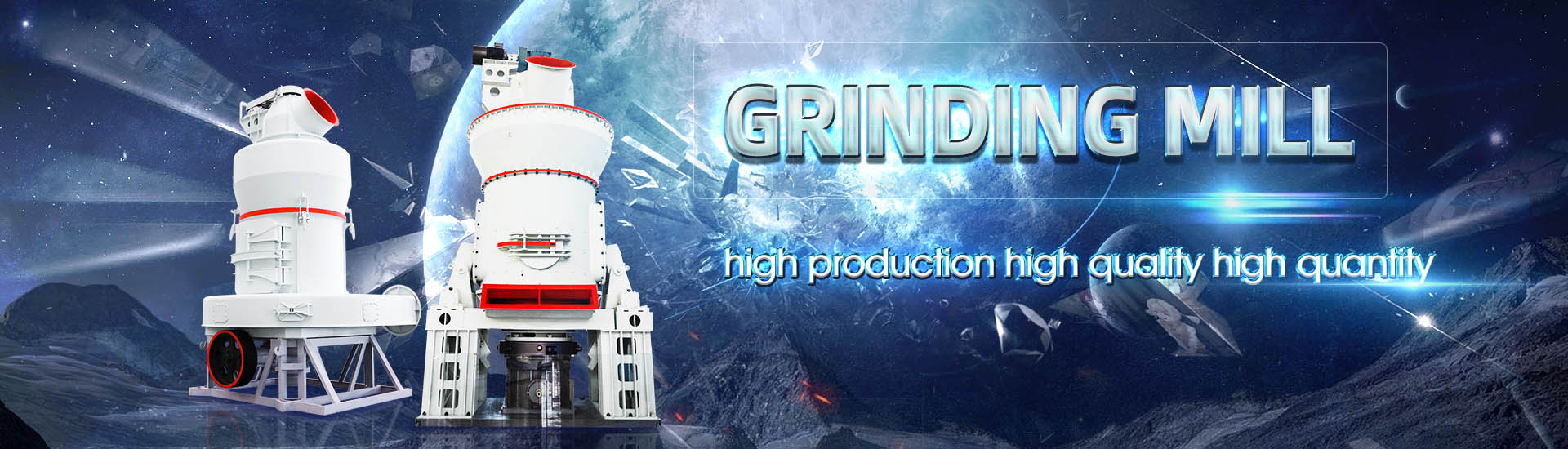
HOME→Will the ore grinding mill produce resonance when it is crushed on the bridge Will the ore grinding mill produce resonance when it is crushed on the bridge Will the ore grinding mill produce resonance when it is crushed on the bridge
Will the ore grinding mill produce resonance when it is crushed on the bridge Will the ore grinding mill produce resonance when it is crushed on the bridge Will the ore grinding mill produce resonance when it is crushed on the bridge
.jpg)
Ore Grinding SpringerLink
2023年7月20日 With a certain amount of grinding medium in the cylinder, when the cylinder rotates, the grinding medium is fluctuated to produce impact and grinding effects According to the ore discharging method, the grinding mill is divided into overflow type, grating type, and For example, hard materials like rocks need to be broken down into smaller pieces while soft materials like sand can be simply crushed The speed at which the ball is rotated: Ball mills are Factors affecting ores grinding performance in ball mills2019年1月1日 Theoretically, it has been proved that in the first case, quartz crystals accumulate more energy, and this effect is manifested mostly in terms of resonance For the first time, the Research into the crushing and grinding processes of iron ore with The ore is fed into the mill and as the cylinder rotates, the balls crush and grind the ore, causing the particles to break down in size Rod Mills: Rod mills operate on the same principle as ball Understanding the operation of grinding mills in the mining and
.jpg)
Ore Grinding Methods and Process of Ore Grinding
Ore grinding is a process to further reduce and disperse the ore particle size In the mineral processing industry, ore grinding is the particle size preparation before the separation of the 2013年4月1日 In the case of a ball mill the ore is crushed before it enters the mill, whereas a SAG mill receives runofmine (ROM) ore directly (Stanley, 1987) A SAG mill in a singlestage Analysis and validation of a runofmine ore grinding mill circuit A simple and novel nonlinear model of a runofmine ore grinding mill circuit, developed for process control and estimation purposes, is validated The model makes use of the minimum Analysis and validation of a runofmine ore grinding mill circuit 2020年10月13日 The performance of grinding mills depends on many operating factors among which are the time of grinding, mill speed, grinding mediatoore ratio, and filling ratio These THE EFFECTS OF PROCESS VARIABLES ON THE GRINDING OF
.jpg)
THE EFFECTS OF PROCESS VARIABLES ON THE GRINDING OF
Grinding is the highest energy consumer in all the unit processes of mineral beneficiation The performance of grinding mills depends on many operating factors among which are the time of 2023年7月22日 Ore crushing is the process of breaking, splitting, extrusion, impacting, and grinding of large solid ore with external force to reduce the particle size of large ore materials Ore Crushing SpringerLink2018年8月17日 The concept of ore blending is a very relevant notion in modern high tonnage production mines It is not only essential for the prolongation of the mine life of the concerned mine but as well as a The effects of ore blending on comminution operation (1) Structure parameters of grinding mill, including its specifications, model, aspect ratio, ore discharging method, and liner form (2) Various working parameters of grinding mill, including fraction of critical speed for grinding mill, filling rate for grinding mill, grinding concentration,grindingcycleload,etc(3)AndgrindOre Grinding Methods and Process of Ore Grinding
