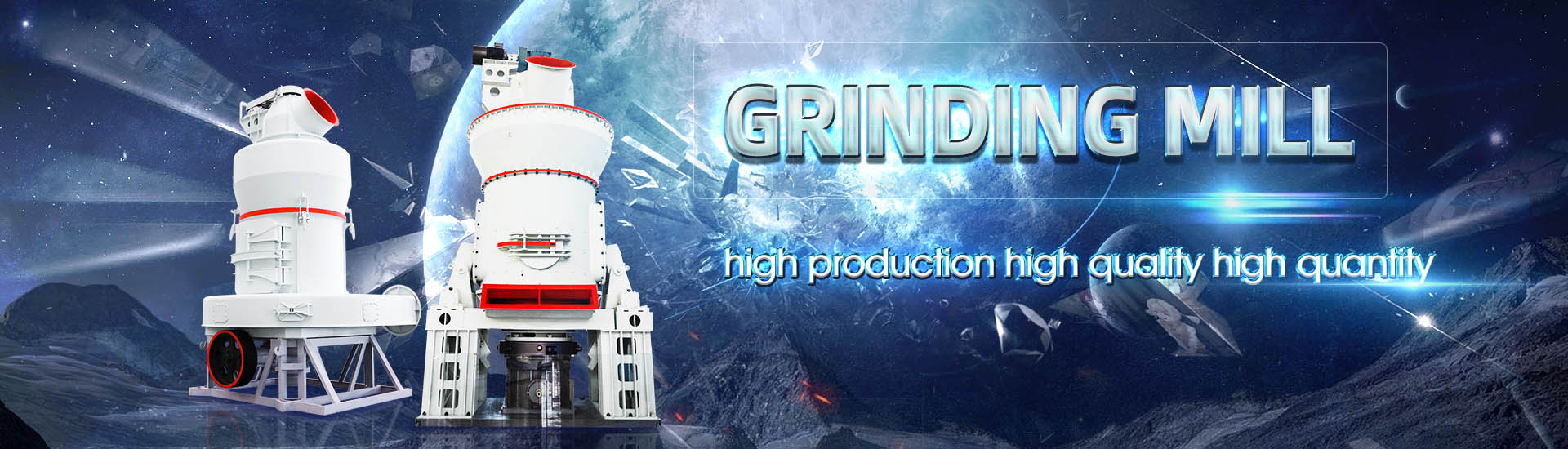
Cement mill production
.jpg)
Cement mill Wikipedia
A cement mill (or finish mill in North American usage ) is the equipment used to grind the hard, nodular clinker from the cement kiln into the fine grey powder that is cement Most cement is currently ground in ball mills and also vertical roller mills which are more effective than ball mills 展开The Cement Plant Operations Handbook is a concise, practical guide to cement manufacturing and is the standard reference used by plant operations personnel worldwide Providing a The Cement Plant Operations Handbook International Cement There are six main stages of the cement manufacturing process The raw cement ingredients needed for cement production are limestone (calcium), sand and clay (silicon, aluminum, iron), How Cement is Made Cement Manufacturing ProcessThis page and the linked pages below summarize the cement manufacturing process from the perspective of the individual components of a cement plant the kiln, the cement mill etc For information on materials, including reactions in Cement manufacturing: components of a cement plant
.jpg)
StepbyStep Guide to the Manufacturing of Cement
This article will guide readers through each step in the manufacturing of cement, detailing critical processes such as blending, hydration, and the role of calcium carbonate, silica, alumina, and iron oxide in cement productionCement is produced by mixing and finegrinding clinker, gypsum and mineral components (eg limestone, pozzolana, fly ash or granulated blast furnace slag, silica fume) in cement mills Cement Production Process Regain MaterialsBoth types of mills are commonly used in the production of cement Once the clinker and additives have been milled into a fine cement powder, the cement is transported to storage silos and Cement Production Demystified: StepbyStep Process and Carbon Discover the cement production process Learn how Heidelberg Materials creates highquality cement from raw materialsHow cement is made Heidelberg Materials
.jpg)
A practical guide to improving cement manufacturing processes
The cement production process 1 The Quarry: The cement production process begins with the extraction of limestone and clay from the quarry 2 Crusher and PreBlending: The material is then crushed to reduce particle sizes and blended to reduce variability in composition 3 Raw Mill and Kiln: Raw materials and additives areAdjusting mill parameters: Finetuning mill parameters such as mill speed, ball charge, filling ratio, and grinding media size can have a substantial impact on the grinding efficiency of the mill For example, a 10% increase in mill speed can Cement Mill Optimization: Practical Strategies for Raw mill is the grinding equipment applied in the raw material preparation processIn the wet process of cement production, raw materials should be ground into raw slurry with a water content of 30% – 40% While in the dry process of Cement Mill Cement Grinding Machine AGICO 2014年11月18日 CEMENT PRODUCTION PROCESS ROLLER MILL ROLLER MILL VerticalRollerMill(VRM) 3 Sections Separation Grinding Drive Vertical Roller Mill (VRM) Details VRM Working principle Grinding force = Roller weight + (pressure) Force Material bed Roller rolls freely with table Feed material Table moves with drive Max Particle size in feed: 5 CEMENT PRODUCTION PROCESS SlideServe
