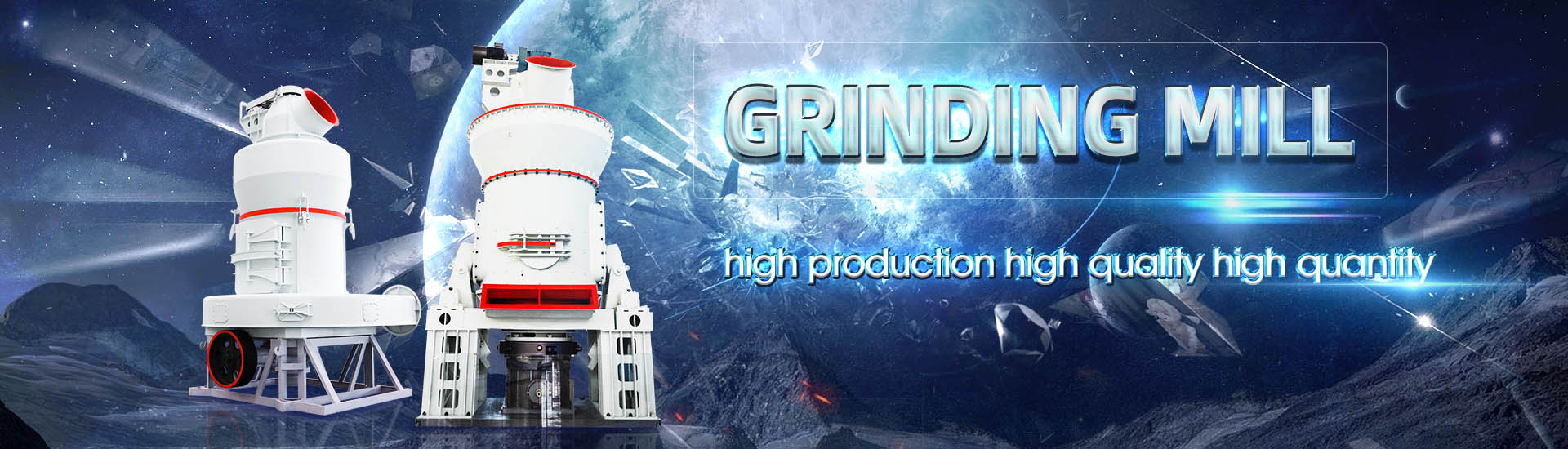
Quick lime nickel cobalt ore slag powder making process
.jpg)
Hydrometallurgical nickel and cobalt plants and processes
offer technology and equipment for the entire nickel and cobalt production chain from mine to metal, with a project scope ranging from equipment packages to turnkey plant delivery We have several processing alternatives for nickel and cobalt raw materials, ranging from It has been the first to launch a large vertical roller mill, LM series vertical roller mill, suitable for quicklime grinding processing This equipment integrates crushing, drying, grinding, and Large scale equipment for quick lime powder production2019年3月11日 Ravensthorpe Nickel /Cobalt Project proposed flow sheet CONCLUSIONS The solvent extraction of nickel and cobalt from laterite leach solutions and recent development of (PDF) Hydrometallurgical Processing of Nickel Laterites—A Brief 2020年7月22日 This review covers past technologies for hydrometallurgical processing of nickel and cobalt (Caron), current technologies (highpressure acid leaching, atmospheric leaching, Review of the past, present, and future of the hydrometallurgical
.jpg)
(PDF) Establishment of a Hydrometallurgical Scheme for
2023年7月3日 The present study focuses on the process development of slag to recover cobalt, nickel, copper, and iron using hydrometallurgical methods The slag sample utilized in this study2024年9月1日 HPAL is the main hydrometallurgical process for treating nickel laterite ores It has a fast reaction efficiency and is suitable for limonitic laterites HPAL can precipitate iron Hydrometallurgical process and recovery of valuable elements for 2014年1月1日 Nickel and cobalt are produced from laterite and sulfide ores Cobalt is also made from Central African Cu–Co ores and cobalt arsenide ores from Morocco The processes and Nickel and Cobalt Production ScienceDirect2021年12月4日 In this paper, the recovery of REEs from aluminosilicate ores, and nickel and cobalt from laterite ores is described Atmospheric pressure leaching of ores in lixiviant con Hydrometallurgical Processes for the Recovery of Rare Earths,
.jpg)
Review on hydrometallurgical processing technology of lateritic
Current technological schemes for the production of nickel and cobalt using combined manufacturing processes are presented, as well as the results of scientific research on 2004年1月1日 Using an organic phase composed of 07 M NEHPCA, 035 M DNNSA, and 02 M TBP under 1:1 O/A operation, after threestage theoretical extraction, more than 99% of nickel and cobalt can be recovered Cobaltnickel separation in hydrometallurgy: a reviewPDF On Mar 11, 2019, Sait Kursunoglu and others published Hydrometallurgical Processing of Nickel Laterites—A Brief