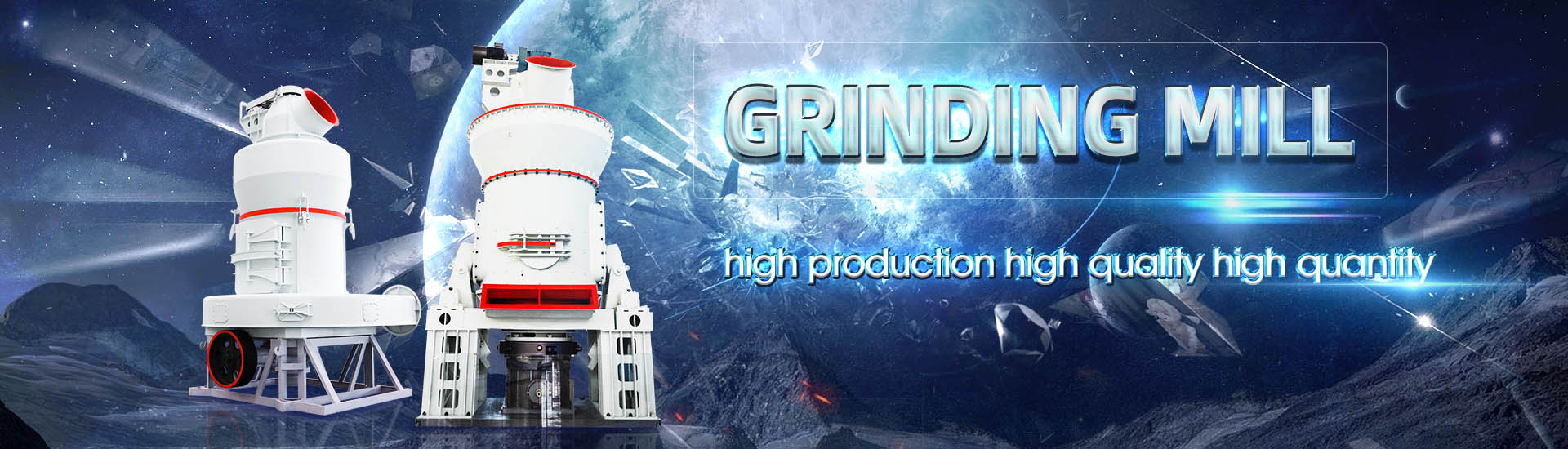
Steelmaking ladle Steelmaking ladle Steelmaking ladle
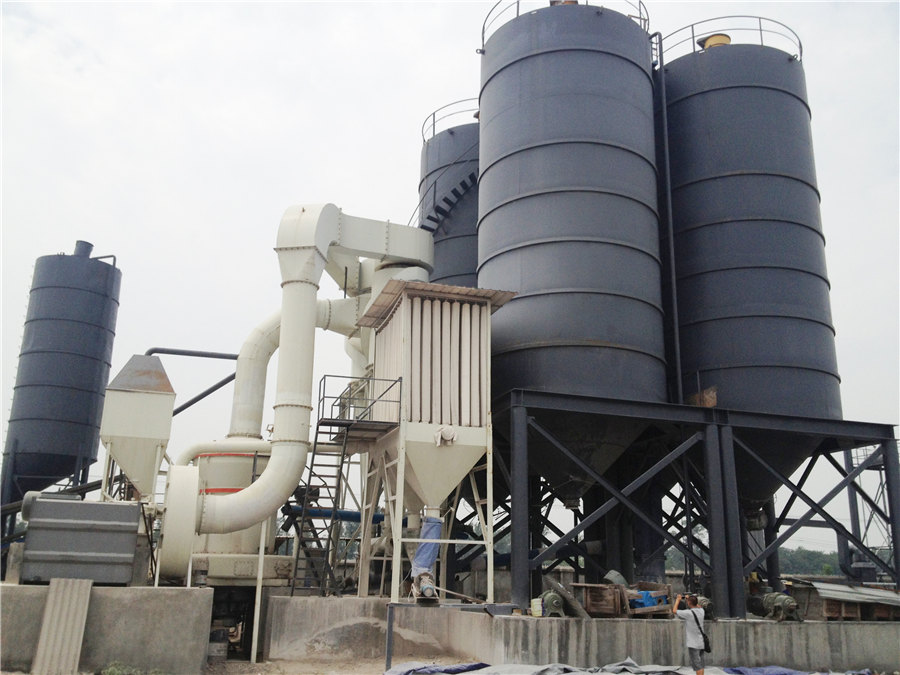
Unlocking the Secrets of Steelmaking Ladles: Crucial
2024年6月3日 Steelmaking ladles are essential in the steel production process, designed to transport and refine molten metal while withstanding extreme temperatures and chemical corrosion They come in various types tailored for 2014年4月23日 Ladle metallurgy is sometimes also called ladle refining or secondary steelmaking Ladle metallurgy processes are normally performed in ladles Tight control of ladle metallurgy is associated with the production of Ladle Metallurgy IspatGuru2022年6月1日 The ladle furnace (LF) is widely used in the secondary steelmaking process in particular for the desulfurization, alloying, and reheating of liquid steel prior to the casting processLadle Steelmaking Processes Using FactSage and Its observe in actual industrial processes of steelmaking with ladle metallurgy Further validation with actual industrial data will help develop FactSage models as effective guiding tools for the Ladle Steelmaking Processes Using FactSage and Its Macro Facility
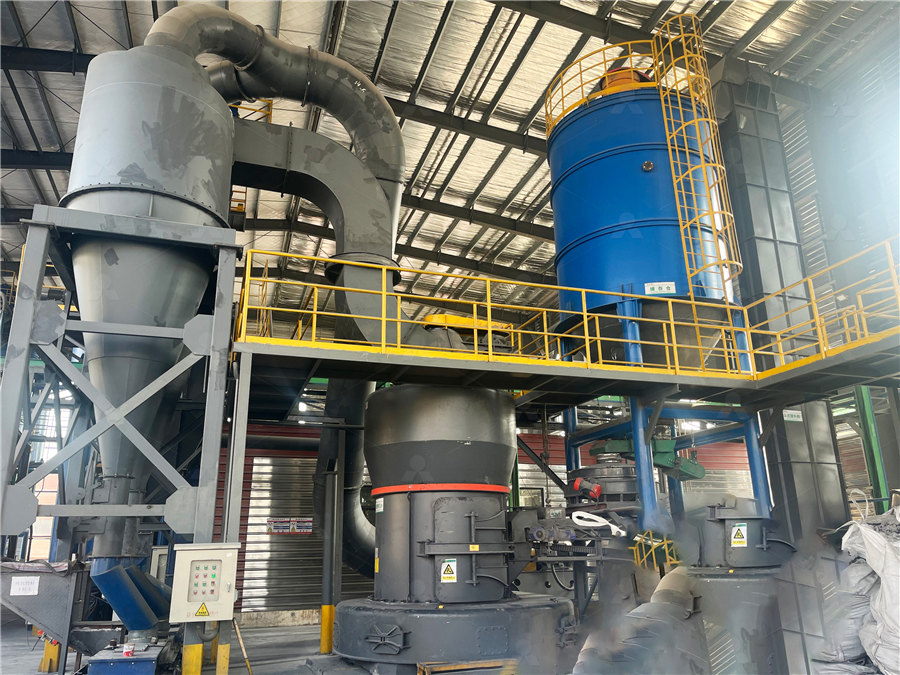
Steel ladle exchange models during steelmaking and continuous
2017年6月1日 The models and influencing factors of steel ladles exchange during the steelmaking and continuous casting process of H steel plant were investigated Based on 2024年6月20日 Steelmaking in the ladle, a key stage in the steel production process, involves the transport, refining and casting of molten steel The ladle, a refractorylined vessel, Advances in the technology of ladle steelmaking and the role of Process of ladle running in steelmaking workshop can generally be divided into two phases, which are the stage of ladles operating with molten steel and that of empty ladle runningPhysical Model of Ladle Running for Steelmaking Workshop2024年7月31日 Three interconnected equilibrium/adiabatic stoichiometricreactorbased approaches describe the overall ladle steelmaking process The macroprogramming facility Simulation of Ladle Steelmaking Process: Effective Equilibrium
.jpg)
MODELLING OF MASS TRANSFER IN A STEELMAKING LADLE