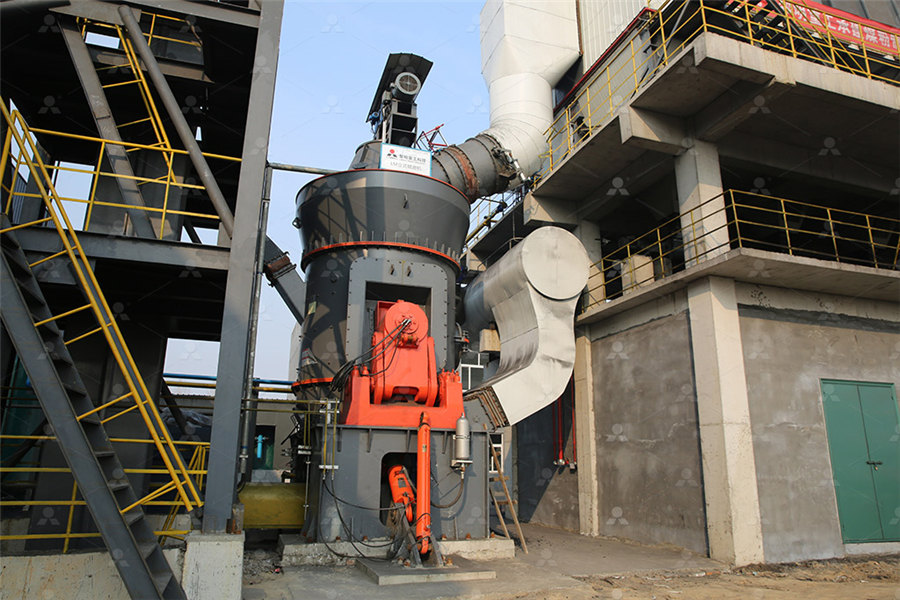
Analysis and validation of a runofmine ore grinding mill circuit
2013年4月1日 However, a lot of academic applications have been developed using Matlab/Simulink R le Roux et al (2013) proposed and validated a novel and simple nonlinear model, Sbárbaro (2010), Liu and A crushing plant delivered ore to a wet grinding mill for further size reduction The size of crushed ore (F 80) was 40 mm and the SG 28 t/m 3 The work index of the ore was determined as 122 kWh/t A wet ball mill 1 m × 1 m was chosen to grind the ore down to 200 micronsGrinding Mill an overview ScienceDirect Topics2023年10月27日 The ball mill is a rotating cylindrical vessel with grinding media inside, which is responsible for breaking the ore particles Grinding media play an important role in the comminution of mineral A Review of the Grinding Media in Ball Mills for Mineral Processing2022年5月23日 Grinding experiments were conducted in a laboratoryscale stirred mill on a lowgrade PGE bearing chromite ore HighPressure Grinding Rolls (HPGR) product of −1 mm was used as feed material to Modeling and application of stirred mill for the coarse grinding
.jpg)
Analysis and validation of a runofmine ore grinding mill circuit
which use both ore and steel balls as grinding media (Wei and Craig, 2009b) In the case of a ball mill the ore is crushed before it enters the mill, whereas a SAG mill receives runofmine (ROM) ore directly (Stanley, 1987) A SAG mill in a singlestage closed circuit con guration, as shown in Fig 1, is considered for this study A description2015年3月15日 For the grinding tests, a Loesche mill LM45 (table diameter 045 m) is used (Fig 2a) This pilot scale mill is a special development for ore grinding, which is reflected by several features The mill has four rollers, which are able to stress the particle bed with grinding pressures of up to 5000 kN/m 2Research of iron ore grinding in a verticalrollermill2017年4月28日 Testing Plant Equipment: In order to determine, among other things, the operating conditions of the ballmill when working on this rock, a test mill of about 300 T daily capacity was erected at Duluth, MinnThe finecrushing plant contains a Hardinge 8ft by 22in (24m by 558cm) conical mill, a 6 by 27ft (18 by 82m)Ball Mill Grinding Theory – Crushing Motion/Action InsideGrinding Mills: Ball Mill Rod Mill Design PartsCommon types of grinding mills include Ball Mills and Rod Mills This includes all rotating mills with heavy grinding media loads This article focuses on ball and rod mills excluding SAG and AG mills Although their concepts are very similar, they are not discussed herePhotographs of a glass ended laboratory ball mill show Grinding Mills 911Metallurgist
.jpg)
Ore Grinding SpringerLink
