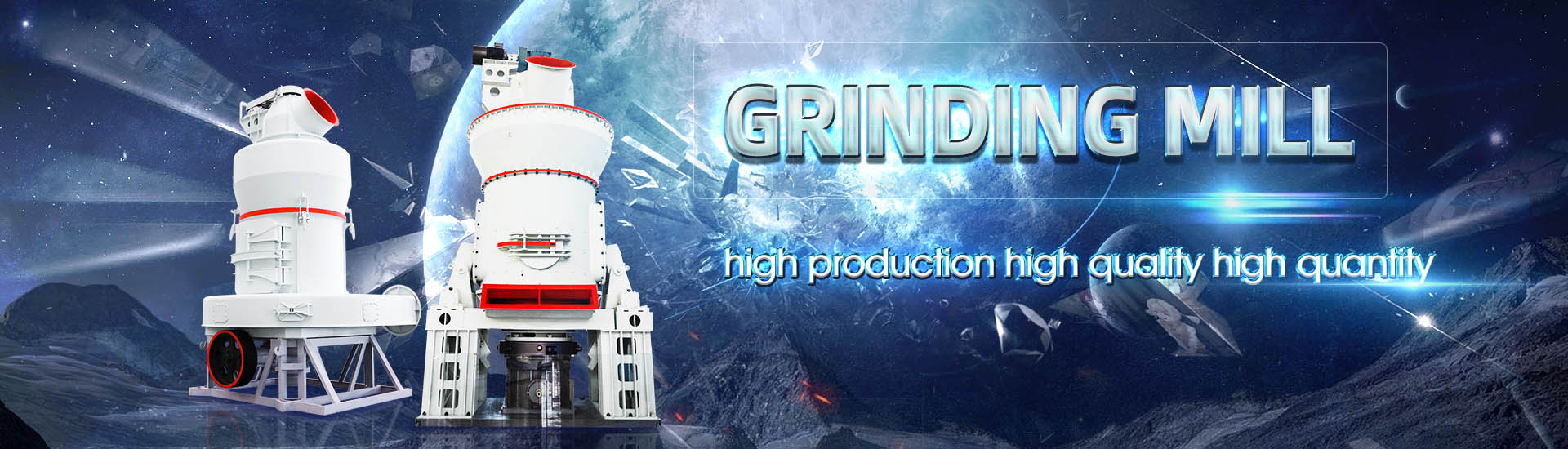
The following series of specifications of cement mill high production and high fine grinding
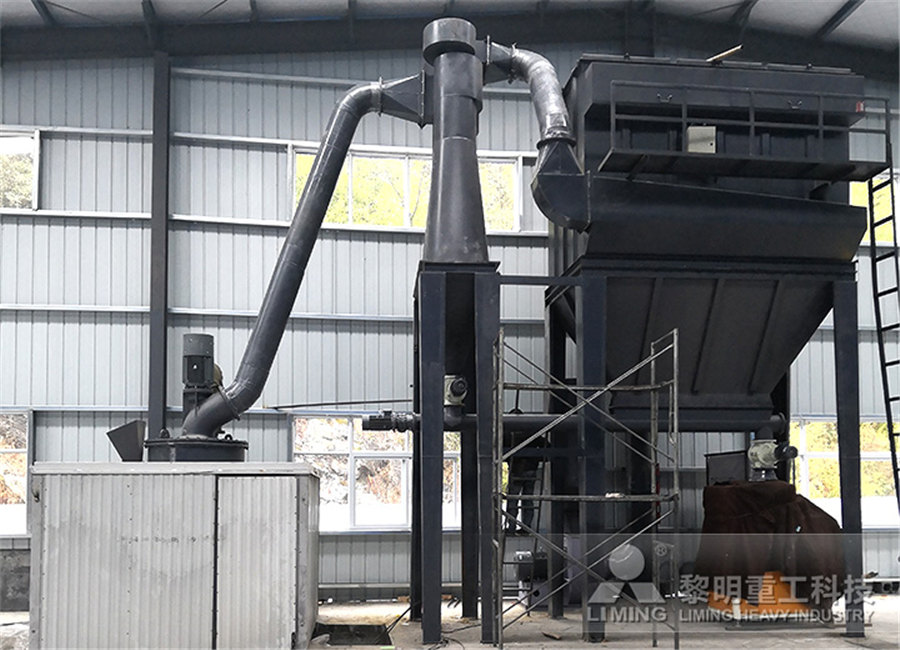
OPTIMIZATION OF CEMENT GRINDING OPERATION IN BALL MILLS
optimization of cement grinding operation in ball mills Several energy efficient options for cement grinding are available today such as vertical roller mills, roller presses (typically in combination mill systems with pre‑grinders (HPGR, roller presses, or VRM pre‑grinders) to increase cement production from about 30% to 100%, depending on the system installed As there are so many Thomas Holzinger, Holzinger Consulting, grinding system This document provides an overview of cement production including: The types of cement and their raw material compositions The schematic diagram of the cement production process Cement Mill Report PDF Cement Mill (Grinding) ScribdAs grinding accounts for a sizeable share in a cement plant’s power consumption, optimisation of grinding equipment such as ball mills can provide significant cost and CO 2BALL MILLS Ball mill optimisation Holzinger Consulting
.jpg)
Cement Grinding Cement Plant Optimization
Highly energy intensive unit operation of size reduction in cement industry is intended to provide a homogeneous and super fine (30004000 Blain) cement Grinding operation is monitored for By optimizing the grinding process, cement manufacturers can achieve higher productivity and lower energy consumption Let’s explore some practical strategies with realworld figures and Cement Mill Optimization: Practical Strategies for Enhanced OptimizeIT Expert Optimizer has successfully applied this technique and achieves more than 2 million hours, runtime in closed loop control every year As today, Expert Optimizer is Industrial : Optimization for the Cement Industry ABBCement ball mills typically have two grinding chambers The first chamber is filled with larger diameter grinding media and lined with lifting liners The first chamber coarsegrinds the feed Optimization of Cement Grinding Operation in Ball Mills PEC
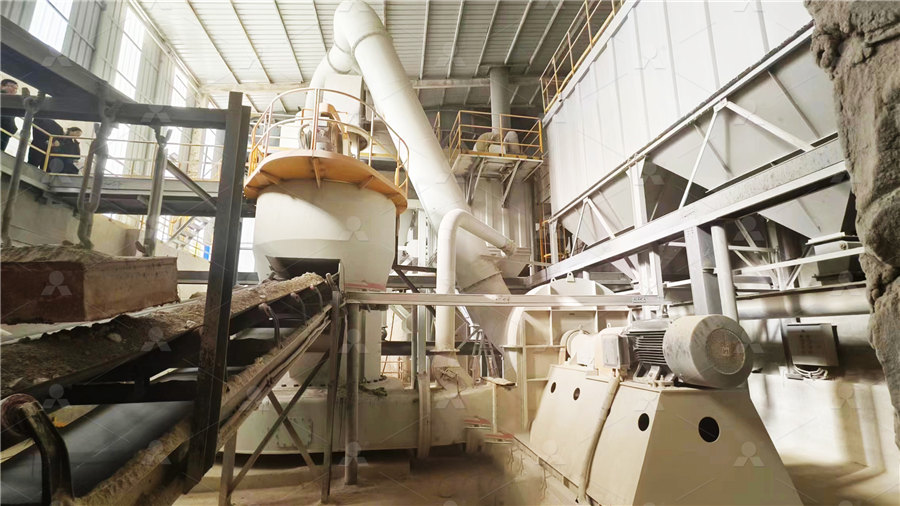
Cement grinding optimisation ScienceDirect
2004年11月1日 There are efficiency factors for dry grinding, open circuit ball milling, mill diameter, oversize feed, grinding finer than 75 μm and too large or too small reduction ratios 2015年4月1日 Production capacity of a fully airswept industrial scale twocompartment KHD Humboldt Wedag® cement ball mill was optimized with the aid of simulation It was proposed Optimization of a fully airswept dry grinding cement raw meal 2017年5月19日 Grinding is an essential operation in cement production given that it permits to