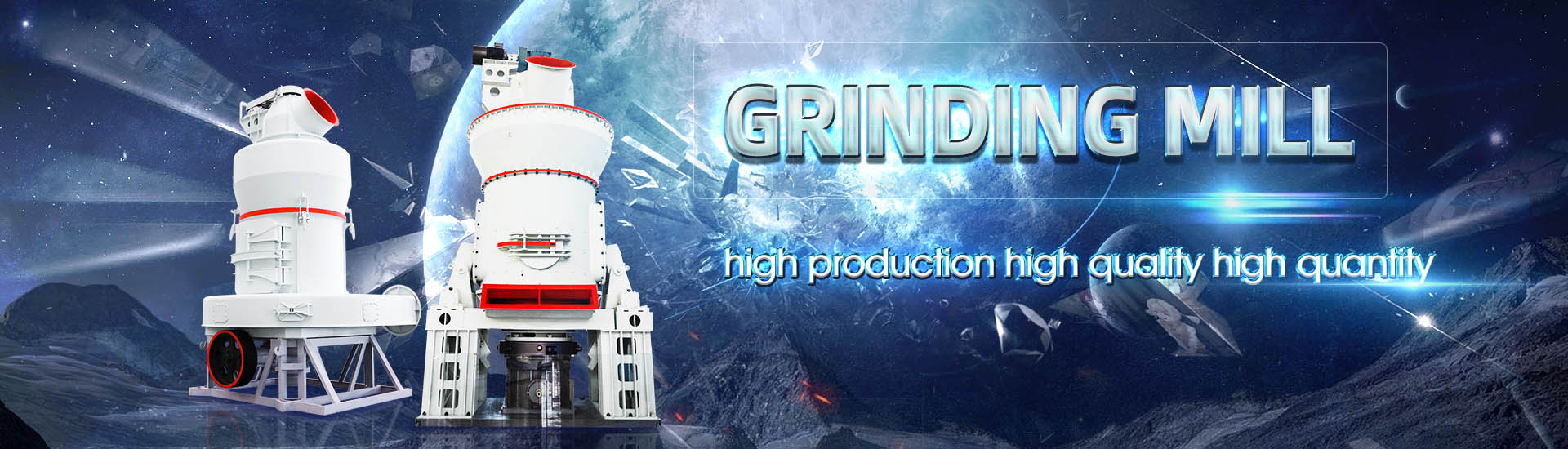
Accessories generally needed for cement production
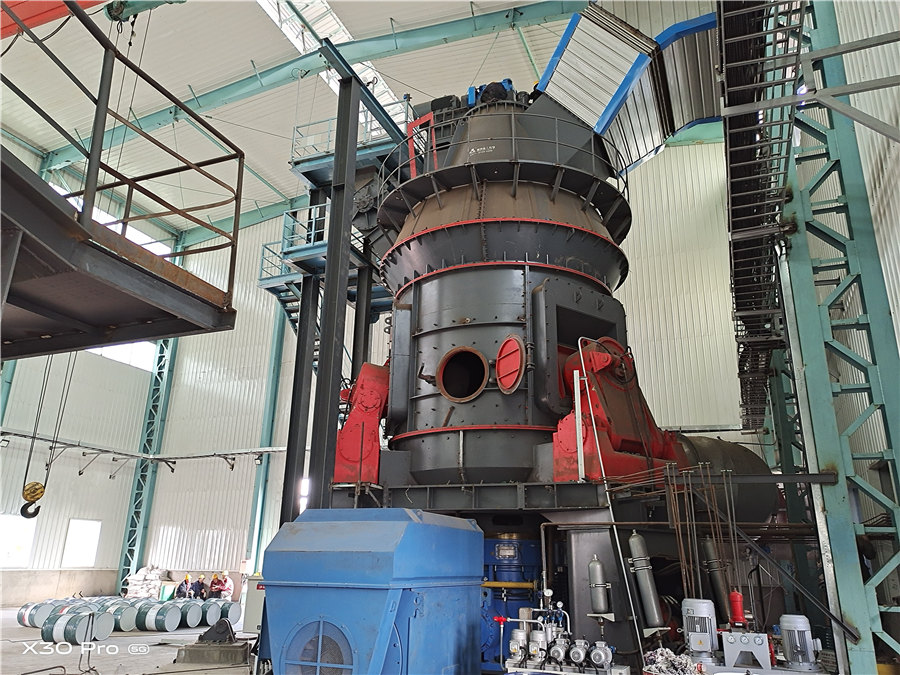
Cement Additives Sika
Sika offers many types of cement additives known to improve cement quality, increase production efficiency and meet your local demands:Other accessories may be needed to promote proper drainage, attach finishes, and complete the wall Finishes Simplified Finishes: CMU walls are extremely versatile in appearance, whether using plain or architectural units Options Applications of Cement Portland Cement AssociationThere are six main stages of the cement manufacturing process The raw cement ingredients needed for cement production are limestone (calcium), sand and clay (silicon, aluminum, iron), How Cement is Made Cement Manufacturing ProcessTraditional cement production is based on the push principle of making and storing goods ahead of demand, which is costly and inefficient Our MULTICOR blending system makes the sustainable cement revolution possible by Cement processing equipment Qlar
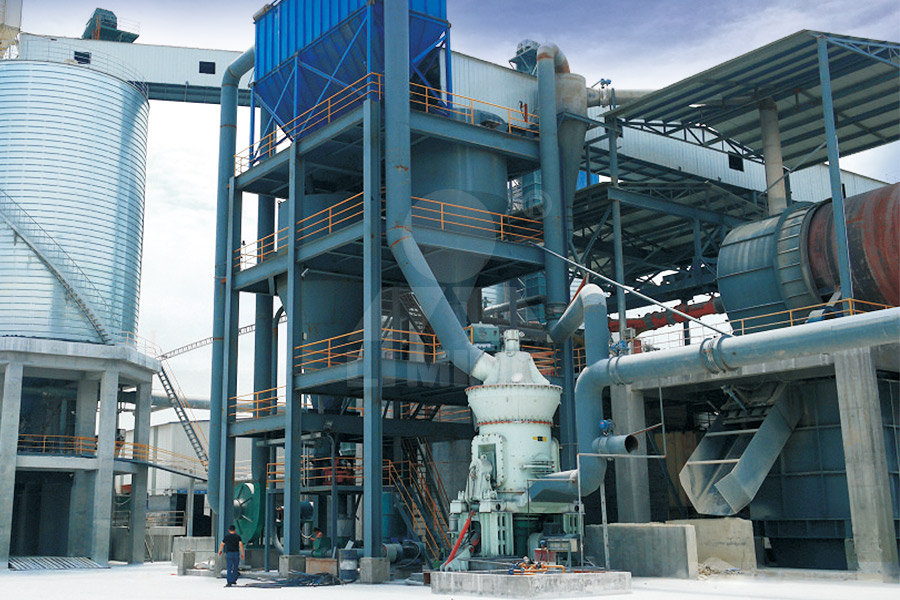
Cement Euipment Overview Cement Making
2019年9月27日 In general, we can divide the cement production line into three main steps: raw material preparation of cement, clinker production, and cement grinding Each step has some cement manufacturing machines, such as raw Determine the scale of production and type of cement to be produced Choose an optimal location for the cement plant Design the layout of the cement factory Acquire the necessary equipment Construct the factory and install the StepbyStep Guide to the Manufacturing of CementCement manufacturing: components of a cement plant This page and the linked pages below summarize the cement manufacturing process from the perspective of the individual components of a cement plant the kiln, the cement mill etc Cement manufacturing: components of a cement plant 2024年9月5日 Cement is one of the most widely used materials in the construction industry worldwide Most building projects utilize cement in one or the other form, including concrete, mortar, and flooring This blog provides a A Comprehensive Guide to the Cement Manufacturing
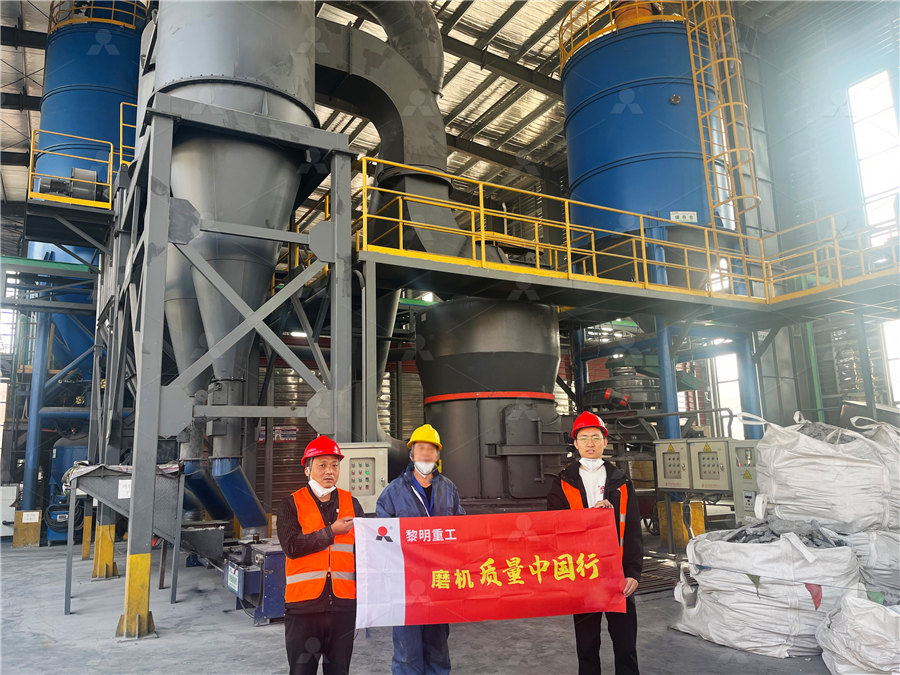
Mineral Additions for Cement Production SpringerLink