Mass transfer between liquid steel and slag is an important point during secondary metallurgy for prediction of the chemical reaction rate and adjustment of liquid steel composition We want to 2016年3月1日 Measurement the Thermal Profile of Steelmaking Ladle with Subsequent Evaluation the Reasons of Lining Damage March 2016; Archives of Metallurgy and Materials 61(1):279282;(PDF) Measurement the Thermal Profile of Steelmaking Ladle Secondary steelmaking in ladles has become an integral part of steelmaking Ladles have additional heating facility and are called Ladle furnaces (LF) There are several practices adopted for degassing, like vacuum tank deg asser, stream degassing and recirculation degassing In recirculation degassing steel is made to flow fromKey words: Primary steelmaking, ladle metallurgy, ingot casting 2024年8月14日 VAD steelmaking, or Vacuum Arc Degassing, is a process that refines molten steel under vacuum to remove impurities and control chemical composition, essential for producing highgrade steel used in critical The Art of VAD Steelmaking: From Tradition to
.jpg)
Analysis of Ladle Turnover and Matching Based on the Modern Steelmaking
PDF On Jan 1, 2021, 小明 董 published Analysis of Ladle Turnover and Matching Based on the Modern Steelmaking Process Find, read and cite all the research you need on ResearchGateLadle nozzle filling compound is used to prevent erosion and corrosion of slide plates and the ladle nozzle during steel tapping, and acts as a seal until casting begins to prevent leakage or breakouts The material needs to sinter at steel making temperatures to form a protective hard layer while not fusing, and slight expansion is desired to avoid gaps forming Common Ladle Nozzle Filling Compound PDF Refractory SteelmakingIRONMAKING AND STEELMAKING Ladle Furnaces Since the early ‘80s Danieli has been among the leaders in secondary refining for ordinary, specialty and stainless steels The knowhow gained over many years has been used to develop and optimize equipment and processes, and also to meet our customers’ most stringent requirementsProducts › Ironmaking and steelmaking › Ladle Furnaces Since 2021年9月1日 Powder injection metallurgy can effectively improve the reaction efficiency, ameliorate the properties, and reduce the production cost of steel This paper reviews recent innovations in submerged gaspowder injection technologies in the converter steelmaking, electric arc furnace (EAF) steelmaking, and ladle refining processesApplication of submerged gaspowder injection technology to steelmaking

