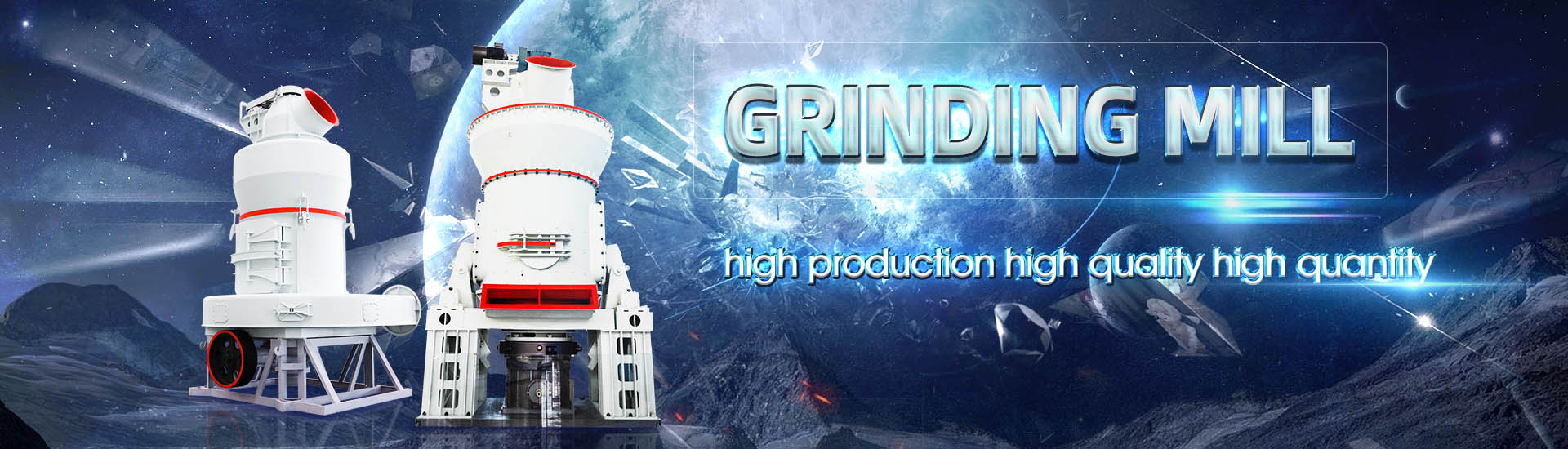
What is the wear of the milling cutter related to
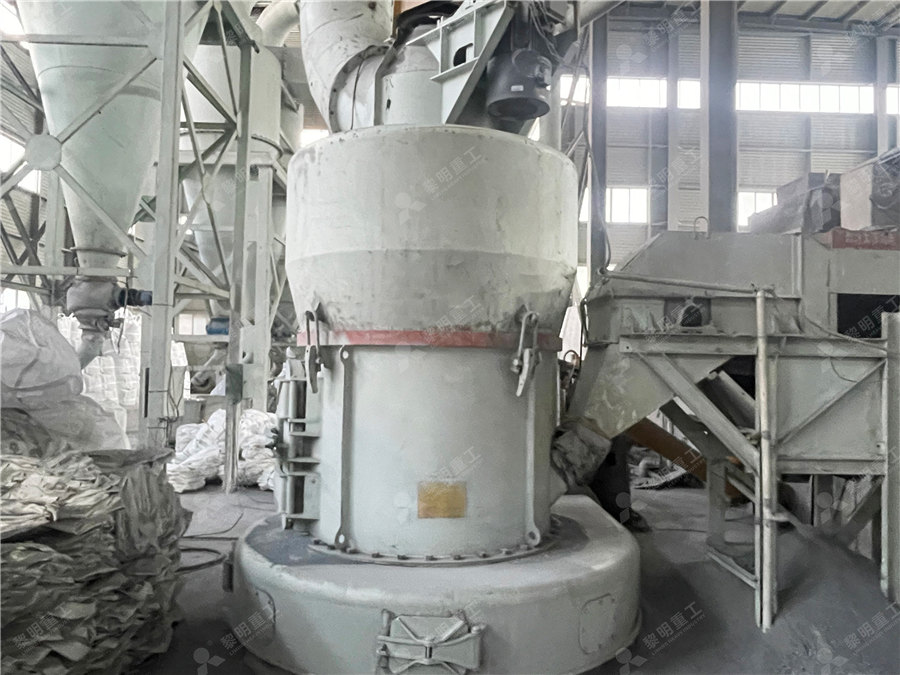
Intelligent recognition of milling cutter wear state with cutting
2020年7月10日 We present LeNetWSRMC network, a novel approach to recognize wear state of milling cutter based on the clutter signal of spindle current The cutting vibration and tool wear are the main reasons for exciting the dynamic cutting force and the clutter signal of spindle 2006年1月1日 Fretting wear occurs when repeated loading and unloading cause cyclic stresses that induce surface or subsurface breakup and loss of material Cutting tool wear is a result of Chapter 4 Cutting tool wear, tool life and cutting tool physical 2024年2月15日 To address this challenge, the paper proposes a new tool wear monitoring framework that identifies the wear state of milling cutters under different cutting parameters Intelligent monitoring of milling tool wear based on milling force 2021年6月16日 Tool wear condition is a key factor in milling which directly affects machining precision and part quality It is essential to seek a convenient method to model and predict tool Tool wear estimation and life prognostics in milling: Model
.jpg)
Milling cutter wear prediction method under variable working
2022年6月15日 Datadriven based methods predict tool wear by collecting signals related to tool wear during machining (such as cutting force, vibration, acoustic emission, and current) and 2011年6月1日 In this paper, the wear characteristics of seven milling cutters in milling of TC4 (Ti6Al4V) titanium alloys are investigated The results indicated that the averaged flank wear Wear of Milling Cutters in Machining of TC4 (Ti6Al4V) Titanium 2022年4月24日 In this paper, four kinds of micromilling cutters with different wear states were obtained by designing micromilling experiments, and the wear process and wear mechanism were observed and analyzed The cutter Development of Tool Wear Standards and Wear 2021年12月10日 In turning operations, the wear of cutting tools is inevitable As workpieces produced with worn tools may fail to meet specifications, the machining industries focus on replacement policies that mitigate the risk of A Systematic Literature Review of Cutting Tool Wear
