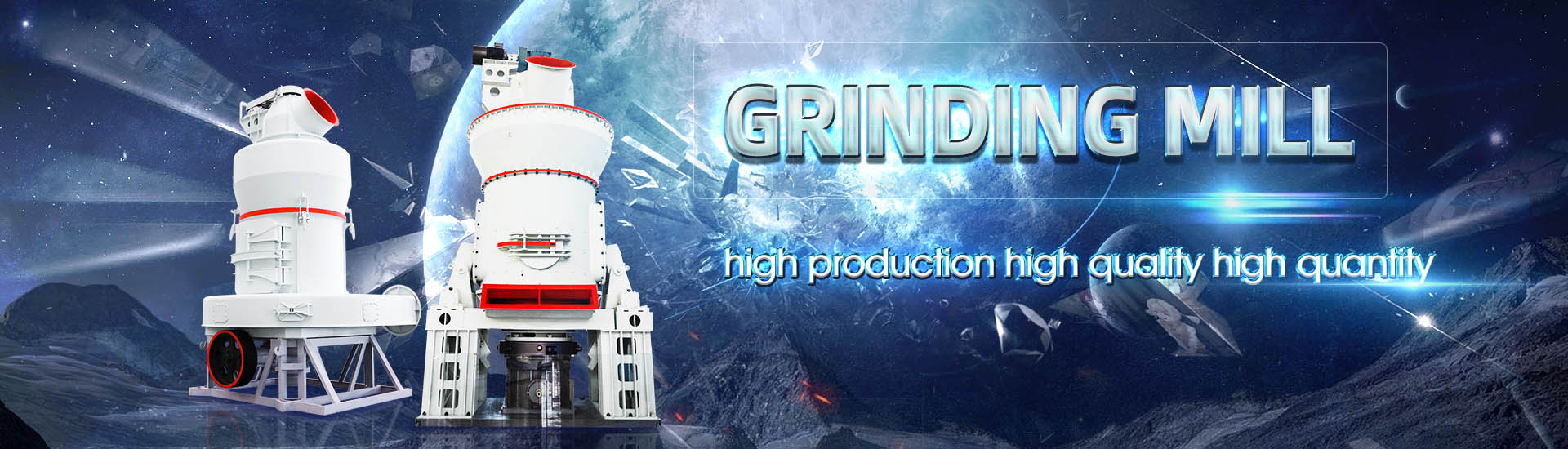
Production of pulverized coal
.jpg)
Pulverised Coal an overview ScienceDirect Topics
Pulverized coal (PC) combustion is presently the system of choice for coalfired powergenerating plants In PC combustion, the coal is dried and is ground to a specified fineness, with a maximum particle size of 250–300 μm, depending on the reactivity of the coalThis study proposed a twostage gasification (TSG) process of pulverized coal to allow for hTwostage gasification process simulation and optimization of Pulverized coal combustion (PCC) is the most widely used technology for coal power generation In this process, coal is milled, pulverized, and injected in the boiler with air to allow Pulverised Coal Combustion an overview ScienceDirect Topics2024年1月2日 This study proposed a twostage gasification (TSG) process of pulverized coal to allow for hydrogenrich (HR) production The balance flow of this process is constructed using Twostage gasification process simulation and optimization of

Fundamentals of pulverised coal combustion ICSC
Combustion of coal in pulverised form has been developed over several decades, with continuous improvements in design and performance It is most commonly used in either large scale utility 2019年2月1日 The aim of present paper is to review various aspects of pulverized coal combustion such as oxy‐fuel combustion, co‐combustion of coal and biomass, emissions from (PDF) A complete review based on various aspects of pulverized Pulverised coal firing has been the dominant technology for generating power in utility boilers for almost a century During this period, boiler designs have evolved through an accumulating Understanding pulverised coal, biomass and waste combustion2019年2月14日 The aim of present paper is to review various aspects of pulverized coal combustion such as oxyfuel combustion, cocombustion of coal and biomass, emissions from A complete review based on various aspects of pulverized coal
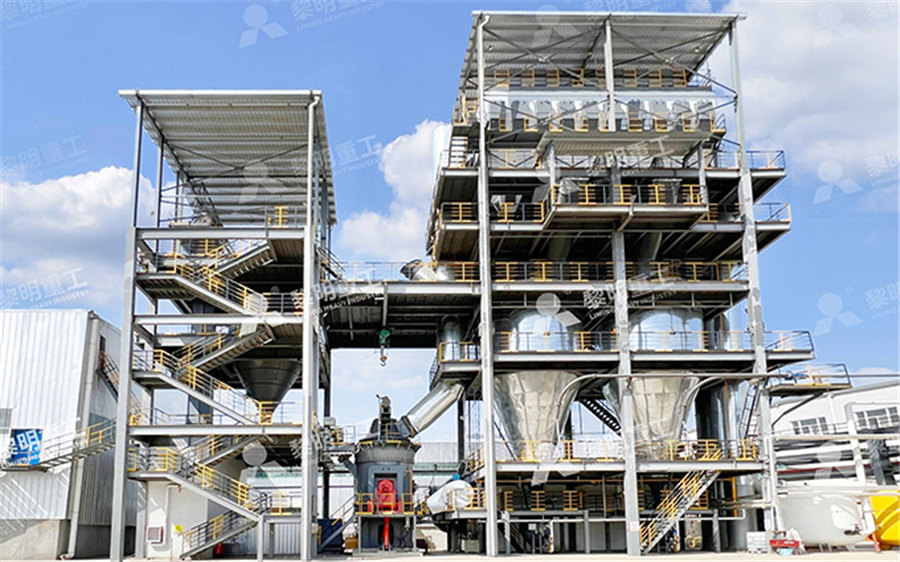
How is pulverized coal processed? SBM Ultrafine
2022年2月24日 The production of clean pulverized coal is used for boiler combustion heating and power supply to improve the operating efficiency of small and mediumsized coalfired boilers to 80%, while reducing harmful gas and IHI is accelerating studies such as “building carbonfree energy networks using ammonia as fuel” in the mission of reducing greenhouse gas emissions We have been researched and Development of CoFiring Method of Pulverized Coal and For a higher efficiency of the technology supercritical and ultrasupercritical coalfired technologies have been developed These technologies can combust pulverised coal and Pulverised Coal Combustion with higher efficiencyPulverized coal (PC) combustion is presently the system of choice for coalfired powergenerating plants In PC combustion, the coal is dried and is ground to a specified fineness, with a maximum particle size of 250–300 μm, depending on the reactivity of the coalPulverised Coal an overview ScienceDirect Topics