A New and Highly Efficient Argon Blowing Mode for a 70t Steelmaking Ladle
Download Citation On Jan 1, 2020, Zhanpeng Tie and others published A New and Highly Efficient Argon Blowing Mode for a 70t Steelmaking Ladle Find, read and cite all the research you need on 2017年6月1日 The models and influencing factors of steel ladles exchange during the steelmaking and continuous casting process of H steel plant were investigated Based on analysis of the operation process and turnover time of steel ladles, relationship models for the turnover number, turnover rate, continuous casting number, number of ladles with additional turnover, Steel ladle exchange models during steelmaking and continuous the ladle Thus, the potential for mixing of slag and liquid steel is greater for steel produced by the BOF route Regardless of the primary steelmaking process (BOF or EAF), slag carryover from the primary metallurgical vessel into the ladle is harmful for Making Ferroniobium Additions During Ladle Steelmaking Optimizing 2021年9月1日 Powder injection metallurgy can effectively improve the reaction efficiency, ameliorate the properties, and reduce the production cost of steel This paper reviews recent innovations in submerged gaspowder injection technologies in the converter steelmaking, electric arc furnace (EAF) steelmaking, and ladle refining processes Using bottomblowing O 2lime Application of submerged gaspowder injection technology to steelmaking
.jpg)
Ladle Metallurgy an overview ScienceDirect Topics
2012年1月5日 Ladle metallurgy is a process associated with the clean steelmaking process, wherein the process follows after the steel from converter or electric arc furnace, which may involve deoxidation, decarburization, and fine chemical adjustment of fine alloying elements or even the gases in the steel2015年11月24日 Following a successful benchmark for the steelmaking tundish in 2009 and 2010, the latest benchmark covered the subject of mixing and alloying phenomena in a steelmaking ladleMultiphase flow simulation of a steelmaking ladle2003年1月1日 The experiment results showed that the prediction accuracy of ladle refractory corrosion reaches 92%, which met the