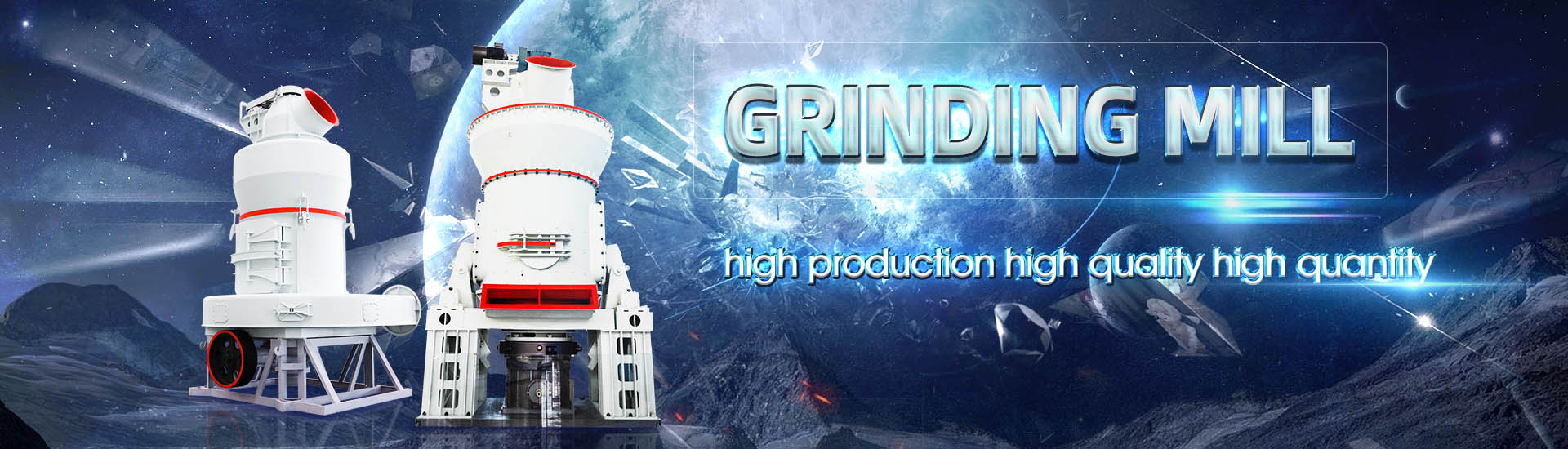
Equipment for producing pulverized coal, 2014
.jpg)
Performance of Pulverized Coal Combustion under High
2014年3月25日 In this paper, performances of pulverized coal combustion under the high preheated and oxygen deficient air are studied by both experimental and numerical 2019年1月1日 Paper presents short review of research problems, applied methods for solving problems and main results obtained by the researchers in Laboratory for Thermal Engineering (PDF) Review of the investigations of pulverized coal combustion 2019年2月14日 The aim of present paper is to review various aspects of pulverized coal combustion such as oxyfuel combustion, cocombustion of coal and biomass, emissions from A complete review based on various aspects of pulverized coal The article presents a review of modern technologies for firing up pulverized coalfired boiler units, as well as presents the original technology of electric ignition and the results of tests on the Novel technology of electric combustion of pulverized coal and
.jpg)
Technology Development for Advanced Pulverized CoalFired Boilers
1996年12月4日 New pulverized coalfired systems routinely installed today generate power at net thermal cycle efficiencies ranging from 34 to 37% (higher heating value) while removing up 2023年1月13日 In order to develop effective catalysts for use in pulverized coalfired boilers, researchers would need to consider a number of factors, including the chemical composition of Pulverized CoalFired Boilers: Future Directions of Scientific Research2023年1月13日 ways to improve the efficiency of pulverized coalfired boilers This could involve developing new combustion technologies that are able to more thoroughly burn the coal and (PDF) Pulverized CoalFired Boilers: Future Directions of Scientific 2015年1月5日 Equipment and systems for online monitoring of various species and conditions in coalfired plants will need to be developed Examples include nonintrusive techniques for Understanding pulverised coal, biomass and waste combustion –
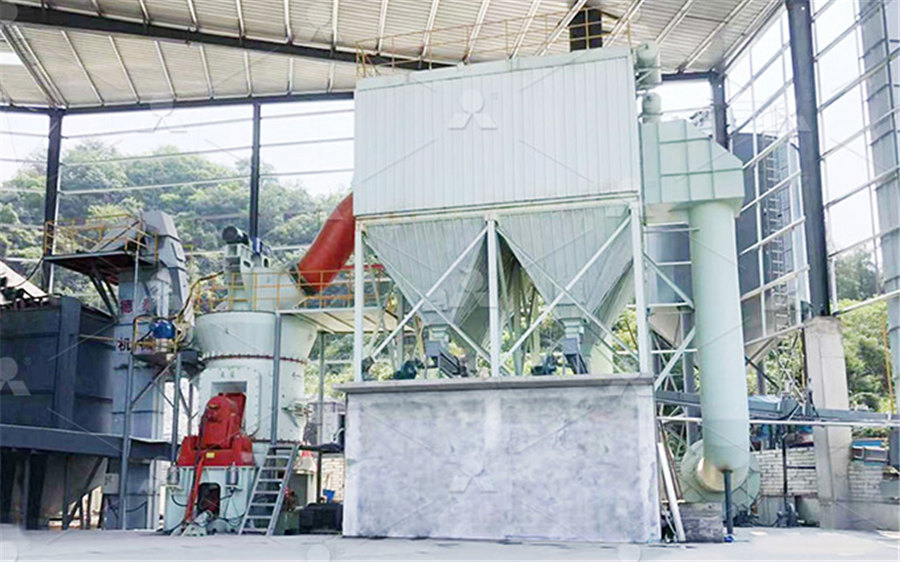
Coal Combustion Equipment SpringerLink