Simulation of Pulverized Coal Combustion in Blast Furnace Tuyere
2024年11月1日 The combustion of pulverized coal in tuyere and raceway directly affects the production efficiency of smelting Based on the design and production data of a 2000 m 3 blast furnace, a threedimensional mathematical model of2021年12月15日 However, ammonia production based on pulverized coal, the most common feedstock in China's ammonia industry, has not been analyzed Research on ammonia production in China has primarily focused on the hydrogenproduction stage in the upstream industrial chain of ammonia synthesisLife cycle assessment of ammonia synthesis based on pulverized coal 2024年10月1日 Pyrolysis and gasification were common methods for the multistage utilization of pulverized coal, generating two high application products of tar and syngas [2, 3], which were the raw materials of chemical productionThe coalbased polygeneration technology coupling with pyrolysis or gasification aimed to realize the multistage utilization of coal resources and An experimental investigation on gasificationpyrolysis coupling The injection of the pulverized coal into the BF results into (i) increase in the productivity of the BF, ie the amount of hot metal (HM) produced per day by the BF, (ii) reduce the consumption of the more expensive coking coals by replacing coke with cheaper soft coking or thermal coals, (iii) assist in maintaining furnace stability, (iv) improve the consistency of the quality of the HM and Understanding Blast Furnace Ironmaking with Pulverized Coal
.jpg)
A complete review based on various aspects of pulverized coal
2019年2月14日 Coal is the most abundant energy source, and around 40% of the world's electricity is produced by coal combustion The emission generated through it put a constraint on power production by coal combustion There is a need to reduce the emissions generated through it to utilize the enormous energy of coal for power production2024年11月1日 The combustion of pulverized coal in tuyere and raceway directly affects the production efficiency of smelting Based on the design and production data of a 2000 m 3 blast furnace, a threedimensional mathematical model ofSimulation of Pulverized Coal Combustion in Blast Furnace Tuyere2015年1月5日 During the last hundred years, pulverised coal combustion has been widely applied for electricity generation [1] More recent, deregulation of the European power sector [1], low coal prices and a Understanding pulverised coal, biomass and waste combustion – 2019年2月14日 Coal is the most abundant energy source, and around 40% of the world's electricity is produced by coal combustion The emission generated through it put a constraint on power production by coal combustion There is a need to reduce the emissions generated through it to utilize the enormous energy of coal for power productionA complete review based on various aspects of pulverized coal
