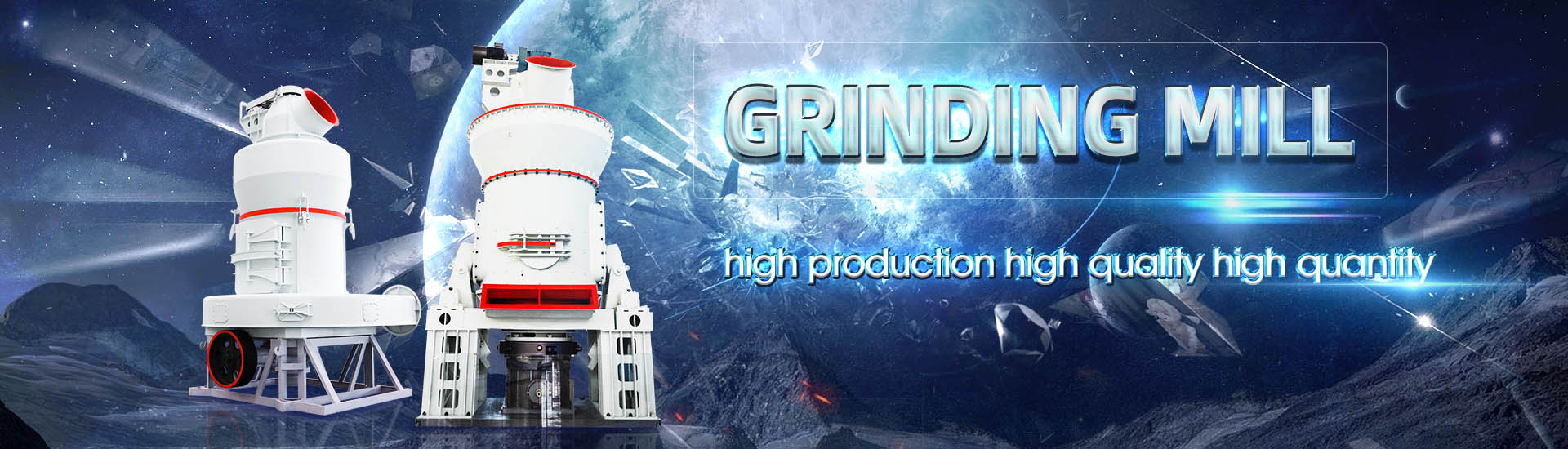
How to refuel the accumulator of cement raw material vertical mill
.jpg)
Vertical roller mill for raw Application p rocess materials
Vertical roller mills are adopted in 20 cement plants (44 mills) in Japan In the vertical roller mill which is widely used in the raw material grinding process, raw materials input grinding table 2013年5月15日 The vertical raw mill uses compression, shear and impact forces for grinding raw materials into powder Materials are fed into the center of a grinding plate and distributed Vertical raw mill pradeep kumar PPT SlideShareVertical roller mills (VRM) have found applications mostly in cement grinding operations where they were used in raw meal and finish grinding stages and in power plants for coal grinding (PDF) CEMENT RAW MATERIAL GRINDING ; VERTICAL ROLLER The document discusses optimization and operation of vertical roller mills (VRMs) Key points include: 1) Continuously monitor and adjust process parameters to find the optimum operating Optimization of Vertical Raw Mill Operation PDF
.jpg)
Vertical raw mill Cement Plant
Vertical raw mill is an ideal grinding mill that crushing, drying, grinding, grading transfer set in one It can be widely used in cement, electric power, metallurgy, chemical industry, nonmetallic This document provides the standard operating procedure for starting up, shutting down, and operating cement mills at Anjani Portland Cement Limited It outlines the specific sequence SOPStartup Shutdown and Operation of Cement MillsDrying of moisture in raw materials is required for effective grinding and subsequent handling of raw meal This is achieved normally by ducting part of the kiln exhaust gas through the mill Raw Material DryingGrinding Cement Plant OptimizationThe Vertical Raw Mill (VRM) is a pivotal component in the grinding process within a cement plant Efficient control and optimization of this process are critical for the quality of the end product Cement Application Page Vertical Raw Mill Promecon
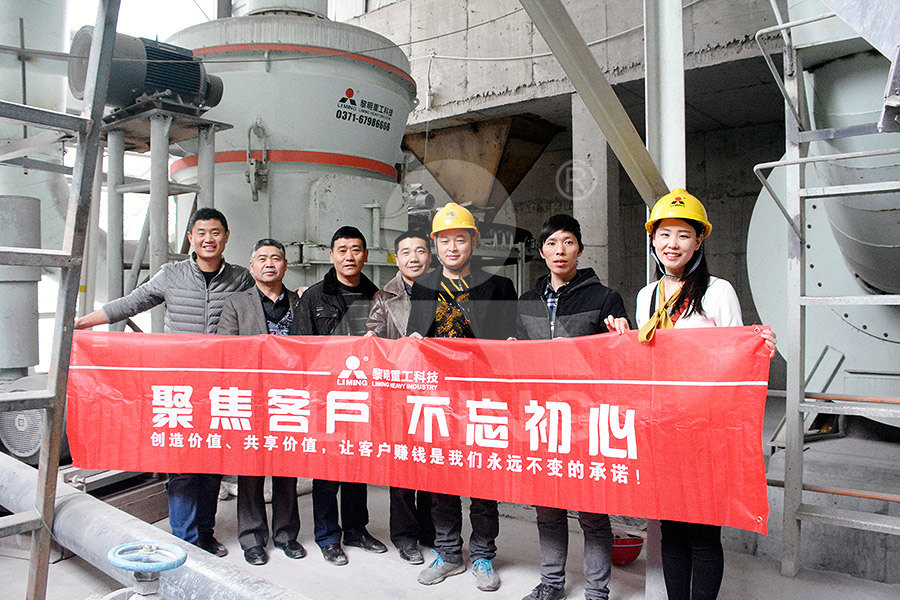
Review on vertical roller mill in cement industry its performance
