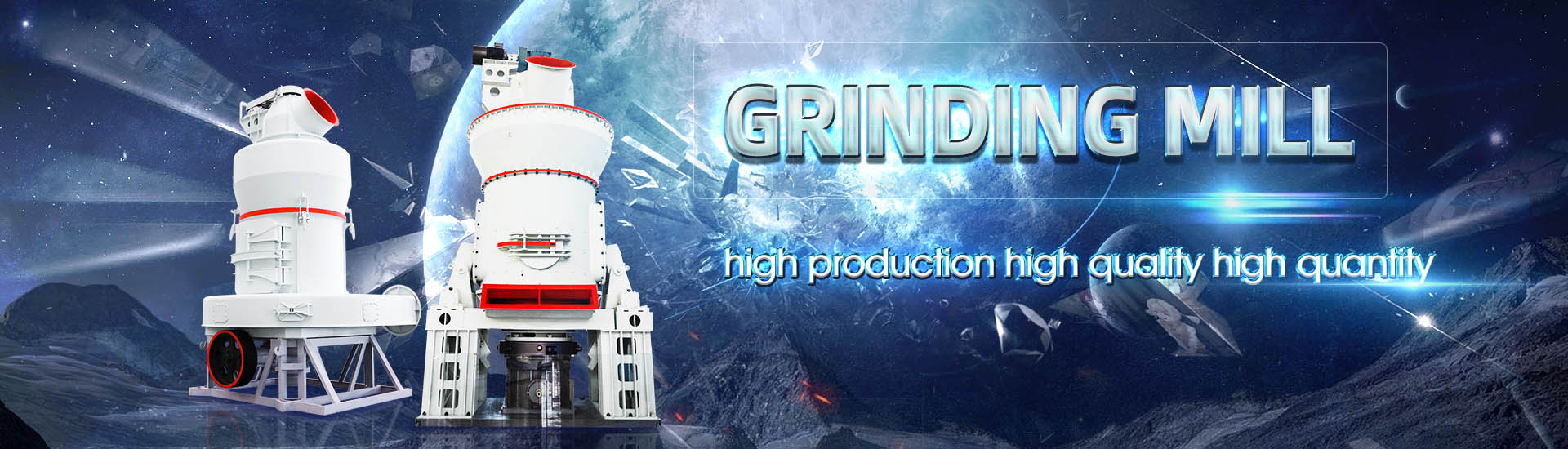
Energy saving of cement grinding drill
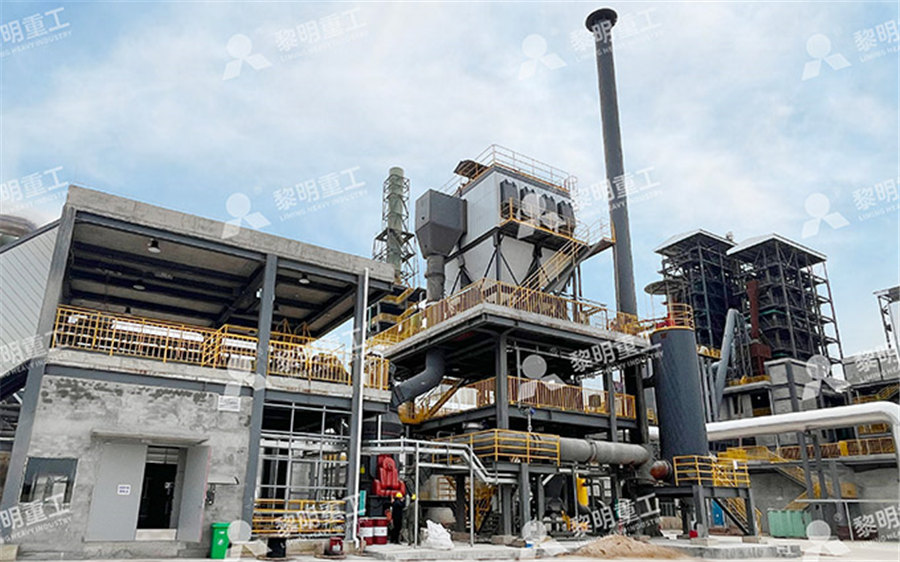
(PDF) Optimizing Energy Efficiency in Cement Grinding Processes
In this chapter an introduction of widely applied energyefficient grinding technologies in cement grinding and description of the operating principles of the related equip‐ ments and 2013年3月1日 In this paper, energy saving measures in the cement industry, such as energyefficiency measures for the preparation of raw materials, production of clinker, and the An overview of energy savings measures for cement industries2011年5月1日 Fig 3 shows that grinding (finish and raw grinding) consumes major share (ie 60%) of total energy consumption in a cement manufacturing process This can be targeted to A critical review on energy use and savings in the cement industriesCement accounts for at least 5 percent of anthropogenic emissions of greenhouse gases, and, according to some estimates, this share may be even higher At the same time, energyrelated IMPROVING THERMAL AND ELECTRIC ENERGY EFFICIENCY AT
.jpg)
ENERGY SAVING IN CEMENT GRINDING Project CORDIS
1999年10月21日 Aim of the project is the reduction in energy consumption by 27 % for the grinding of cement The reduction will be achieved by usage of special grinding equipment Various technologies are discussed for raw material preparation, clinker production, product changes, and general efficiency improvements The largest recorded savings from these measures include reductions of 34 GJ/t in An Overview of Energy Savings Measures For Cement 2016年10月5日 In this chapter an introduction of widely applied energyefficient grinding technologies in cement grinding and description of the operating principles of the related equip‐ ments and comparisons over each other in EnergyEfficient Technologies in Cement GrindingJoint grinding system is the preferred cement grinding system of current cement process design, the advantages are high productivity, low energy consumption of system and low noise, etc It Applications of Efficient EnergySaving Cement Grinding
