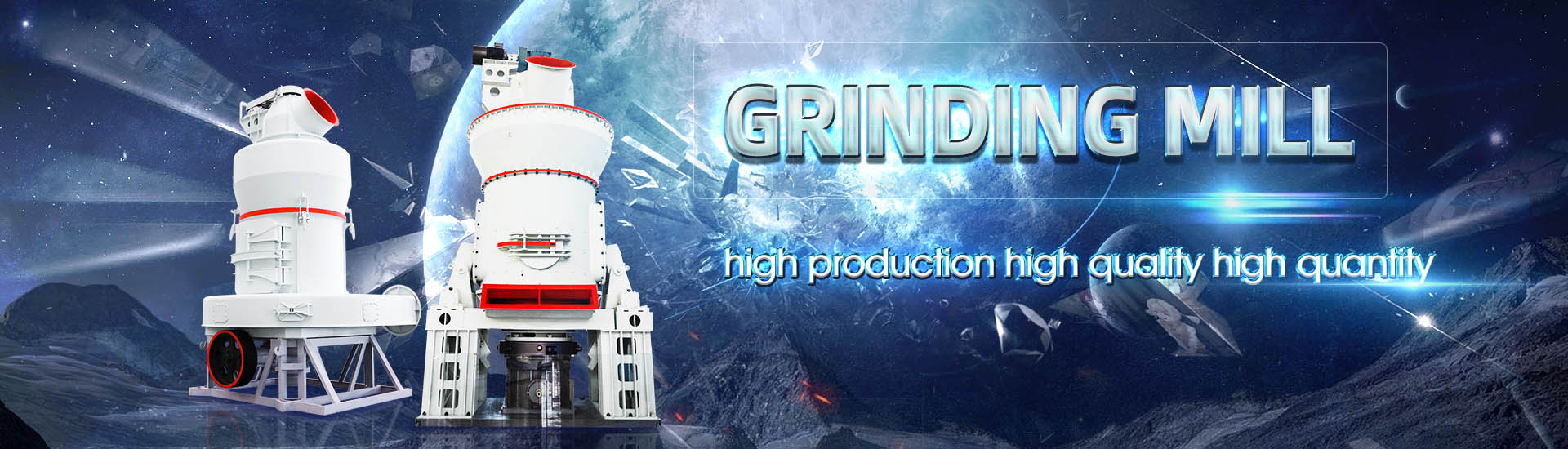
Rotary Kiln Coal Powder Fineness
.jpg)
Modeling of Pulverized Coal Combustion in Cement Rotary Kiln
simulation of a 3000 t/d rotary kiln with a fourchannel burner The predicted results indicated that the improved model accounts for the thermal enthalpy of the clinker formation process and can give more insight (such as fluid flow, temperature, etc,) from within the cement rotary kiln, 1999年1月1日 A mathematical model is described for the numerical prediction of the distribution of velocity, temperature, species concentration and particle trajectories in an axisymmetric rotary cement(PDF) Modeling coal combustion in a rotary cement Coal powder fineness impacts combustion integrity and uniformity Excessively coarse coal powder results in incomplete combustion, raising fuel consumption Conversely, overly fine coal powder can generate ash deposits on clinker Quality Requirements for Traditional Kiln Fuel Coal in The predicted results indicated that the improved model accounts for the thermal enthalpy of the clinker formation process and can give more insight (such as fluid flow, temperature, etc,) from Modeling of Pulverized Coal Combustion in Cement Rotary Kiln
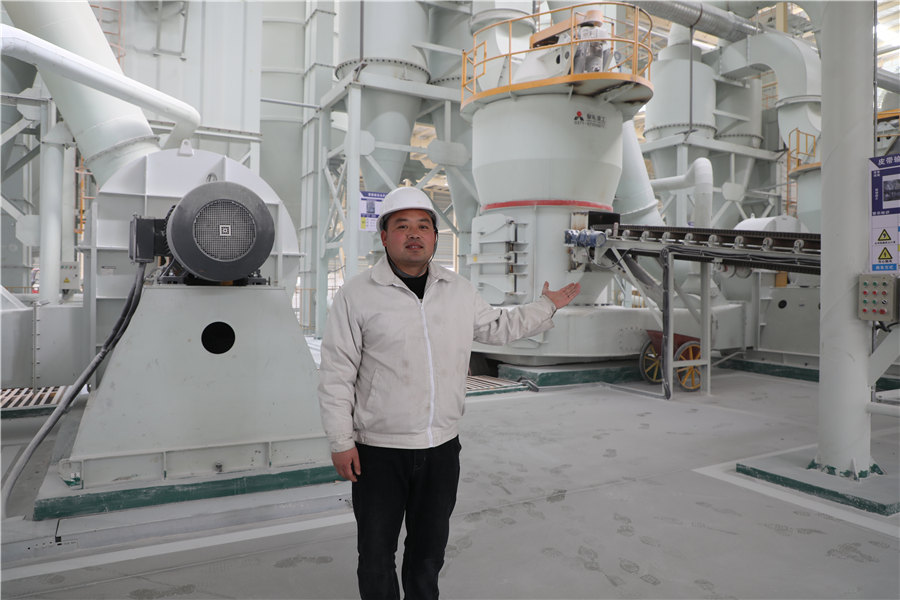
How to Accelerate Coal Powder Combustion Inside
Optimizing coal powder combustion within rotary kilns and preheaters is a critical endeavor in the cement industry By understanding the intricacies of combustion stages, adjusting burner designs, and adopting innovative approaches for low 2020年12月11日 This paper represents the medialization of alternative fuels cocombustion, in a cement rotary kiln, established on the commercial computational fluid dynamic (CFD) software ANSYS FLUENT The focus is placed on the Coal and Biomass CoCombustion: CFD Prediction of 2024年5月28日 The issue of ring formation in rotary kilns poses a significant obstacle to the efficient and costeffective production of oxide pellets This study focuses on sampling and Inhibiting the Accretion in the CoalFired Rotary Kiln of HighSilica An integrated process was developed to produce DRI powder and semicoke simultaneously from the excessive coalbased direct reduction of siderite ore in rotary kiln The optimization of Coproduction of DRI Powder and Semicoke from Siderite Ore and