2024年1月1日 Coal combustion equipment is an equipment that converts the chemical energy of coal into heat energy through combustion According to the coal combustion mode, it can be The ATRITA pulverizer is a highspeed, compactly designed machine which reduces raw coal to pulverized coal by the combination of crushing, impact and attrition The AT RITA has A Comparison of Three Types of Coal Pulverizers Babcock PowerThe invention discloses grinding equipment for producing superfine pulverized coal, which belongs to the technical field of coal processing and comprises a base, a grinding box body, a motor, a heater, a first driving mechanism, a second driving mechanism, a suction fan, a third driving mechanism and a blower, wherein the surface of the base is fixedly connected with the CNA Grinding equipment for superfine pulverized coal JSC EVRAZ NTMK is the first metallurgical plant in modern Russia to launch a complex for the production and use of pulverized coal in blast furnace production Implementation of the project meets the objectives of introducing the best available technologies in blast furnace production at the plant`s industrial site, the project was developed on the basis of technical solutions of the Technology for the production and use of pulverized coal at JSC
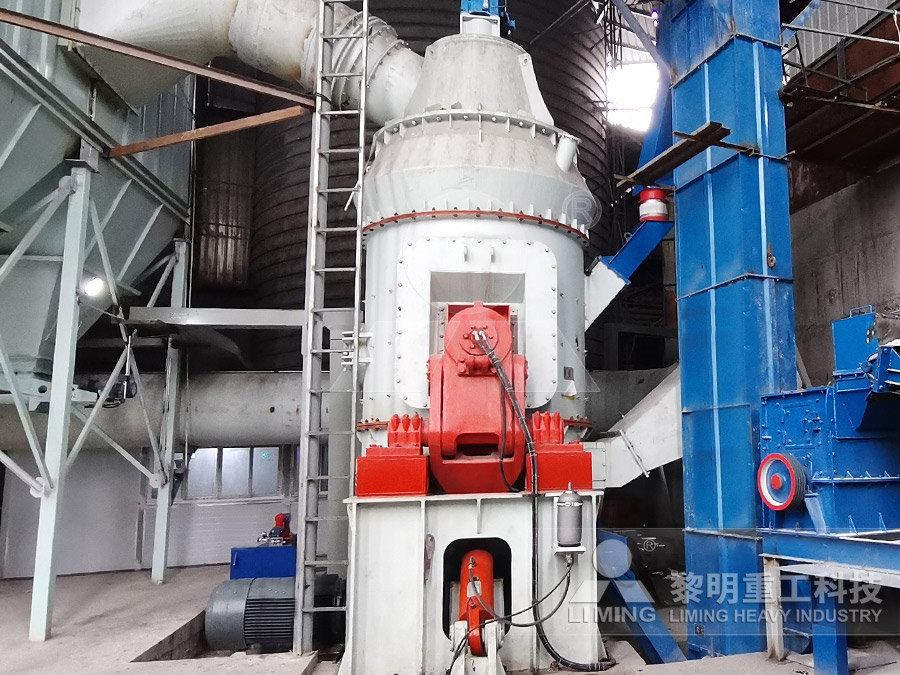
Improving the Sustainability of Cement Production by Using
2014年5月1日 The cement production has been known as the largest carbon emitting industrial sector (Yang et al 2014, Mikulčić et al 2015, Teixeira et al 2015, releasing an average of one ton of CO 2 into 2016年12月26日 Combustion mechanism of a 300 MW pulverized coal boiler is analyzed and the optimization of the performance of the boiler is carried out The flow field, temperature field, devolatilization, char Analysis of combustion mechanism and combustion optimization 2014年3月25日 In this paper, performances of pulverized coal combustion under the high preheated and oxygen deficient air are studied by both experimental and numerical methodology The experimental facilities have been accomplished in a HiTAC chamber with coal injection velocity that ranges from 10 to 40 m/sPerformance of Pulverized Coal Combustion under High 2014年6月24日 The use of waste wood biomass as fuel is increasingly gaining significance in the cement industry The combustion of biomass and particularly cofiring of biomass and coal in existing pulverized Numerical study of cofiring pulverized coal and biomass inside a
.jpg)