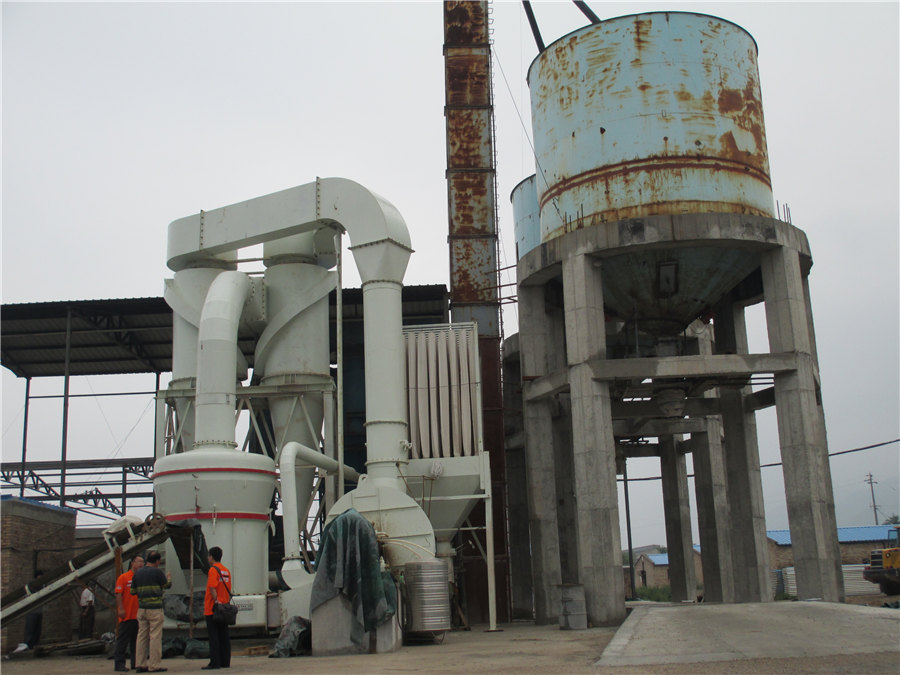
EnergyEfficient Technologies in Cement Grinding ResearchGate
2016年10月5日 When compared with ball mills the HOROMILL® gives power savings of 35 to 40% when grinding cement and of up to 50% when producing raw meal2018年7月1日 Raw meal preparation, clinker manufacturing, and cement grinding recorded the highest thermal energy savings of 430 GJ/t, 24 GJ/t, and 029 GJ/t, respectively Gravitytype silos are the best blending system for the dry process, saving a maximum of Energy and cement quality optimization of a cement grinding circuit 2018年4月1日 Cement, as a very basic raw material for infrastructure, consumes high energy during its production process [1][2][3] Note that a large amount of energy was consumed in order to grind cement into Energy and cement quality optimization of a cement grinding 2018 In this chapter an introduction of widely applied energyefficient grinding technologies in cement grinding and description of the operating principles of the related equip‐ ments and comparisons over each other in terms of grinding efficiency, specific energy consumption, production capacity and cement quality are givenEnergyEfficient Technologies in Cement Grinding Academia
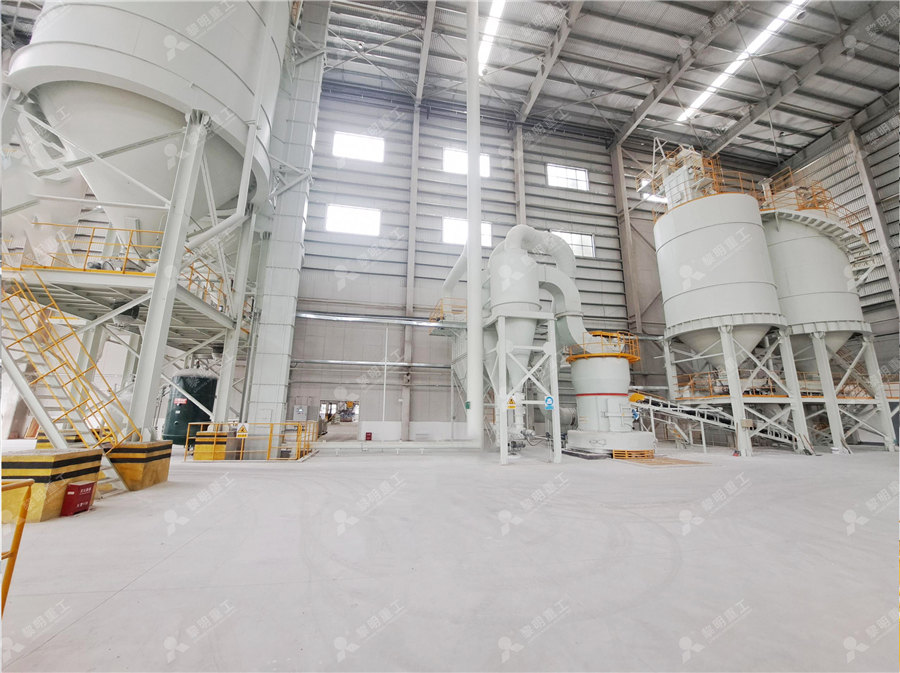
Review on energy conservation and emission reduction
2022年12月1日 In the cement industry, the total energy consumption accounts for 50–60% of the overall manufacturing cost, while thermal energy accounts for 20–25% (Wang et al, 2009; Singhi and Bhargava, 2010)The modern cement industry requires 110–120 kWh of electrical power to produce one ton of cement (Mejeoumov, 2007)Thermal energy is used mainly during Energy Saving Cement Plant Free download as PDF File (pdf), Text File (txt) or read online for free Energy use at different sections of cement industries, specific energy consumption, types of energy use, details of cement manufacturing processes, various energy savings measures were reviewed and presented A state of art review on the energy use and savings is necessary to Energy Saving Cement Plant PDF