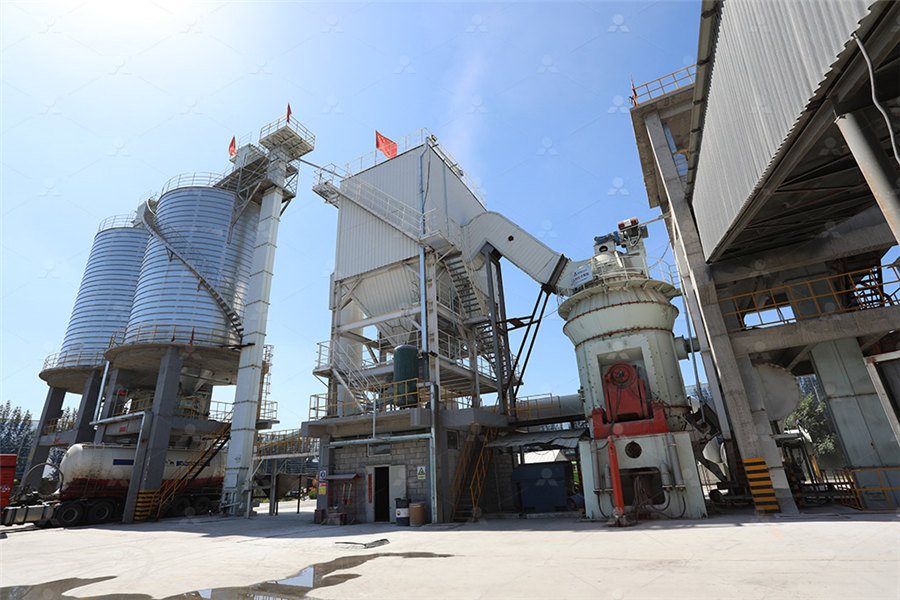
Onmachine Wear Measurement for Milling Cutter Based on
Abstract: As a key factor in the milling process, the wear status of the milling cutter has a significant impact on the machining quality of the workpiece To detect wear on a milling 2017年5月25日 The material removal process uses cutting tools in order to produce the desired shape of the work piece Tool wear has been a problem for cutting tools, since cutting tools wear and break Research has been accomplished in the tool wear field for tool life and more recently tool wear The computer generation has created a method to simulate the material removal Wear Analysis of Multi Point Milling Cutter using FEACoating tool has become a symbol of modern cutting tools, which has exceeded 50% usage to improve their working performance , including drill bits, reamers, taps, milling cutters, forming tools, etc As a chemical and thermal barrier, the How to choose the coating of the milling tools?2022年10月1日 In the milling process, under the highefficiency and intermittent cutting loads, the instantaneous posture of the milling cutter and the instantaneous cutterworkpiece engagement are in an unstable state It is difficult to accurately identify the friction and wear boundary of the cutter tooth flank It has become an urgent problem to be solved in the life Crossscale identification for friction and wear boundaries of tooth
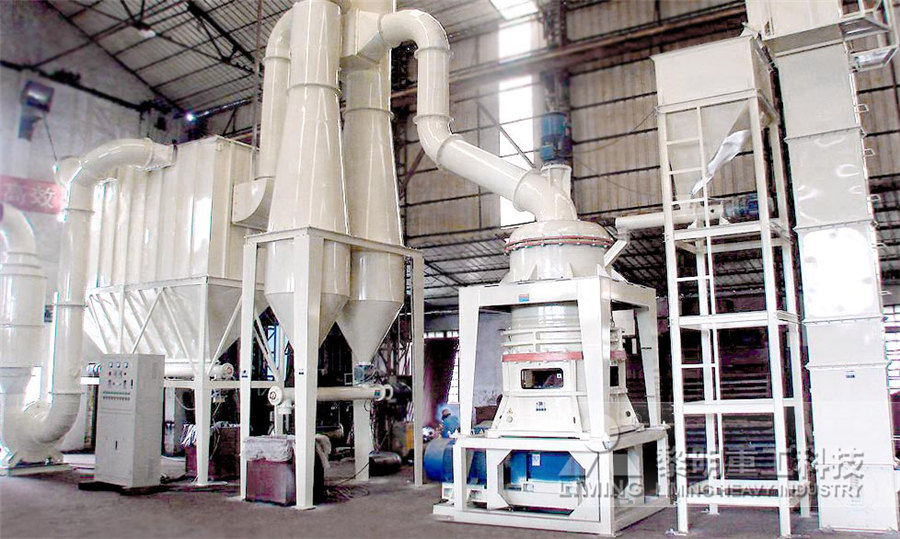
What Are the Reasons for Fast Wear of Cutting Tools CNC Tool Wear
2020年1月24日 Cemented carbide blade usually are secured on the cutter body and become one of the main cutter materials now 2) Use specific cutting fluid The special cutting fluid with sulfurized EP antiwear additive can effectively protect The experimental results show that the proposed SSDAEPSOLSSVM model performs better than Partial Least Squares Regression (PLSR), Back Propagation Neural Network (BPNN) and Extreme Learning Machine (ELM) in terms of prediction accuracy In order to ensure