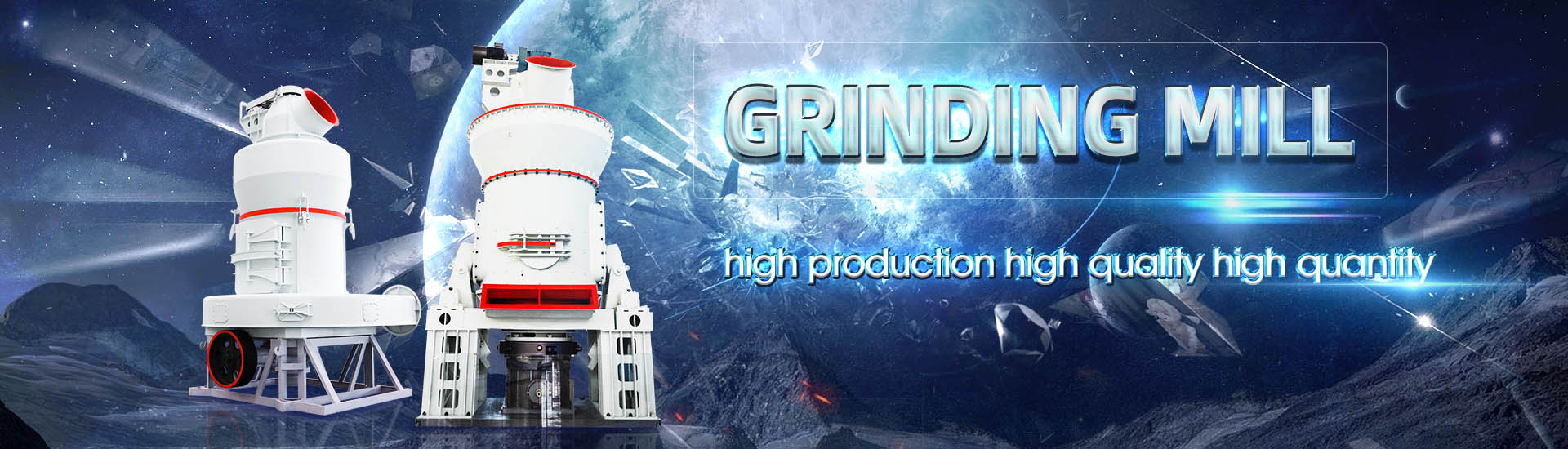
Coal mill capacity is prone to wear due to wind
.jpg)
Coal Mill an overview ScienceDirect Topics
Coal mills or pulverizers play a very essential part in the coalfired power production system Coal mills grind the coal into fine powder, and the primary air entering the mill dries and drives the coal into the power plant furnace for combustion Mills can be a bottleneck for the power generation 1997年8月1日 The consequences of mill wear are that it alters the mill coal grindability, increases the coal grinding residence time and the mill becomes sluggish in responding to the Analysis of coal Mill Dynamic Characteristics Under Normal and 2020年8月12日 Obtained results indicate that grinding pressure, primary air (PA) temperature and mill motor current have a tendency to rise by increasing coal feeding mass flow rates for An investigation of performance characteristics and energetic Bentek study (April 2010) claims coal cycling results in increases in total SO2, NOx and CO2 emissions in Xcel/PSCO and ERCOT Xcel refutes (May 2010) this, saying they have added How Does Wind Affect Coal? Cycling, Emissions, and Costs
.jpg)
WEAR ANALYSIS OF VERTICAL COAL MILL PLATE APS
Some VCM components are prone to wear, such as hammer crushers, grate plates, and lining plates It is caused by friction between the material being produced, those passing2019年11月27日 Derate Analysis and Operating Concerns • Pulverizer capacity limitation : A derate is due to the fuel burn rate exceeding predicted pulverizer capacity with all pulverizers The Coal mill performance monitoring PPT SlideShareKey aspects covered include the different principles of grinding, types of pulverizers, performance criteria such as fineness and factors affecting capacity The document also discusses wear Coal Mill in Thermal Power Plant PDF Mill (Grinding) Coal Scribd1996年3月1日 This project found that the coal property giving the best initial indication of likely component wear in high speed, medium speed, or low speed mills was the coal abrasiveness Component wear in vertical spindle mills grinding coal
.jpg)
Flexible Coal: An Example Evolution from Baseload to Peaking Plant
Flexibility of operation—the ability of a power system to respond to change in demand and supply—is a characteristic of all power systems Flexibility is especially prized in twentyfirst 2019年9月11日 Thus, retrofitting existing coalfired power plants with steam extraction and thermal energy storage is a promising option to accommodate the high penetration of wind Flexible Operation of Retrofitted CoalFired Power Plants to Coal Mills are the Heart of a Coal Fired Plant Maximum capacity, This area is often described as the