Mill (Grinding) Scribd2013年3月1日 Processes like grinding, transport of materials and crushing utilize machine drives and account for the majority of electricity consumption, as is evident in the result of the Manufacturing Energy Consumption Survey (MECS) in 1998 presented in Fig 3Process heating, by which clinker is made in large kilns, accounts for about 90% of the natural gas consumption An overview of energy savings measures for cement industriesCembureau [48] experimented vertical roller mills for coal grinding and achieved an energy saving of 7–10 kW h/t coal Buzzi, S, Sassone, G, 1993 Optimization of clinker cooler operation [82] Birch E Energy savings in cement kiln systems energy efficiency in the cement industry Elsevier Applied Science; 1990 118–128 [83] Cowi, C An overview of energy savings measures for cement industries
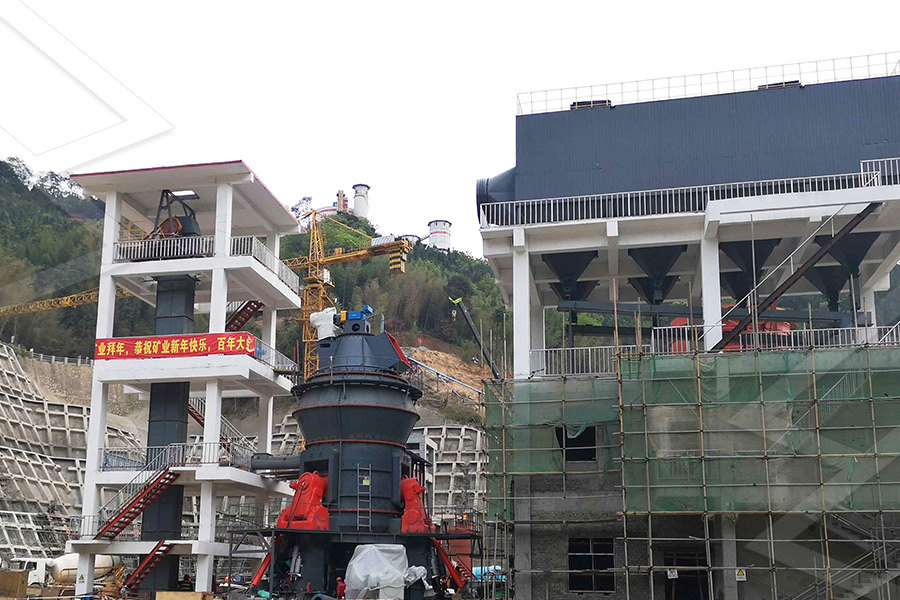
Improvement of cement performances through the use of grinding
Cement Additives Division 1 Improvement of cement performances through the use of grinding aids in vertical roller mill PD’Arcangelo, MMagistri – Mapei SpA, Milan, Italy Abstract Due to the stringent requirement of energy saving, the use of vertical The consumption of energy by the cement grinding operation amounts to one third of the total electrical energy used for the production of cement The optimization of this process would yield substantial benefits in terms of energy savings and capacity increase Optimization of the Cement Ball Mill OperationOPTIMIZATION OF CEMENT GRINDING OPERATION IN BALL MILLSSaving and Efficient Equipment for Cement Industry Free download as PDF File (pdf), Text File (txt) or read online for free Great Wall Machinery provides energy saving and efficient equipment for the cement industry, including vertical roller mills, ball mills, and rotary kilns Vertical roller mills offer high grinding efficiency and lower energy consumption compared to ball millsSaving and Efficient Equipment For Cement Industry Scribd2024年10月23日 The cement industry has long relied on traditional grinding media, predominantly steel balls, for the milling processes in ball mills However, this conventional method is increasingly becoming unsustainable due to the high energy demands and environmental regulations that are shaping the industry landscapeEnergySaving Advantages Of Ceramic Grinding Media In Cement
