from these cost factors, one of the major unsolved problems in the optimal design of ball mills concerns the equilibrium media size distribution in the mill, which is determined by the rate at which makeup media is added to the mill, as well as the rate at which these grinding media are consumed (Austin and Klimpel, 1985)Reliable prediction of grinding media Consumption of steel grinding media in mills – A review
.jpg)
Research of iron ore grinding in a verticalrollermill
2015年3月15日 For the grinding tests, a Loesche mill LM45 (table diameter 045 m) is used (Fig 2a) This pilot scale mill is a special development for ore grinding, which is reflected by several features The mill has four rollers, which are able to stress the particle bed with grinding pressures of up to 5000 kN/m 22016年7月8日 The Work Index values listed in Table I and II apply directly to a wet grinding overflow type rod mill 75 feet in diameter in open circuit; and to a wet grinding overflow type ball mill 75 feet in diameter in closed circuit with a rake classifier at 250% circulating load, and with 80% or more of the feed passing 4 meshEquipment Sizing: Crusher or Grinding Mill 911MetallurgistThe fraction of the mill volume lled with water, ore and steel balls is represented by J T The mill is the most power intensive element in a grinding mill circuit and the power draw of the mill motor is represented by P mill [4] The slurry mixture of ground ore and water in the mill is discharged into the sump through an enddischargeHybrid nonlinear model predictive control of a runofmine ore Grinding Mills: Ball Mill Rod Mill Design PartsCommon types of grinding mills include Ball Mills and Rod Mills This includes all rotating mills with heavy grinding media loads This article focuses on ball and rod mills excluding SAG and AG mills Although their concepts are very similar, they are not discussed herePhotographs of a glass ended laboratory ball mill show Grinding Mills 911Metallurgist
.jpg)
Grinding Mill an overview ScienceDirect Topics
A crushing plant delivered ore to a wet grinding mill for further size reduction The size of crushed ore (F 80) was 40 mm and the SG 28 t/m 3 The work index of the ore was determined as 122 kWh/t A wet ball mill 1 m × 1 m was chosen to grind the ore down to 200 micronsSpecific grinding rate of Ball mill = coarse particles (in the plant ball mill) grinding efficiency Ore grindability (in the lab ball mill) The units of "ball mill grinding efficiency" will be covered in detail in the first part of the module Alternatively, we can say that: Specific grinding rate = Ball mill x MODULE #5: FUNCTIONAL PERFOMANCE OF BALL MILLINGthe mill speed allowing improved control of the product particle size (Viklund et al, 2006) The mill motor power draw serves as an indication of the energy required to lift the mill charge The ground ore in the mill mixes with the water to form a slurry and Throughput and product quality control for a grinding mill circuit 2018年8月8日 One of the most effective methods of grinding Portland cement is the use of an electromagnetic mill, which has proven its advantage in creating clinkerless binders [2], regulating the kinetics of (PDF) Grinding Kinetics Adjustment of Copper Ore Grinding in
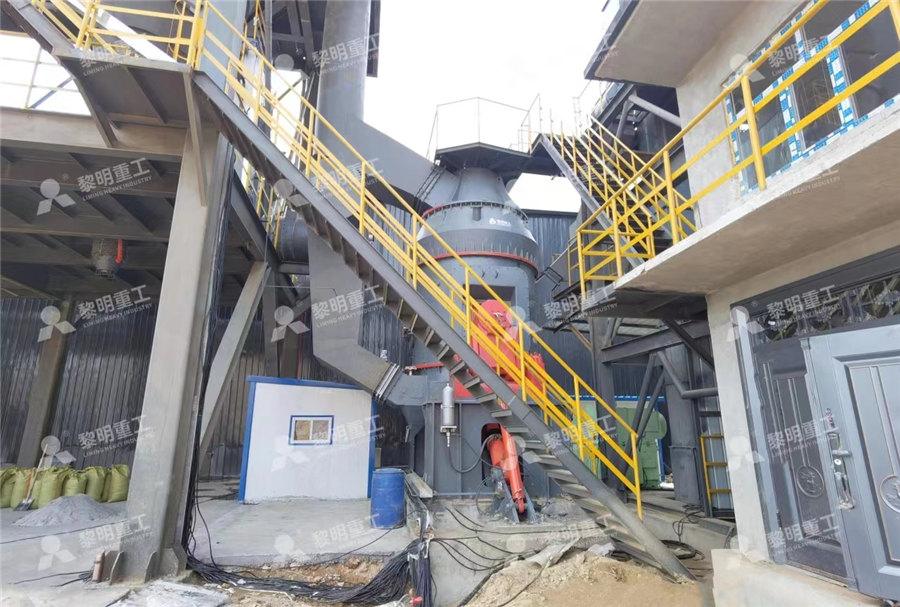
Analysis and validation of a runofmine ore grinding mill circuit