underbowl, undertable, reject area, pyrite area or primary air inlet wind box depending on the type of mill high volatile matter and highly reactive coals are prone to self heating and can spontaneously ignite due to rewettingMill Inerting Systems Presentation to the ASBCUG2020年6月29日 6 TYPES OF COAL PULVERIZER • Tube or ball mills: Lowspeed machines that grind the coal with steel balls in a rotating horizontal cylinder If the diameter of the cylinder is greater than the length of the classifications and working of mills in a power plant
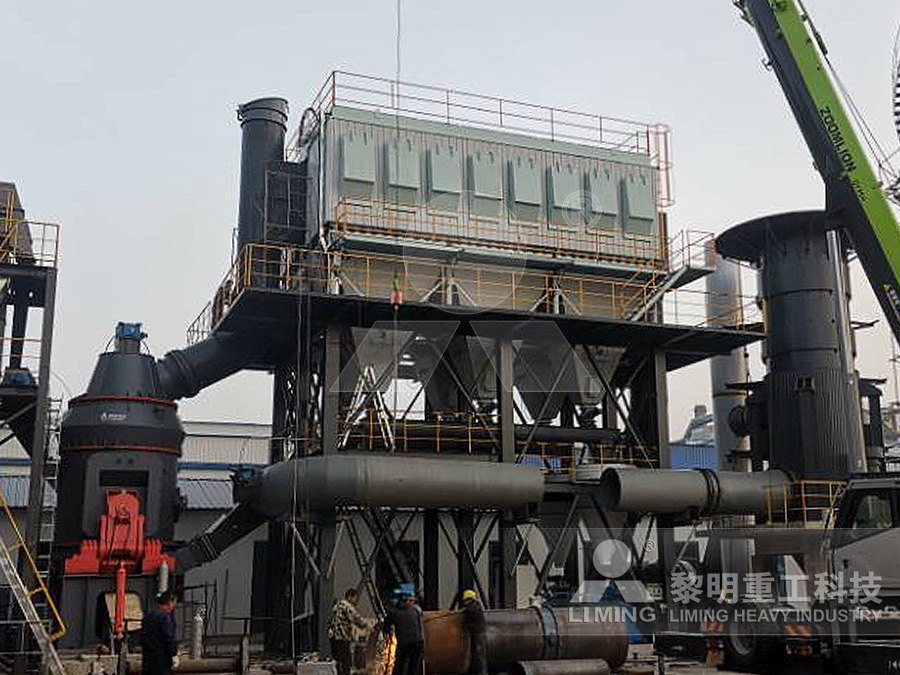
Nonlinear coal mill modeling and its application to model
2013年3月1日 This limit is imposed by the size of the coal mill and by the available grinding capacity of the rollers The parameter BR 1 can be used to simulate a deterioration of the roller performance (eg due to wear damage) The third term in Eq2019年11月27日 12 Capacity • For example, consider a 100 KPPH (45360 kg/hr) pulverizer which was designed for a Hardgrove Grindability Index (HGI) of 60, a surface moisture of less than 10%, and a feed size of 25" • The 100 KPPH (4536 T/hr) rating means that operating at those stated conditions the pulverizer product will have a fineness of 70% through a 200 mesh The Coal mill performance monitoring PPT SlideShareOur ATOX® Coal Mill has large rollers with great grinding capability of virtually all types of raw coal The rollers work harmoniously with a highlyefficient separator and feed sluice to consistently and reliably deliver coal meal to your desired fineness and moisture levelATOX® Coal Mill FLSmidth Cement2013年2月1日 Wear mechanisms in a coal pulveriser Compression, abrasion and impact are the three wear mechanisms that act upon the grinding elements and the pulveriser internals Compression is a wear component that results from the crushing of the material upon itself (attrition) between the grinding elements, ie between the tyres/rolls and the tableCoal pulverisation with vertical roller mills Engineer Live
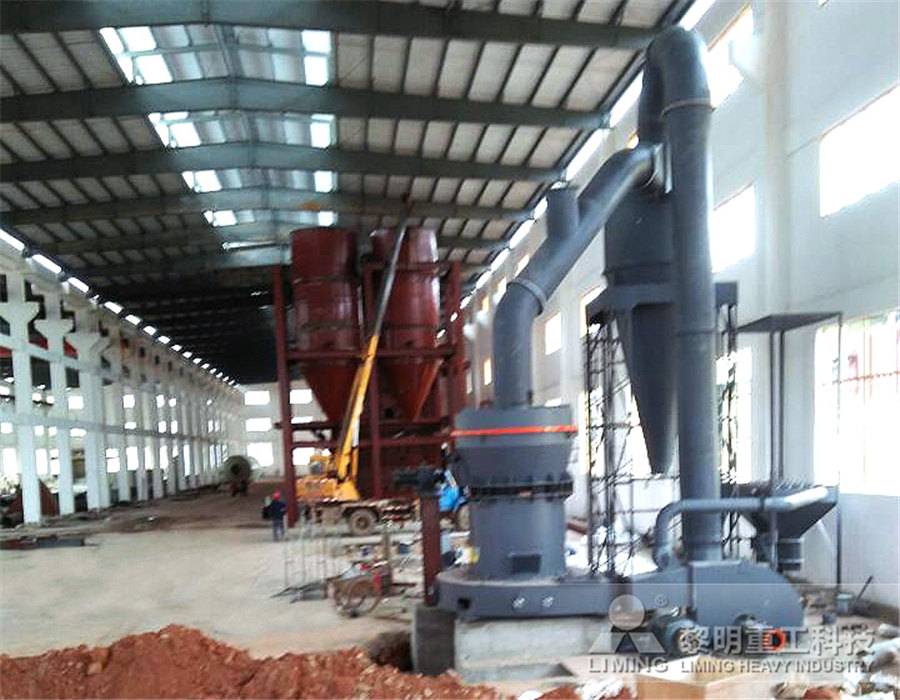
Coal Mill in Thermal Power Plant PDF Mill (Grinding) Scribd
Coal Mill in Thermal Power Plant Free download as Word Doc (doc / docx), PDF File (pdf), Text File (txt) or read online for free This document discusses coal pulverizers/mills which are critical components that convert the stored energy in coal into electricity There are various types of pulverizers that primarily utilize grinding, drying, classification and circulation processescoal mill Free download as Powerpoint Presentation (ppt), PDF File (pdf), Text File (txt) or view presentation slides online This document discusses maintenance of coal mills and coal feeders Key points include: Maintenance is