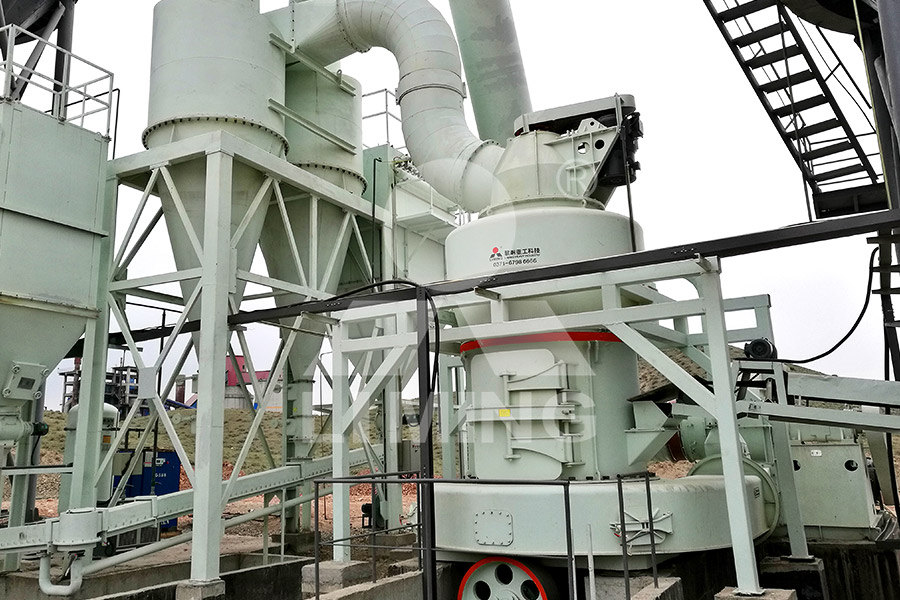
Energy and cement quality optimization of a cement grinding circuit
2018年7月1日 Among the industries, the nonmetallic industry was reported as the third largest energy user and accounted for about 12% of the global energy use [1]Within this portion, cement industry had the majority of the utilization with 85–12% [1], [2]US Energy Information Administration (EIA) [7] named cement industry as the most energy intensive among the 2011年5月1日 Cement manufacturing is an energy intensive process consuming about 12–15% of total energy consumption Therefore opportunities exist to identify areas where energy savings measures can be applied so that energy can be saved along with the reduction of emission pollution Table 15 presents list of energy savings measures for cement industriesA critical review on energy use and savings in the cement industries2010年10月1日 Download Citation Applications of Efficient EnergySaving Cement Grinding Technology and Equipment Joint grinding system is the preferred cement grinding system of current cement process Applications of Efficient EnergySaving Cement Grinding2023年1月1日 In this study, the effects of four grinding aids with three different levels on the three important characteristics of the cement, namely the specific surface area, the compressive strength of the (PDF) EFFECTS OF VARIOUS GRINDING AIDS DOSAGE ON
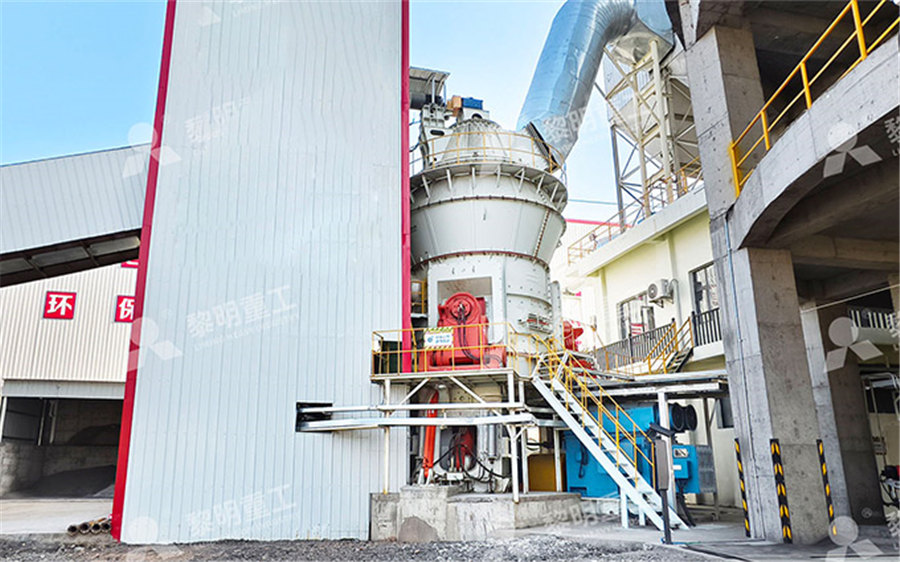
Energy Efficiency Improvement and Cost Saving Opportunities for Cement
