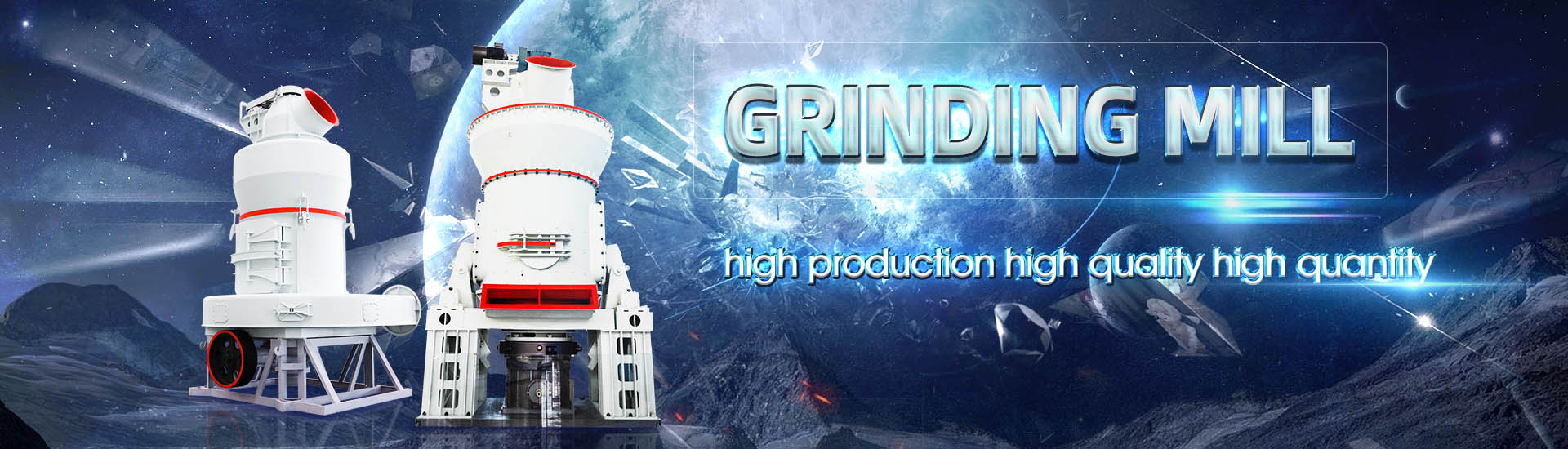
Ore grinding mill particle size factors
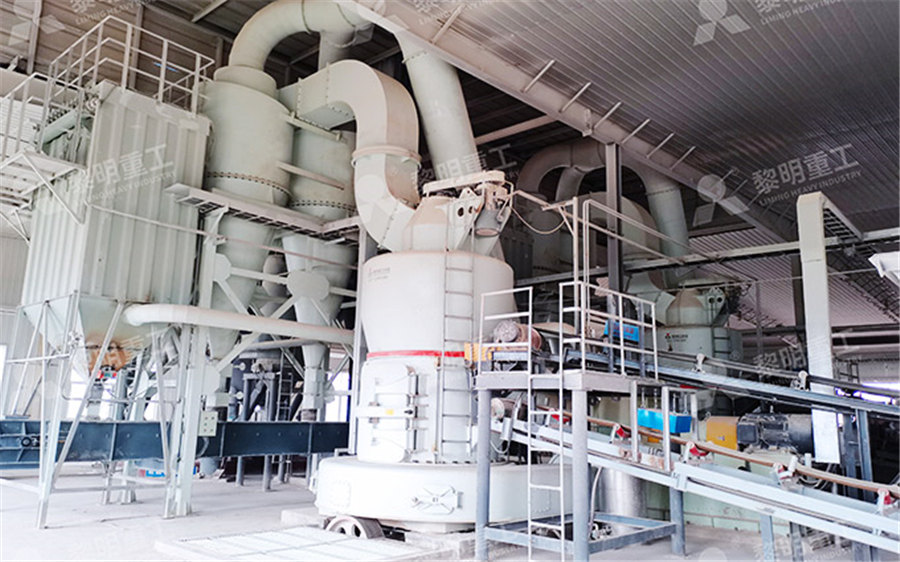
Fine grinding: How mill type affects particle shape characteristics
2017年9月1日 The authors concluded that, for the specific ore and particle size used, both shape and liberation were predominantly a function of ore texture and not whether milling was 2018年6月1日 In this article, alternative forms of optimizing the milling efficiency of a laboratory scale ball mill by varying the grinding media size distribution and the feed material particle size Effect of ball and feed particle size distribution on the milling 2023年7月20日 According to the particle sizes of grinding products, the grinding process is divided into coarse grinding, medium grinding, fine grinding, microfine grinding, and ultrafine Ore Grinding SpringerLink2024年8月29日 This study utilizes a pinstirred mill for the wet fine grinding of limonite to examine four different widths of PSD functions and compares their quantitative descriptions of the PSD Skewness is a parameter introduced to The effects of processing parameters on the shape of
.jpg)
Research on prediction model of ore grinding particle size
2019年3月28日 The results show that particle size distribution of crushing products under different crushing energies and ore particle sizes is obtained by drop weight test, and the 2019年3月28日 The results show that particle size distribution of crushing products under different crushing energies and ore particle sizes is obtained by drop weight test, and the crushing parameters A and b are calculated by fitting Research on prediction model of ore grinding particle Based on the total retention time of each ore, the optimum grinding time for each ore was identified to obtain the desired P 80 passing particle size with acceptable hematite liberation Estimation of Grinding Time for Desired Particle Size Distribution 2017年9月1日 The objective of this work is to assess the influence of fine grinding in ball mills and stirred mills on valuable mineral liberation and particle shape characteristics of UG2 ore, a Fine grinding: How mill type affects particle shape characteristics
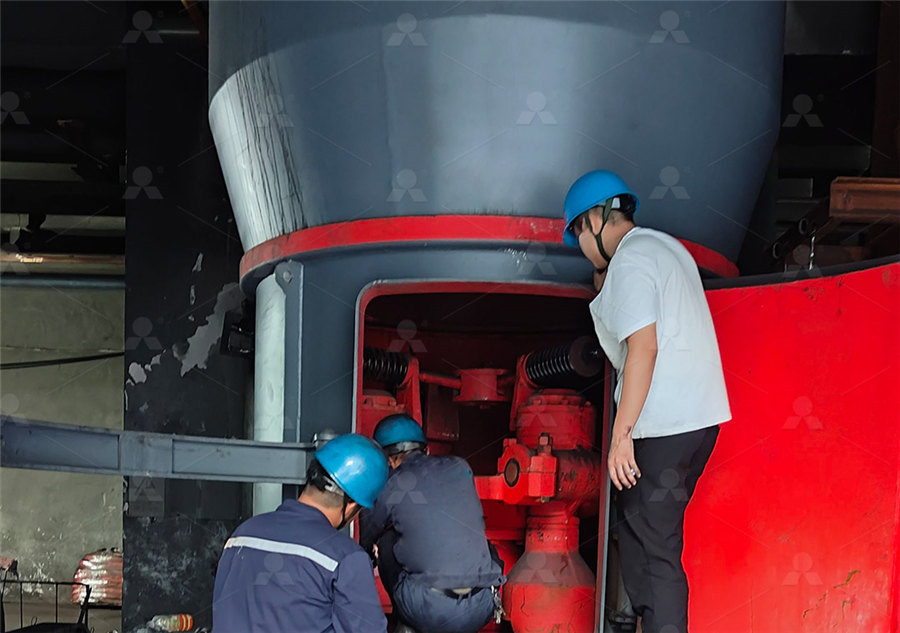
Estimation of Grinding Time for Desired Particle Size Distribution
The grinding of ore is a highly energyintensive process [1–4] In this process, the size of the particle obtained depends on the energy consumption of the ball mill The major challenge encountered in the process of iron ore grinding is to maintain the desired product particle size distribution (PSD) with sufficient liberation of valuable 2021年3月26日 Ball mill grinding efficiency is influenced by many factors: ore grindability, feed size, grinding product size, ball mill diameter and length, ball mill working speed, liner type, steel ball loading system, grinding concentration, What Factors Will Influence Ball Mill Grinding 2017年3月20日 An effect of a grinding method, that is ball mill and high pressure grinding rolls (HPGR), on the particle size, specific surface area and particle shape of an iron ore concentrate was studiedPhysicochemical Problems of Mineral Processing Request PDF On Mar 15, 2015, Mathis Reichert and others published Research of iron ore grinding in a verticalrollermill Find, read and cite all the research you need on ResearchGateResearch of iron ore grinding in a verticalrollermill