obtain fine powder which reacts quickly with water, sets in few hours and hardens over a period of weeks i Overview of cement grinding: fundamentals, Reducing the clinker factor without compromising quality and the rising demand for highperformance cements are great challenges for the fine grinding technology used in cement plants As part of its green cement plant project, Let’s talk: polysius® booster mill – the next level in
.jpg)
Effects of Mill Speed and Air Classifier Speed on
2021年6月29日 The aim of this work was to observe the impact of the milling technique employed by the DESI 11 disintegrator on the properties of fly ash This type of mill is a highspeed pin mill with two In a correct operation the residue will be high initially, falling gradually as grinding progresses, which is not the case in the above graph Compare this with the milling progress as presented in Figure 4 after optimization The following picture shows the condition of the grinding media and the material in one of the grinding chambers of the Optimization of Cement Grinding Operation in Ball Mills PEC 2012年8月4日 grinding of clinker and gypsum in the finishin g mill, can account for more than 50% of a cement plant’s electricity consumption [Thi esen, 1993; Kohlhaas Laban, 1983] The m ostAn Overview of Cement production: How “green” and sustainable This document discusses optimizing cement separator and ball mill systems through periodic testing and evaluation It provides guidance on when and why to conduct optimization, including abnormal operations, poor performance, or high costs Conventional grinding systems and their main components are described The document then covers ball charge optimization factors Cement Separator Ball Mill Optimization PDF Mill (Grinding
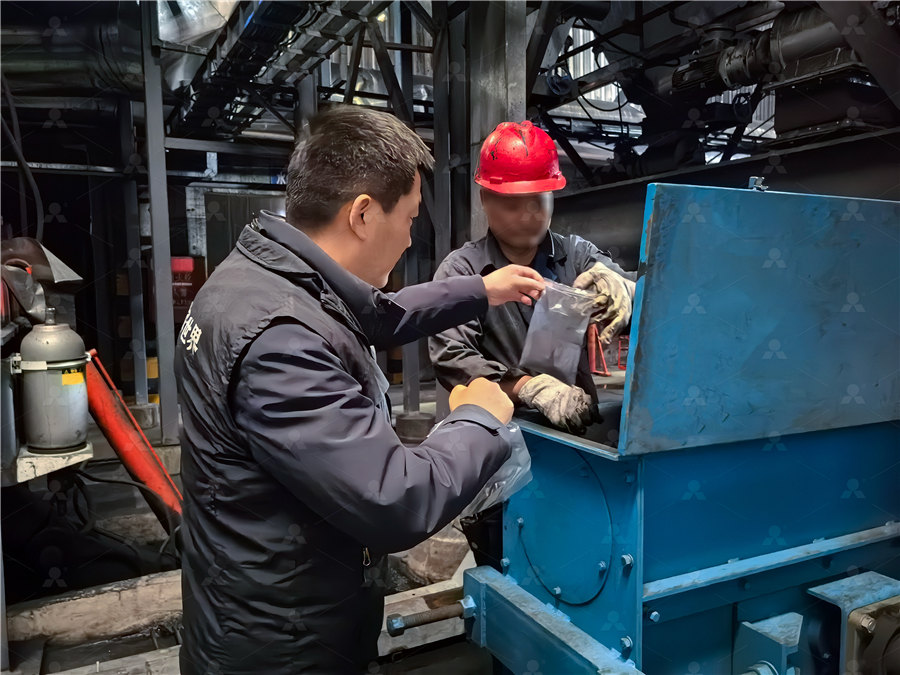
143 LOESCHE Mills For Cement and Granulated Blast Furnace Slag
The document discusses vertical roller mills for grinding cement clinker and granulated blast furnace slag It provides a brief history of Loesche's role in developing this technology from the 1930s to present Key points include Loesche selling the first mill for cement clinker in 1935, developing a patented tworoller mill configuration in 1994, and selling over 100 mills for 2018年8月1日 In fine grinding of cement in a ball mill, it is sometimes impractical to grind finer in a dry state Even though the chemical reactivity requires the material to be dry ground, it is sometimes Effect of Grinding Aids in Cement Grinding ResearchGate2018年7月1日 Among the industries, the nonmetallic industry was reported as the third largest energy user and accounted for about 12% of the global energy use [1]Within this portion, cement