Energy Efficiency Improvement and Cost Saving Opportunities for Cement Making An ENERGY STAR® Guide for Energy and Plant Managers August 2013 ENERGY STAR is a US Environmental Protection Agency Program helping organizations and individuals fight climate change through superior energy efficiency Document Number 430R13年8月26日 Resource saving and energy saving at the simultaneous production of two types of cement August 2020 IOP Conference Series Materials Science and Engineering 907(1):(PDF) Resource saving and energy saving at the simultaneous 2024年4月26日 Grinding and milling account for 58% of cement/concrete energy consumption These operations have an energy efficiency ranging from 6 to 25% and also offer a large opportunity for energy saving The following figure presents the cement production process Cement production processEnergy Efficiency and Saving in the Cement Industry2023年5月3日 Türkiye is the largest cement producer of Europe and the second biggest cement exporter in the world The industry is responsible for more than 8% of global carbon dioxide (CO2) emissions and around 15% of the primary energy consumed worldwide In this paper, the specific energy consumption (SEC) and related emissions of a real scale cement factory currently A comprehensive investigation of a grinding unit to reduce energy
.jpg)
Measures of energy saving and consumption reduction for final grinding
Journal of Cement 2022, Vol 0 Issue (06): 31 DOI: Current Issue Archive Adv Measures of energy saving and consumption reduction for final grinding of raw material roller press: XIAO Dongling, et al Abstract; Figure/Table; References ; Related Citation 2016年10月5日 Considering the energy consumption for RCW grinding equivalent to cement grinding with ball mill, typically 0030 kWh/kg [71], the CO 2 release due to RCW processing would be about 00027 kgCO 2 EnergyEfficient Technologies in Cement Grinding ResearchGateCement Ball Mill Cement Separator Cement Vertical Mill Adopt new grinding technology The application of new technology in cement grinding unit can greatly reduce energysaving investment and obtain maximum economic benefits, Making Your Cement Grinding Plant Energy SavingEnergy saving and carbon reduction reform based on cement grinding system diagnosis: WEI Huaijun, et alEnergy saving and carbon reduction reform based on cement grinding
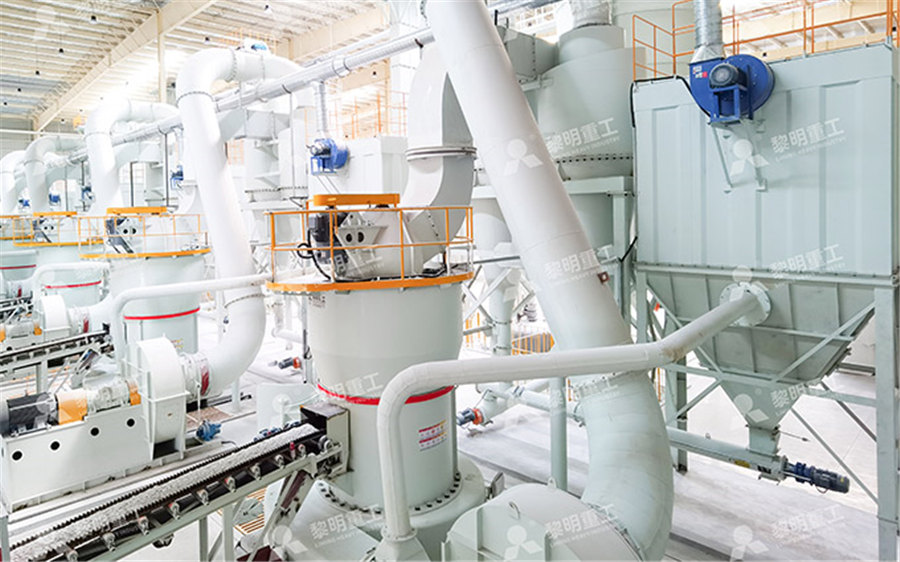