important to improve reliability, efficiency and reduce downtime Wear parts include grinding rolls, bull ring segments, and separator body linersCoal Mill PDF Mill (Grinding) Troubleshootinggeneration industry due to its ability to dry higher moisture coals and wide range of capacity Typically each mill supplies the finely ground coal particles to the boiler through four to six CFD Modeling of MPS Coal Mill for Improved Performance and 2020年4月2日 This case indicates and measures the changes of boiler parameters due to different mill in service Mill capacity with coal B worst 66 t/h 5 Number of grinding Journal 3 (with splash Analysis of the Coal Milling Operations to the Boiler Parameters
.jpg)
Coal Mill Modeling for Monitoring and Control (Extended Abstract)
2011年1月1日 The main performance indicator will be the level of wear in the grinding elements which will show up as a degradation in the grinding rate parameters Potential faults that can be detected includes plugging in the feed system due to excessive moisture and mill chocking due to capacity restrictions 32024年5月1日 The model is utilized to predict the future state variable values of the coal mill through multi step time sequence prognosis Furthermore, it detects the abnormality of the coal mill as a whole through the deviation distance between the real value and the predicted value A dual warning method is thus developed to warn of coal mill failuresDual fault warning method for coal mill based on ScienceDirect2024年5月1日 In this section, a case study of a coal mill in a thermal power plant located in the eastern China is presented The coal mill operating status variables are measured by pressure sensors, RTD temperature sensors, and so on Then, the measurement data is transmitted to the DCS for storageDual fault warning method for coal mill based on ScienceDirectPerformance optimization of 1800MT capacity stacker Reclaimer in coal handling plant in 600MW/660MW sub/super critical units SN Dubey, idlers, paddle feeders crushers, screens, stacker reclaimer, due to which more prone to maint spares parts consumption Rail Bobron Coal is unloaded from Wind out of OperationPerformance optimization of 1800MT capacity stacker Reclaimer in coal
.jpg)
Waste Coal: How to Avoid Flow Stoppages During Storage and Handling
2007年10月1日 Most waste coals tend to have large amounts of fines Because up to 50 percent of the composition can be ash (and for many waste coals a large portion of this ash is clay) waste coals tend to be 2011年7月6日 Thermal power plants in India are facing the problem of forced outages due to unexpected boiler tube failures Fly Ash Erosion (FAE) is one of the prime reasons for these failures(PDF) Use of Cold Air