industry had the majority of the utilization with 85–12% [1], [2]US Energy Information Administration (EIA) [7] named cement industry as the most energy intensive among the Energy and cement quality optimization of a cement grinding circuitDownload scientific diagram Processing units and departments of a cement plant from publication: Mass customisation of process plants This case study describes how FLSmidth A/S, a Processing units and departments of a cement plant
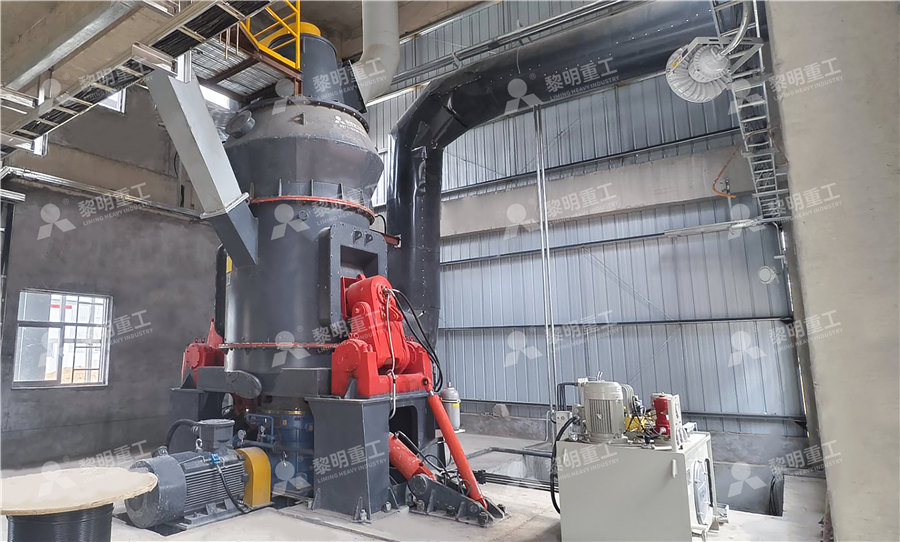
(PDF) Performance Evaluation of Vertical Roller Mill
2017年9月11日 PDF In this study, an extensive sampling study was carried out at vertical roller mill of ESCH Cement Plant in Luxemburg Samples were collected from Find, read and cite all the research 09 khd ball mill Free download as PDF File (pdf), Text File (txt) or view presentation slides online Separator 1520 Closed circuit mills with separator 1520 Double compartment mills 3040 Ball mills are commonly used for 09 KHD Ball Mill PDF Mill (Grinding) Bearing 2014年10月15日 1 Introduction Cement is an important material that its consumption has been steadily increasing depending on the construction business growing all around the globe [1]However, the manufacturing process is known as energy intense since the energy utilization is about 110–150 kW h per tonne of cement varying with the process modernization and raw The influences and selection of grinding chemicals in cement grinding 2022年12月23日 Even if cement is a wellconsolidated material, the chemistry of cement (and the chemistry inside cement) remains very complex and still nonobvious(PDF) An Insight into the Chemistry of Cement—A Review
.jpg)
Effect of Feed Amount and Composition on Blaine and Residue in Cement Mill
: Blaine fineness, residue, ball mill, grinding, cement Introduction: The world cement production has been increasing constantly since the early 1950s, especially in developing countries [1] Current world consumption of cement is about 15 billion tonnes per annum and it is increasing at about 1% per annum [2]High geometric precision: The molding process of mill balls adopts highprecision molding processes such as compression molding and injection molding, which can control the size, density, and shape of the balls to ensure their geometric accuracy and consistency, thereby improving the grinding efficiency and product quality of the ball mill Ball Mill Balls Manufacturing Of High Quality Ball Mill Ball2021年11月1日 Alloyed Ductile iron, austenitized at 840 °C for 30 min in a special sealed austempering furnace, was austempered for 30 min in molten salt mixture at 4 trial temperatures of 300 °C, 320 °C (PDF) Morphology and wear of high chromium andproduction costs as well as maintenance costs Ball mills and grinding tools Cement ball mills are typically twochamber mills (Figure 2), where the first chamber has larger media with lifting liners installed, providing the coarse grinding stage, whereas, in the second chamber, medium and fine grinding is carried outBALL MILLS Ball mill optimisation Holzinger Consulting