requirements of steelmaking plant for ladle safety monitoring in green and Modelling of Temperature Distribution in Refractory Ladle The method of using the ladle management system for steelmaking and refining includes the following steps: [6] International Journal of Frontiers in Engineering Technology ISSN 2706655X Vol2, Issue 1: 95105, DOI: 1025236/IJFET2020 Published by Francis Academic Press, UKA ladle management system and method for steelmaking and
.jpg)
Schematic illustration of gas stirring in the ladle Download
In ladle metallurgy of steelmaking, the role of gas injection into the metal bath is been studied to a great extent as it improves the quality of steel– In the ladle wall, heat flow occurs only in radial direction (wall height wall thickness) – In the ladle bottom and the slag, heat flow occurs only in axial direction 24 Ladle Lining The ladle lining consists of inner lining, back lining, insulating lining and steel shell, Fig 1 There exist two different types of inner linings Modelling of Temperature Distribution in Refractory Ladle Lining 2003年8月15日 Modelling of Temperature Distribution in Refractory Ladle Lining for Steelmaking @article{Volkova2003ModellingOT, title={Modelling of Temperature Distribution in Refractory Ladle Lining for Steelmaking}, author={Olena Volkova and Dieter Janke}, journal={Isij International}, year={2003}, volume={43}, pages= {11851190 Modelling of Temperature Distribution in Refractory Ladle Lining This is due to the rapid development of contemporary steelmaking and new ladle designs The purpose of this paper is to review some of the literature dealing with heat transfer in steelmaking ladle refractories and mathematical models thereof The reviewed works are classified into experimentallyand theoreticallyfocused investigations(PDF) Heat transfer in steelmaking ladle refractories and steel
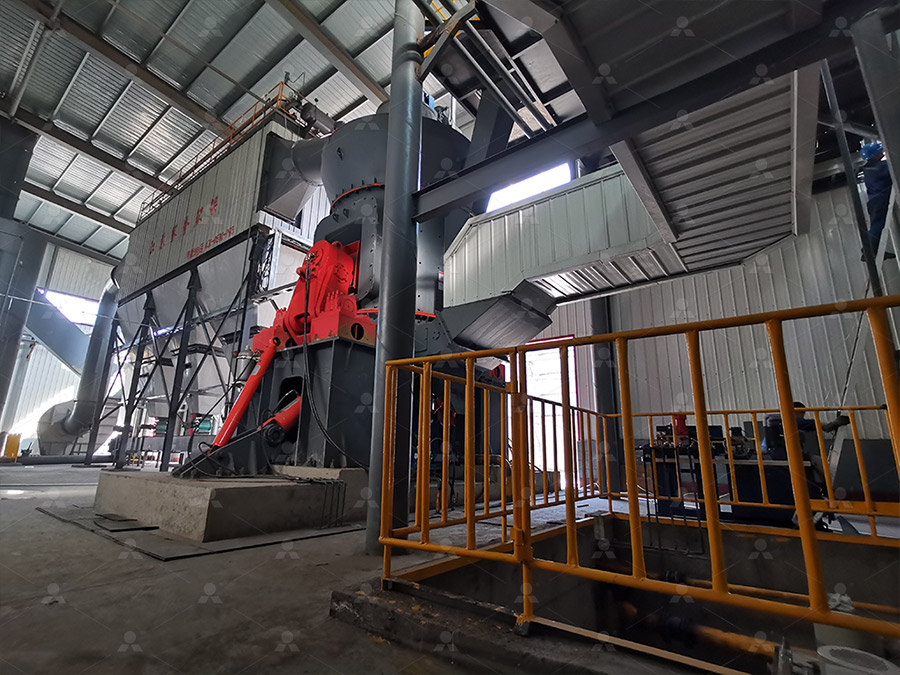
Steelmaking North American Forgemasters
The ladle furnace steelmaking is accomplished with split ASEASKF secondary steelmaking equipment: Two ladle refining units; A custom alloy delivery system ; One ladle vacuum degasser; THE PROCESS First, scrap is loaded into clamshell buckets and charged into an ultrahigh powered (UHP) eccentric bottomtapping (EBT) electric arc furnace1 Ladle Furnace Function Ladle