Overview On The Use of Solvent Extraction and Nickel/Cobalt Project For The (PDF) Hydrometallurgical Processing of Nickel In the process of coagulation, alum and ferric chloride are used to lower the pH Lime is used to counteract the pH level and allow efficient nitrogen removal − Industrial Wastewater Lime is used by neutralizing sulfuric acid in steel plants where the iron salts are precipitated Lime also neutralizes and precipitates chrome, copper, and heavyQUICK LIME AND BYPRODUCTS PEC Consulting Group
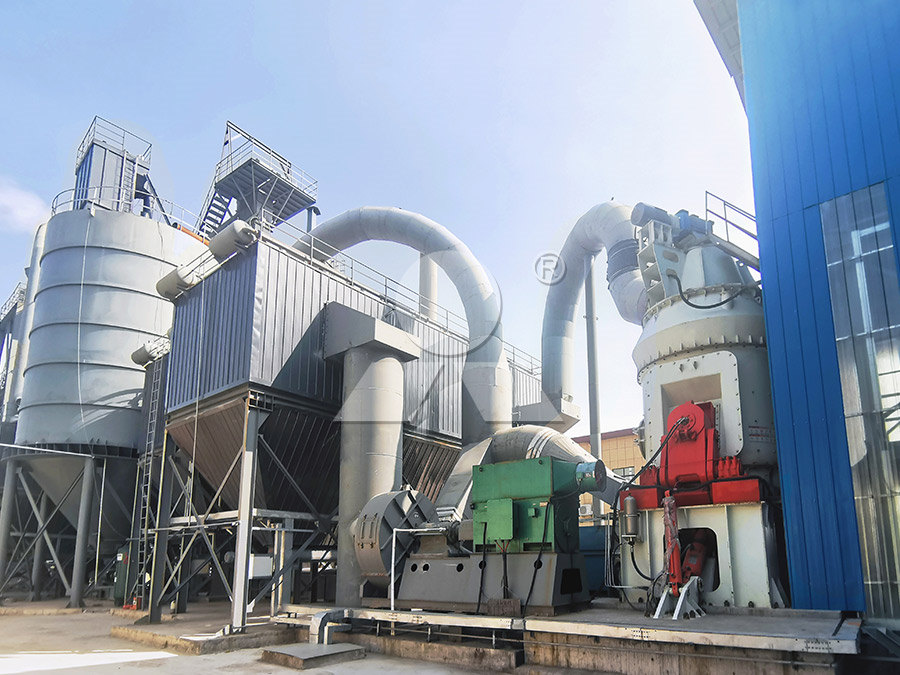
Separation of cobalt from slag of nickel pig iron using solvent
Park, K H, and Mohapatra, D (2006) 'Process for cobalt separation and recovery in the presence of nickel from sulfate solutions by Cyanex 272’, Metals and Materials 444 Ulin Herlina, Sudibyo, E Prasetyo, Donny Lesmana, dan Syafira Eka Gestya Pengaruh Ph, Waktu, Nisbah Volume Organik Dan Aqueous (O/A) Terhadap Proses Pemisahan Kobalt Dari Slag Nickel Pig Formation of slag: calcium oxide is used in slag formation which, among other things, accumulates the waste materials that are produced in the steel making process Moreover, it protects the metal from the elements in the atmosphere, such as nitrogen and hydrogen, it is also an insulator allowing the high temperatures reached in the process to be maintained (1,600 Lime, an essential component in the steel industry2024年7月10日 The rapid development of lithiumion batteries has led to a shortage of cobalt and nickel resources Recycling of nickel and cobalt slag can promote sustainable development and environmental protection In this study, a reductive ammonia leaching method is proposed for the recovery of Ni and Co from nickel and cobalt slag (NCS) with high Ni and Co contents The An Ammonia Leaching Process for the Recovery of Value Metals 2023年1月17日 Once the ore has been processed at the plant, it moves on to the refining stage, where it will become usable cobalt products The two primary refining processes used are hydrometallurgy and pyrometallurgy Hydrometallurgy involves treating the ore with certain chemicals to extract elemental cobalt, while pyrometallurgy is melting down the ore How Cobalt is Processed and Refined – A Complete Guide
.jpg)
Extraction of nickel and cobalt from a laterite ore using the
2019年8月1日 Request PDF Extraction of nickel and cobalt from a laterite ore using the carbothermic reduction roastingammoniacal leaching process The carbothermic reduction roasting followed by ammoniacal 2014年1月1日 Operational differences from nickel H 2 reduction are: (1) cobalt “seed” is made by precipitation from cobaltous diamine solution using sodium cyanide catalyst and sodium sulfide particle nucleation sites, (2) cobalt reduction is slightly