.jpg)
How Cement is Made Cement Manufacturing Process
Stage of Cement Manufacture There are six main stages of the cement manufacturing process Stage 1: Raw Material Extraction/Quarry The raw cement ingredients needed for cement production are limestone (calcium), sand and clay (silicon, aluminum, iron), shale, fly ash, mill scale, and bauxite The ore rocks are quarried and crushed into smaller pieces of about 6 inchesArticles like this one can provide a lot of useful material However, reading an article or two is perhaps not the best way to get a clear picture of a complex process like cement production To get a more complete and integrated understanding of how cement is made, do have a look at the Understanding Cement book or ebookCement Millinghardest materials The OK™ cement mills are available in all sizes 0 100 200 300 400 500 600 700 800 OK 776 OK 434 OK 484 OK 404 OK 524 OK 716 OK 816 OK 666 OK 614 OK 564 OK ™ cement mill production and slag grinding production (t/h) OK 283 OK 373 OK ™ cement mill and slag grinding Actual capacity depends on product fineness OK™ CEMENT MILLFor a cement mill: intermediate or outlet diaphragm For the case of; cement mills with a drying chamber see raw mills Mill working conditions: ventilation air speed through the mill Bigger or smaller than 12 [m/s] Material abrasivity The [%] of slag or pouzzolana content on the fresh mill feed for cement grindingEverything you need to know about clinker/cement Grinding
.jpg)
Cement manufacturing process PPT SlideShare
2014年6月10日 Cement manufacturing process • Global production is 5 billion cubic yards per year (using approximately 125 billion tons of cement) 7 – Sand (SiO2) – Shale, Clay (SiO2, Al2O3, Fe2O3) – Iron Ore/Mill Scale (Fe2O3) 10 Portland Cement (cont’d) Cement Production Seminar: Grinding Understand the fundamentals and gain insights on how to improve the performance and productivity, efficiency, and product quality of your grinding systems This 3day seminar covers ball and vertical mills with a focus oncomminution theory, design basis, operational principles, control and regulation, process troubleshooting, Cement Production Seminar: GrindingThe OK™ mill has been our standard cement VRM since 1993 Since its introduction the OK™ mill has proven to be the most efficient cement VRM available with the highest reliability and ease of operation In 2017, we introduced the OK raw mill, which is designed with the same proven technology and modular design as the OK cement millOK RAW AND CEMENT MILLAdvantages of cement ball mill Less investment: cement ball mill with advantages of a perfect motor system, low energy consumption and power consumption, and ultralow operating cost, which can save a lot of cost input; Cement Ball Mill Ball Mill For Sale Cement Mill 15
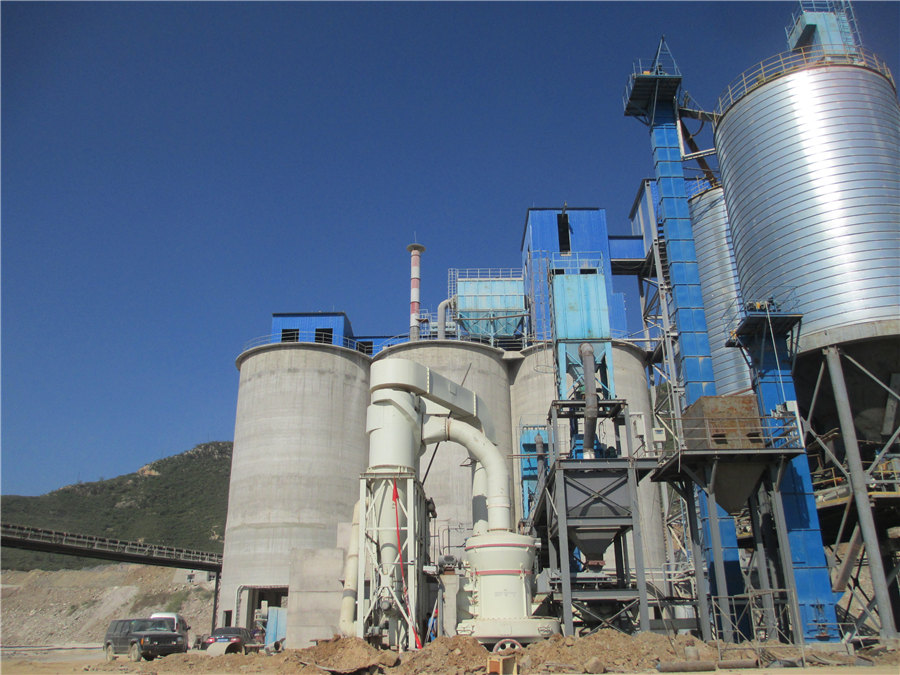
Preparation Of Cement Raw Material Cement Mill,