2014年1月1日 The history of mineral additions to cement is as long as the history of cement In Chap 1 the original applications of natural pozzolanas are mentioned According to Smolczyk [], the usage of granulated blastfurnace slag as binder became important in 1862, when Emil Langen found the hydraulic properties of this materialThe production of slag binder activated with Cement production involves quarrying limestone and clay, grinding and blending the materials, burning them at high temperatures to form clinker, and finely grinding the clinker to produce cement powder The key steps are: 1) Chapter 1 Introduction To Cement Production2019年11月1日 Clinker production is the most important stage of cement production in terms of energy input and emission potential (EEA, 2016)While approximately half of CO 2 emissions related to clinker production is derived from the combustion of fossil fuels, remaining portion is derived from the calcination of limestone (Gürsel, 2014)Additionally, sulfur dioxide (SO 2) and A comparative life cycle assessment for sustainable cement production THE NEED FOR EFFECTIVE RISK MITIGATION IN CEMENT PLANTS THE NEED FOR EFFECTIVE RISK MITIGATION IN CEMENT PLANTS 2,000 cement production plants in operation across the globe in more than 160 countries; Cement plants are generally regarded as less prone to major fire and explosion lossesTHE NEED FOR EFFECTIVE RISK MITIGATION IN CEMENT PLANTS THE NEED
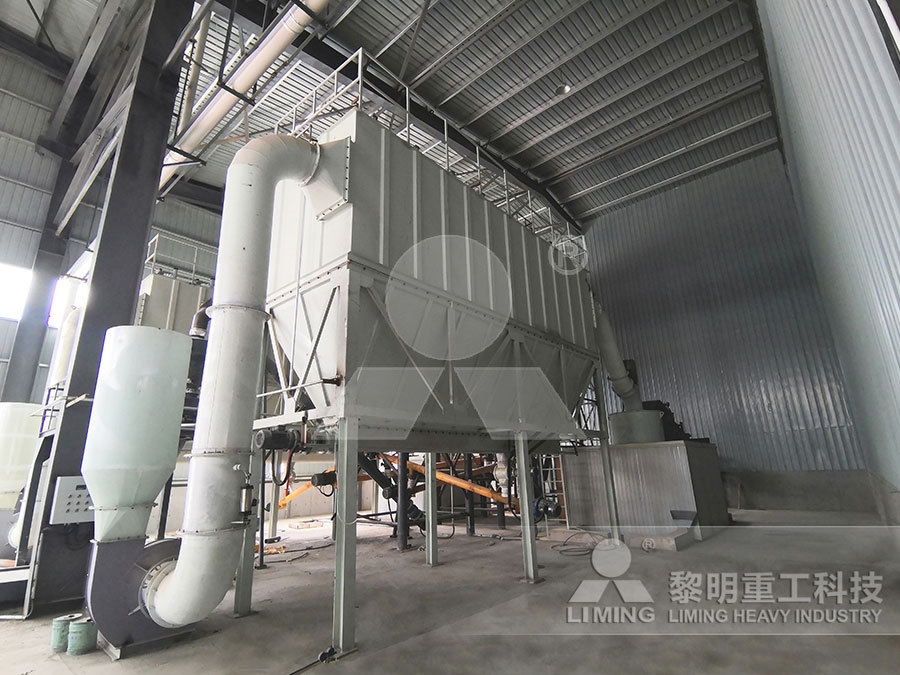
Is Coal Needed for Cement Production? A Comprehensive Analysis
2024年8月31日 In the realm of cement production, understanding the role of coal is crucial for assessing its impact on both the environment and production efficiencyCement, an essential construction material, is traditionally produced using a combination of raw materials, energy sources, and processing techniquesThis article provides an indepth exploration of whether 2023年11月1日 This study presents the LCA of cement clinker production following the implementation of CCS or CCUS by 2050 in an actual cement plant in Denmark The modelling includes all the activities of the value chain: capture, liquefaction, transport, permanent storage, and conversion of the biogenic fraction to methanol for ekerosene productionPreconditions for achieving carbon neutrality in cement production As an alternative replacement of clay, sewage sludge is also combined with other solid waste in cement production Lin and Lin (2004; 2005) used different types of waste sludge ash, including sewage sludge ash, water purification sludge ash and steel slag and limestone, as raw components for the production of ecocement clinkers by burning at 1400 °C for 6 hCement Clinker Production an overview ScienceDirect Topics2018年12月18日 This research paper describes mineralogical analysis technique of primary raw materials, auxiliary components for cement production, byproduct clinker and final product, cementCharacterization of raw materials and final product in the cement
.jpg)
CADD: What are cement additives? Mapei