furnace steelmaking is an important process used to refine the molten steel melted in the primary smelting furnace (electric arc furnace, open hearth furnace and converter), and can adjust the temperature of molten steel, buffer the process and meet the requirements of continuous casting and continuous rollingLadle Furnace Steelmaking Hani MetallurgySecondary treatment and casting ladles play a substantial role in steelmaking Initially ladles were used exclusively as transfer vessels At present, they serve as versatile steel reactors where homogenisation, deoxidation, desulphurisation and alloying are Modelling of Temperature Distribution in Refractory Ladle Lining 2024年11月19日 Steel Ladle Metallurgy, Alloying, Refining: The carrying out of metallurgical reactions in the ladle is a common practice in practically all steelmaking shops, because it is costefficient to operate the primary furnace Steel Ladle Metallurgy, Alloying, Refining Britannica
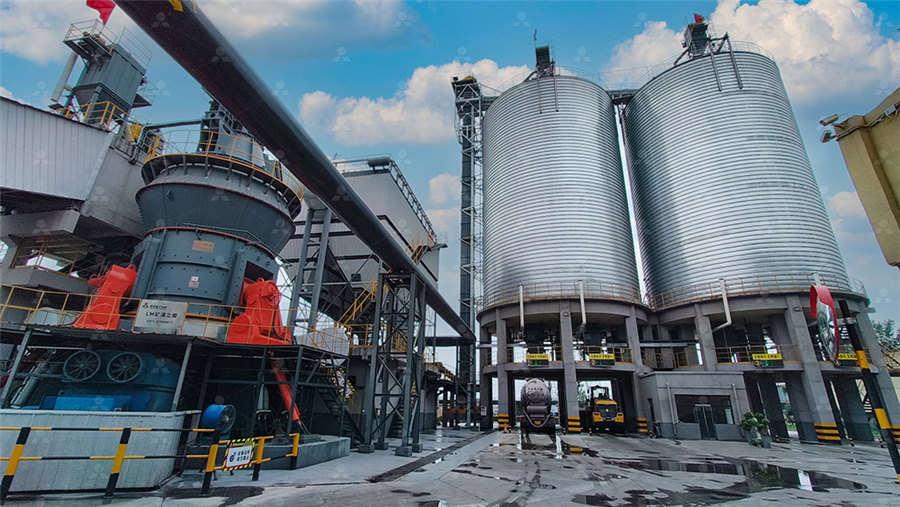
Method of preheating steelmaking ladles Google Patents
A method for when preheating a ladle for use in steelmaking where less fuel is consumed in heating the ladle efficiently accurately to a controlled temperature A temperature of a preheating process is varied by controlling a burner of the heating unit based on measurements of refractories of the ladle taken by a pyrometer The heating unit includes an emissive coating 2001年5月1日 As a first step towards prediction of temperatures in secondary steelmaking, mathematical modelling of fluid flow and heat transfer in ladle furnace was undertaken A twodimensional quasisingle phase model has been developed for turbulent recirculating flow by solving Reynolds averaged NavierStokes equations along with a twoequation ke model The Prediction of temperature in secondary steelmaking: In the downstream area of steelmaking, attempts have been made to automatically identify slabs and ingots using bar codes and warm embossed stamping [22] However, these visual techniques for identification purposes were found to be not feasible on steelmaking ladles, probably due to the harsh environment (dust and high temperaAdvanced strategies for alloying processes in steelmaking ladles2019年4月22日 10 10 BASIC OXYGEN FURNACE (BOF) From the blast furnace, molten pig iron (hot metal) is poured into a torpedo car and subsequently into a ladle The metal in the ladle is sent directly to the basic oxygen furnace (BOF) or to a pretreatment stageBASIC OXYGEN STEELMAKING (BOS) The Processing Route