the reliability and stability of the manufacturing process, tool wear state should be realized realtime and Tool Wear Status Recognition and Prediction Model of Milling Cutter 2023年11月21日 An attention mechanismbased method is proposed for milling cutter wear detection that can classify the tool wear status, extract the side edge surface contour, and improve the accuracy and efficiency of digital milling With the development of modern manufacturing industry, the requirements for machining accuracy of CNC machine tools are Attention Mechanism Based CNC Milling Cutter Wear Detection 2024年3月28日 While cobalt milling cutters are not quite as wearresistant as carbide, they offer an excellent balance between performance and cost, making them a reliable choice for many applications Diamond Diamond milling cutters are another highperforming option, made from polycrystalline diamond (PCD) or natural diamond10 Types of Milling Cutters: Uses and Selection Principles
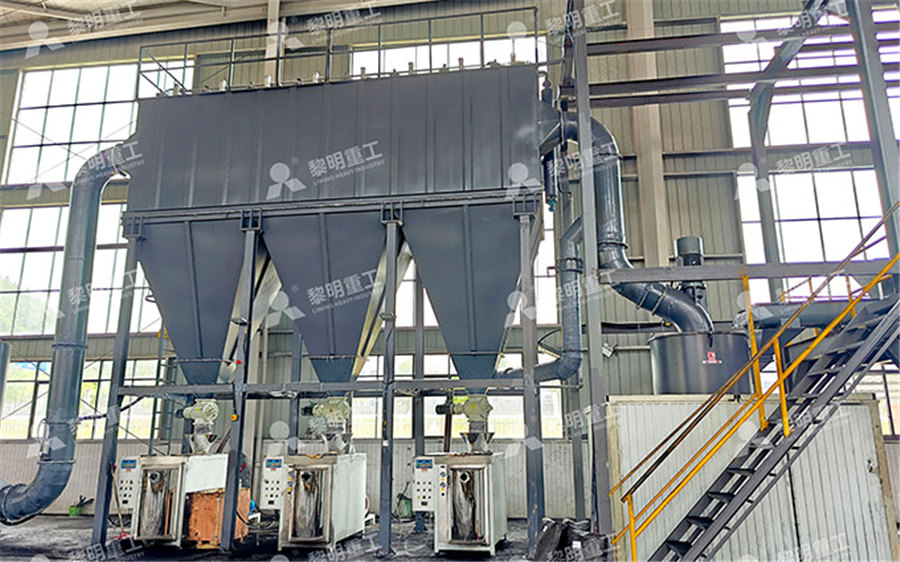
Cutting Tool Wear Prediction in Machining Operations, A Review
2022年10月9日 for the uncoated milling cutter tool wear prediction considering periodic process factors is described [93] Figure 9 depicts the tool wear prediction procedure using a FEM model [93]2020年7月1日 LeNetWSRMC network is presented, a novel approach to recognize wear state of milling cutter based on the clutter signal of spindle current, which uses the deep convolutional neural network (DCNN) model to extract features from the spindleCurrent clutter signal (SCCS) as the wear state In the process of milling, tool wear directly affects the quality and accuracy of Intelligent recognition of milling cutter wear state with cutting A monitoring method for identifying the wear state of the milling cutter by using the spindle current combined with the deep learning network is proposed and the experimental results show that this method can effectively monitor the wearState of the Milling cutter : In the machining process of CNC machine tools, the state of tool wear has a great influence on the surface quality and Wear Status Recognition for Milling Cutter Based on 