.jpg)
Particle motion simulation and pulverized coal injection
2022年3月16日 The production process of direct reduced iron from titanomagnetite by coal reduction in air in rotary kiln is a key step in the extraction of titanium and iron This process is 2023年2月25日 The rotary kiln is used in many solid processes, including drying, incineration, heating, cooling, humidification, calcination and reduction This widespread application can be Rotary kiln process: An overview of physical mechanisms, models CPG has an experience of successfully executing numerous complete Rotary Kiln Cement Green Field Projects, Cement Rotary Kiln Plant and Rotary Kiln Turnkey Cement Plant To make our solution easily understandable, we have split it into three sections: Raw Material Crushing, Grinding And ,Blending; Pyro Processing; Cement ProductionTurnkey Rotary Kiln Cement Plant Manufacturers andProcess introduction Vertical coal mill, also known as vertical roller coal mill or vertical coal grinding mill, is a mechanical equipment for crushing and grinding coal into coal powerMainly used for grinding raw coal, bituminous coal, and other fuels into coal powder, which is supplied to rotary kiln and other kilns in the cement plant and thermal power plantcoal grinding machine CHAENG
.jpg)
Quantitative Optimization of Cement Rotary Kiln for Heat
Fuel Oil (LPFO) and natural gas to firing the kiln to generate heat energy required in the kiln for production of clinker from the kiln feed In modern cement plant, natural gas and fuel oil are preferred for firing the kiln over coal The main reason being that firing of cement kiln with solid fuel like coal requiresRotary Kiln Menu Toggle Girth Gears; Rotary Kiln Shell; Kiln Tyre; Kiln Support Roller; Rotary Kiln Thrust Roller; Rotary Kiln Pinion; VRM Menu Toggle Coal powder fineness (008mm hole sieve residue, %) 8: 8: Grinding capacity(t/h) 40: 38: Drying capacity: Very High: High: Main motor capacity(kW) 630: 1250: Total installed capacity(kW)Coal Mill in Cement Plant Vertical Roller Mill AirSwept Ball Mill2021年8月17日 The Deposit Formation Mechanism in CoalFired Rotary Kiln for Iron Ore Pellet Production: A Review August 