.jpg)
Improving Particle‐Burning Efficiency of Pulverized Coal in New
2024年12月4日 1 Introduction Coal holds a prominent position in the energy landscape and climate discussions because it serves as the primary energy source for worldwide power generation, steel and cement production, while also being a major contributor to carbon dioxide (CO 2) emissionsThere have been numerous studies on coal particle combustion addressing 161 Pulverized coal combustion In pulverized coal combustion (PCC), dust burners are used to feed coal into the combustion chamber, where flame core zones of the combustion chamber having a temperature range between 1450°C and 1600°C are present To attain the required efficiency, pulverized coal is given a swirling motion around the flame Pulverised Coal Combustion an overview ScienceDirect Topics2024年10月16日 This study proposes a feasible gasificationcombustion technology for coalfired boilers operating at low loads for the purpose of providing strong support for stable output of the power grid system that accommodates more renewable energy power In this technology, a multinozzle impinging entrainedflow gasifier is used for the first time to preheat pulverized Nitrogen migration and gasification characteristics of pulverized coal Download Citation On Aug 1, 2023, Binxuan Zhou and others published Twostage gasification process simulation and optimization of pulverized coal for hydrogenrich production using Aspen plus Twostage gasification process simulation and optimization of
.jpg)
Toward Carbon Emission Reduction in Steel Production by
2024年3月22日 On average, the production cost of biochar is estimated at $200 to $400 per ton, with energy consumption ranging from 1000 to 1500 kWh per ton In contrast, the production processes of pulverized coal and coke are usually more complex, requiring significantenergy and equipment inputs The production cost of pulverized coal and coke can range2015年4月20日 Coal fines can block fractures in coal reservoirs, leading to the nonrecoverable decrease of coal permeability Therefore, coal fines can directly affect the gas production of CBM wells ( Cao et Analysis of pulverized coal migration during CBM productionproduction, transportation, and storage infrastructure, and IHI is developing technologies for the use of ammonia in gas turbines, pulverized coalfired boilers, and solid oxide fuel cells(2) This paper reports on the development of technology to cofire ammonia and pulverized coal aimed at reducing CO 2 emissions from coalfired power plantsDevelopment of CoFiring Method of Pulverized Coal and 2012年1月1日 To evaluate the potential of pulverized coals partially replaced by rice husks used in blast furnaces, thermal behavior of blends of rice husks and an anthracite coal before and after passing The production of stalk char as pulverized coal injection of blast