2024年11月11日 Choosing the Right Milling Cutter When I’m trying to choose a particular milling cutter, there are a few aspects that I take into consideration to maintain output and accuracy I first check the workpiece This is because various materials have different cutter compositions that yield the best resultsUnderstanding the Milling Process: A Comprehensive Guide to
.jpg)
Wear state detection of the end milling cutter based on wear
2024年10月12日 In the assessment of the tool wear state for the spiral edge of milling cutter based on machine vision, the traditional assessment criterion is often inaccurate due to the problem of missing of The aim of the paper is to determine changes of parameters (cutting power, roughness of wooden surface and rounding of cutting edge) which characterize the wear of the cutting tool in the milling process of aspen wood (Populus tremula), depending on the rake angle of the cutting tool The milling process was performed by means of a computer numerical control milling machine and Parameter changes which characterize the wear of the cutting tool DOI: 101016/jjmatprotec2023 Corpus ID: ; An oscillating milling strategy based on the uniform wear theory for improving service life of the ballend cutter @article{Guo2023AnOM, title={An oscillating milling strategy based on the uniform wear theory for improving service life of the ballend cutter}, author={Liuwei Guo and Xuezhi Liao and Wei An oscillating milling strategy based on the uniform wear theory 2023年4月23日 Threeedge milling cutter It’s used for machining various grooves and stepped surfaces, with teeth on both sides and circumference Chamfer milling cutter It’s used for milling grooves at a certain angle, with two types of singleangle and doubleangle milling cutters Saw blade milling cutter6 Types of milling cutters and Toknows about them
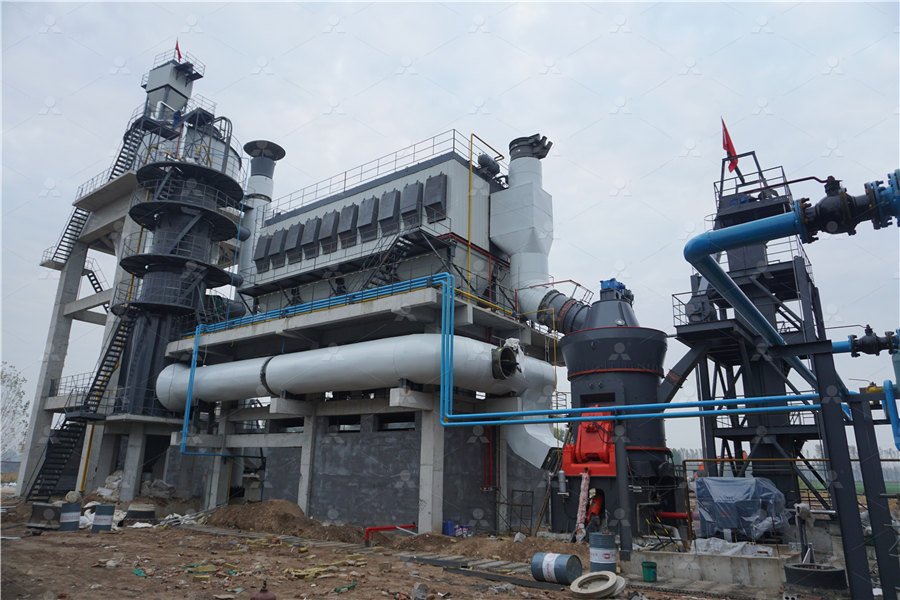
Onmachine Wear Measurement for Milling Cutter Based on