Velocity Test (CAVT) to Locate Erosion Prone 2017年1月1日 It is estimated that only 10% of bearings are appropriately functioning without any failure till their life cycle, while 90% of bearings failures include insufficient lubrication (30%), poor (PDF) Wear Analysis of Wind Turbine Bearings ResearchGate– Lower rank coals are generally more easily ignited inside the coal mill – High volatile matter and highly reactive coals encourage preignition inside the mill – Higher moisture content requires temperature extremes inside the mill – High moisture, high volatile matter and highly reactive coals are prone to self heating and canMill Inerting and Pulverizer/Mill Explosion Mitigation
.jpg)
Damage to coal power plants due to cyclic operation
2014年1月1日 As shown in Eq 132, creep–fatigue interactions can be correlated with the C* parameter An example is shown in Fig 132, which shows good correlation of experimental and prediction of the creep–fatigue crack growth rates for a wide range of steels and hold timesThere are some inaccuracies, or scatter, however, mainly due to the assumption of steadystate 2020年1月1日 Due to the blockage in the coal mill, the amount of coal powder entering the boiler will be lower than the coal supply , thus decreasing the main steam pressure and the unit loadEarly Warning of Critical Blockage in Coal Mills Based on coal pile) a 055 001 16 10 Uncrusted coal pile a 112 03 23 21 Scraper tracks on coal pile a,b 062 006 15 12 Fine coal dust on concrete pad c 054 02 11 10 a Western surface coal mine Reference 2 b Lightly crusted c Eastern power plant Reference 3 The fastest mile of wind for the periods between disturbances may be 1325 Industrial Wind Erosion2023年10月1日 Wear of inner ring and outer ring; rusty discoloration of outer ring: Axial load; radial load: Fretting wear; electrical erosion: 1 Improper selection or design: 2005/ [49] 58: Highpower marine gearbox: Cylindrical roller bearing: Wear, agglutination and plasticity flow of inner ring, outer ring and roller: Vibration load: Fretting fatigue: 1A review of bearing failure Modes, mechanisms and causes

(PDF) Literature Review of Wind Turbines
2018年11月15日 First wind mill built by Charles Brush in 1888 [6] wind capacity has been observed to 10% in 2017 [2][3] wind turbines due to variations and unavailability of consistent wind speeds in the2021年3月31日 3 COAL QUALITY –IMPACT COMPLEX • Pulverizer capacity, fineness wear • Slagging fouling in boiler • Corrosion erosion in boiler • Ash characteristics affect efficient collection in ESP • Affects furnace convective pass heat absorption boiler availability • Quantification of impact is complex 31Mar2021 total output power solutions 3Effect of Coal Quality and