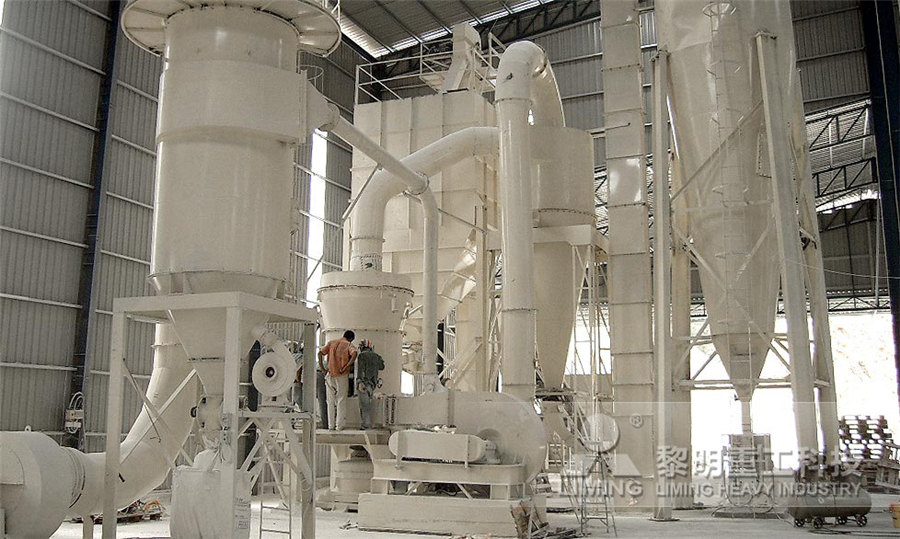
(PDF) Application of ladle electric steelmaking slag as a flux
2020年8月13日 Silicomanganese slag and ladle electric steelmaking slag were used in the experiments Flux additive was introduced in a ratio of 5, 10, 20, 30, 50% to the silicomanganese slag2017年6月1日 Download Citation Steel ladle exchange models during steelmaking and continuous casting process The models and influencing factors of steel ladles exchange during the steelmaking and Steel ladle exchange models during steelmaking and2001年8月1日 Transient, turbulent flow and heat transfer in a ladle during the holding period are numerically investigated The ladle refractories including the working lining, safety lining, insulation layer, and steel shell have been simultaneously taken into account No assumptions are made for the heat transfer between the liquid steel and the inside ladle walls Both the initial Transient flow and heat transfer in a steelmaking ladle during 2016年3月1日 Measurement the Thermal Profile of Steelmaking Ladle with Subsequent Evaluation the Reasons of Lining Damage March 2016; Archives of Metallurgy and Materials 61(1):279282;(PDF) Measurement the Thermal Profile of Steelmaking Ladle
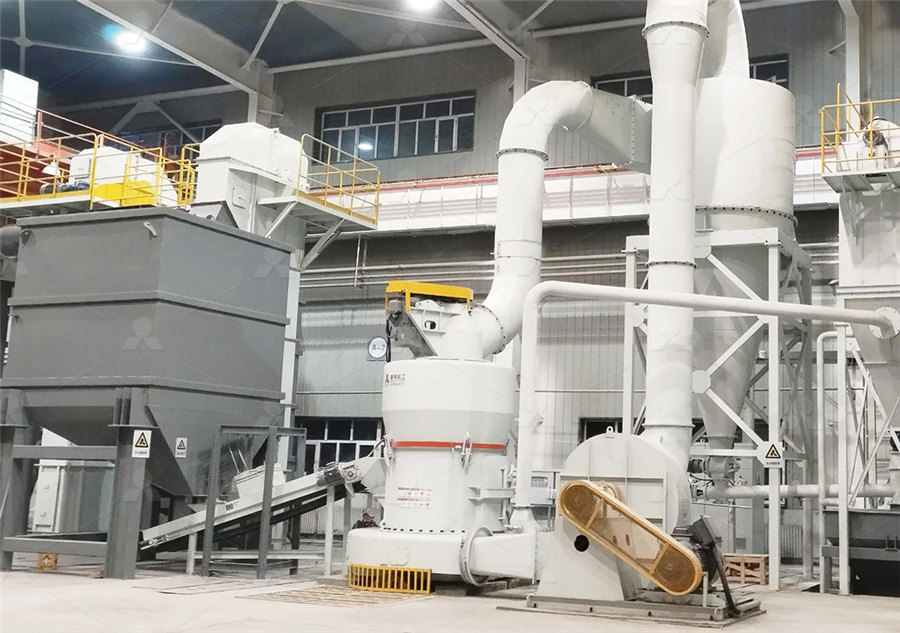
Key words: Primary steelmaking, ladle metallurgy, ingot casting
Secondary steelmaking in ladles has become an integral part of steelmaking Ladles have additional heating facility and are called Ladle furnaces (LF) There are several practices adopted for degassing, like vacuum tank deg asser, stream degassing and recirculation degassing In recirculation degassing steel is made to flow from2024年8月14日 VAD steelmaking, or Vacuum Arc Degassing, is a process that refines molten steel under vacuum to remove impurities and control chemical composition, essential for producing highgrade steel used in critical The Art of VAD Steelmaking: From Tradition to PDF On Jan 1, 2021, 小明 董 published Analysis of Ladle Turnover and Matching Based on the Modern Steelmaking Process Find, read and cite all the research you need on ResearchGateAnalysis