AGICO Cement supplies cement equipment for cement raw material production as you need, such as cement mill, cement crusher, onestop turnkey project, welcome to contact! Skip to content +86 info@cement After cooling, the clinker may be stored temporarily in a clinker store, or it may pass directly to the cement mill The cement mill grinds the clinker to a fine powder A small amount of gypsum a form of calcium sulfate is normally ground up with the clinker The gypsum controls the setting properties of the cement when water is addedCement manufacturing components of a cement plant Understanding Cement2024年10月14日 Although the production process of cement mill is complicated, every link is carefully designed and operated to ensure the high quality and efficient production of the final product The vertical cement mill we launched is a modern grinding equipment that integrates high efficiency, energy saving and environmental protectionWhat Role Does Cement Mill Play In Production?The cyclone preheating system Phase IV: Calcination The calcination is the core phase of the cement making dry process The calcination of the preheated raw meal takes place in the rotary kiln of the cement plant The rotary kiln is a huge rotating furnace in which the raw meal is heated up to 1450 ⁰C and turned to clinkerHow Is Cement Produced in Cement Plants Cement Making
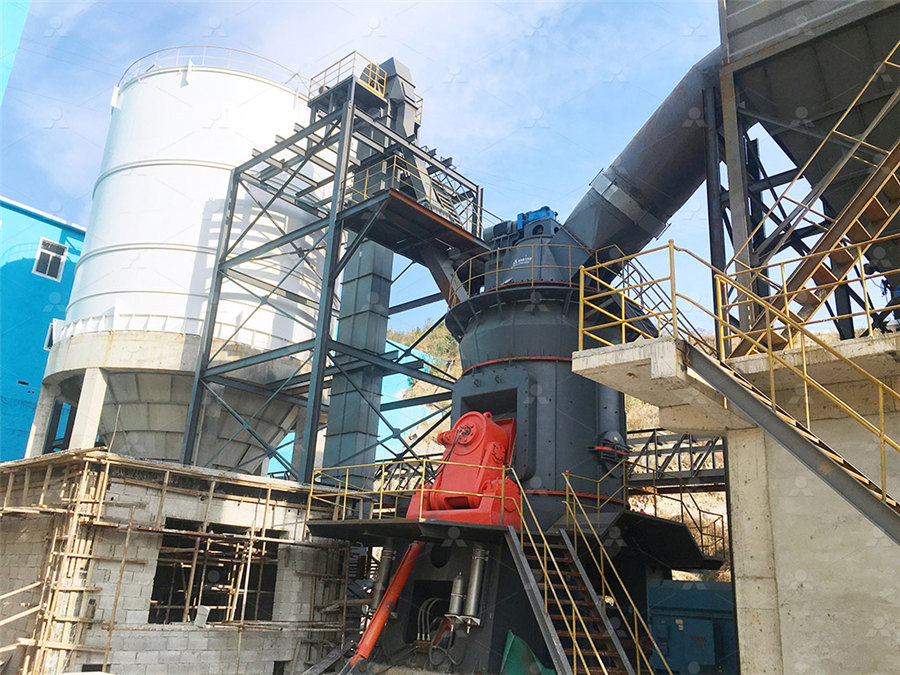
polysius® booster mill
For two years, the mill operated in fly ash grinding, the results in product quality and high energy efficiency convinced to keep the mill Since the second half of 2019, this mill upgrades an existing ball mill grinding circuit of the integrated cement production, achieving an increase in production capacity and also in cement qualityCement Production Portland Cement By Production Clinker Phases Alite or 3CaO SiO2 or C3S Hydrates hardens quickly High early strength Higher heat of hydration – A free PowerPoint PPT presentation (displayed as an HTML5 slide show) on PowerShow id: 4091fbZDU5YCement Production PowerPoint PPT PresentationThe dry process cement production line is composed of cement crushers, cement raw mill, cement kiln, cement cooler, cyclone preheater, cement silo, dust collector, etc AGICO offers cement production lines from 1000 TPD to 10000 TPD Skip to Cement Production Line Cement Manufacturing Plant AGICO Cement At present, it has completed over 60 new dryprocess cement clinker production lines of various sizes (3008000 tons/d), more than 10 pure low temperature waste heat power generation projects for cement clinker production lines and over Leading Supplier of Cement Plant Equipments Rotary
.jpg)
Cement Separator HighEfficiency Cement Mill
Cement production line: Cement Mill Separator is mainly used in the clinker mill system of the cement production line to separate ground cement clinker and cement powder It can improve the production efficiency and product quality of The journey of cement production begins with the extraction of raw materials, The main process in cement grinding units involves grinding the clinker into a fine powder using a cement ball mill or vertical roller mill This step is crucial as the StepbyStep Guide to the Manufacturing of CementProduction Process We source our