2021; Crystals 11(8) it binds the pellet powder and coal ash from the material layer, (PDF) The Deposit Formation Mechanism in CoalFired Rotary Kiln 2022年5月1日 Effect of coal ash on ring behavior of ironore pellet powder in kiln Powder Technol, 323 (2018), pp 195202 View PDF View article View in Scopus Google Scholar The deposit formation mechanism in coalfired rotary kiln for iron ore pellet production: a review Crystals, 11 (2021), p 974, 103390/cryst Google ScholarCharacterization and comparison of deposits in a coalfired rotary kiln
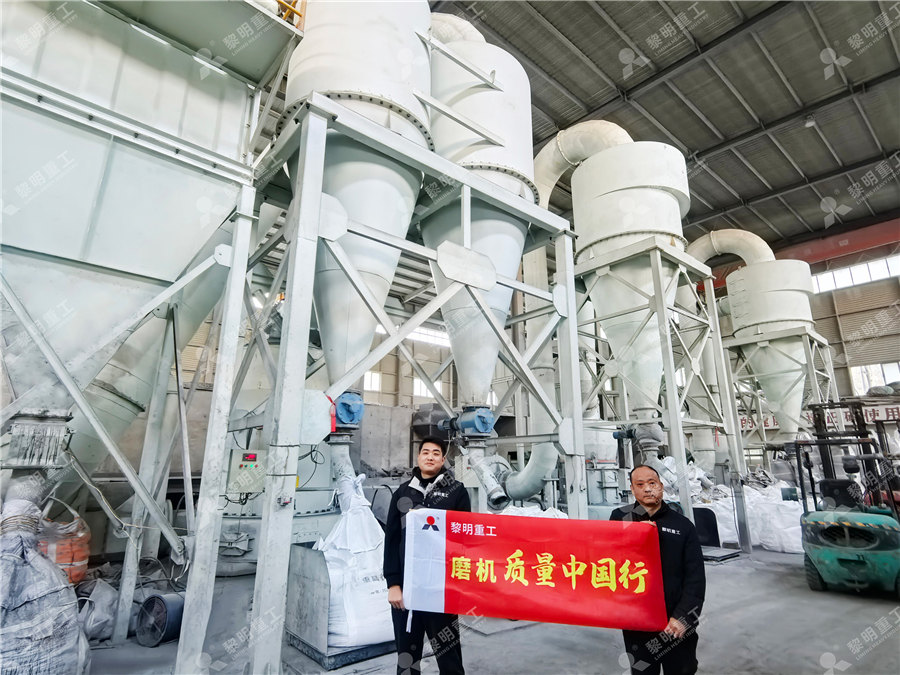
Powder Concentrator/Powder Concentrator Manufacturers/Powder
Product fineness 008% Air volume(m³/h) Rotary speed(rpm) otor power (kw) Max treatment volume(t/h) Output(t/h) TS1 03 16000 250500 15 50 Shanghai Sievo Rotary Kiln Equipments Manufacturer is a chinabased supplier for Powder Concentrator,Powder Concentrator Manufacturers,Powder Concentrator For Sale, 2021年8月17日 The depositforming problem is one of the main bottlenecks restricting the yield and production benefit of iron ore pellets produced by coalfired rotary kilns In order to implement measures to ensure the efficient production of pellets by coalfired rotary kilns, the mechanism and influencing factors on the deposit formation were reviewed The pellet powder and coal The Deposit Formation Mechanism in CoalFired Rotary Kiln Rotary kiln Electromagnetic Rotary Kiln; External Heating Electric Rotary Kiln; ensuring the desired fineness and quality of coal powder coalfired boilers for power generation and heating boilers in the metallurgical industry, coal powder preparation in shaft kiln, coal chemical industry Type specification: VRM800M: VRM1100M HighEfficiency Vertical Coal Mill Enhancing Coal PulverizationPowder Processing Technology provides contract calcination and drying services using rotary calciners or kilns We have a broad range of equipment and the knowhow to meet virtually any hightemperature requirement Our gasfired calciners and Rotary Calcining Services Powder Processing and Technology
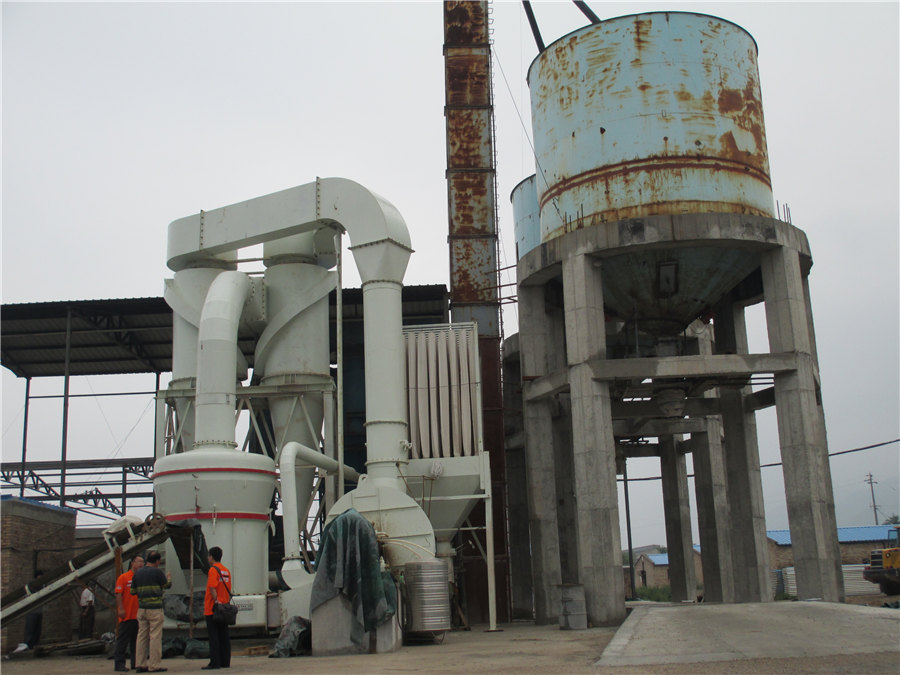
The Deposit Formation Mechanism in CoalFired Rotary Kiln for