.jpg)
Investigating of the effect of ore work index and particle size on
2016年4月1日 The amount of feed was set at 1175 g, which was proportional to industrial scaleThe ball mill speed was constantly set at 768% CsExperiments were conducted at different ball sizes (between 20 and 40 mm), grinding time (10–30 min), solids content (65–80%) and work index of copper sulphide ore (12–154)RSM and Box–Behnken design were used for the 2017年7月3日 Closedcircuit grinding was employed to study the different ball loads Effect of Particle Size and Mill Power The influence that particle size may have on power is illustrated in table 5 There the variation in comminution was moderate but the power varied almost 10 percentVariables Affecting Grinding Mill Power 911MetallurgistThere are several impact factors of the grinding operation (1) Structure parameters of grinding mill, including its specifications, model, aspect ratio, ore discharging method, and liner form (2) Various working parameters of grinding mill, including fraction of critical speed for grinding mill, filling rate for grinding mill, grinding conOre Grinding Methods and Process of Ore GrindingParticle size distributions for many processes are contained in B26 EMISSION FACTORS (Reformatted 1/95) 9/90 Table B21 PARTICLE SIZE CATEGORY BY AP42 SECTION Anode baking furnace 9 1218 Leadbearing ore crushing and grinding 4 Prebake cell a Miscellaneous sourcesAP42, Appendix B2 Generalized Particle Size Distributions
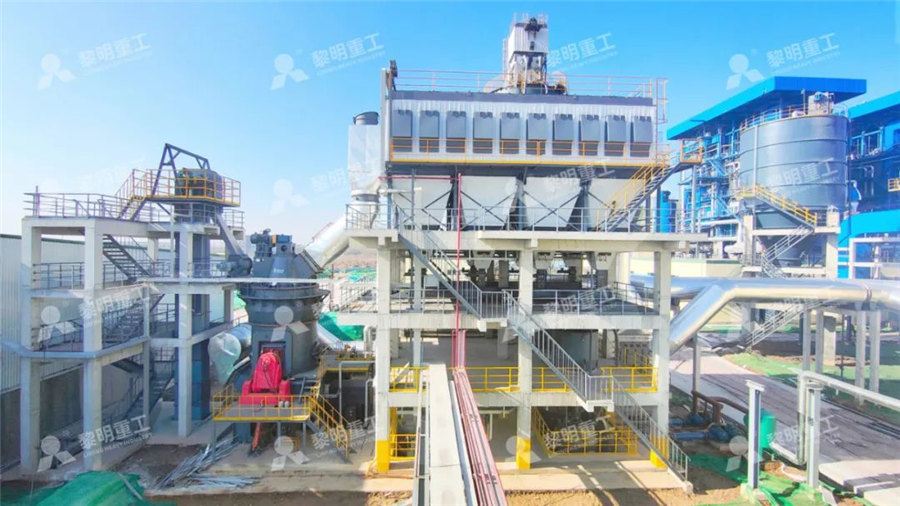
Fine grinding: How mill type affects particle shape characteristics and
2017年9月1日 In minerals processing it is typical for significant process fluctuations, due to ore variability, to affect mill throughput and/or flotation grade and recovery When these fluctuations cannot be explained by operational factors, they are typically ascribed to mineralogy or poorly understood factors such as particle shape2018年8月8日 Copper ore with a particle size between 0–1 mm was production process requires also car eful analysis of all of the factors influencing the mill in the grinding of a given particle size(PDF) Grinding Kinetics Adjustment of Copper Ore Grinding in 2020年4月1日 Balls or rods are placed inside the rotating drum which when combine with ore will break up the larger particles until the desired particle size is achieved Mill liners and grinding media (balls or rod) sizes along with ore Grinding Mills: How they Work Neumann their bond strength Ore size reduction is the result of the following three main fragmentation mechanisms 1 Abrasion 2 Cleavage 3 Fracture Figure 1 Grinding of ores inside a ball mill In practice, the three mechanisms never operate separately, and in the process of particle size reduction, they all work with possible advantage depending Control of ball mill operation depending on ball load and ore