2024年11月27日 Cement additives play a crucial role in modern cement production, and in all cases where a significant increase in strength is needed BXR additives are generally formulated to satisfy the goals of the cement factory One option for their use is increase early and ultimate strengths to improve the binder quality2023年1月1日 It was generally adopted where alkali content in raw materials and fuel was on the higher side and raw material properties Vietnam, China and India presented an increase in the CO 2 emission from cement production of 496%, 238% and 215%, respectively On the other hand, Spain and Germany mass of cement needed to Production of cement and its environmental impact ScienceDirect2024年5月23日 Cement production ensure continuous operation, peak performance, dust control, and durability with conveyor belt for cement industry : [ protected] Phone:+86 HomeConveyor Belt for Cement Industry: Technology Choose the right cement manufacturing machine is an important influence factor to produce highquality cement The cement making machine frequently used in cement plants includes cement rotary kiln, shaft kiln, cement vertical mill, Cement Manufacturing Machine Cement Making
.jpg)
A life cycle assessment of clinker and cement production in
2024年6月1日 The cement industry is the secondlargest source of direct CO 2 emissions and the thirdlargest energy consumer in the industrial sector (IEA, 2018)The heat required for the pyroprocessing (clinker production phase) is obtained primarily by combusting fossil fuels (mainly, coal) (Ige et al, 2022)Efforts are underway to decrease the dependence on fossil The cement production process 1 The Quarry: The cement production process begins with the extraction of limestone and clay from the quarry 2 Crusher and PreBlending: The material is then crushed to reduce particle sizes and blended to reduce variability in composition 3 Raw Mill and Kiln: Raw materials and additives areA practical guide to improving cement manufacturing processes STEP4: Preheating and precalcining of Portland cement When the airflow carries the raw meal into the cyclone, it is forced to make a rotating flow in the annular space between the cyclone cylinder and the inner cylinder (exhaust pipe), and it moves downward while rotating, from the cylinder to the cone, and the movement can be extended to the end of the cone, and then Portland Cement Manufacture Portland Cement Production2016年3月1日 Cement production is extremely costly in terms of energy consumption In May 2014, South Valley Cement (SVCC) said that the investments needed to use coal as fuel would cost US$198m, while for agricultural wastes it would cost Coal for cement: Present and future trends