.jpg)
Pulverized Coal Injection of Blast Furnace Ironmaking
2023年6月15日 The characteristics of pulverized coal injection of blast furnace ironmaking include basic performance (ash, sulfur, and fixed carbon) and process performance (ignition point, explosibility, grindability, ash fusion temperature, combustibility, and reactivity), which is an important basis for the selection of coal types for pulverized coal injection of blast furnace DOI: 101016/JFUPROC201703012 Corpus ID: ; Deposit formation mechanisms in a pulverized coal fired grate for hematite pellet production @article{Guo2017DepositFM, title={Deposit formation mechanisms in a pulverized coal fired grate for hematite pellet production}, author={YuFeng Guo and Shuai Wang and Yu He and Tao Jiang and Feng Chen Deposit formation mechanisms in a pulverized coal fired grate for 2024年11月1日 Pulverized coal injection (PCI) is a technology that can reduce both production costs and carbon emissions by injecting pulverized coal into the blast furnace (BF) through the tuyere and mixing and combusting with hot blast at about 1200 °C in the raceway, utilizing cheap pulverized coal to partially replace the use of expensive metallurgical coke [1], [2], [3]Theoretical and experimental investigation on the effect of transferrable to other coals, even those that closely resemble the original fuel Morrison’s principal conclusions from his study were as follows: 211 Coal structure Our lack of understanding of the molecular structure of coal is impeding progress in coal combustion researchUnderstanding pulverised coal, biomass and waste combustion
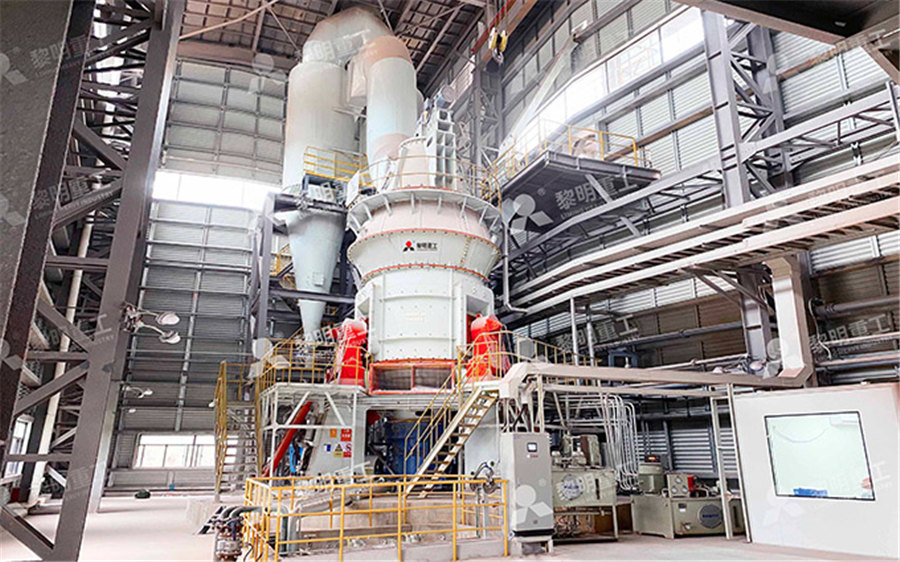
Improvement of the efficiency of blast furnace smelting
2024年10月28日 Based on the theory of full and complex compensation, taking into account the charge and technological conditions, the article presents calculations of promising modes of blast furnace smelting with injection of pulverized coal fuel 2013年5月10日 Fig 3 Schematic of pulverized coal injection at the tuyere and the raceway BF operation and PCI This index is being used in some plants to determine the operating strategy of the BFs, if Iglobalcoke is low the coal Pulverized Coal Injection in a Blast Furnace – 2023年12月15日 The pulverized coal and Al 2 O 3 powder used in the experiment were uniformly mixed at a ratio of 1:10 to ensure that the pulverized coal is uniformly heated and the residue after burning was not adhered to the corundum crucible surface This leads to a higher NO production than that in pure pulverized coal combustionInfluences of ammonia cofiring on the NO generation Steel Production: In the steel industry, pulverized coal injection (PCI) is used in blast furnaces to reduce coke consumption and enhance furnace efficiency Cement Production: Pulverized coal is used as a fuel in rotary kilns for cement production, contributing to the clinker formation process Benefits of Pulverized Coal The use of Understanding Pulverized Coal: Benefits, Risks, and Safety