limestone, pozzolans and clay primarily from ALQC and IQAC We also source raw materials, including limestone, mixed with gypsum and fed in specified proportions into a cement grinding mill where they are ground into an extremely fine powder and mixed with grinding aids including admixtures Production Process CEMEX PhilippinesCement production involves quarrying limestone and clay, grinding and blending the materials, burning them at high temperatures to form clinker, and finely grinding the clinker to produce cement powder The key steps are: 1) Quarrying limestone and clay and grinding them to powder; 2) Blending the powders in precise proportions; 3) Burning the blend at high heat to form Chapter 1 Introduction To Cement Production
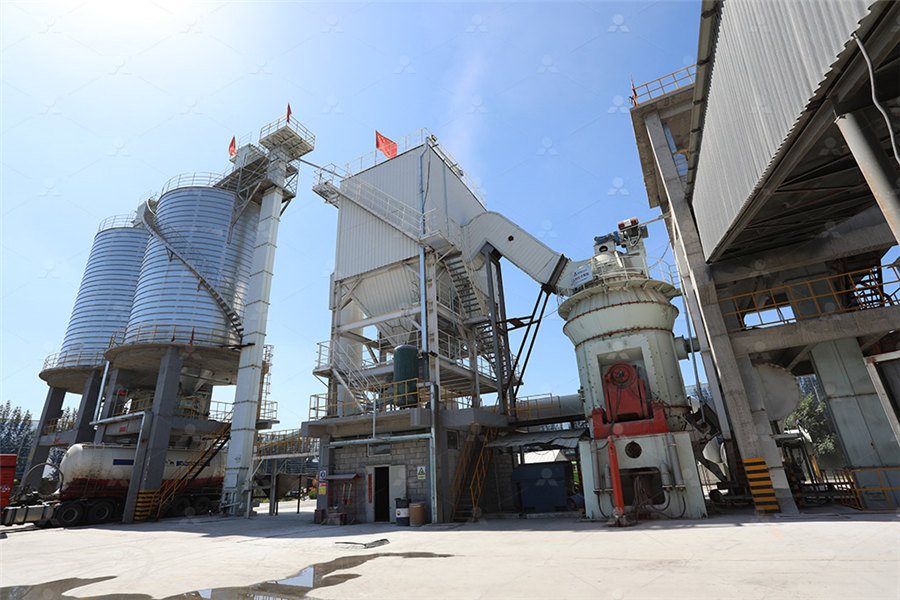
Cement Mill MadeinChina
China Cement Mill wholesale Select 2024 high quality Cement Mill products in best price from certified Chinese Cement Mixer manufacturers, China Horizontal 26X13m Cement Mill Production Line with ISO, CE Certificate 700tpd Ball Mill US$ 20000 / set 1 set (MOQ) ZHENGZHOU ZHENGJIA HEAVY INDUSTRY CO,LTD2024年11月23日 Cement Extraction, Processing, Manufacturing: Raw materials employed in the manufacture of cement are extracted by quarrying in the case of hard rocks such as limestones, slates, and some shales, with the aid of blasting when necessary Some deposits are mined by underground methods Softer rocks such as chalk and clay can be dug directly by Cement Extraction, Processing, Manufacturing Britannica2022年7月4日 project of the factory which will have 10 cyclones due to addition of another cement mill responsible for cement production while the rest are subordinates The report focuses on three Mining Activities, Cement Production Process and Quality Control2014年4月16日 cement machinery,cement making machinery,Tube Mill,Cement production line Skip to content Home; About Us; Products; Contact Us; technical support, and general contracting Specific cement production line scale Haijian can undertake ranges from 6000t/d, 5000t/d, 4000t/d, 3000t/d, 2500t/d, 2000t/d, 1500t/d, 1300t/d, Cement production line Shenghui Machinery (CSM)
.jpg)
Cement Equipment Manufacturer PENGFEI Grinding Mill
Our company provides a complete range of cement making machinery including the crusher, dust collector, cement rotary kiln, cement grinding mill, vertical coal mill, cooling and drying equipment, as well as cement conveying, lifting, and packaging machines Complete sets of cement production lines can be purchased View AllChoose the right cement manufacturing machine is an important influence factor to produce highquality cement The cement making machine frequently used in cement plants includes cement rotary kiln, shaft kiln, cement vertical mill, cement ball mill, cement roller press, etcCement Manufacturing Machine Cement Making Machine Cement The cement production process 1 The Quarry: The cement production process begins with the extraction of limestone and clay from the quarry 2 Crusher and PreBlending: The material is then crushed to reduce particle sizes and blended to reduce variability in composition 3 Raw Mill and Kiln: Raw materials and additives areA practical guide to improving cement manufacturing processes Adjusting mill parameters: Finetuning mill parameters such as mill speed, ball charge, filling ratio, and grinding media size can have a substantial impact on the grinding efficiency of the mill For example, a 10% increase in mill speed can Cement Mill Optimization: Practical Strategies for