22 The Distribution of Deposit in CoalFired Rotary Kiln The distribution of deposits in a grate and rotary kiln is mainly affected by pulverized coal injection and temperature field [21,22] As shown in Figure2, at the heads of the rotary kiln, pulverized coal is sprayed with highpressure air and burned to provide heat22 Procedure of Experiment The test flow sheet of excessive coalbased direct reduction process to coproduce DRI powder and semicoke is presented in Fig 2Firstly, siderite lump ore was charged into a rotary kiln (bench scale: ϕ120×200 mm, pilot scale: ϕ1000×500 mm) for reductionThe amount of coal required for reduction was determined by designed C/Fe mass Coproduction of DRI Powder and Semicoke from Siderite Ore In addition, too high temperature will bring about a risk of ring formation in rotary kiln and more energy consumption In consideration of that operation reduction temperature should be lower by 100–150°C than the softening temperature of coal ash in rotary kiln, therefore, the optimum reduction temperature is recommended at 1050°C 312Coproduction of DRI Powder and Semicoke from Siderite Ore 1The raw coal from storage and conveying system come into air swept coal mill for grinding The coal powder mass and heat transfer with 200℃~350℃ hot air The moisture enter into flue gas from coal Coal powder is dried by hot air Then coal powder come to powder separator with airflow for classificationPulverized Coal Preparation Production LineZK Ball MillCement
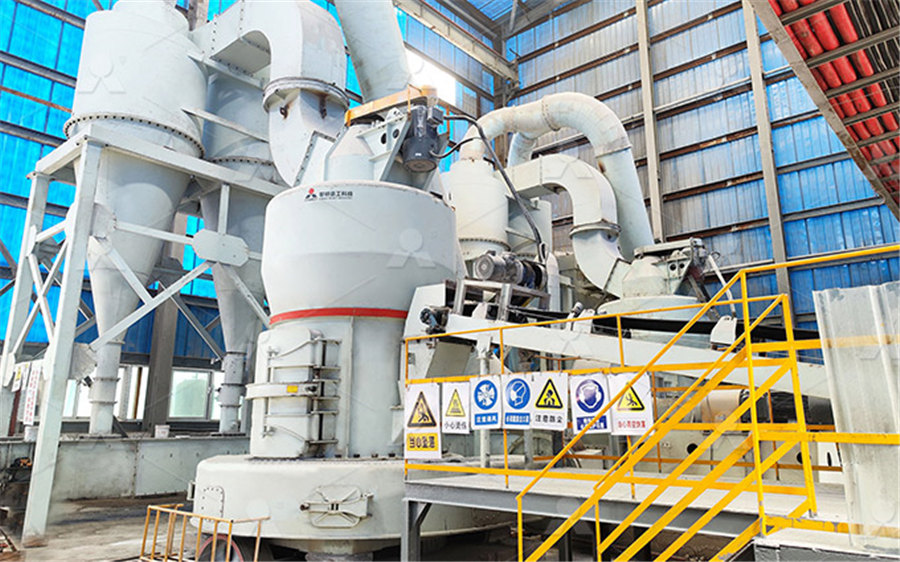
Bauxite Rotary Kiln Calcination Process and Refractory
2023年5月15日 In the rotary kiln, the raw material particles gradually move towards the kiln head with the rotation of the rotary kiln, and are calcined into petroleum proppant ceramsite sand at a temperature of 1400°C~1600°C in the firing zone The ceramsite sand enters the single cylinder cooler for cooling, and the secondary air of the cooler enters the kiln Fig4 Rotary kiln: Clinkerisation Process The kiln composes the clinker in the form of mould like balls, which consists of silicates, aluminates, and ferrites of calcium Clinker along with blast furnace slag and coal fly ash is ground to a fine and matching powder, which is called cementDevelopment and Evaluation of Mathematical Model based Gypsum powdermaking process