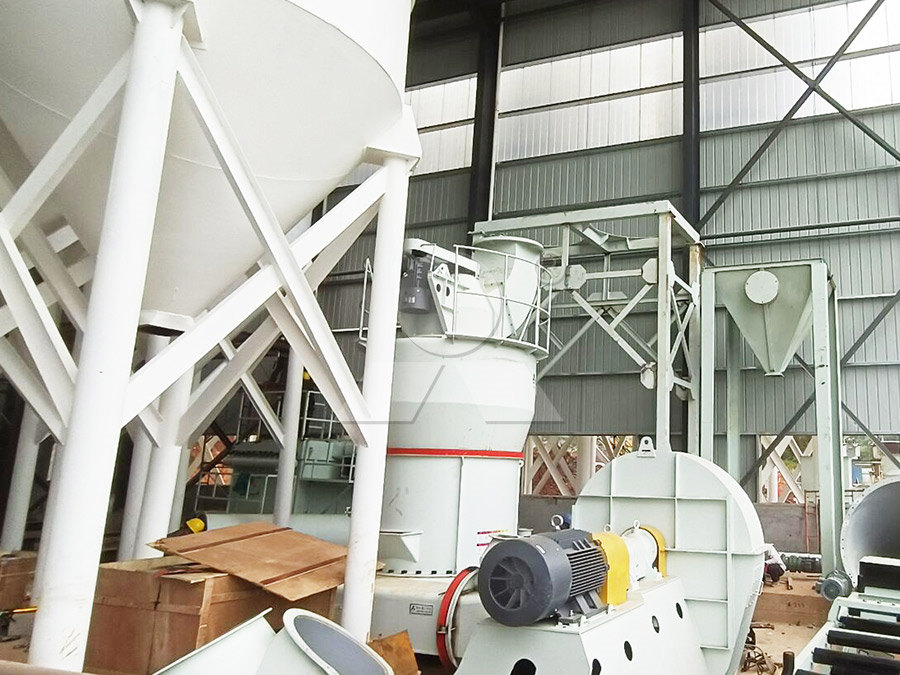
Novel coaltomethanol process with nearzero carbon emission
2022年3月10日 For coalbased methanol production, coal is intermingled with O 2 of AS and subsequently subjected to CG for producing crude syngas The cryogenic separation technology is primarily used in the AS for oxygen production, which is a high energy consumption process (Xiang et al, 2014)Because of the small hydrogentocarbon (H/C) ratio in coal, WGS process Download scientific diagram Schematic diagram of pulverized coal production and blocking flow pathways from publication: A new coal reservoir permeability model considering the influence of Schematic diagram of pulverized coal production and blocking 2018年2月21日 4 WHATIS PCI ? Pulverized Coal Injection (PCI) is a process that involves injecting large volumes of fine coal particles into the raceway of a blast furnace (BF) What it does in BF : Reduces the need of metallurgical coke for reactions in the blast furnace Supplemental source of carbon Speeds up the production of liquid ironPulverized coal injection PPT SlideShare2019年2月1日 Coal is the most abundant energy source, and around 40% of the world's electricity is produced by coal combustion The emission generated through it put a constraint on power production by coal (PDF) A complete review based on various aspects of pulverized coal
.jpg)
Migration models of pulverized coal flowing with fluid and its
2018年3月1日 Download Citation Migration models of pulverized coal flowing with fluid and its production in CBM channels for the coal reservoirs The mathematical models of fluid mechanism in porous medium Pulverized coal (PC) combustion is presently the system of choice for coalfired powergenerating plants In PC combustion, the coal is dried and is ground to a specified fineness, with a maximum particle size of 250–300 μm, depending on the reactivity of the coalPulverised Coal an overview ScienceDirect Topics2024年11月1日 The combustion of pulverized coal in tuyere and raceway directly affects the production efficiency of smelting Based on the design and production data of a 2000 m 3 blast furnace, a threedimensional mathematical model ofSimulation of Pulverized Coal Combustion in Blast Furnace Tuyere2021年12月15日 However, ammonia production based on pulverized coal, the most common feedstock in China's ammonia industry, has not been analyzed Research on ammonia production in China has primarily focused on the hydrogenproduction stage in the upstream industrial chain of ammonia synthesisLife cycle assessment of ammonia synthesis based on pulverized coal