Experimental results show that the proposed milling machine wear detection system is suitable for industrial use due to its rapid detection speed and strong recognition accuracy, which are desirable for engineering applications As a key factor in the milling process, the wear status of the milling cutter has a significant impact on the machining quality of the workpiece To detect 2020年7月10日 In the process of milling, tool wear directly affects the quality and accuracy of workpieces Online recognition of milling cutter wear state has been and remains a growing interest in intelligent manufacturing to increase the machining efficiency and control the unqualified rate of workpieces The effective value of spindle current can effectively Intelligent recognition of milling cutter wear state with cutting 2023年7月16日 In the process of highefficient milling titanium alloy(Ti6Al4V) workpieces, the ICS (instantaneous contact stiffness) and its distribution between flank face of milling cutter tooth and workpiece change instantaneously due to cutting vibration, which makes tool flank friction and wear status be of instability In this work, the tool flank microconvex body stiffness model was Effect of contact stiffness on cutter flank friction and wear in The ballnose end milling cutter is an important cutting tool which is used to cut the complicated highprecision curved surfaceIn the manufacturing process of grinding ballnose end milling cutter,as the grinding time increased,the wheel will be wear,the edge curve of ballnose end milling cutter will also changeIn the paper,the grinding simulation system and parameters Effects of Wheel Wear on the Manufacturing Errors of BallNose
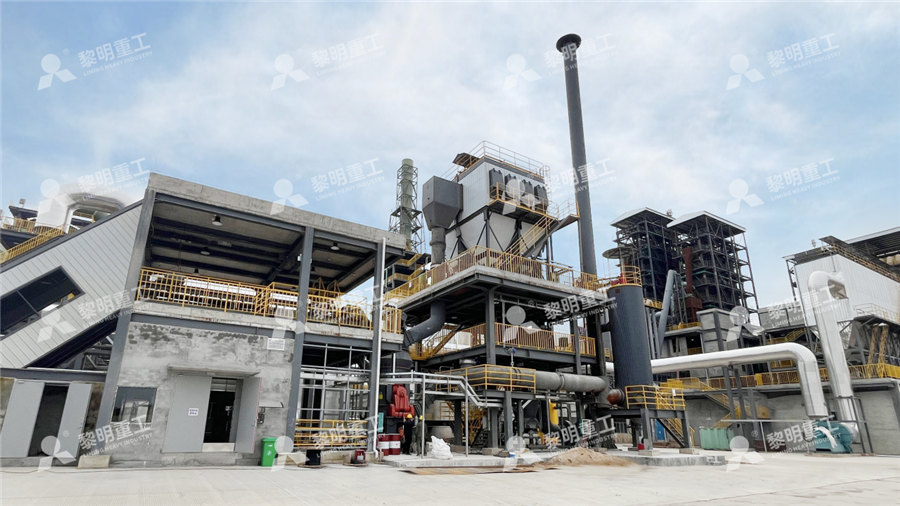
The Ultimate Guide to Climb Milling: What It Is and Why It Matters
Climb milling, also known as down milling, refers to a cutting technique where the cutter rotates in the same direction as the feed, allowing it to engage with the material smoothly Key Features of Climb Milling Direction: Cutter rotates in the same direction as the feed Chip Formation: Thin chips are produced, enhancing surface finish2024年4月15日 Different Types of CNC Milling Operations Based On Milling Mechanisms There are three primary variations of operations on milling machines: manual, CNC, and conventional climb 1 Manual Milling In 