.jpg)
Grinding in Ball Mills: Modeling and Process Control Sciendo
55 known as the distribution function [45, 46]) describes the distribution of fragment sizes obtained after a breakage of particles of size xjThus, b1j, b2j, , bnj are the mass fractions of particles in size classes 1, 2, , n after a breakage of particles in size class j The mechanism of breakage is illustrated in [23] by a diagram shown in Fig 3A 6week modular course is designed to give the course attendee a solid understanding of the grinding system and its auxiliary equipment The purpose of the training is to Identify and understands necessary known and unknown information towards the completed cycle of the grinding system, whether it is a ball mill, vertical mill, or crushing processGRINDING TECHNOLOGY COURSE The Cement Institutedesign as our standard OK™ cement mill Energy efficient High capacity OK™ RAW MILL Optimum raw, cement and slag grinding BEST IN CLASS 0 200 400 600 800 1000 1200 1400 1600 1800 OK 373 OK 283 OK 776 OK 716 OK 666 OK 614 OK 564 OK 524 OK 434 OK 484 OK 404 OK 816 OK ™ raw mill production (t/h) FLSmidth Cement G u] OK RAW AND CEMENT MILL2004年1月14日 Growing population and development both increase the need for cement production 100 kW h/t specific energy consumption is rather high compared to the real cement manufacturing process Energysaving ultrafine grinding with the SALA Agitated Mill ZementKalkGips, 46 (9) (2002), pp 600601 Google Scholar [6]Open and closed circuit dry grinding of cement mill rejects in a
.jpg)
The impacts of dry stirred milling application on quality and
2020年8月15日 Throughout the studies, the data related to cement grinding process was collected from two different cement grinding circuits of Bursa Cement Plant/Turkey Turkish cement sector with 90 million tons of capacity is in the first place of European production, and third and fourth in export and production in the world rankings respectively ( Saka, 2019 )55 known as the distribution function [45, 46]) describes the distribution of fragment sizes obtained after a breakage of particles of size xjThus, b1j, b2j, , bnj are the mass fractions of particles in size classes 1, 2, , n after a breakage of particles in size class j The mechanism of breakage is illustrated in [23] by a diagram shown in Fig 3Grinding