Performance of Coal pulverisers / Mills2016年9月1日 Furthermore, VRM separator speed (rpm) is one of the key operational parameters that determines product particle size Increasing the classi er rotor speed from 60 to 80 rpm decreases the particle Operational parameters affecting the vertical roller mill 2022年5月31日 The coal mill is one of the important auxiliary equipment of thermal power units Power plant performance and reliability are greatly influenced by the coal mill To avoid abnormal operating conditions of coal mills in time and effectively, a dual fault warning method for coal mill is A brannew performance evaluation model of coal mill based on
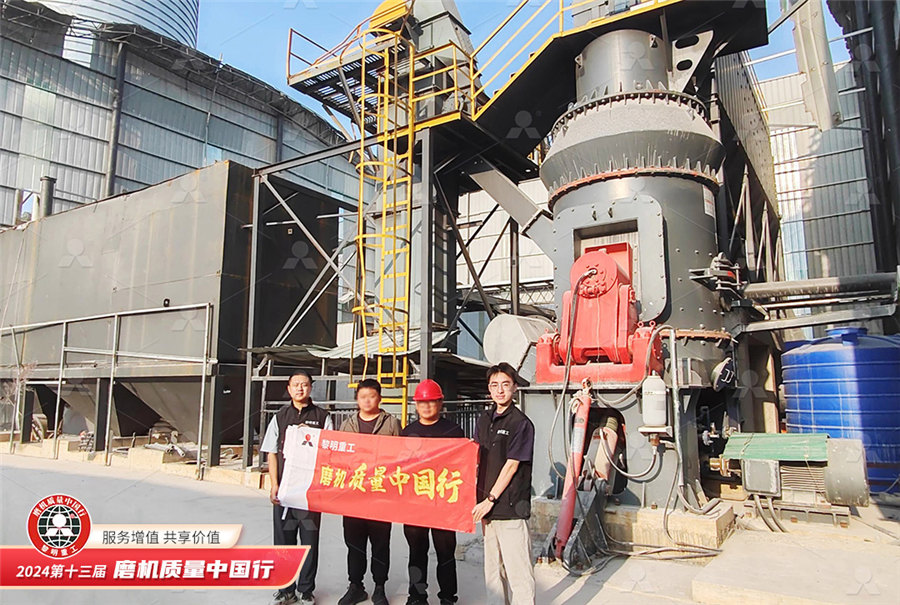
(PDF) Risk assessment of hazards due to the installation and
PDF On Feb 1, 2018, Albara M Mustafa and others published Risk assessment of hazards due to the installation and maintenance of onshore wind turbines Find, read and cite all the research you 2005年12月1日 The wear of tumbling mill liners influences the load behaviour and consequently the performance and efficiency of tumbling mills The ability to accurately predict the evolving mill liner profile Discrete element method (DEM) modelling of evolving mill Once complete Company will have a combined capacity of 9900 MW or close to 7% of India’s installed power capacity Stage 1 : 660 MW Stage 2 : 660 MW Stage 3 : 1320 MW Stage 4 : 1980 MW Product : XL CC 590 – QTY : 2000KG; XL CC610 – QTY : 500 KG; Coal Mill Capacity : 70 TPH No of Mill : 52 MILLSIn situ Reconditioning of Coal Mill Tyre WearresistLubrication protects wind turbines from premature wear of many critical parts so they operate at maximum performance for greater In wind turbines, micropitting occurs due to a constantly changing load In Typically, the oil fill volume is 60% of the gearbox capacity Likewise, the frequency also varies based on the condition How Much Oil Do Wind Turbines Use? – Wind Turbine Magazine
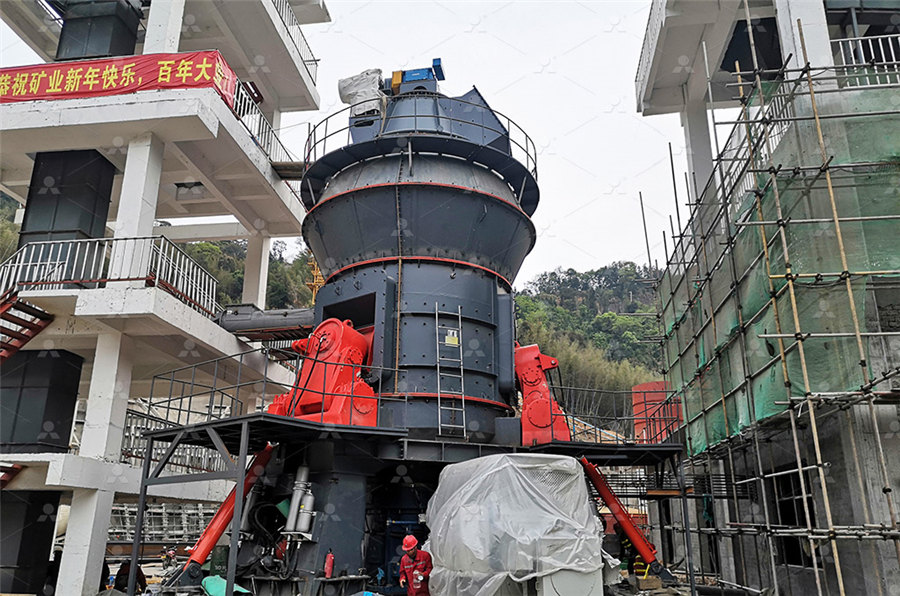
Mill Inerting Systems Presentation to the ASBCUG
Coal Mills are the Heart of a Coal Fired Plant Maximum capacity, This area is often described as the underbowl, undertable, reject area, pyrite area or primary air inlet wind box depending on the type of mill high volatile matter and highly reactive coals are prone to self heating and can spontaneously ignite due to rewetting2020年6月29日 6 TYPES OF COAL PULVERIZER • Tube or ball mills: Lowspeed machines that grind the coal with steel balls in a rotating horizontal cylinder If the diameter of the cylinder is greater than the length of the classifications and working of mills in a power plant2013年3月1日 This limit is imposed by the size of the coal mill and by the available grinding