.jpg)
Cement Extraction, Processing, Manufacturing Britannica
2024年11月23日 Cement Extraction, Processing, Manufacturing: Raw materials employed in the manufacture of cement are extracted by quarrying in the case of hard rocks such as limestones, slates, and some shales, with the aid of blasting when necessary Some deposits are mined by underground methods Softer rocks such as chalk and clay can be dug directly by Cement is the most essential construction material that acts as a binding agent for concrete, laying bricks and more From limestone to clay and supplementary additives, each ingredient contributes to the durability and strength of cement Let us learn about the essential raw materials used for cement production Composition of CementExplore Raw Material Used For Cement Production JK CementThe cement which is widely used from 2003 is the Portland Composite Cement (PCC) which is made following European Standard Methods (EN), called BDS EN Now the ratio of production of PCC and OPC is around 95:5 (Kabir, 2013) Raw Materials: Two types of materials are needed for the production of cement one is calcium orCement Industry of Bangladesh2006年9月1日 Concrete is in desperate need of revitalisation in the 21st century due to growing durability, maintenance and environmental concerns Improving the cement within concrete is an essential part of Green Chemistry for Sustainable Cement Production and Use
.jpg)
Cement and Clinker Production by Indirect
2022年9月21日 PDF Global cement production has reached 39 billion tons However, the clinkerization process, which is the basis of cement production, is Find, read and cite all the research you need on 2023年1月1日 After production in the kiln, clinker is stored onsite in silos or clinker domes until needed for cement production Clinker along with up to 5% gypsum is ground together in a cement mill Portland cement particles are generally in the range of 1–50 micrometer (μm), Coal utilization in the cement and concrete industriesTo a great extent, operation of the rotary kiln system also determines the quality of the cement produced Stable operation of the kiln system will result in improved operational efficiency, higher production rates, and better quality clinkerIt can also result in reduced environmental emissions, a factor of everincreasing importanceEverything you need to know about Kiln System Operations in Cement A review of the effectiveness of Life Cycle Assessment for gauging environmental impacts from cement production Oluwafemi E Ige, Collins Obiora, in Journal of Cleaner Production, 2021 223 Production of clinker The clinker production stage is where the raw material (the raw meal) converts into clinker The raw meal is fed into a rotary kiln through a preheater at about 1450 Clinker Production an overview ScienceDirect Topics