Developments in Pulverized CoalFired Boiler Technology
1996年4月10日 Exhaust gas temperature in coalfired power plants can reach approximately 120 °C to 140 °C, with the thermal energy accounting for approximately 3% to 8% of the total input energy2019年2月14日 Coal is the most abundant energy source, and around 40% of the world's electricity is produced by coal combustion The emission generated through it put a constraint on power production by coal combustion There is a need to reduce the emissions generated through it to utilize the enormous energy of coal for power productionA complete review based on various aspects of pulverized coal 2024年10月31日 Renewable energy sources are becoming increasingly crucial in the global energy industry and are acknowledged as a significant substitute for fossil fuels Oil palm fronds are a type of biomass fuel that can be utilized as a substitute for fossil fuels in the combustion process of boilers Cofiring (HTFRD) is a beneficial technology for reducing exhaust gas Utilization of Palm Frond Waste as Fuel for CoFiring Coal andImproving the sustainability of cement production by using numerical simulation of limestone thermal degradation and pulverized coal combustion in a cement calciner Journal of Cleaner Production (2014), The measurement equipment of this fully operating industrial calciner was placed on its outlet(PDF) Improving the sustainability of cement production by using
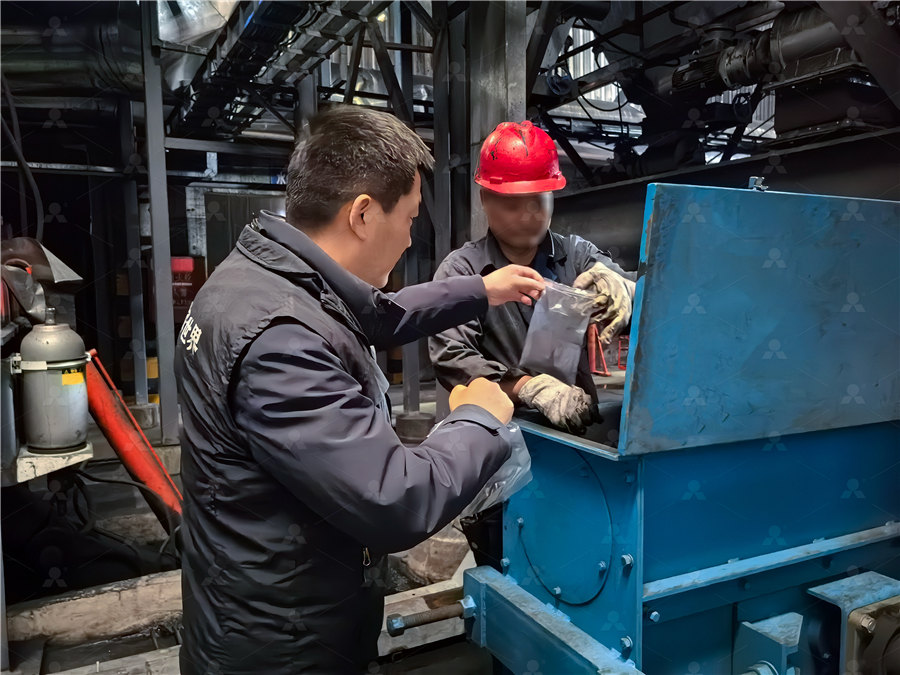
Understanding pulverised coal, biomass and waste combustion –
2015年1月5日 During the last hundred years, pulverised coal combustion has been widely applied for electricity generation [1] More recent, deregulation of the European power sector [1], low coal prices and a 2021年10月21日 Combustion Characteristics of Coal for Pulverized Coal Injection (PCI) Blending with Steel Plant Flying Dust and Waste Oil SludgeCombustion Characteristics of Coal for Pulverized 1996年12月4日 Coalfired boiler systems will continue to be major contributors in the future New pulverized coalfired systems routinelyinstalled today generate power at net thermal cycle efficienciesranging Technology Development for Advanced Pulverized 2014年1月1日 This article analyzes the problems of perfecting grinding equipment for largescale production – cement, ore, coal An improved design of a ball mill, equipped with internal energy Exchange (PDF) MPS mills for coal grinding ResearchGate