faster than nickel reduction and the resulting cobalt particles are slightly larger and more irregular due to particle agglomeration, Nickel and Cobalt Production ScienceDirect2023年10月12日 The demand for nickel has been steadily increasing in the 21st century, primarily driven by the rising demand for electric vehicle batteries Nickel in laterite is associated within silicate in saprolite ore and hydroxide/oxide in limonite ore Recently, the sulfation–roasting–leaching process has been developed to address the challenges of Extraction Behavior of Nickel and Cobalt From SerpentineRich Ore 2003年2月1日 Regarding the settling process in nickel/cobalt slag, Mitrašinović and Wolf [21] found that the most favorable temperature was 1300 • C, for one hour of settling time, considering the ratio Nickel, copper, and cobalt slag losses during converting
.jpg)
Review of the past, present, and future of the
2020年7月22日 This review covers past technologies for hydrometallurgical processing of nickel and cobalt (Caron), current technologies (highpressure acid leaching, atmospheric leaching, heap leaching 1 Introduction The basic oxygen steelmaking (BOS) process produced over 70% of the global crude steel in 2018, [] generating 100 to 150 kg of slag (“BOS slag”) for every tonne of crude steel produced BOS slag, a product of hot metal Basic Oxygen Steelmaking Slag: Formation, Reaction, 2021年2月27日 Request PDF Separation and Recovery of Cobalt and Nickel from End of Life Products Via Solvent Extraction Technique: A Review The significant development in advanced technologies such as Separation and Recovery of Cobalt and Nickel from End of Life 2024年3月15日 Increasing the amount of sulfuric acid or additives can improve leaching efficiency for Ni and Co Ribeiro (Ribeiro et al, 2022) increased the leaching efficiencies for Ni and Co to 81% and 92%, respectively, by adding 50 wt% H 2 SO 4In addition, the leaching efficiency for Ni markedly improved to 87% by increasing the mass ratio of Na 2 SO 4 with a Transformation mechanism and selective leaching of nickel and cobalt
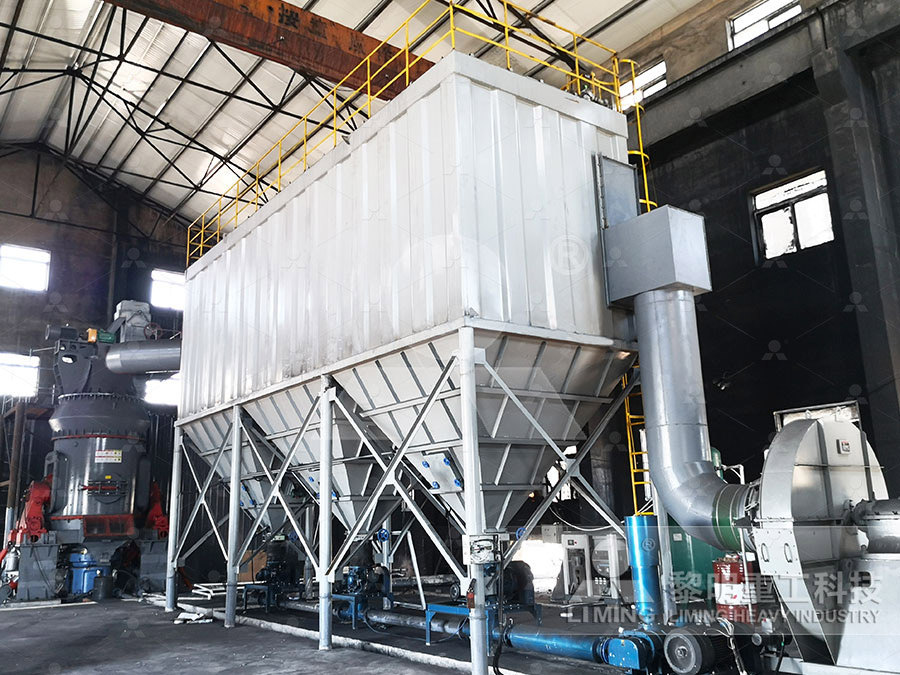
Magnetic separation for recovering iron resources from acid
2024年8月21日 Currently, nickel laterite ore is mainly treated by the wet acid leaching process, leading to the substantial generation of acidleaching tailings of laterite nickel ore during the process [4], [5] The management of the acidleaching tailings of laterite nickel ore significant challenge due to its substantial quantity and complex content, with an iron grade of 35–40 % 2011年9月1日 The reduction smelting process for cobalt recovery from converter slag of the Chambishi Copper Smelter in Zambia was studied The effects of reducing agent dosage, smelting temperature