According to the process requirements, the construction gypsum production line is usually divided into five parts, including crushing system, storage conveying system, grinding system, calcining system, and electric control system STEP1 crushing system The size and specifications of gypsum ores are different after mining, and Gypsum Powder Manufacturing Gypsum Powder Making The invention discloses a kind of rotary kiln coal mill system, including coal mill, coal mill is arranged between coal bunker and rotary kiln to be connected by pipeline, the rotary kiln coal mill system also includes powder concentrator, bag dust collector, Pulverized Coal Bin and fourair channel coal burner, coal mill is by pipeline successively through powder concentrator, bag A kind of rotary kiln coal mill system Google Patents
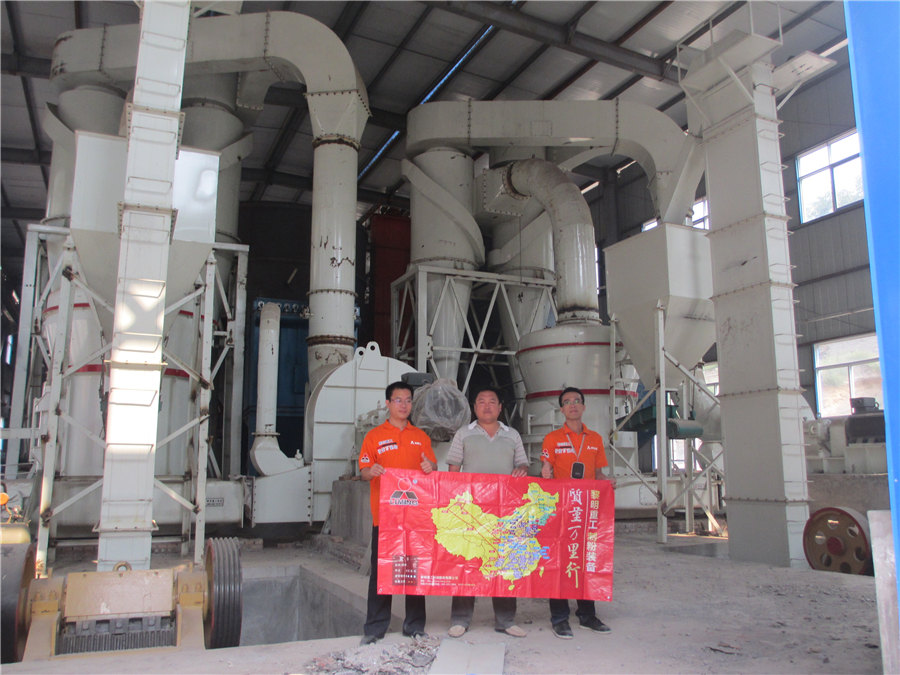
Cofiring of hydrogen and pulverized coal in rotary kilns using one
2024年10月5日 The gratekiln process for ironore pellet induration utilizes pulverized coal fired burners In a developed infrastructure for H 2 , it might be desirable to heat the existing rotary kilns with 2022年2月15日 To verify our inference that molten wrappage was developed by reduced iron ore powder and coal ash, the briquettes of mixed powder were reacted in a lab horizontal tube furnace by simulating the typical condition within 5 ∼ 6 m zone of rotary kiln (roasted at 950 ∼ 1050 °C for 30 min in atmosphere of CO)Coal ash induced ring formation in a pilot scale rotary kiln for low 2024年10月25日 Fly ash, coal gangue powder, cement kiln dust, recycled concrete powder are the most popular used byproduct materials, which can serve as a substitute for cement Adding fly ash can slow down heat growth at a initial stage, and there's evidence that it may reduce chloride infiltration, increasing the durability of reinforced concrete structuresDurability of high strength selfcompacting concrete with fly ash, coal mass transfer, and pulverized coal combustion, a set of mathematical models for a fullscale cement rotary kiln were established In terms of CFD model, gas velocity, gas temperature, and gas components in a cement rotary kiln were obtained by numerical simulation of a 3000 t/d rotary kiln with a fourchannel burnerCFD MODELING OF A CEMENT KILN WITH MULTI CHANNEL