2013年4月1日 A simple and novel nonlinear model of a runofmine ore grinding mill circuit, developed for process control and estimation purposes, is validatedIn the mill, the mixture of medium, ore, and water, known as the mill charge, is intimately mixed, the medium comminuting the particles by any of the above methods Apart from laboratory testing, grinding in mineral processing is a continuous process, material being fed at a controlled rate into one end of the mill and discharging at the other end after a suitable dwell (residence) timeGrinding Mill an overview ScienceDirect TopicsUFG mills overcome these limitations by the use of rotating stirrers inside a stationary mill shell Ultra fine grinding mills have been in use for many years in a large number of every day applications such as pharmaceuticals, dyes, clays, paint and pigments before being used in the mineral processing industryUltra Fine Grinding A Practical Alternative to Oxidative 2015年8月6日 There are basically two groups of Grinding Mill Liners Ones with a HIGH PROFILE and those with a LOW PROFILE The high profile liner is designed to give the The amount of unground material will slowly increase until the mill can no longer grind the bigger oreGrinding Mill Liners 911Metallurgist

Analysis and validation of a runofmine ore grinding mill circuit
which use both ore and steel balls as grinding media (Wei and Craig, 2009b) In the case of a ball mill the ore is crushed before it enters the mill, whereas a SAG mill receives runofmine (ROM) ore directly (Stanley, 1987) A SAG mill in a singlestage closed circuit con guration, as shown in Fig 1, is considered for this study A description2023年7月20日 Therefore, the rod mill is mostly used for coarse grinding of the previous period of ball mill, or grinding of brittle materials and materials against overcrushing, such as tungsten and tin ore before gravity separation; and (3) autogenous mill – it refers to the materials which themselves are collided and ground mutually to be crushed when the grinding mill rotates, and Ore Grinding SpringerLink2024年9月26日 Energy savings and consumption reduction of ball mills are crucial for industrial production The grinding medium is an important component of a ball mill In theory, using higherdensity grinding media can yield better grinding results However, for materials with varying grindability, employing grinding media of different densities can reduce energy consumption Optimization and Experimental Study of Iron Ore Grinding grinding balls perform for longer hours, it is advisable to subject these types of ores to grinding balls, which can withstand the higher energy that the ores possess (Yusupov et al, cations: 2007) interaction between grinding media and mineral in Selection of Grinding Media for Use in the Gold Processing
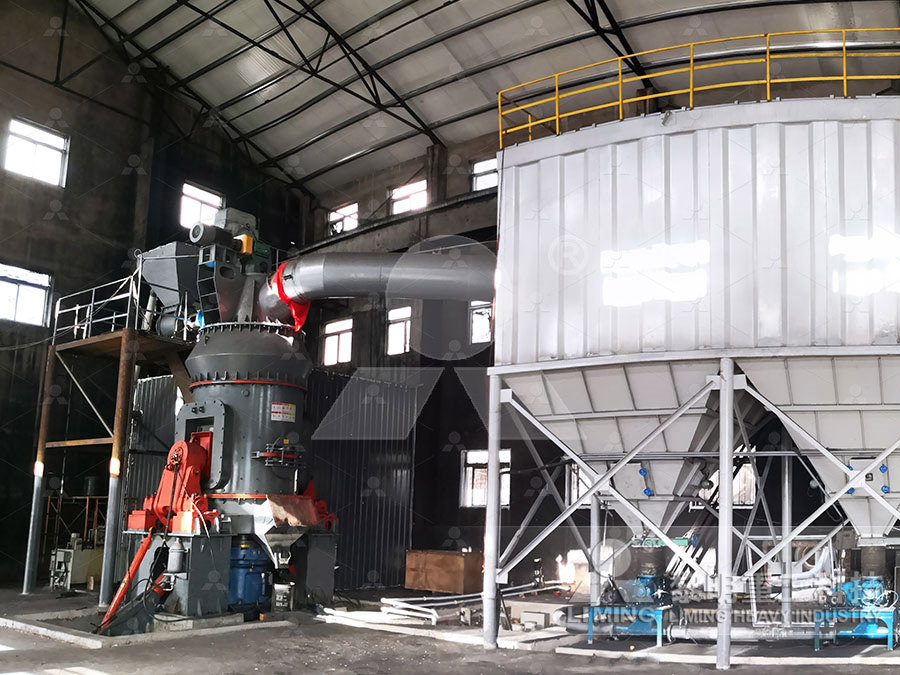
Grinding Media in Ball MillsA Review ResearchGate
Table 1 Chemical composition of typical grinding media (% wt) Adapted from [24] 211 Cast Iron Cast iron can be grey cast iron or white cast iron, but white cast irons are commonly used in 2016年11月7日 In Fig 13 is shown a large ball mill, designed for the dry grinding of limestone, dolomite, quartz, refractory and similar materials; this type of mill being made in a series of sizes having diameters ranging from about 26 in to 108 in, with the corresponding lengths of drum ranging from about 15 in to 55 inGrinding Mills Common Types 911Metallurgist