12 Types of Milling Operations: A Detail Explanation2022年11月30日 Another characteristic feature of milling is that the cutting edges of the milling tool are not engaged over the entire stroke, but each revolution of the tool is accompanied by at least one interruption of the cut per cutting edge The corresponding technical term is proverbial, because it is an "interrupted cut" The constant "in and out" means that the cutting edges have What is milling? Fundamentals of Production Engineering2022年6月15日 Milling tool wear prediction is of great significance to ensure machining quality and save production cost Wear is a complex nonlinear physical process under the action of high pressure, high strain, and high temperature, and has different laws under different working conditions, which makes it difficult to predict tool wear under variable working conditions In Milling cutter wear prediction method under variable working

Milling Machine: Definition, Parts, Operation, Working Principle
2022年7月4日 Milling Machine Definition: The milling machine is a type of machine which removes the material from the workpiece by feeding the work past a rotating multipoint cutterThe metal removal rate is higher very high as the cutter has a high speed and many cutting edges It is the most important machine in the tool room as nearly all the operations can be performed on 2021年7月30日 Timely and effective identification and monitoring of tool wear is important for the milling process However, traditional methods of tool wear estimation have run into difficulties due to under New Tool Wear Estimation Method of the Milling Process Based 2022年11月30日 Another characteristic feature of milling is that the cutting edges of the milling tool are not engaged over the entire stroke, but each revolution of the tool is accompanied by at least one interruption of the cut per cutting edge The corresponding technical term is proverbial, because it is an "interrupted cut" The constant "in and out" means that the cutting edges have What is milling? DMG MORI Australia and New Zealand2023年7月10日 What is Milling? Milling is a type of machining process that