of Ladle Turnover and Matching Based on the Modern Steelmaking Ladle nozzle filling compound is used to prevent erosion and corrosion of slide plates and the ladle nozzle during steel tapping, and acts as a seal until casting begins to prevent leakage or breakouts The material needs to sinter at steel making temperatures to form a protective hard layer while not fusing, and slight expansion is desired to avoid gaps forming Common Ladle Nozzle Filling Compound PDF Refractory Steelmaking
.jpg)
Products › Ironmaking and steelmaking › Ladle Furnaces Since
IRONMAKING AND STEELMAKING Ladle Furnaces Since the early ‘80s Danieli has been among the leaders in secondary refining for ordinary, specialty and stainless steels The knowhow gained over many years has been used to develop and optimize equipment and processes, and also to meet our customers’ most stringent requirements2021年9月1日 Powder injection metallurgy can effectively improve the reaction efficiency, ameliorate the properties, and reduce the production cost of steel This paper reviews recent innovations in submerged gaspowder injection technologies in the converter steelmaking, electric arc furnace (EAF) steelmaking, and ladle refining processesApplication of submerged gaspowder injection technology to steelmaking Download Citation On Jan 1, 2020, Zhanpeng Tie and others published A New and Highly Efficient Argon Blowing Mode for a 70t Steelmaking Ladle Find, read and cite all the research you need on A New and Highly Efficient Argon Blowing Mode for a 70t Steelmaking Ladle2017年6月1日 The models and influencing factors of steel ladles exchange during the steelmaking and continuous casting process of H steel plant were investigated Based on analysis of the operation process and turnover time of steel ladles, relationship models for the turnover number, turnover rate, continuous casting number, number of ladles with additional turnover, Steel ladle exchange models during steelmaking and continuous
.jpg)
Making Ferroniobium Additions During Ladle Steelmaking Optimizing
the ladle Thus, the potential for mixing of slag and liquid steel is greater for steel produced by the BOF route Regardless of the primary steelmaking process (BOF or EAF), slag carryover from the primary metallurgical vessel into the ladle is harmful for