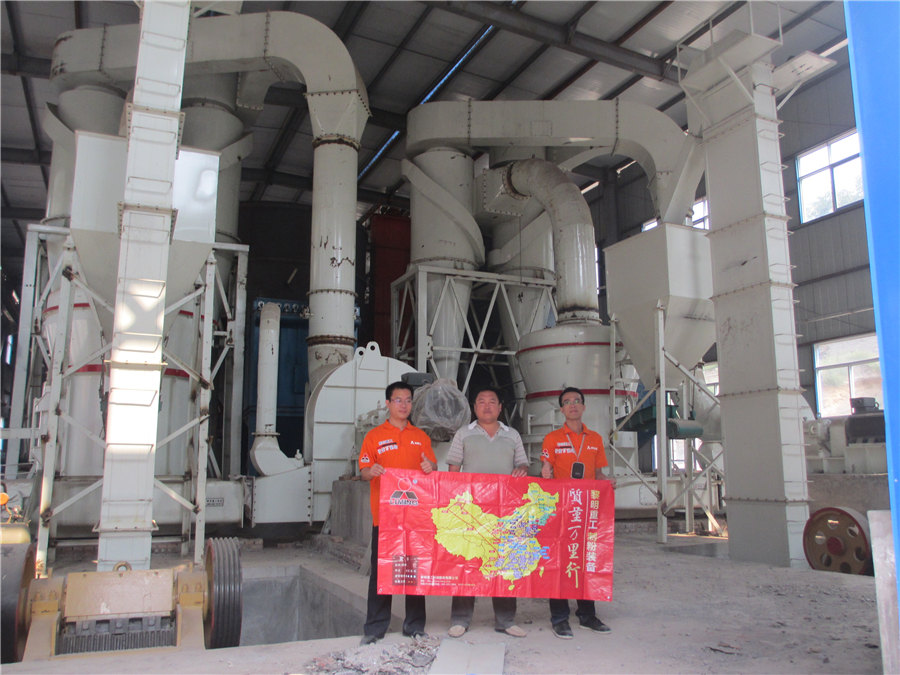
Estimation of Grinding Time for Desired Particle Size Distribution
Ball mills are progressively used to grind the ores for particle size reduction and to liberate valuable minerals from the ores The grinding of ore is a highly energyintensive process [1,2,3,4]In this process, the size of the particle obtained depends on the energy consumption of An investigation conducted on magnetite ore grinding with a dry HPGR machine to reduce the particle size from 50 mm to 90 µm has revealed that using two stages HPGR closed circuit with an air classifier can reduce energy consumption by 46% compared to a circuit in which there is a tertiary crushing with a wet ball millGrinding SpringerLink2024年11月11日 where P 1 is the sieve aperture size in µm, G is weight of the test sieve fresh undersize per mill revolution in g/rev, and 445 is a value related to the mass of balls in pounds, 3 which is approximately 2018 kg The determination of technical solutions for ore grinding and processing involves a lot of factors that need to be carefully consideredExploring the Link between HY Wet Ball Mill Work Index and Grinding ROLLER MILL AND BOWL MILL GRINDING B176 1126 NONMETALLIC MINERALS: TALC PEBBLE MILL data used to develop particle size distributions and emission factors for this appendix were: 1 Particle size distribution data AP 42, Appendix B1: Particle Size Distribution Data and Sized
.jpg)
Understanding the operation of grinding mills in the mining and
Understanding the operational principles and factors that influence mill performance is crucial for optimizing mill operations and achieving the desired particle size for downstream processes By considering these factors, mining companies can enhance the productivity and costeffectiveness of their grinding mill operationsparticle size reduction and to liberate valuable minerals from the ores The grinding of ore is a highly energyintensive process [1–4] In this process, the size of the particle obtained depends on the energy consumption of the ball mill The major challenge encountered in the process of iron ore grinding is to maintain the desiredEstimation of Grinding Time for Desired Particle Size Distribution2018年2月1日 In another study to investigate ball size distribution on ball mill efficiency by Hlabangana et al [50] using the attainable region technique on a silica ore by dry milling, a threeball mix of Effect of ball and feed particle size distribution on the milling 2019年8月15日 In this article, alternative forms of optimizing the milling efficiency of a laboratory scale ball mill by varying the grinding media size distribution and the feed material particle size (PDF) Effect of interstitial filling, ball and feed size on particle
.jpg)
Grinding Kinetics Adjustment of Copper Ore Grinding in an