2021年1月1日 Raw mix, high grade limestone, sand and iron ore are transported from their bins to raw mills for drying and further fine grinding The raw mill is either a Ball mill with two vertical planetary gear reducer At the same time, raw material is dried by hot gas induced through the louver ring installed at outer side of the table Construction This Machine is a vertical type roller mill which performs drying grinding classification and pneumatic transportation simultaneously Material is fed at aVERTICAL ROLLER MILLS AMCLOur bestinclass OK™ Mill is a globally successful vertical roller mill solution for grinding raw material, cement and slag Its cuttingedge design features consistently deliver the highest quality products with the greatest efficiency It OK™ Raw and Cement MillMixing: according to the requirement of clinker, compound desired raw material for cement production line Grinding: grinding all materials into required fineness by cement mill Cement ball mill and vertical cement mill are two common Preparation Of Cement Raw Material Cement Mill,
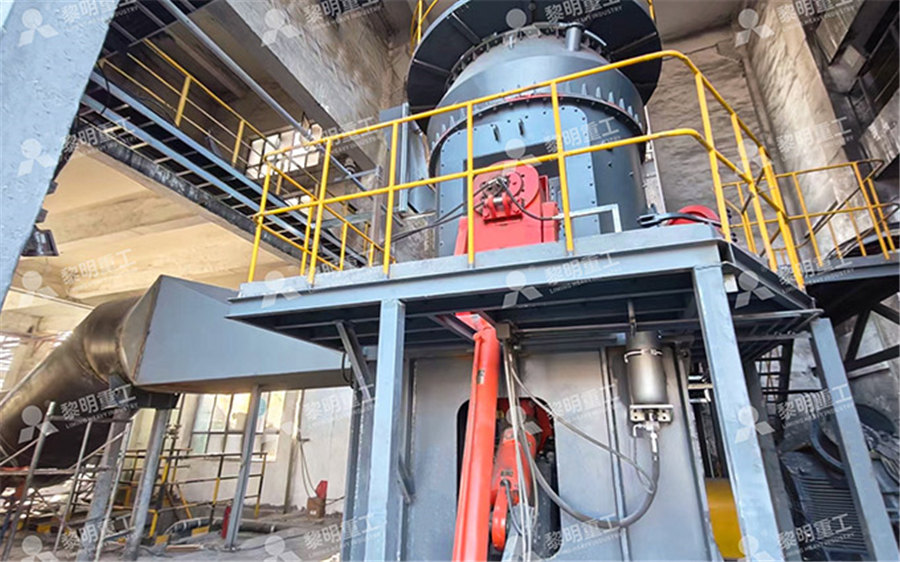
Vertical raw mill pradeep kumar PPT SlideShare
2013年5月15日 Exception handling • 21 vertical roller mill vibration is too large: (1) Feed uneven, when the mixture into the vertical roller mill over the powder, the vertical roller mill's loading rate, leading to the vertical roller mill on the thin material, and even disc direct contact with the roller, resulting in mechanical milling; when into the vertical roller mill multimaterial mixture 2024年1月23日 The cement mill is a crucial equipment in cement production, operating through key steps including feeding, grinding, separation, and discharge Initially, raw materials such as clinker and auxiliary materials are conveyed to the cement grinding mill through a feeding systemHow To Optimize The Operation Of The Cement Mill(22) 26112019 (43) 02072020 (57) An energysaving optimization method of a cement raw material vertical mill system Safe, convenient and reasonable auxiliary decisionmaking is smartly provided by a machine learning method without changing any structure and principle of a production equipment, adding additional measuring spots and affecting normal productionEnergysaving optimization method of cement raw material vertical mill 2021年6月24日 To reduce the proportion of very