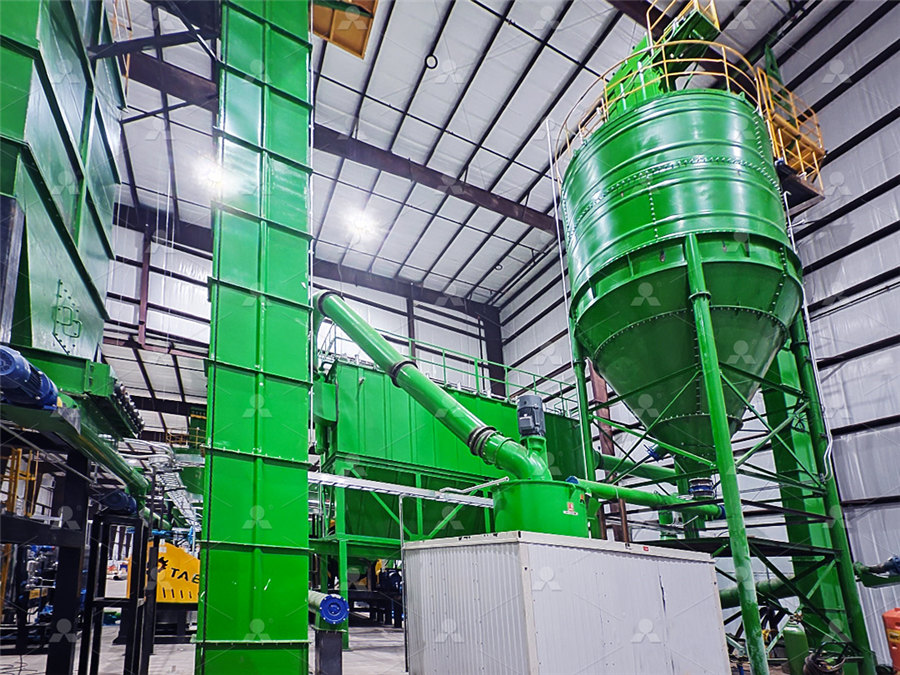
An experimental investigation on gasificationpyrolysis coupling
2024年10月1日 Pyrolysis and gasification were common methods for the multistage utilization of pulverized coal, generating two high application products of tar and syngas [2, 3], which were the raw materials of chemical productionThe coalbased polygeneration technology coupling with pyrolysis or gasification aimed to realize the multistage utilization of coal resources and The injection of the pulverized coal into the BF results into (i) increase in the productivity of the BF, ie the amount of hot metal (HM) produced per day by the BF, (ii) reduce the consumption of the more expensive coking coals by replacing coke with cheaper soft coking or thermal coals, (iii) assist in maintaining furnace stability, (iv) improve the consistency of the quality of the HM and Understanding Blast Furnace Ironmaking with Pulverized Coal 2019年2月14日 Coal is the most abundant energy source, and around 40% of the world's electricity is produced by coal combustion The emission generated through it put a constraint on power production by coal combustion There is a need to reduce the emissions generated through it to utilize the enormous energy of coal for power productionA complete review based on various aspects of pulverized coal 2024年11月1日 The combustion of pulverized coal in tuyere and raceway directly affects the production efficiency of smelting Based on the design and production data of a 2000 m 3 blast furnace, a threedimensional mathematical model ofSimulation of Pulverized Coal Combustion in Blast Furnace Tuyere
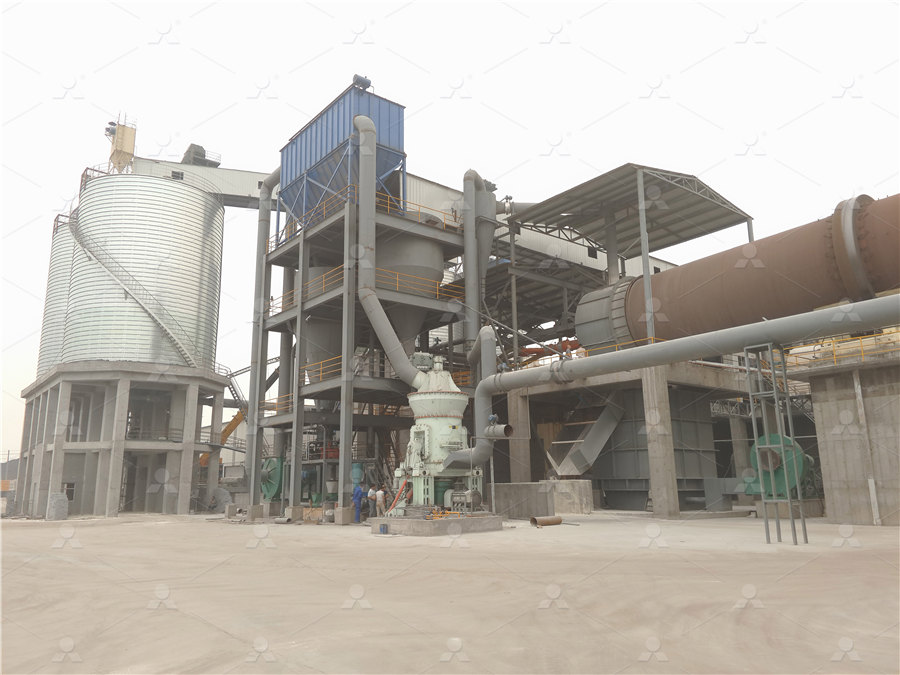
Understanding pulverised coal, biomass and waste combustion –
2015年1月5日 During the last hundred years, pulverised coal combustion has been widely applied for electricity generation [1] More recent, deregulation of the European power sector [1], low coal prices and a 2019年2月14日 Coal is the most abundant energy source, and around 40% of the world's electricity is produced by coal combustion The emission generated through it put a constraint on power production by coal combustion There is a need to reduce the emissions generated through it to utilize the enormous energy of coal for power productionA complete review based on various aspects of pulverized coal 2024年12月4日 1 Introduction Coal holds a prominent position in the energy landscape and climate discussions because it serves as the primary energy source for worldwide power generation, steel and cement production, while also being a major contributor to carbon dioxide (CO 2) emissionsThere have been numerous studies on coal particle combustion addressing Improving Particle‐Burning Efficiency of Pulverized Coal in New