applied sciences Article Grinding Kinetics Adjustment of Copper Ore Grinding in an Innovative Electromagnetic Mill Marta WołosiewiczGłab˛ 1,*, Paulina Pieta˛ 1, Dariusz Foszcz 1, Szymon Ogonowski 2 ID and Tomasz Niedoba 1 1 Department of Environmental Engineering and Mineral Processing, Faculty of Mining and Geoengineering, AGH University of Science and 2020年5月28日 In the iron and steel industry, the production of narrow particle size distribution (PSD) for pellet feed making with acceptable liberation of valuables from the iron ore is very difficultInvestigation on Iron Ore Grinding based on Particle Size Distribution 2017年9月1日 This situation makes it necessary to examine parameters such as the type of grinding material (coal/ore), grinding type/medium, grinding technique, particle size, shape, size distribution Fine grinding: How mill type affects particle shape characteristics Grinding is the final stage of comminution, which reduces particle size to micron size level The size reduction is achieved by attrition, abrasion, and impact between the ore itself and between Grinding Media in Ball MillsA Review ResearchGate
.jpg)
Size reduction performance evaluation of HPGR/ball mill and
2022年12月15日 In the present study, size reduction experiments were performed on HighPressure Grinding Rolls (HPGR), ball mill and stirred mill of PGE bearing chromite ore2019年3月28日 In the ball mill, the main grinding method was the impact of the steel ball medium with the finer ore particles, and the Ecs was high because the weight of the single steel ball was significantly Research on prediction model of ore grinding particle size distribution2023年1月1日 As grinding time increases, the ore's particle size gradually reduces due to the grinding and impact forces exerted by the grinding media Consequently, the useful minerals and the pulsed minerals within the ore reach their maximum dissociation (Fan et A prediction of blend grinding result based on individual ore size Estimating Ore Particle Size Distribution grinding mill performance Tessier et al (2007) of the most important factors affecting semiautogenous grinding mill performance Tessier et al (2007) also notes that feed size variations strongly affect mill performance,Estimating Ore Particle Size Distribution using a Deep
.jpg)
Should the slurry density in a grinding mill be adjusted as a
2007年7月1日 When the specifications and models of the ball mill are determined, the factors affecting the operation indexes of the grinding process include three facets [15–19]: one, the properties of the ore entering the grinding process, including the mechanical properties of the ore, the particle size distribution of the feed, and the required product 2018年7月1日 Hybrid nonlinear model predictive control of a runofmine ore grinding mill circuit The economic evaluation of a grinding mill circuit is done by using the relationship between the grinding mill circuit product particle size and the separation concentrate recovery and Systems, Human Factors, and Political Risk 2019, Mining Hybrid nonlinear model predictive control of a runofmine ore The grinding of ore is a highly energyintensive process [1–4] In this process, the size of the particle obtained depends on the energy consumption of the ball mill The major challenge encountered in the process of iron