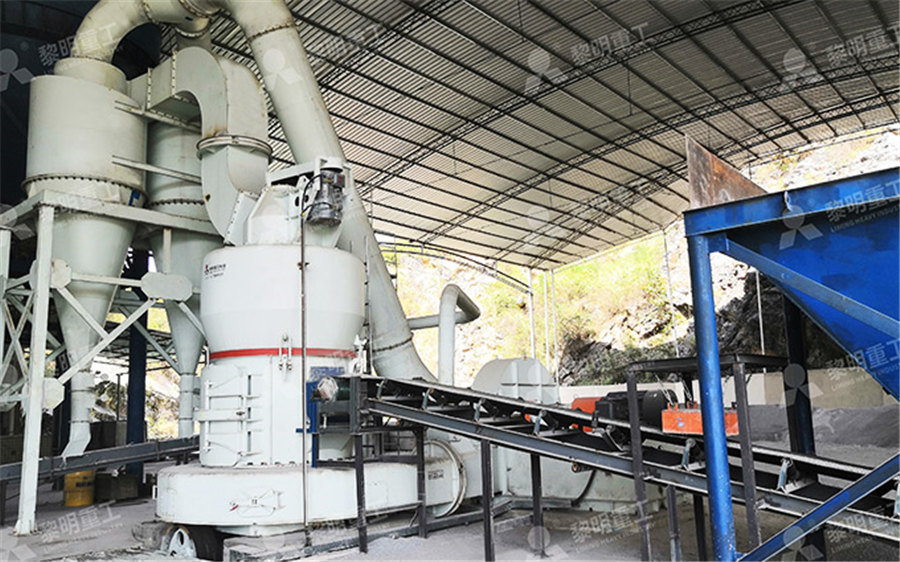
(PDF) Operation of CoalBased Sponge Iron Rotary
2019年6月4日 KONA Powder and P article Journal, Vol 32, 2015, pp 115130 4 Minimum response time of a large coal fired rotary kiln (80 m in length) is approximately 34 hours View fulltext2024年5月30日 Solution II: Easily prevent kiln ring formation Ensuring normal rotary kiln flame is one challenge; another is material looping This occurs when furnace charge adheres in a ring shape to the inner wall of the hightemperature zone Minor adhesion is termed kiln skin, while thicker adhesion affecting furnace operation is called ring formationFacing Rotary Kiln Challenges? 4 Solutions to Help You!The utility model relates to a lime rotary kiln coal powder preparation conveying device, wherein a raw coal bin is connected with a rationed coal feeding machine inlet; the rationed coal feeding machine outlet is connected with a coal mill; a separator is arranged above the coal mill; an inlet of a bagtype powder collector is connected with CNU Lime rotary kiln coal powder preparation 2019年5月19日 Kiln specializing in the production of highyield lime kilns, large lime kilns, our company combines advanced foreign technology and many domestic research technology to design high quality and high yield lime kilns, mainly divided into coal burning shaft kiln series, gas burning shaft kiln series, Rotary kiln series of three series of more than a dozen kiln type, the Analysis and Design of Key Parameters in Intelligent System of
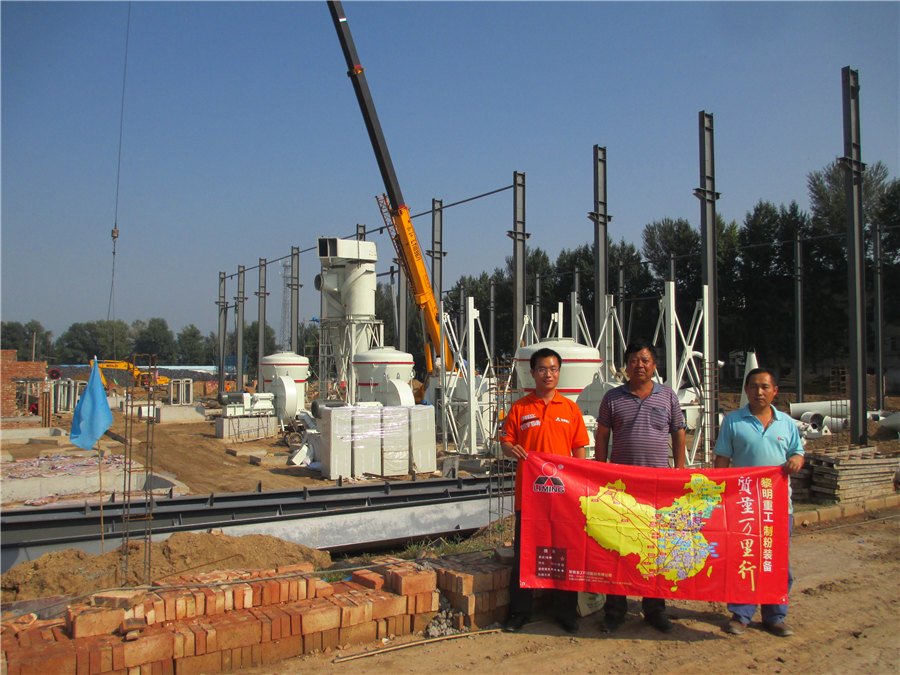
Coproduction of DRI Powder and Semicoke from Siderite Ore
KEY WORDS: siderite; low rank coal; coalbased direct reduction; DRI; semicoke; rotary kiln obtained sponge iron powder with iron grade in range of 8485%–8850% and metallization degree above 90% after magnetic separation of coalbased reduction of siderite in a fixed bed reactor Wei7) crushed the siderite ore to −2 mm2024年6月14日 To achieve environmental sustainability and improve material characteristics, this study examines the performance of selfcompacting concrete (SCC) that incorporates different industrial byproducts, including fly ash (FA), coal gangue powder (CGP), cement