fine and very coarse particles, the raw mill circuit should be optimised to produce the narrowest practical PSD, like those usually produced by vertical roller mills (VRMs) Another option may be to replace the problematic raw material with a finer, easiertogrind and/or easiertoburn alternativeBetter and cheaper cement: Optimising raw material properties
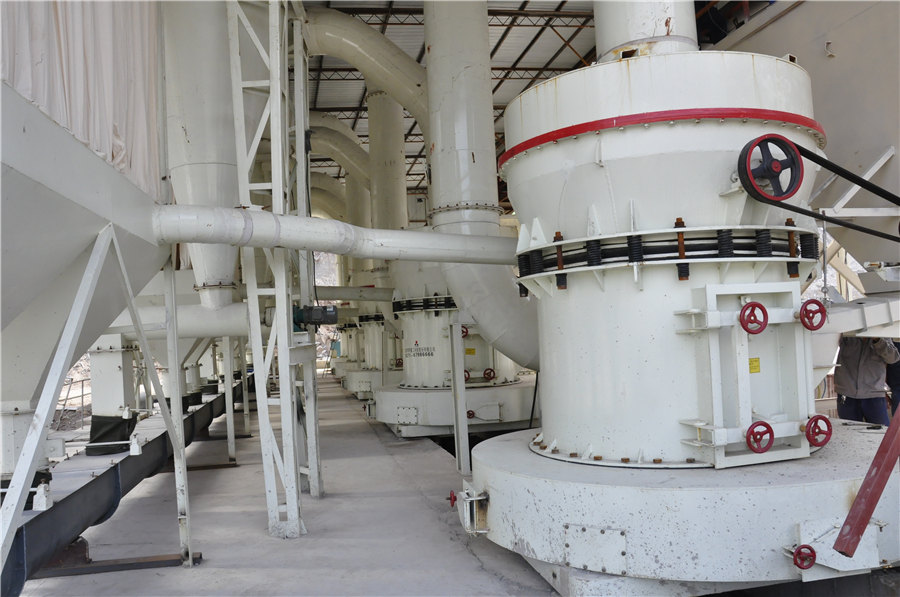
How Does a Raw Mill Work in a Cement Industry
2024年2月23日 The operation of the cement raw mill is a critical step in cement production By grinding the raw materials into a fine powder, these powders can be more easily mixed with other cement ingredients and burn more evenly during the cement clinker process Therefore, the efficient operation of the cement raw mill directly impacts the production efficiency and quality a Loesche mill, with a grinding track diameter of only 11 metres, was used as long ago as 1935 However, the breakthrough in grinding this type of material on the vertical roller mill did not take place until the beginning of the 1990’s 1935 The first Loesche mill for grinding cement clinker, an LM 11, was commissioned in Joao Pessao, Brazil2 µm 5 µm LoescheCommonly, there are three hot types of cement mill in the cement industry: cement ball mill, Raymond mill, and vertical cement mill AGICO Cement can supply cement mill according to your requirements We also provide the Cement Mill Cement Ball Mill Vertical Cement Mill sbm how to accumulate the accumulator of cement raw material vertical millraw mill hydraulic system hydraulic accumulator used at raw mill hydraulic accumulator in vertical raw mill hydraulic accumulator,hydraulic fluid,hydraulic oil,hydraulic #187; Get Price hydraulic accumulator used at raw mill,A hydraulic power pack is the heart of a hydraulic system and provides energy for the sbm/sbm how to accumulate the accumulator of cement raw material
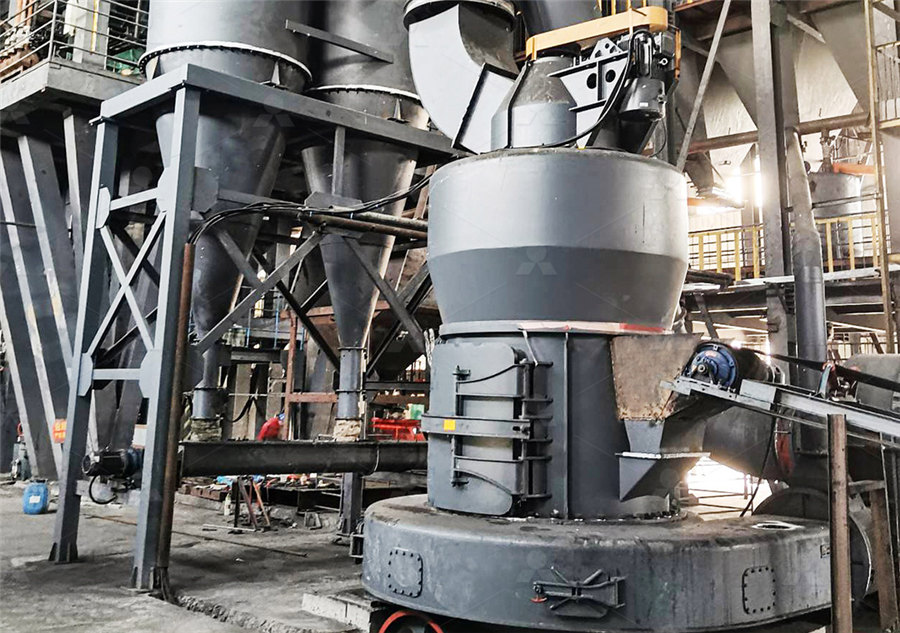
(PDF) CEMENT RAW MATERIAL GRINDING ;