ore grinding is to maintain the desired product particle size distribution (PSD) with sufficient liberation of valuable Estimation of Grinding Time for Desired Particle Size Distribution 2021年3月26日 Ball mill grinding efficiency is influenced by many factors: ore grindability, feed size, grinding product size, ball mill diameter and length, ball mill working speed, liner type, steel ball loading system, grinding concentration, What Factors Will Influence Ball Mill Grinding
.jpg)
Physicochemical Problems of Mineral Processing
2017年3月20日 An effect of a grinding method, that is ball mill and high pressure grinding rolls (HPGR), on the particle size, specific surface area and particle shape of an iron ore concentrate was studiedRequest PDF On Mar 15, 2015, Mathis Reichert and others published Research of iron ore grinding in a verticalrollermill Find, read and cite all the research you need on ResearchGateResearch of iron ore grinding in a verticalrollermill2016年4月1日 The amount of feed was set at 1175 g, which was proportional to industrial scaleThe ball mill speed was constantly set at 768% CsExperiments were conducted at different ball sizes (between 20 and 40 mm), grinding time (10–30 min), solids content (65–80%) and work index of copper sulphide ore (12–154)RSM and Box–Behnken design were used for the Investigating of the effect of ore work index and particle size on 2017年7月3日 Closedcircuit grinding was employed to study the different ball loads Effect of Particle Size and Mill Power The influence that particle size may have on power is illustrated in table 5 There the variation in comminution was moderate but the power varied almost 10 percentVariables Affecting Grinding Mill Power 911Metallurgist
.jpg)
Ore Grinding Methods and Process of Ore Grinding
There are several impact factors of the grinding operation (1) Structure parameters of grinding mill, including its specifications, model, aspect ratio, ore discharging method, and liner form (2) Various working parameters of grinding mill, including fraction of critical speed for grinding mill, filling rate for grinding mill, grinding conParticle size distributions for many processes are contained in B26 EMISSION FACTORS (Reformatted 1/95) 9/90 Table B21 PARTICLE SIZE CATEGORY BY AP42 SECTION Anode baking furnace 9 1218 Leadbearing ore crushing and grinding 4 Prebake cell a Miscellaneous sourcesAP42, Appendix B2 Generalized Particle Size Distributions2017年9月1日 In minerals processing it is typical for significant process fluctuations, due to ore variability, to affect mill throughput and/or flotation grade and recovery When these fluctuations cannot be explained by operational factors, they are typically ascribed to mineralogy or poorly understood factors such as particle shapeFine grinding: How mill type affects particle shape characteristics and 2018年8月8日 Copper ore with a particle size between 0–1 mm was production process requires also car eful analysis of all of the factors influencing the mill in the grinding of a given particle size(PDF) Grinding Kinetics Adjustment of Copper Ore Grinding in