.jpg)
3A2 Pulverized Coal Injection for Blast Furnaces (PCI)
production rate period and the experience of longterm results, the capacity of the Oita No 1 blast furnace was designed for 80 kg/t various types of injection for the blast furnace pulverized coal equipment Table 2 shows the highest level attained in Japan for the typical operational index of blast furnaces utilizing pulverized2015年1月5日 Worldwide, the major thrust for coal research and development is focussed on developing and commercialising high efficiency low polluting plant In particular, coalfired plant capable of carbon capture and storage is a high priority Work on fundamental coal science therefore tends to be organised to support these aimsUnderstanding pulverised coal, biomass and waste combustion It is the main equipment of pulverized coal preparation system It is used for pulverizing all kind of coal in different harness It is also used for the coal grinding in the industries of cement, metallurgy, chemical, etc In Power Plant, the ball mill will dry, crush and grind the coal to be powder for the boiler fuelBall Mill Coal Pulverizer for power plant – ZJH minerals2022年10月1日 The generation and transport of coal powder has caused great harm to coal reservoir channeling conductivity, affecting the capacity of coalbed methane wells, causing the failure of engineering equipment and great distress to production, while current unblocking methods have many shortcomings In this study, a series of laboratory experiments on coal Experimental study on coal blockage removal based on pulverized coal
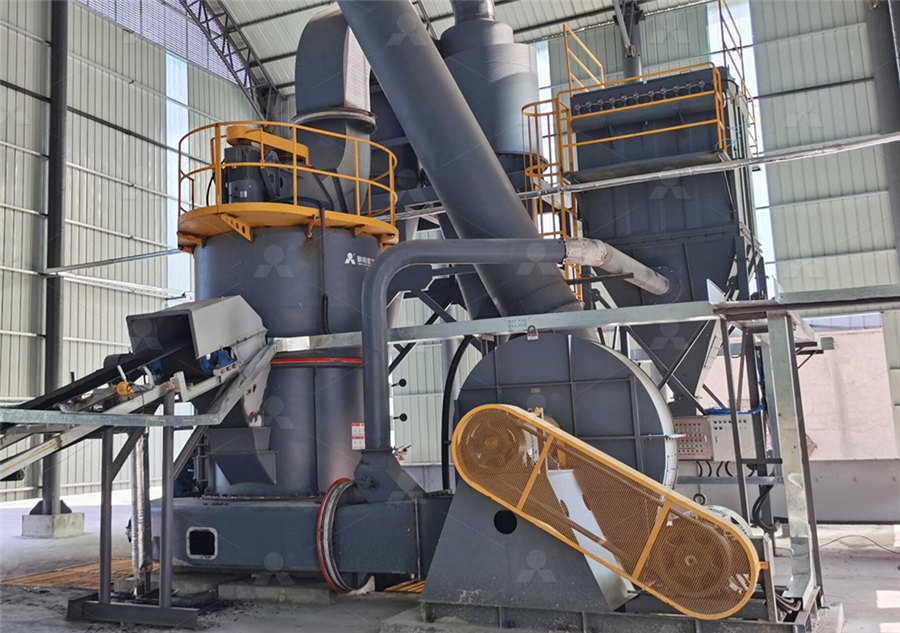
Design and construction of a PCI rig for evaluation of pulverized
2018年1月1日 Pulverized coal injection (PCI) is a technique worldwide used in blast furnaces (BFs) to reduce coke consumption Burning of pulverized coal injected into tuyeres of BFs takes place under medium Producing Electricity from Coal How does it work? Pulverized Coal Furnace Water Turbine Electricity Pulverized coal is converted to electricity through the Rankine cycle: 1 The coal is blown into the furnace, becomes airborne, and is burned 2 The heat generated from the burning heats water flowing through tubes in the