Vertical roller mills (VRM) have found applications mostly in cement grinding operations where they were used in raw meal and finish grinding stages and in power plants for coal grinding The mill combines crushing, grinding, Vertical mill merges fine crushing, drying, grinding and powder selecting into a single, which simplifies the production process It has the advantages of high grinding efficiency, low power consumption, large feed particle size, easy adjustment of grinding fineness, simple process, less land occupation, low noise, simple operation and maintenance, low cost and less wear Vertical Mill In Cement Plant Cement Vertical Mill AGICO CementVertical Raw Mill is a main equipment that is used in grinding or refining raw materials at PT Semen Baturaja (Persero) Tbk using a tire roller that can produce raw meal with theANALISA KINERJA ALAT VERTICAL RAW MILL PABRIK II PT2014年11月6日 3 2 Cement raw material has been almost exclusively ground in roller mills (vertical airswept grinding mills) since the sec ond half of the 20th century Loesche was and is the pio neer of this technology Hundreds of Loesche mills have been used in the cement industry across the world to the present dayLoesche Technology Always a Step Ahead: Loesche Mills for Cement Raw
.jpg)
A Survey and Analysis on Electricity Consumption of Raw Material Mill
Sustainability 2021, 13, 1126 2 of 11 decomposition waste gas as a drying heat source for suspension preheater kiln, etc, have promoted the development of raw material preparation technologyraw material grinding, a modular vertical roller mill with 5 m table diameter and 4 rollers was added The existing kiln systems were partly modernized, one kiln system was replaced by new system Grinding Process Optimization Featuring Case Studies and Application of Vertical Roller Mill in Cement Industry Vertical roller mill (VRM) technology has become an integral part of the cement industry, offering several advantages over traditional grinding mills Today, this type of grinding machine is becoming more and more popular in both the raw material grinding process and the cement grinding Application of Vertical Roller Mill in Cement ProductionVertical Mill Calculations Free download as Powerpoint Presentation (ppt / pptx), PDF File (pdf), Text File (txt) or view presentation slides online There are two main layouts for a vertical roller mill (VRM) system, with product collection in cyclones or a filter The power consumption of a VRM is calculated using factors like the specific grinding pressure, roller dimensions, Vertical Mill Calculations PDF Mill (Grinding) Nozzle