in Ball Mills: Modeling and Process Control SciendoThis document provides guidance on ball mill grinding processes It covers topics such as ball mill design including length to diameter ratios, percent loading, critical speed, and internals evaluation Methods for assessing ball charge, wear rates, and liner management are described Empirical relationships for power draw and grinding laws are presented The document also discusses Ball Mill Grinding Process Handbook2009年5月1日 Fig 5 shows the FTIR spectra of ground muscovite, TEA, and muscovite ground with 2000 g/t TEA The stretching vibration band of OH is detected between 3000 and 3600 cm 1 in the FTIR spectrum of Characterization of Various Cement Grinding Aids and their
.jpg)
Determination of correlation between specific energy consumption
2016年4月25日 In cement industry about 110 kWh of electrical energy is consumed to produce one ton of cement and about 26% of the total electrical power is used during farine productionGrinding aids for high performance cements Grinding aids are organic compounds that are added to the mill during cement grinding Their main purpose is to reduce the energy required to grind the clinker into a given fineness In addition, some products (usually referred to as performance enhancers) provide positive effect on cement hydration Grinding aids for high performance cements CADD MapeiThe Cement Production Process Milling of raw material and clinker is an area where power use is high, and the efficiency of grinding systems has been relatively low The efficiency of ball mills can be improved by modernising the internal components of the mill and fine tuning such things as the ball charge designThe Cement Production Process2015年4月1日 1 Introduction Airswept raw meal ball mills introduced by the cement mill manufacturers FLSmidth ® (Smidth, 2002), Polysius ® (Polysius, 2002) and KHD Humboldt Wedag® are the most commonly used onesKHD Humboldt Wedag® manufactured fully airswept raw meal mills which have two compartments used for drying and grinding processesOptimization of a fully airswept dry grinding cement raw meal
.jpg)
Overview of cement grinding: fundamentals,
2017年5月19日 Grinding is an essential operation in cement production given that it permits to obtain fine powder which reacts quickly with water, sets in few hours and hardens over a period of weeks i Reducing the clinker factor without compromising quality and the rising demand for highperformance cements are great challenges for the fine grinding technology used in cement plants As part of its green cement plant project, Let’s talk: polysius® booster mill – the next level in 2021年6月29日 The aim of this work was to