furnace 3The Production of Electricity Power from Coal University of proponents of coal maintain it is a lowcost energy source, both the min ing and power generation processes can be costly and damaging to the environment Almost all coal plants operating today use pulverized coal technology, which involves grinding the coal, burning it to make steam and channeling the steam through a turbine to generate From Coal to Combined Cycle CRANE ChemPharma EnergyKeywords: circulating fluidized bed, pulverized coal, emissions Abstract—Power generation in South Africa has historically and continues to depend on the use of pulverized coal combustion The pulverized coal boilers are used by the majority of power stations around South Africa Although other types of technologies, such asPulverized coal versus circulating fluidizedbed boilers Perspectives
.jpg)
Pretreatment of biomass by torrefaction and carbonization for coal
2014年6月26日 To evaluate the utility potential of pretreated biomass in blast furnaces, the fuel properties, including fuel ratio, ignition temperature, and burnout, of bamboo, oil palm, rice husk, sugarcane COAl 2018 2017 2016 2015 2014 OIlBASED NATURAl GAS (CFB) and PulverizedCoal (PC), with the latter having different categories and efficiencies While coal energy production is a multibillion industry, its environmental, health andCOAL FACT2019年12月16日 This paper presents plasma technology for pulverisedcoal ignition and improving energy efficiency of power stations Plasma–fuel systems (PFS) were developed to accomplish this technologyPlasmafuel systems for clean coal technologies ResearchGate2022年3月3日 For drainage control, in accordance with the pulverized coal production, water production, and reservoir pressure of coalbed methane wells, different drainage control measures are applied at different drainage stages to achieve refined drainage 14,15 Meanwhile, different wellwashing measures are adopted for process management, and a powderproof tail pipe or Investigation on Pulverized Coal Control Using Calcium
.jpg)
A Sustainability Approach in the Development of Coal Blend