2024年1月1日 Therefore, the rod mill is mostly used for coarse grinding of the previous period of ball mill, or grinding of brittle materials and materials against overcrushing, such as tungsten and tin ore before gravity separation; and (3) autogenous mill – it refers to the materials which themselves are collided and ground mutually to be crushed when the grinding mill rotates, and 2020年10月13日 The results of the analyses clearly show that using a sieve of +180µm and its bottom180µm, the best time for grinding 05kg of Itakpe iron ore with 3kg of grinding media and a mill speed of 92 THE EFFECTS OF PROCESS VARIABLES ON THE GRINDING OF IRON ORE Table 1 Chemical composition of typical grinding media (% wt) Adapted from [24] 211 Cast Iron Cast iron can be grey cast iron or white cast iron, but white cast irons are commonly used in Grinding Media in Ball MillsA Review ResearchGate2022年1月1日 As a result, calculating power (or energy) is one of the essential factors in estimating operating costs and determining the best operating conditions for ball mills [4]Effect of grinding media on the milling efficiency of a ball mill

Analysis and validation of a runofmine ore grinding mill circuit
2013年4月1日 Two types of mills commonly found in the minerals processing industry are ball and semiautogenous (SAG) mills, which use both ore and steel balls as grinding media (Wei and Craig, 2009b)In the case of a ball mill the ore is crushed before it enters the mill, whereas a SAG mill receives runofmine (ROM) ore directly (Stanley, 1987)A SAG mill in a singlestage 2021年1月14日 Ball Mill Work Index tests using crushed feed, and Standard Autogenous Grinding Design (SAGDesign) Tests, patented by Outokumpu (See reference 8 below) The comparison of these results gives context to how the various measurements relate to each other and how they can be used to obtain an accurate design for the grinding mills required forComparison of Ore Hardness Measurements for Grinding Mill 2023年1月1日 The grinding parameters were determined and used to calculate T g (i), the time required for an ore of type i to reach d rr = 45 µm in a Bond laboratory ball mill The experiments illustrate the applied method, show the quality at which the laboratory grinding is modelled and how this quality depends on the assumptions made beforehandA prediction of blend grinding result based on individual ore size 2023年1月1日 The grinding section of the pelletizing plant of Tata Steel’s integrated steel works in IJmuiden (the Netherlands) consists of three parallel dry grinding lines with a capacity of 180–230 t/hr each (Fig 1)The heart of the lines is a combined rotary dryer and ball mill (Fig 2)The purpose of the installation is to supply a dry mineral mix of constant size distribution to A prediction of blend grinding result based on individual ore size
.jpg)
HIGH PRESSURE GRINDING ROLLS—A PROMISING AND COST
GR Polycom24/17 to implement pretreatment of SAG mill feed and concurrently produce crushed stone In recent years stronger ore is expected to come and productivity decline is anticipated; for this reason, HPGR have been timely installed as a preact At the present time, two HPGR Polycom20/15 areWhen iron ore is extracted from a mine, it must undergo several processing stages Six steps to process iron ore 1 Screening We recommend that you begin by screening the iron ore to separate fine