.jpg)
Cement Mill Cement Grinding Machine AGICO
Raw mill is the grinding equipment applied in the raw material preparation processIn the wet process of cement production, raw materials should be ground into raw slurry with a water content of 30% – 40% While in the dry process of 2014年11月18日 CEMENT PRODUCTION PROCESS ROLLER MILL ROLLER MILL VerticalRollerMill(VRM) 3 Sections Separation Grinding Drive Vertical Roller Mill (VRM) Details VRM Working principle Grinding force = Roller weight + (pressure) Force Material bed Roller rolls freely with table Feed material Table moves with drive Max Particle size in feed: 5 CEMENT PRODUCTION PROCESS SlideServeStage of Cement Manufacture There are six main stages of the cement manufacturing process Stage 1: Raw Material Extraction/Quarry The raw cement ingredients needed for cement production are limestone (calcium), sand and clay (silicon, aluminum, iron), shale, fly ash, mill scale, and bauxite The ore rocks are quarried and crushed into smaller pieces of about 6 inchesHow Cement is Made Cement Manufacturing ProcessArticles like this one can provide a lot of useful material However, reading an article or two is perhaps not the best way to get a clear picture of a complex process like cement production To get a more complete and integrated understanding of how cement is made, do have a look at the Understanding Cement book or ebookCement Milling

OK™ CEMENT MILL
hardest materials The OK™ cement mills are available in all sizes 0 100 200 300 400 500 600 700 800 OK 776 OK 434 OK 484 OK 404 OK 524 OK 716 OK 816 OK 666 OK 614 OK 564 OK ™ cement mill production and slag grinding production (t/h) OK 283 OK 373 OK ™ cement mill and slag grinding Actual capacity depends on product fineness For a cement mill: intermediate or outlet diaphragm For the case of; cement mills with a drying chamber see raw mills Mill working conditions: ventilation air speed through the mill Bigger or smaller than 12 [m/s] Material abrasivity The [%] of slag or pouzzolana content on the fresh mill feed for cement grindingEverything you need to know about clinker/cement Grinding2014年6月10日 Cement manufacturing process • Global production is 5 billion cubic yards per year (using approximately 125 billion tons of cement) 7 – Sand (SiO2) – Shale, Clay (SiO2, Al2O3, Fe2O3) – Iron Ore/Mill Scale (Fe2O3) 10 Portland Cement (cont’d) Cement manufacturing process PPT SlideShareCement Production Seminar: Grinding Understand the fundamentals and gain insights on how to improve the performance and productivity, efficiency, and product quality of your grinding systems This 3day seminar covers ball and vertical mills with a focus oncomminution theory, design basis, operational principles, control and regulation, process troubleshooting, Cement Production Seminar: Grinding