observe the impact of the milling technique employed by the DESI 11 disintegrator on the properties of fly ash This type of mill is a highspeed pin mill with two Effects of Mill Speed and Air Classifier Speed on In a correct operation the residue will be high initially, falling gradually as grinding progresses, which is not the case in the above graph Compare this with the milling progress as presented in Figure 4 after optimization The following picture shows the condition of the grinding media and the material in one of the grinding chambers of the Optimization of Cement Grinding Operation in Ball Mills PEC
.jpg)
An Overview of Cement production: How “green” and sustainable
2012年8月4日 grinding of clinker and gypsum in the finishin g mill, can account for more than 50% of a cement plant’s electricity consumption [Thi esen, 1993; Kohlhaas Laban, 1983] The m ostThis document discusses optimizing cement separator and ball mill systems through periodic testing and evaluation It provides guidance on when and why to conduct optimization, including abnormal operations, poor performance, or high costs Conventional grinding systems and their main components are described The document then covers ball charge optimization factors Cement Separator Ball Mill Optimization PDF Mill (Grinding The document discusses vertical roller mills for grinding cement clinker and granulated blast furnace slag It provides a brief history of Loesche's role in developing this technology from the 1930s to present Key points include Loesche selling the first mill for cement clinker in 1935, developing a patented tworoller mill configuration in 1994, and selling over 100 mills for 143 LOESCHE Mills For Cement and Granulated Blast Furnace Slag 2018年8月1日 In fine grinding of cement in a ball mill, it is sometimes impractical to grind finer in a dry state Even though the chemical reactivity requires the material to be dry ground, it is sometimes Effect of Grinding Aids in Cement Grinding ResearchGate
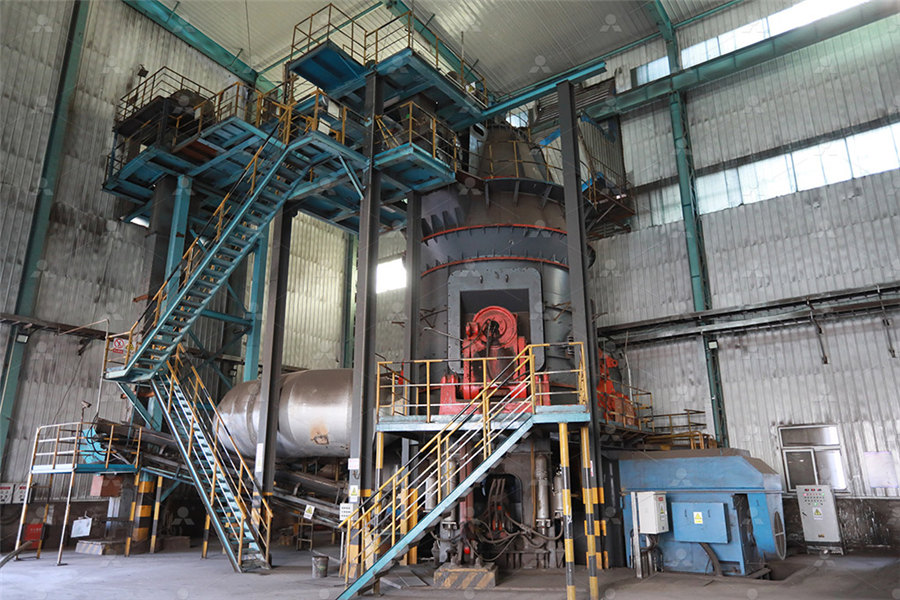
Energy and cement quality optimization of a cement grinding circuit
2018年7月1日 Among the industries, the nonmetallic industry was reported as the third largest energy user and accounted for about 12% of the global energy use [1]Within this portion, cement industry had the majority of the utilization with 85–12% [1], [2]US Energy Information Administration (EIA) [7] named cement industry as the most energy intensive among the Download scientific diagram Processing units and departments of a cement plant from publication: Mass customisation of process plants This case study describes how FLSmidth A/S, a Processing units and departments of a cement plant