particles below the crusher’s CSS before the crushing stageThe six main steps of iron ore processing Multotec2016年1月1日 In wet grinding practice, highstress abrasion occurs over a small region when ore particles are trapped between the grinding balls and the mill liner, and the load is sufficient to fracture A comparison of wear rates of ball mill grinding 2016年1月1日 It has been observed by many authors that the breakage rates of coarse particles in a ball mill slow down with increasing grinding time and deviate from the first orderFirstorder and secondorder breakage rate of
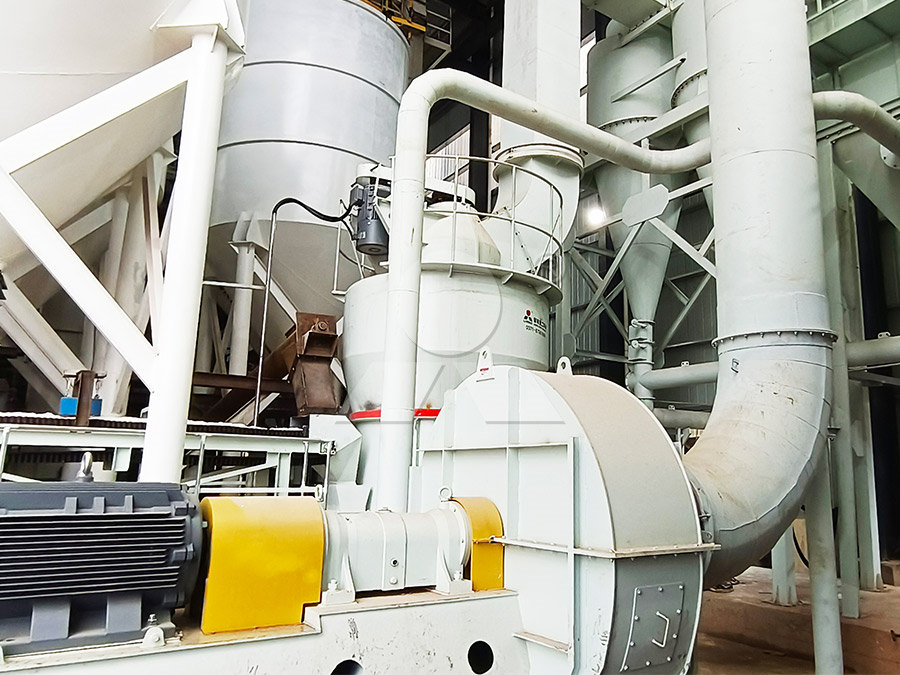
The Effect of Grinding Media on Mineral Breakage
2021年12月11日 In experiments done by Si et al [98] using magnetite ores to determine the effect of grinding media diameter on the mineral liberation degree, 8 different sizes of steel balls were used ie 2015年10月20日 This is based on the understanding that grinding media directly affects energy consumption, product size, and consequently the grinding costs [9], and that proper selection of the grinding media INVESTIGATION OF EFFECTS OF GRINDING MEDIA SHAPES TO THE GRINDING 2022年3月19日 An iron ore concentrate sample was ground separately in a pilotscale HPGR mill in multiple passes and a dry opencircuit ball mill to increase the specific surface area of particlesGrinding iron ore concentrate by using HPGR and ball mills and 2017年1月1日 An increase of over 10% in mill throughput was achieved by removing the ball scats from a single stage SAG mill These scats are non spherical ball fragments resulting from uneven wear of balls (PDF) Performance optimization of an industrial ball mill for
.jpg)
Comminution and classification technologies of iron ore
2022年1月1日 The crushed ore then enters a grinding circuit consisting of six grinding mill lines Each line consists of a 122 m (40 ft) diameter × 11 m (36 ft) long AG mill with a 28 MW gearless motor in closed circuit with a pebble crusher and primary classifying cyclonesfrom the ores The grinding of ore is a highly energyintensive process [1–4] In this process, the size of the particle obtained depends on the energy consumption of the ball mill The major challenge encountered in the process of iron ore grinding is to maintain the desired product particle size distribution (PSD) with sufficientEstimation of Grinding Time for Desired Particle Size Distribution2017年6月2日 Autogenous grinding (AG) and semiautogenous grinding (SAG) mills use the material to be ground as the grinding media Autogenous grinding mills use larger rocks to impact and break smaller rocks as the mill rotates Semiautogenous mills are basically the same autogenous mills, but with the addition of balls, similar to those in ball millsHow it Works: Crushers, Grinding Mills and Pulverizers2017年1月6日 Grinding coarse ore in a ballmill is done by steel balls of three sizes (5, 4, and 3 inches); fine ore is ground in a tubemill by 2 and 1½inch balls or by flint pebbles or by hard, rounded mine rock such as quartzite These grinding media wear to small sizes, and new ones must be added regularly to make up the weightBasic Ball Mill Grinding Circuit 911Metallurgist
.jpg)
The effects of ore blending on comminution