.jpg)
Raw Mill – Raw Mill In Cement Plant AGICO Cement
AGICO Cement Vertical Mill AGICO Cement Ball Mill Cement Vertical Mill Grinding System Cement vertical mill, also called roller mill, is another raw mill commonly used in cement plants Compared with the cement ball mill, it has a Brochure154LoescheMillsforcementrawmaterialENpdf Free download as PDF File (pdf), Text File (txt) or read online for free Cement raw material has been almost exclusively ground in roller mills (vertical airswept grinding mills) Brochure 154 LoescheMills For Cement Raw Material 2023年3月1日 β [1 − α; p 2; n − p − 1 2] = (1–α) th quantile of β [p 2; n − p − 1 2] distribution For α = 005, the number of outliers is 44 among 280 data corresponding to an upper limit control U C L M a h a l a n o b i s = 455 as illustrated in Fig 3The results of these outliers have been carefully analyzed by a process expert from the cement plant Indeed, if an outlier carrying Efficient machine learning model to predict fineness, in a vertical raw 2022年10月3日 A raw mill’s production line is to grind the raw material mixed with limestone, clay and basalt of certain proportion; it decides the quality of the cement clinker(PDF) ANALISA KINERJA ALAT VERTICAL RAW MILL PABRIK II PT
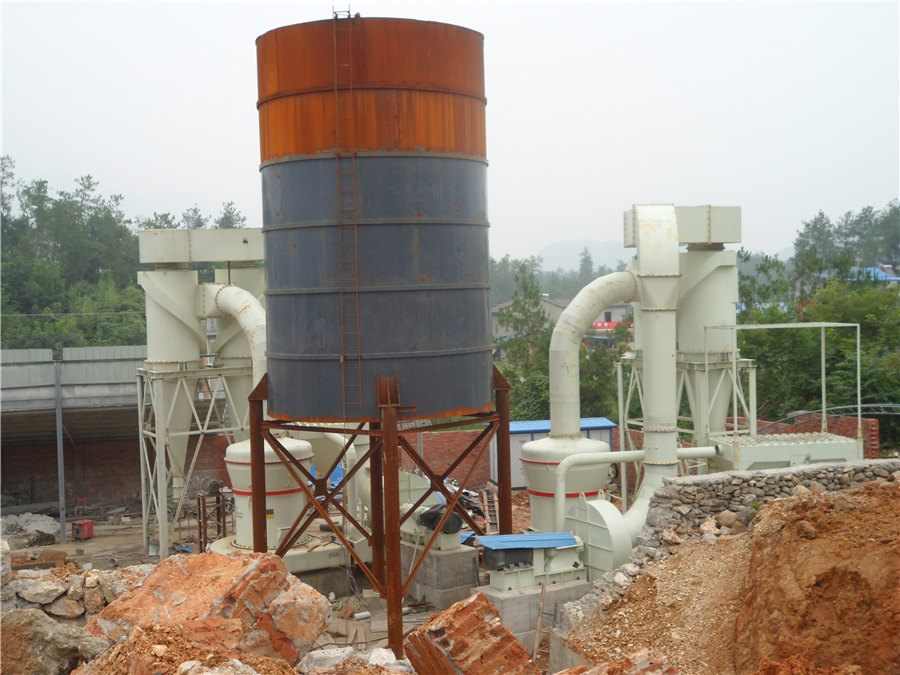
Raw Mill Feeding Cement Plant Optimization
After monitoring and controlling the quality of incoming raw material, the area of high activity for quality department to ensure quality mix for smooth production of high quality of cement is “mill feeding system” The system consists of material hoppers/bins, weighing, conveying, venting and mill feeding gate Mill Feeding Hoppers2016年9月1日 Modern cement plants trend for the usage of vertical mill in cement grinding because of its many advantages of lower energy requirements, higher feed rates, simple layout (drying, grinding Operational parameters affecting the vertical roller mill menyatakan bahwa Vertikal roller mill / vertical cement mill adalah alat utama dalam proses produksi transport material sampai menjadi produk semen sesuai dengan kualitas produk yang diinginkanANALISIS PENGGILINGAN DAN PENCAMPURAN