Blend Model for Subcritical Pulverized Coal Fired Power Plants in the Philippines Marvin I Noroña and Annabelle R Laureta 2014) In India, the coal production is unable to match the rapidly increasing demand of coal (Raaj, et al 2016) According to the International Energy Agency (IEA), in the year 2030 the use of coal isRequest PDF On Dec 1, 2014, Bo Jin and others published Dynamic simulation for mode switching strategy in a conceptual 600 MWe oxycombustion pulverizedcoalfired boiler Find, read and cite Dynamic simulation for mode switching strategy in aThe actual combustion rate of pulverized coal in the blast furnace tuyere is hard to be measured In this research, the combustion rate of pulverized coal injected into oxygen blast furnace was obtained by a new equipment This equipment can simulate the actual blast furnace well, and the relationship between pulverized coal injection (PCI) ratio and A O/C was established by Experiment Research on Pulverized Coal Combustion in the 2023年1月10日 The utilization of cofiring (coalbiomass) in existing coalfired power plants (CFPPs) is the fastest and most effective way to increase the renewable energy mix, which has been dominated by TechnoEconomic Analysis of Cofiring for Pulverized Coal Boilers
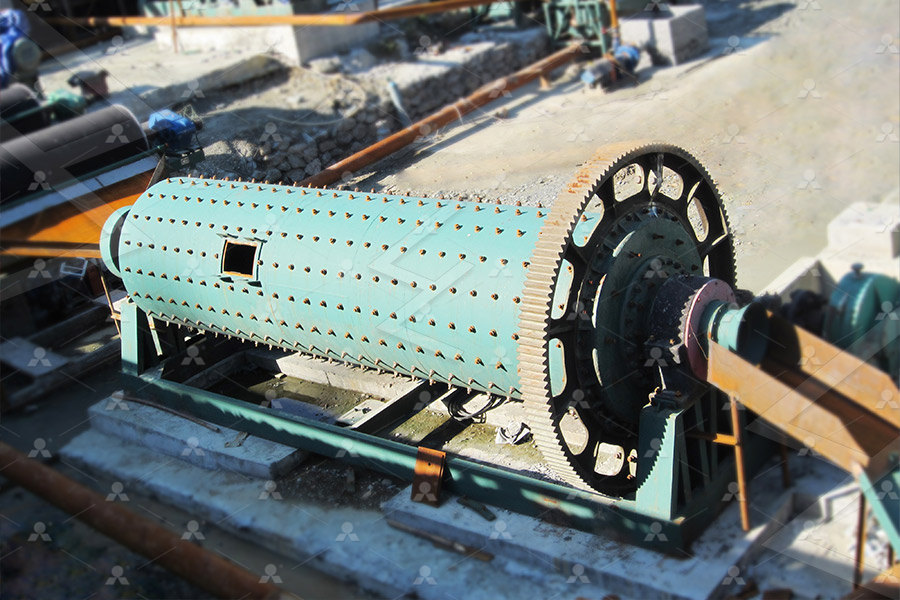
CNA Grinding equipment for superfine pulverized coal
The invention discloses grinding equipment for producing superfine pulverized coal, which belongs to the technical field of coal processing and comprises a base, a grinding box body, a motor, a heater, a first driving mechanism, a second driving mechanism, a suction fan, a third driving mechanism and a blower, wherein the surface of the base is fixedly connected with the JSC EVRAZ NTMK is the first metallurgical plant in modern Russia to launch a complex for the production and use of pulverized coal in blast furnace production Implementation of the project meets the objectives of introducing the best available technologies in blast furnace production at the plant`s industrial site, the project was developed on the basis of technical solutions of the Technology for the production and use of pulverized coal at JSC 2014年5月1日 The cement production has been known as the largest carbon emitting industrial sector (Yang et al 2014, Mikulčić et al 2015, Teixeira et al 2015, releasing an average of one ton of CO 2 into Improving the Sustainability of Cement Production by Using 2016年12月26日 Combustion mechanism of a 300 MW pulverized coal boiler is analyzed and the optimization of the performance of the boiler is carried out The flow field, temperature field, devolatilization, char Analysis of combustion mechanism and combustion optimization