ENERGY AUDIT OF THERMAL UTILITIES IN A CEMENT PLANT
Schuer et al (1992) gave energy consumption values and described the energy saving methods and potentials for German Cement Industry The research was based on electrical and thermal energy saving methods The results were given in the form of energy flow diagram Shaleen et al (2002) conducted research on energy balance in a cement industrythe potential energy savings opportunity The costs associated with realizing these energy savings was not in the scope of this study The purpose of this data analysis is to provide macroscale estimates of energy savings opportunities for cement manufacturing subprocesses and sectorwide This is a step toward understanding the processes thatBandwidth Study on Energy Use and Potential Energy Saving Tangshan Jidong Cement attributed the growth to increased prices due to a 99% yearonyear increase in infrastructure spending to US$186tn Throughout the year, the company said, it completed energysaving optimisation and upgrades to improve efficiency, implemented strategic marketing and reduced the cost of material procurementEnergy Saving Cement industry news from Global Cement2022年2月18日 1) In our increasingly climateconscious world, emissions reduction remains a key goal for the cement industry What steps can be taken to reduce the environmental impact of cement grinding operations? FIVES FCB As well the consideration of production costs and carbon footprints, one key issue is energy consumptionWorld Cement Grinding Milling QA
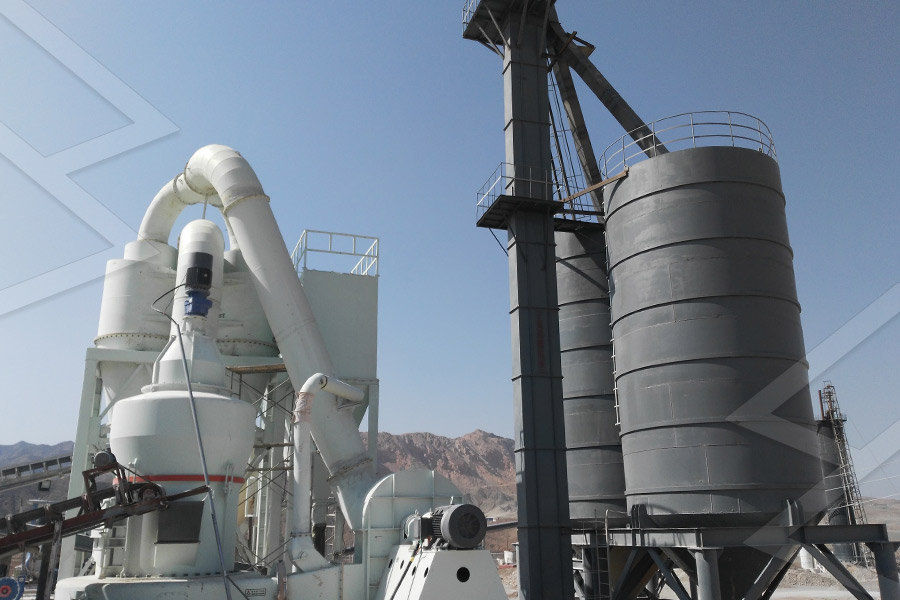
cement energy saving grinding equipment YouTube
cementmachine cement energy saving grinding equipment; Jiangsu Pengfei Group Co, Ltd is one of the leading manufacturers of rotary kiln and gri2013年3月1日 Request PDF An overview of energy savings measures for cement industries Due the advances in the industrial processes, in which the cement industry is a major contributor, energy consumption An overview of energy savings measures for cement industriesof energy efficiency in cement production in Nigeria