KARAKTERISTIK 2024年1月15日 Sun et al [9] carried out study of a roller mill (HRM 4800 by Hefei Zhong Ya, China) and analysed air flow patterns in the mill to improve the energy efficiency of the mill Shah et al [ 10 ] used modelling to optimise the performance of a coal pulveriser by studying the influence of variation in inlet vane angles on the collection efficiency of the powder and desired Optimisation of the performance of a new vertical roller mill by
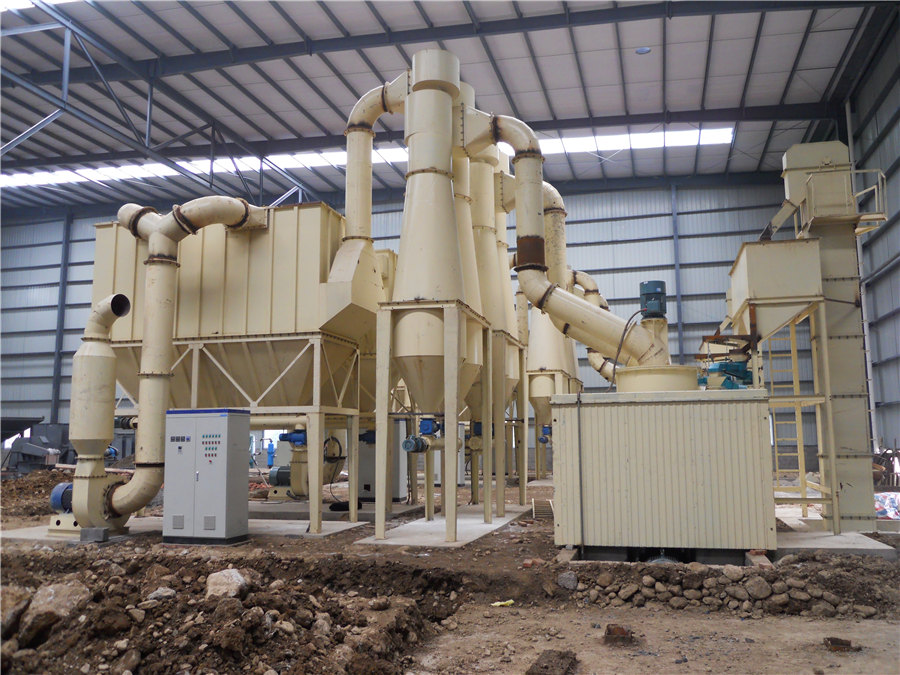
The important role of vertical roller mills in the cement industry
It is widely used in clinker grinding production of cement plant and slag grinding plant CHAENG can provide various types of vertical cement mills with productivity of 50250t/h The biggest advantage of CHAENG is to have a large casting base and large machining workshops, which greatly shortens the delivery cycle of cement vertical millFor the preparation of cement raw material, cement, and granulated blastfurnace slag with small to medium output rates, the MVR mill with conventional drive is the right choice This mill type is by the way the core piece of our modular ready2grind systemCement mills and raw mills for small to medium throughput ratesvertical planetary gear reducer At the same time, raw material is dried by hot gas induced through the louver ring installed at outer side of the table Construction This Machine is a vertical type roller mill which performs drying grinding classification and pneumatic transportation simultaneously Material is fed at aVERTICAL ROLLER MILLS AMCLOur bestinclass OK™ Mill is a globally successful vertical roller mill solution for grinding raw material, cement and slag Its cuttingedge design features consistently deliver the highest quality products with the greatest efficiency It OK™ Raw and Cement Mill
.jpg)
Preparation Of Cement Raw Material Cement Mill,
Mixing: according to the requirement of clinker, compound desired raw material for cement production line Grinding: grinding all materials into required fineness by cement mill Cement ball mill and vertical cement mill are two common 2013年5月15日 Exception handling • 21 vertical roller mill vibration is too large: (1) Feed uneven, when the mixture into the vertical roller