and time Recovery of cobalt from converter slag of Chambishi Copper 2023年1月19日 Nickel is an indispensable metal in hightech field It is mainly used as an alloying element for production of stainless steel, hightemperature alloy steel, highperformance special alloy, and nickelbased plating materials (Fig 11) []Nickel can alloy readily with many other metals, including chromium, iron, copper, and cobaltAn Overview of Nickel Utilization from Laterite Ore2017年5月1日 The extraction and stripping of Cu and Ni ions from synthetic and industrial solutions of Sarcheshmeh Copper Mine containing Cu (770 mg/L), Ni (3200 mg/L), Fe (800 mg/L) and Zn (200 mg/L) were Solvent Extraction Process for the Recovery of Nickel and Cobalt
.jpg)
A novel process for cobalt and copper recovery from cobalt
2020年1月1日 In the present study, the extraction of copper, nickel, and cobalt from copper slag was investigated through the process of sulfation roasting–water leaching and the process of sulfation 2021年5月1日 Slag from the manufacturing of nickel pig iron (NPI) from laterite soil was still containing 82370 ppm of cobalt In this research, the separation process was carried out from slag NPI by using Optimization of Electrometal Electrowinning Cobalt 2023年12月8日 1 Introduction Southwest China has several nickel and cobalt production bases that greatly contribute to local industrial development and regional economic construction [1]However, mineral processing also causes serious environmental pollution, of which the most alarming is the pollution caused by nickel–cobalt tailings (NCT) [2]NCT is the waste slag Preparation of nickel–cobalt tailingsbased cementing materials Nickel and Cobalt Production Michael S Moats, William G Davenport, in Treatise on Process Metallurgy: Industrial Processes, 2014 226 Cobalt from Central African Copper–Cobalt Ores While most cobalt (~ 50%) is produced as a coproduct from the processing of nickel/ cobalt ores, a significant amount of cobalt (~ 35%) is produced from Central African copper–cobalt oresCobalt Ore an overview ScienceDirect Topics
.jpg)
Hydrometallurgical process for the separation and recovery of nickel
2009年11月1日 Mihaylov et al (2000) have developed a novel hydrometallurgical process for nickel and cobalt recovery from the Goro laterite ore Their study proposed the simultaneous extraction of 06 g/L Co and 6 g/L Ni from 3 g/L Mn and 10 g/L Mg sulphate solutions by 15% Cyanex 301, at an aqueous to organic phase ratio A:O = 252019年9月3日 nickel ore having nickel less than 17% to recommenc e [20] Together with the start of lowgrade ferro nickel production in Indonesia, many Indonesian studies examined this process(PDF) Nickel Laterite Smelting Processes and SomeRequest PDF On Jan 1, 2020, Sudibyo