uses a rotating cutter to remove material in a controlled manner from a workpiece This subtractive manufacturing technique aims to turn the workpiece into the required shape A modern milling machine is often paired with Computer Numerical Control (CNC) for automated control over the whole processWhat is Milling: Definition, Process Operations
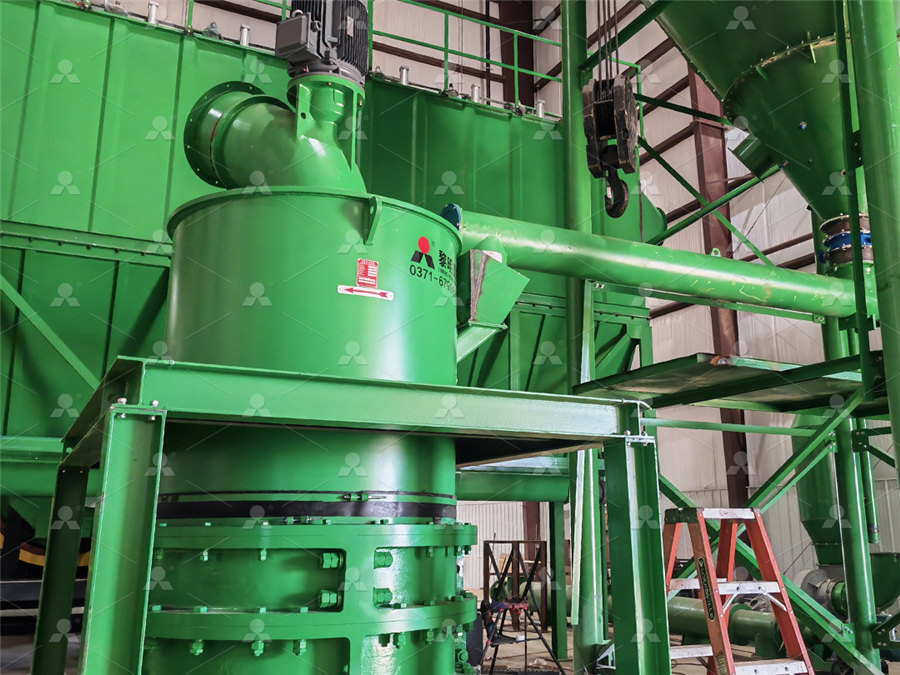
The Ultimate Guide to Different Types of Milling Machine Cutters
2024年7月24日 Squareended ones come in handy when you need sharp corners; ballnose cutters are designed specifically for making 3D contoured shapes during milling operations, whereas corner radius tools offer improved edge strength and wear resistance, thus being able to withstand higherspeed milling applications2020年1月1日 Aimed at solving the problems of tool wear and poor surface quality in milling a Ti alloy with a ballend milling cutter, a method of applying a microtexture to a tool rake face to reduce tool wear is proposed in this article By comparing the wear morphology of microtextured tools with that of nontextured tools after milling with the same stroke, the antifriction and Wear optimization of titanium alloy cutter milled with 2024年5月16日 The Rise of Indexable Milling in Modern Manufacturing In my quest to learn more about metalworking, I stumbled upon a fantastic creation that has changed manufacturing completely: indexable millingThis latest technology has not only increased the efficiency of milling operations, but it has also created possibilities that could not be achieved earlier with solid Unlock the Potential of Shoulder Milling: Explore Tools, 2017年5月25日 The material removal process uses cutting tools in order to produce the desired shape of the work piece Tool wear has been a problem for cutting tools, since cutting tools wear and break Research has been accomplished in the tool wear field for tool life and more recently tool wear The computer generation has created a method to simulate the material removal Wear Analysis of Multi Point Milling Cutter using FEA
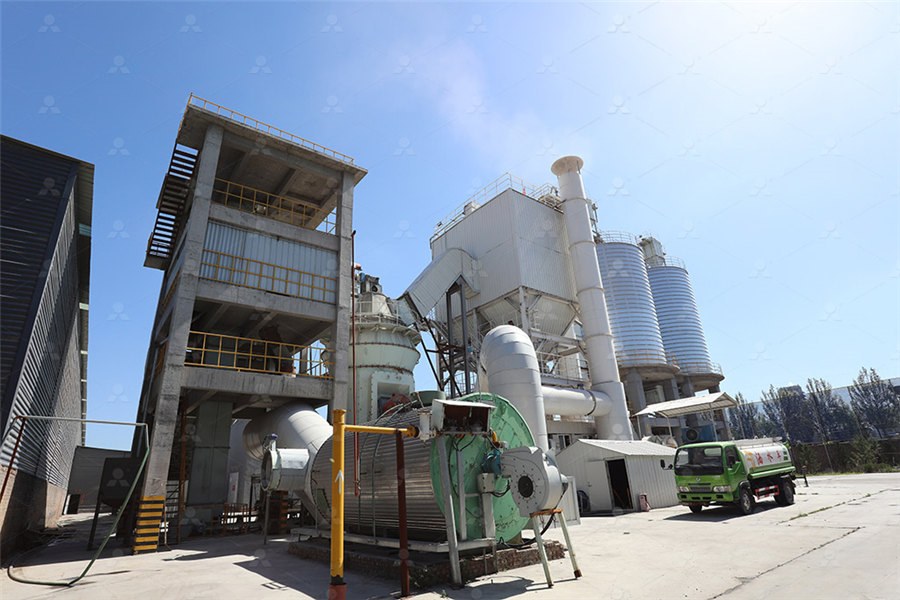
How to choose the coating of the milling tools?