Recently, there has been an increasing interest in using energy analysis techniques for energyutilization assess ments in order to attain energy saving, and hence finan cial savings [5] In this study, indepth energy evaluation is carried out on a large scale cement production firm,Energy and Cost Analysis of Cement Production Using the Wet 2018年7月1日 Raw meal preparation, clinker manufacturing, and cement grinding recorded the highest thermal energy savings of 430 GJ/t, 24 GJ/t, and 029 GJ/t, respectively Gravitytype silos are the best blending system for the dry process, saving a maximum of Energy and cement quality optimization of a cement grinding circuit
.jpg)
Energy and cement quality optimization of a cement grinding
2018年4月1日 Cement, as a very basic raw material for infrastructure, consumes high energy during its production process [1][2][3] Note that a large amount of energy was consumed in order to grind cement into 2018 In this chapter an introduction of widely applied energyefficient grinding technologies in cement grinding and description of the operating principles of the related equip‐ ments and comparisons over each other in terms of grinding efficiency, specific energy consumption, production capacity and cement quality are givenEnergyEfficient Technologies in Cement Grinding Academia2022年12月1日 In the cement industry, the total energy consumption accounts for 50–60% of the overall manufacturing cost, while thermal energy accounts for 20–25% (Wang et al, 2009; Singhi and Bhargava, 2010)The modern cement industry requires 110–120 kWh of electrical power to produce one ton of cement (Mejeoumov, 2007)Thermal energy is used mainly during Review on energy conservation and emission reduction Energy Saving Cement Plant Free download as PDF File (pdf), Text File (txt) or read online for free Energy use at different sections of cement industries, specific energy consumption, types of energy use, details of cement manufacturing processes, various energy savings measures were reviewed and presented A state of art review on the energy use and savings is necessary to Energy Saving Cement Plant PDF Mill (Grinding) Scribd