mill over the powder, the vertical roller mill's loading rate, leading to the vertical roller mill on the thin material, and even disc direct contact with the roller, resulting in mechanical milling; when into the vertical roller mill multimaterial mixture Vertical raw mill pradeep kumar PPT SlideShare2024年1月23日 The cement mill is a crucial equipment in cement production, operating through key steps including feeding, grinding, separation, and discharge Initially, raw materials such as clinker and auxiliary materials are conveyed to the cement grinding mill through a feeding systemHow To Optimize The Operation Of The Cement Mill(22) 26112019 (43) 02072020 (57) An energysaving optimization method of a cement raw material vertical mill system Safe, convenient and reasonable auxiliary decisionmaking is smartly provided by a machine learning method without changing any structure and principle of a production equipment, adding additional measuring spots and affecting normal productionEnergysaving optimization method of cement raw material vertical mill
.jpg)
Better and cheaper cement: Optimising raw material properties
2021年6月24日 To reduce the proportion of very fine and very coarse particles, the raw mill circuit should be optimised to produce the narrowest practical PSD, like those usually produced by vertical roller mills (VRMs) Another option may be to replace the problematic raw material with a finer, easiertogrind and/or easiertoburn alternative2024年2月23日 The operation of the cement raw mill is a critical step in cement production By grinding the raw materials into a fine powder, these powders can be more easily mixed with other cement ingredients and burn more evenly during the cement clinker process Therefore, the efficient operation of the cement raw mill directly impacts the production efficiency and quality How Does a Raw Mill Work in a Cement Industrya Loesche mill, with a grinding track diameter of only 11 metres, was used as long ago as 1935 However, the breakthrough in grinding this type of material on the vertical roller mill did not take place until the beginning of the 1990’s 1935 The first Loesche mill for grinding cement clinker, an LM 11, was commissioned in Joao Pessao, Brazil2 µm 5 µm Loesche