2018年8月17日 The concept of ore blending is a very relevant notion in modern high tonnage production mines It is not only essential for the prolongation of the mine life of the concerned mine but as well as a operation (1) Structure parameters of grinding mill, including its specifications, model, aspect ratio, ore discharging method, and liner form (2) Various working parameters of grinding mill, including fraction of critical speed for grinding mill, filling rate for grinding mill, grinding concentration,grindingcycleload,etc(3)AndgrindOre Grinding Methods and Process of Ore Grinding2013年4月1日 However, a lot of academic applications have been developed using Matlab/Simulink R le Roux et al (2013) proposed and validated a novel and simple nonlinear model, Sbárbaro (2010), Liu and Analysis and validation of a runofmine ore grinding mill circuit A crushing plant delivered ore to a wet grinding mill for further size reduction The size of crushed ore (F 80) was 40 mm and the SG 28 t/m 3 The work index of the ore was determined as 122 kWh/t A wet ball mill 1 m × 1 m was chosen to grind the ore down to 200 micronsGrinding Mill an overview ScienceDirect Topics
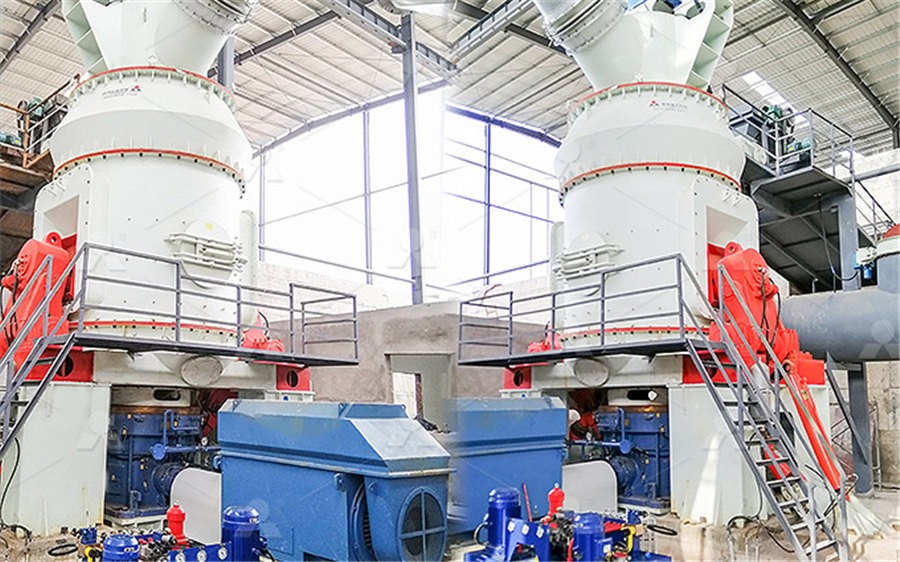
A Review of the Grinding Media in Ball Mills for Mineral Processing
2023年10月27日 The ball mill is a rotating cylindrical vessel with grinding media inside, which is responsible for breaking the ore particles Grinding media play an important role in the comminution of mineral 2022年5月23日 Grinding experiments were conducted in a laboratoryscale stirred mill on a lowgrade PGE bearing chromite ore HighPressure Grinding Rolls (HPGR) product of −1 mm was used as feed material to Modeling and application of stirred mill for the coarse grinding which use both ore and steel balls as grinding media (Wei and Craig, 2009b) In the case of a ball mill the ore is crushed before it enters the mill, whereas a SAG mill receives runofmine (ROM) ore directly (Stanley, 1987) A SAG mill in a singlestage closed circuit con guration, as shown in Fig 1, is considered for this study A descriptionAnalysis and validation of a runofmine ore grinding mill circuit 2015年3月15日 For the grinding tests, a Loesche mill LM45 (table diameter 045 m) is used (Fig 2a) This pilot scale mill is a special development for ore grinding, which is reflected by several features The mill has four rollers, which are able to stress the particle bed with grinding pressures of up to 5000 kN/m 2Research of iron ore grinding in a verticalrollermill
.jpg)
Ball Mill Grinding Theory – Crushing Motion/Action Inside
2017年4月28日 Testing Plant Equipment: In order to determine, among other things, the operating conditions of the ballmill when working on this rock, a test mill of about 300 T daily capacity was erected at Duluth, MinnThe finecrushing plant contains a Hardinge 8ft by 22in (24m by 558cm) conical mill, a 6 by 27ft (18 by 82m)Grinding Mills: Ball Mill Rod Mill Design PartsCommon types of grinding mills include Ball Mills and Rod Mills This includes all rotating mills with heavy grinding media loads This article focuses on ball and rod mills excluding SAG and AG mills Although their concepts are very similar, they are not discussed herePhotographs of a glass ended laboratory ball mill show Grinding Mills 911Metallurgist