Full article: Energy conservation and waste utilization in the cement
2014年12月22日 Cement production is one of the most energyintensive industries It consumes 12–15% of the total energy consumption in various industries Energy consumption involves 50–60% of the direct production cost of cement (Engin and Ari Citation 2005) Calcination and drying processes plus the kiln requires large quantities of thermal energy2021年12月28日 Currently, the production of one ton of ordinary Portland cement (OPC) releases considerable amounts of CO2 into the atmosphere As the need and demand for this material grows exponentially, it Alternative Clinker Technologies for Reducing Carbon Emissions 2022年8月18日 Cement is the core component of concrete, and with the increased demand for more construction worldwide, there is a higher need for the most popular building material: concrete During cement and concrete production, gases are produced that could harm humans and the wider environment; therefore, gas detection solutions are required for safety and Gas Detection Solutions for Cement Production IGD2022年12月1日 In the cement industry, the total energy consumption accounts for 50–60% of the overall manufacturing cost, while thermal energy accounts for 20–25% (Wang et al, 2009; Singhi and Bhargava, 2010)The modern cement industry requires 110–120 kWh of electrical power to produce one ton of cement (Mejeoumov, 2007)Thermal energy is used mainly during Review on energy conservation and emission reduction
.jpg)
The overall input and output of cement production
Abstract: The production of cement is rather complex process which includes a high amount of raw materials (eg, limestone, marl, clay, and iron ore), heat, electricity and different fuels 2014年1月1日 The history of mineral additions to cement is as long as the history of cement In Chap 1 the original applications of natural pozzolanas are mentioned According to Smolczyk [], the usage of granulated blastfurnace slag as binder became important in 1862, when Emil Langen found the hydraulic properties of this materialThe production of slag binder activated with Mineral Additions for Cement Production SpringerLinkCement production involves quarrying limestone and clay, grinding and blending the materials, burning them at high temperatures to form clinker, and finely grinding the clinker to produce cement powder The key steps are: 1) Chapter 1 Introduction To Cement Production2019年11月1日 Clinker