capacity of the rollers The parameter BR 1 can be used to simulate a deterioration of the roller performance (eg due to wear damage) The third term in EqNonlinear coal mill modeling and its application to model 2019年11月27日 12 Capacity • For example, consider a 100 KPPH (45360 kg/hr) pulverizer which was designed for a Hardgrove Grindability Index (HGI) of 60, a surface moisture of less than 10%, and a feed size of 25" • The 100 KPPH (4536 T/hr) rating means that operating at those stated conditions the pulverizer product will have a fineness of 70% through a 200 mesh The Coal mill performance monitoring PPT SlideShare
.jpg)
ATOX® Coal Mill FLSmidth Cement
Our ATOX® Coal Mill has large rollers with great grinding capability of virtually all types of raw coal The rollers work harmoniously with a highlyefficient separator and feed sluice to consistently and reliably deliver coal meal to your desired fineness and moisture level2013年2月1日 Wear mechanisms in a coal pulveriser Compression, abrasion and impact are the three wear mechanisms that act upon the grinding elements and the pulveriser internals Compression is a wear component that results from the crushing of the material upon itself (attrition) between the grinding elements, ie between the tyres/rolls and the tableCoal pulverisation with vertical roller mills Engineer LiveCoal Mill in Thermal Power Plant Free download as Word Doc (doc / docx), PDF File (pdf), Text File (txt) or read online for free This document discusses coal pulverizers/mills which are critical components that convert the stored energy in coal into electricity There are various types of pulverizers that primarily utilize grinding, drying, classification and circulation processesCoal Mill in Thermal Power Plant PDF Mill (Grinding) Scribdcoal mill Free download as Powerpoint Presentation (ppt), PDF File (pdf), Text File (txt) or view presentation slides online This document discusses maintenance of coal mills and coal feeders Key points include: Maintenance is important to improve reliability, efficiency and reduce downtime Wear parts include grinding rolls, bull ring segments, and separator body linersCoal Mill PDF Mill (Grinding) Troubleshooting
.jpg)
CFD Modeling of MPS Coal Mill for Improved Performance and
generation industry due to its ability to dry higher moisture coals and wide range of capacity Typically each mill supplies the finely ground coal particles to the boiler through four to six 2020年4月2日 This case indicates and measures the changes of boiler parameters due to different mill in service Mill capacity with coal B worst 66 t/h 5 Number of grinding Journal 3 (with splash Analysis of the Coal Milling Operations to the Boiler Parameters