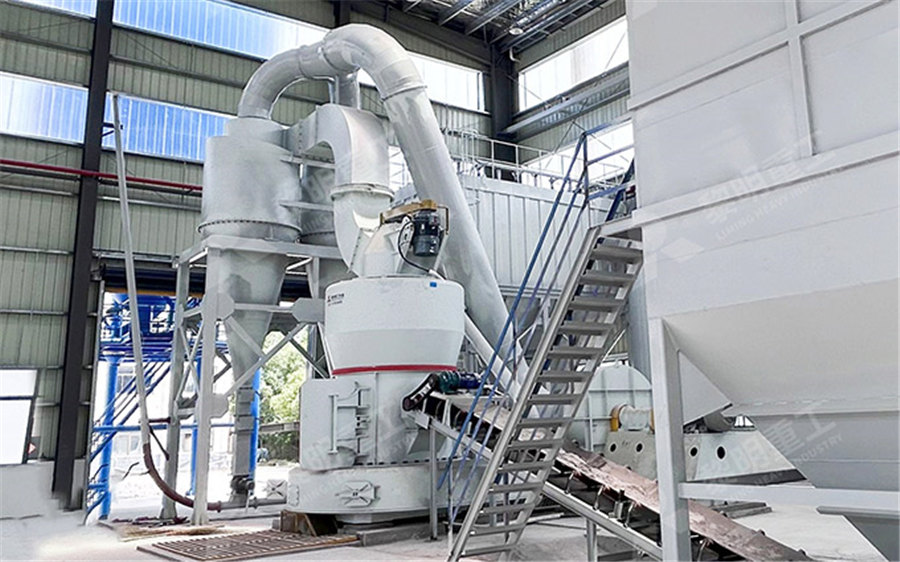
Performance of Pulverized Coal Combustion under High
2014年3月25日 In this paper, performances of pulverized coal combustion under the high preheated and oxygen deficient air are studied by both experimental and numerical methodology The experimental facilities have been accomplished in a HiTAC chamber with coal injection velocity that ranges from 10 to 40 m/s2014年6月24日 The use of waste wood biomass as fuel is increasingly gaining significance in the cement industry The combustion of biomass and particularly cofiring of biomass and coal in existing pulverized Numerical study of cofiring pulverized coal and biomass inside a 1996年4月10日 Exhaust gas temperature in coalfired power plants can reach approximately 120 °C to 140 °C, with the thermal energy accounting for approximately 3% to 8% of the total input energyDevelopments in Pulverized CoalFired Boiler Technology2019年2月14日 Coal is the most abundant energy source, and around 40% of the world's electricity is produced by coal combustion The emission generated through it put a constraint on power production by coal combustion There is a need to reduce the emissions generated through it to utilize the enormous energy of coal for power productionA complete review based on various aspects of pulverized coal
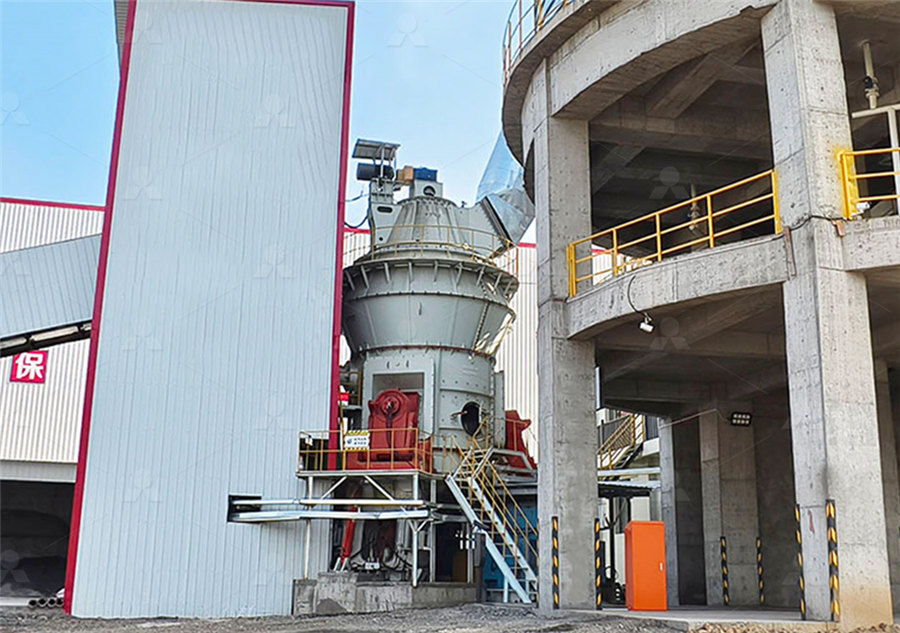
Utilization of Palm Frond Waste as Fuel for CoFiring Coal and
2024年10月31日 Renewable energy sources are becoming increasingly crucial in the global energy industry and are acknowledged as a significant substitute for fossil fuels Oil palm fronds are a type of biomass fuel that can be utilized as a substitute for fossil fuels in the combustion process of boilers Cofiring (HTFRD) is a beneficial technology for reducing exhaust gas Improving the sustainability of cement production by using numerical simulation of limestone thermal degradation and pulverized coal combustion in a cement calciner Journal of Cleaner Production (2014), The measurement equipment of this fully operating industrial calciner was placed on its outlet(PDF) Improving the sustainability of cement production by using