S published Optimization of ElectrometalElektrowinning Cobalt Process from the Slag of Nickel Pig Iron (NPI) Find, read and cite all the research you need Optimization of ElectrometalElektrowinning Cobalt Process from 2011年5月25日 Therfore, nickel extraction process of lateritic ore with high efficiency is investigated by using hydrometellurgy process, specifically the iron removal process in atmospheric condition in mixed Chemical aspects of mixed nickelcobalt hydroxide precipitation and
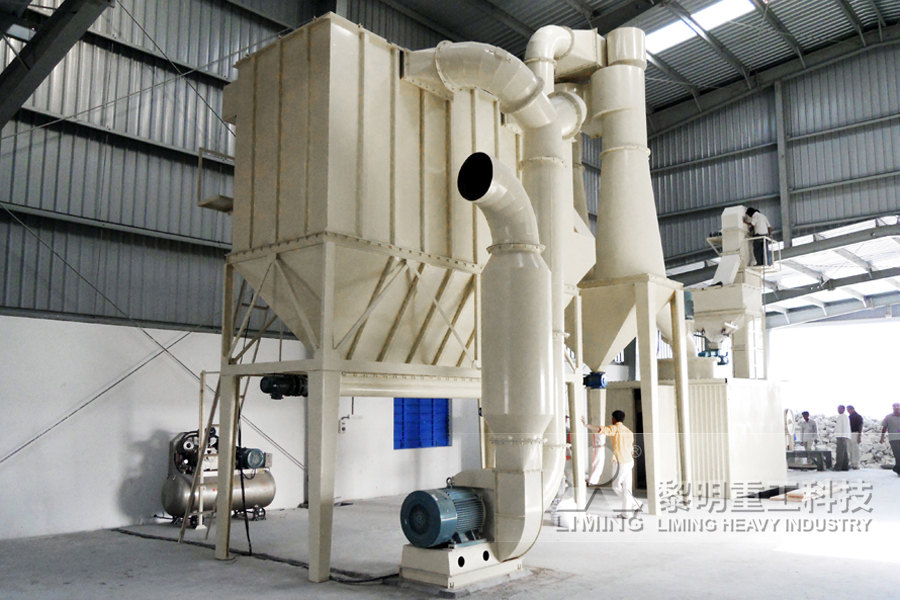
Separation of cobalt from slag of nickel pig iron using solvent
Park, K H, and Mohapatra, D (2006) 'Process for cobalt separation and recovery in the presence of nickel from sulfate solutions by Cyanex 272’, Metals and Materials 444 Ulin Herlina, Sudibyo, E Prasetyo, Donny Lesmana, dan Syafira Eka Gestya Pengaruh Ph, Waktu, Nisbah Volume Organik Dan Aqueous (O/A) Terhadap Proses Pemisahan Kobalt Dari Slag Nickel Pig 2022年12月1日 Nitric acid pressure leaching process (NAPL) uses nitric acid as the leaching medium to produce cobalt and nickel raw materials Based on the benefits of nitric acid pressure leaching process for laterite ore, this paper proposes a process of "nitric acid pressure leachingneutralization precipitationreductive ammonia leaching separation"Ammonia leaching process for selective extraction of nickel and cobalt 2020年2月1日 Nickel (Ni) and cobalt (Co) are amongst the critically rare metals due to their large industrial usage and vital application in rechargeable batteries [1], [2], [3]The laterite ores are accounted for 70% of Ni reserves worldwide but 60% of the global Ni production is still contributed by the sulfide ores [4], [5]Due to the depletion of Nicontaining sulfide ores, increasing Extraction of nickel and cobalt from a laterite ore using the 2004年1月1日 Using an organic phase composed of 07 M NEHPCA, 035 M DNNSA, and 02 M TBP under 1:1 O/A operation, after threestage theoretical extraction, more than 99% of nickel and cobalt can be recovered Cobaltnickel separation in hydrometallurgy: a review
.jpg)
(PDF) Hydrometallurgical Processing of Nickel
PDF On Mar 11, 2019, Sait Kursunoglu and others published Hydrometallurgical Processing of Nickel Laterites—A Brief Overview On The Use of Solvent Extraction and Nickel/Cobalt Project For The In the process of coagulation, alum and ferric chloride are used to lower the pH Lime is used to counteract the pH level and allow efficient nitrogen removal − Industrial Wastewater Lime is used by neutralizing sulfuric acid in steel plants where the iron salts are precipitated Lime also neutralizes and precipitates chrome, copper, and heavyQUICK LIME AND BYPRODUCTS PEC Consulting GroupPark, K H, and Mohapatra, D (2006) 'Process