kiln dust (CKD), and recycled concrete powder (RCP)Performance analysis of self compacting concrete by incorporating Recommended Coal Fineness Fuel Feed Rate In a rotary kiln system producing cement clinker, gas flows are countercurrent to material flows Gases enter the kiln as secondary air at about 600°C – 1100°C and rise abruptly to over 1750°C as heat from fuel combustion, Everything you need to know about Kiln System Operations in 2006年9月6日 In cement kiln a lot of reaction are takes place at different temperatures' in the different zones of the kiln As described in [6] by referring (Wang et al, 2006), When the kiln feed enters the Modeling of Pulverized Coal Combustion in Cement Rotary Kiln
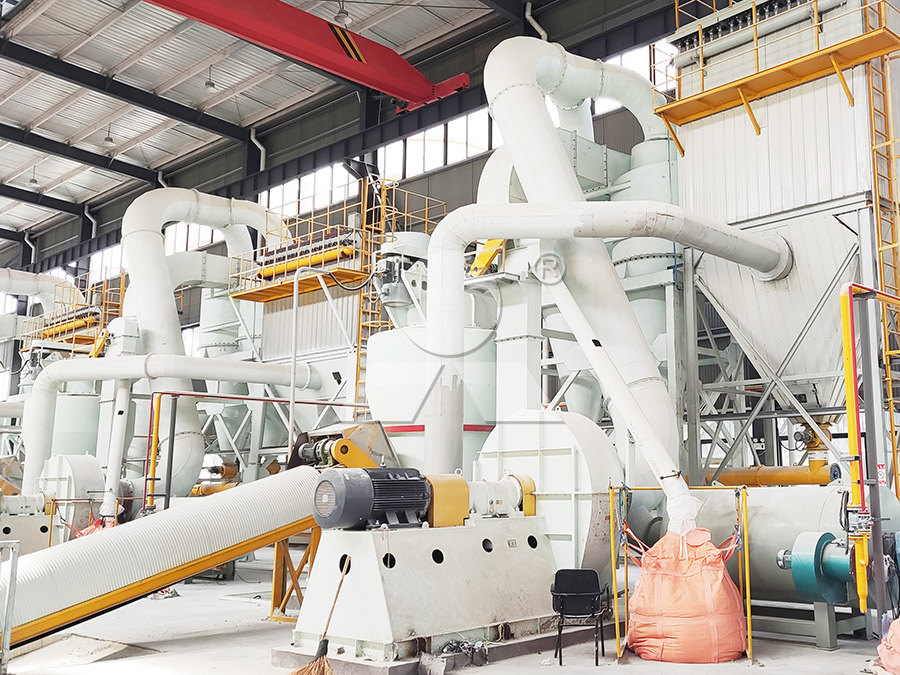
Turnkey Rotary Kiln Cement Plant Manufacturers and
CPG has an experience of successfully executing numerous complete Rotary Kiln Cement Green Field Projects, Cement Rotary Kiln Plant and Rotary Kiln Turnkey Cement Plant To make our solution easily understandable, we have split it into three sections: Raw Material Crushing, Grinding And ,Blending; Pyro Processing; Cement ProductionProcess introduction Vertical coal mill, also known as vertical roller coal mill or vertical coal grinding mill, is a mechanical equipment for crushing and grinding coal into coal powerMainly used for grinding raw coal, bituminous coal, and other fuels into coal powder, which is supplied to rotary kiln and other kilns in the cement plant and thermal power plantcoal grinding machine CHAENGFuel Oil (LPFO) and natural gas to firing the kiln to generate heat energy required in the kiln for production of clinker from the kiln feed In modern cement plant, natural gas and fuel oil are preferred for firing the kiln over coal The main reason being that firing of cement kiln with solid fuel like coal requiresQuantitative Optimization of Cement Rotary Kiln for Heat Rotary Kiln Menu Toggle Girth Gears; Rotary Kiln Shell; Kiln Tyre; Kiln Support Roller; Rotary Kiln Thrust Roller; Rotary Kiln Pinion; VRM Menu Toggle Coal powder fineness (008mm hole sieve residue, %) 8: 8: Grinding capacity(t/h) 40: 38: Drying capacity: Very High: High: Main motor capacity(kW) 630: 1250: Total installed capacity(kW)Coal Mill in Cement Plant Vertical Roller Mill AirSwept Ball Mill