Coating tool has become a symbol of modern cutting tools, which has exceeded 50% usage to improve their working performance , including drill bits, reamers, taps, milling cutters, forming tools, etc As a chemical and thermal barrier, the 2022年10月1日 In the milling process, under the highefficiency and intermittent cutting loads, the instantaneous posture of the milling cutter and the instantaneous cutterworkpiece engagement are in an unstable state It is difficult to accurately identify the friction and wear boundary of the cutter tooth flank It has become an urgent problem to be solved in the life Crossscale identification for friction and wear boundaries of tooth 2020年1月24日 Cemented carbide blade usually are secured on the cutter body and become one of the main cutter materials now 2) Use specific cutting fluid The special cutting fluid with sulfurized EP antiwear additive can effectively protect What Are the Reasons for Fast Wear of Cutting Tools CNC Tool Wear The experimental results show that the proposed SSDAEPSOLSSVM model performs better than Partial Least Squares Regression (PLSR), Back Propagation Neural Network (BPNN) and Extreme Learning Machine (ELM) in terms of prediction accuracy In order to ensure the reliability and stability of the manufacturing process, tool wear state should be realized realtime and Tool Wear Status Recognition and Prediction Model of Milling Cutter
.jpg)
Attention Mechanism Based CNC Milling Cutter Wear Detection
2023年11月21日 An attention mechanismbased method is proposed for milling cutter wear detection that can classify the tool wear status, extract the side edge surface contour, and improve the accuracy and efficiency of digital milling With the development of modern manufacturing industry, the requirements for machining accuracy of CNC machine tools are 2024年3月28日 While cobalt milling cutters are not quite as wearresistant as carbide, they offer an excellent balance between performance and cost, making them a reliable choice for many applications Diamond Diamond milling cutters are another highperforming option, made from polycrystalline diamond (PCD) or natural diamond10 Types of Milling Cutters: Uses and Selection Principles2022年10月9日 for the uncoated milling cutter tool wear prediction considering periodic process factors is described [93] Figure 9 depicts the tool wear prediction procedure using a FEM model [93]Cutting Tool Wear Prediction in Machining Operations, A Review2020年7月1日 LeNetWSRMC network is presented, a novel approach to recognize wear state of milling cutter based on the clutter signal of spindle current, which uses the deep convolutional neural network (DCNN) model to extract features from the spindleCurrent clutter signal (SCCS) as the wear state In the process of milling, tool wear directly affects the quality and accuracy of Intelligent recognition of milling cutter wear state with cutting
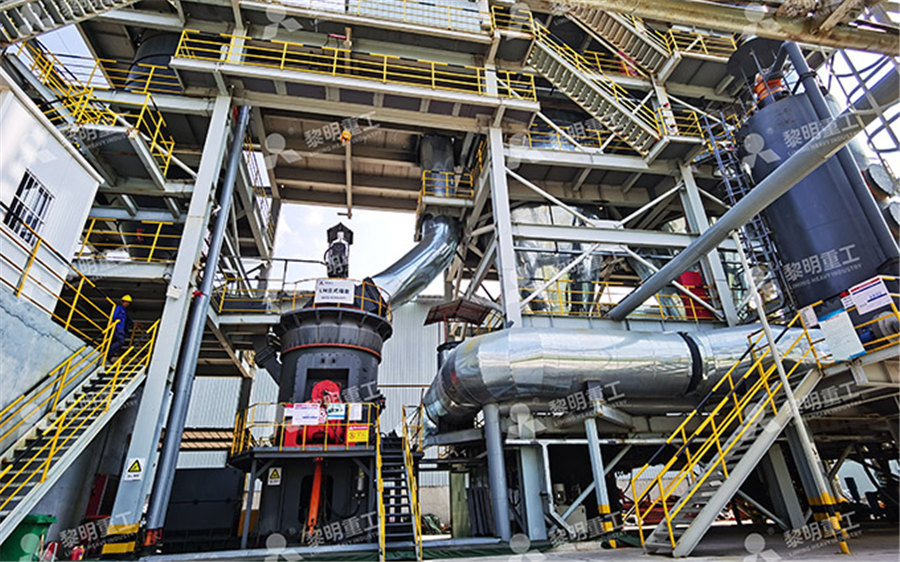
Wear Status Recognition for Milling Cutter Based on
A monitoring method for identifying the wear state of the milling cutter by using the spindle current combined with the deep learning network is proposed and the experimental results show that this method can effectively monitor the wearState of the Milling cutter : In the machining process of CNC machine tools, the state of tool wear has a great influence on the surface quality and