for cobalt separation and recovery in the presence of nickel from sulfate solutions by Cyanex 272’, Metals and Materials 444 Ulin Herlina, Sudibyo, E Prasetyo, Donny Lesmana, dan Syafira Eka Gestya Pengaruh Ph, Waktu, Nisbah Volume Organik Dan Aqueous (O/A) Terhadap Proses Pemisahan Kobalt Dari Slag Nickel Pig Separation of cobalt from slag of nickel pig iron using solvent Formation of slag: calcium oxide is used in slag formation which, among other things, accumulates the waste materials that are produced in the steel making process Moreover, it protects the metal from the elements in the atmosphere, such as nitrogen and hydrogen, it is also an insulator allowing the high temperatures reached in the process to be maintained (1,600 Lime, an essential component in the steel industry
.jpg)
An Ammonia Leaching Process for the Recovery of Value Metals
2024年7月10日 The rapid development of lithiumion batteries has led to a shortage of cobalt and nickel resources Recycling of nickel and cobalt slag can promote sustainable development and environmental protection In this study, a reductive ammonia leaching method is proposed for the recovery of Ni and Co from nickel and cobalt slag (NCS) with high Ni and Co contents The 2023年1月17日 Once the ore has been processed at the plant, it moves on to the refining stage, where it will become usable cobalt products The two primary refining processes used are hydrometallurgy and pyrometallurgy Hydrometallurgy involves treating the ore with certain chemicals to extract elemental cobalt, while pyrometallurgy is melting down the ore How Cobalt is Processed and Refined – A Complete Guide2019年8月1日 Request PDF Extraction of nickel and cobalt from a laterite ore using the carbothermic reduction roastingammoniacal leaching process The carbothermic reduction roasting followed by ammoniacal Extraction of nickel and cobalt from a laterite ore using the 2014年1月1日 Operational differences from nickel H 2 reduction are: (1) cobalt “seed” is made by precipitation from cobaltous diamine solution using sodium cyanide catalyst and sodium sulfide particle nucleation sites, (2) cobalt reduction is slightly faster than nickel reduction and the resulting cobalt particles are slightly larger and more irregular due to particle agglomeration, Nickel and Cobalt Production ScienceDirect
.jpg)
Extraction Behavior of Nickel and Cobalt From SerpentineRich Ore
2023年10月12日 The demand for nickel has been steadily increasing in the 21st century, primarily driven by the rising demand for electric vehicle batteries Nickel in laterite is associated within silicate in saprolite ore and hydroxide/oxide in limonite ore Recently, the sulfation–roasting–leaching process has been developed to address the challenges of