.jpg)
(PDF) The Deposit Formation Mechanism in CoalFired Rotary Kiln
2021年8月17日 The Deposit Formation Mechanism in CoalFired Rotary Kiln for Iron Ore Pellet Production: A Review August 2021; Crystals 11(8) it binds the pellet powder and coal ash from the material layer, 2022年5月1日 Effect of coal ash on ring behavior of ironore pellet powder in kiln Powder Technol, 323 (2018), pp 195202 View PDF View article View in Scopus Google Scholar The deposit formation mechanism in coalfired rotary kiln for iron ore pellet production: a review Crystals, 11 (2021), p 974, 103390/cryst Google ScholarCharacterization and comparison of deposits in a coalfired rotary kiln Product fineness 008% Air volume(m³/h) Rotary speed(rpm) otor power (kw) Max treatment volume(t/h) Output(t/h) TS1 03 16000 250500 15 50 Shanghai Sievo Rotary Kiln Equipments Manufacturer is a chinabased supplier for Powder Concentrator,Powder Concentrator Manufacturers,Powder Concentrator For Sale, Powder Concentrator/Powder Concentrator Manufacturers/Powder 2021年8月17日 The depositforming problem is one of the main bottlenecks restricting the yield and production benefit of iron ore pellets produced by coalfired rotary kilns In order to implement measures to ensure the efficient production of pellets by coalfired rotary kilns, the mechanism and influencing factors on the deposit formation were reviewed The pellet powder and coal The Deposit Formation Mechanism in CoalFired Rotary Kiln
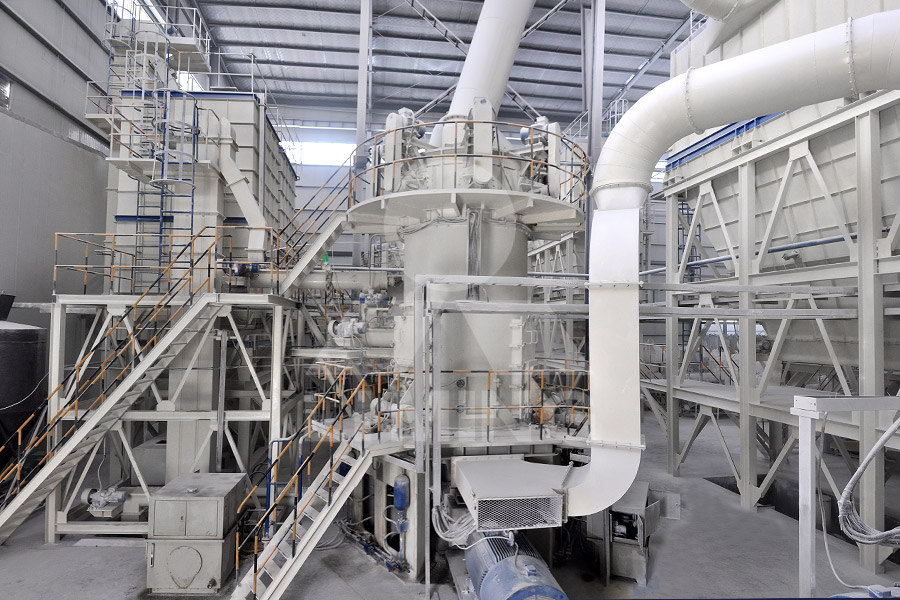
HighEfficiency Vertical Coal Mill Enhancing Coal Pulverization
Rotary kiln Electromagnetic Rotary Kiln; External Heating Electric Rotary Kiln; ensuring the desired fineness and quality of coal powder coalfired boilers for power generation and heating boilers in the metallurgical industry, coal powder preparation in shaft kiln, coal chemical industry Type specification: VRM800M: VRM1100M Powder Processing Technology provides contract calcination and drying services using rotary calciners or kilns We have a broad range of equipment and the knowhow to meet virtually any hightemperature requirement Our gasfired calciners and Rotary Calcining Services Powder Processing and Technology