production is the most important stage of cement production in terms of energy input and emission potential (EEA, 2016)While approximately half of CO 2 emissions related to clinker production is derived from the combustion of fossil fuels, remaining portion is derived from the calcination of limestone (Gürsel, 2014)Additionally, sulfur dioxide (SO 2) and A comparative life cycle assessment for sustainable cement production
.jpg)
THE NEED FOR EFFECTIVE RISK MITIGATION IN CEMENT PLANTS THE NEED
THE NEED FOR EFFECTIVE RISK MITIGATION IN CEMENT PLANTS THE NEED FOR EFFECTIVE RISK MITIGATION IN CEMENT PLANTS 2,000 cement production plants in operation across the globe in more than 160 countries; Cement plants are generally regarded as less prone to major fire and explosion losses2024年8月31日 In the realm of cement production, understanding the role of coal is crucial for assessing its impact on both the environment and production efficiencyCement, an essential construction material, is traditionally produced using a combination of raw materials, energy sources, and processing techniquesThis article provides an indepth exploration of whether Is Coal Needed for Cement Production? A Comprehensive Analysis2023年11月1日 This study presents the LCA of cement clinker production following the implementation of CCS or CCUS by 2050 in an actual cement plant in Denmark The modelling includes all the activities of the value chain: capture, liquefaction, transport, permanent storage, and conversion of the biogenic fraction to methanol for ekerosene productionPreconditions for achieving carbon neutrality in cement production As an alternative replacement of clay, sewage sludge is also combined with other solid waste in cement production Lin and Lin (2004; 2005) used different types of waste sludge ash, including sewage sludge ash, water purification sludge ash and steel slag and limestone, as raw components for the production of ecocement clinkers by burning at 1400 °C for 6 hCement Clinker Production an overview ScienceDirect Topics
.jpg)
Characterization of raw materials and final product in the cement
2018年12月18日 This research paper describes mineralogical analysis technique of primary raw materials, auxiliary components for cement production, byproduct clinker and final product, cement2024年11月27日 Cement additives play a crucial role in modern cement production, and in all cases where a significant increase in strength is needed BXR additives are generally formulated to satisfy the goals of the cement factory One option for their use is increase early and ultimate strengths to improve the binder qualityCADD: What are cement additives? Mapei