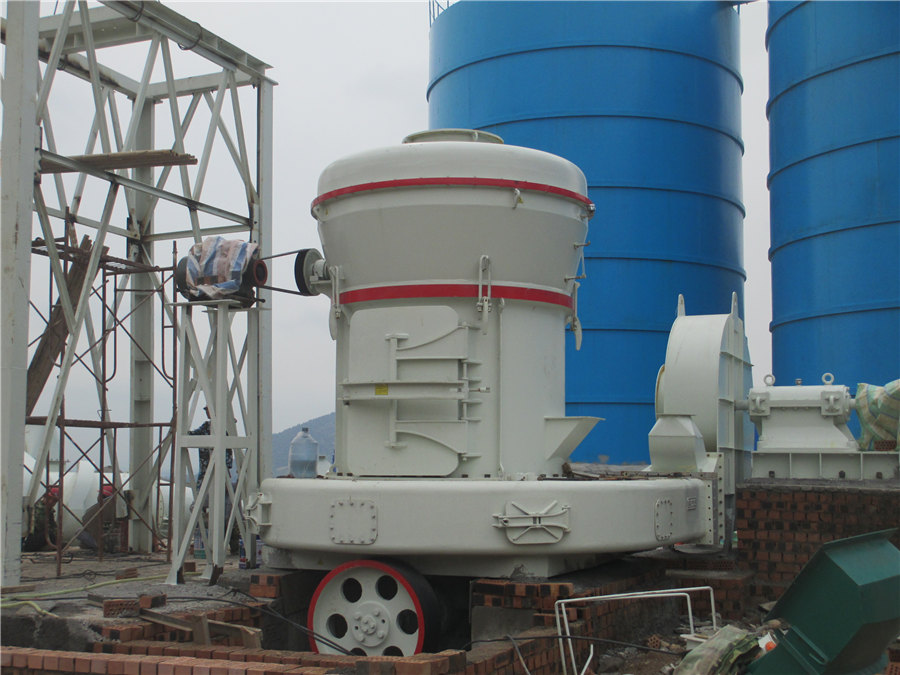
An overview of energy savings measures for cement industries
2013年3月1日 Processes like grinding, transport of materials and crushing utilize machine drives and account for the majority of electricity consumption, as is evident in the result of the Manufacturing Energy Consumption Survey (MECS) in 1998 presented in Fig 3Process heating, by which clinker is made in large kilns, accounts for about 90% of the natural gas consumption Cembureau [48] experimented vertical roller mills for coal grinding and achieved an energy saving of 7–10 kW h/t coal Buzzi, S, Sassone, G, 1993 Optimization of clinker cooler operation [82] Birch E Energy savings in cement kiln systems energy efficiency in the cement industry Elsevier Applied Science; 1990 118–128 [83] Cowi, C An overview of energy savings measures for cement industriesCement Additives Division 1 Improvement of cement performances through the use of grinding aids in vertical roller mill PD’Arcangelo, MMagistri – Mapei SpA, Milan, Italy Abstract Due to the stringent requirement of energy saving, the use of vertical Improvement of cement performances through the use of grinding The consumption of energy by the cement grinding operation amounts to one third of the total electrical energy used for the production of cement The optimization of this process would yield substantial benefits in terms of energy savings and capacity increase Optimization of the Cement Ball Mill OperationOPTIMIZATION OF CEMENT GRINDING OPERATION IN BALL MILLS
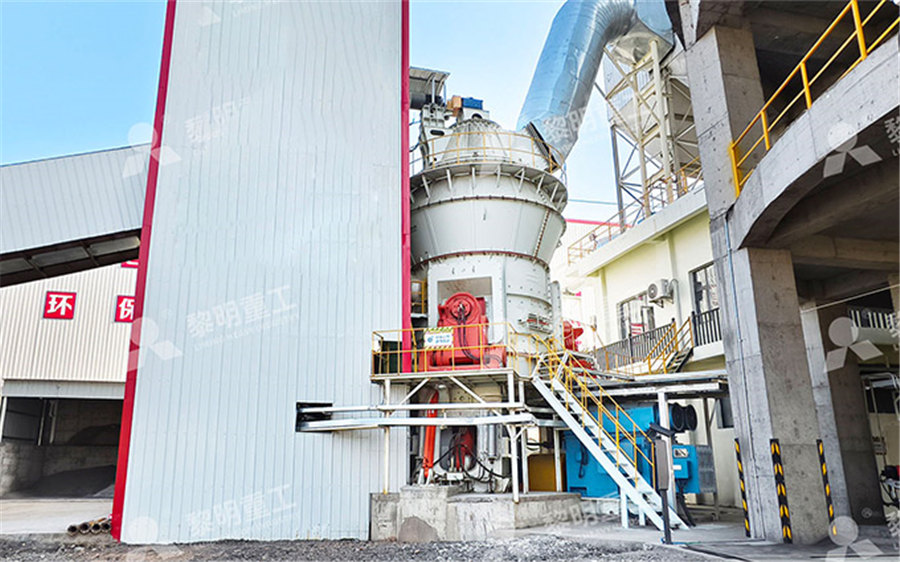
Saving and Efficient Equipment For Cement Industry Scribd
Saving and Efficient Equipment for Cement Industry Free download as PDF File (pdf), Text File (txt) or read online for free Great Wall Machinery provides energy saving and efficient equipment for the cement industry, including vertical roller mills, ball mills, and rotary kilns Vertical roller mills offer high grinding efficiency and lower energy consumption compared to ball mills